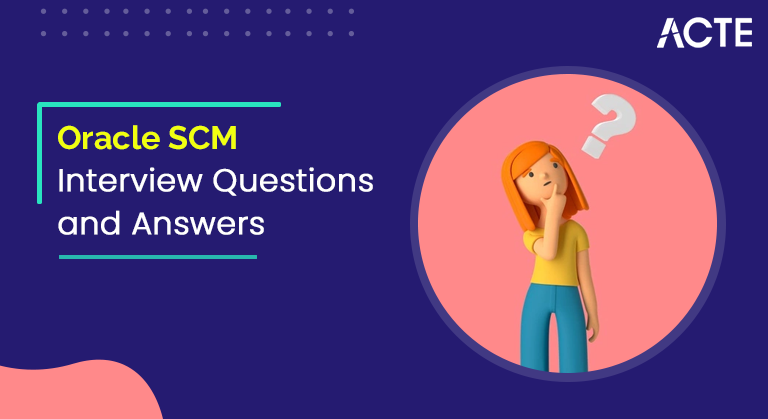
Oracle SCM is a robust suite of applications designed for comprehensive supply chain optimization. Covering procurement, manufacturing, inventory management, order fulfillment, and logistics, this solution offers organizations a unified view and precise control over their supply chain operations. Leveraging advanced technologies like artificial intelligence and machine learning, Oracle SCM enhances decision-making, refines forecast accuracy, and boosts overall operational efficiency. With end-to-end visibility, the platform enables synchronized supply chain activities, cost reduction, improved collaboration with suppliers, increased customer satisfaction, and adaptability to dynamic market conditions. Equipped with real-time analytics, demand planning, and collaboration tools, Oracle SCM empowers businesses to establish agile and responsive supply chains, fostering operational excellence and gaining a competitive edge in the dynamic global market.
1. How do I calculate Total annual cost?
Ans:
Use Total Annual Cost equation:
- TC = DC + (D/Q)*S + (Q/2)*H
- TC = Total annual cost
- D = Demand
- C = Cost per unit
- Q = Order quantity
- S = Cost of the placing an order or setup cost
- H = The Annual holding and storage cost per unit of inventory
2. What is economic order quantity [EOQ]?
Ans:
It is the quantitative inventory model that have used to determine the most economic quantity to order based on the cost and demand factors.
If C=Carrying the cost per unit per year; F=Fixed a cost per order; D=Demand in units per year; Formula for Economic Order Quantity= ((2 × F × D)/C) (1/2)
3. How will I calculate the total length of the supply chain?
Ans:
To calculate the total length of supply chain is:
Total length of supply chain = DRM + DWIP + DFG
4. What is Oracle SCM?
Ans:
Oracle SCM (Supply Chain Management) is the set of applications designed to optimise and streamline the business processes related to supply chain. It includes modules for inventory management, order management.
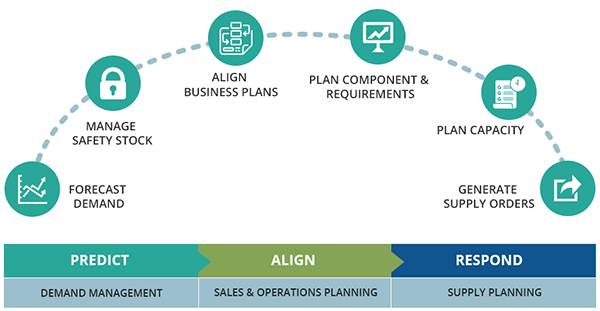
5. How to calculate exponential smoothing?
Ans:
It’s used in the forecasting procedure:
F (t) = (Ft-1 + a ((At-1) – (Ft-1)))
6. How to calculate flow time?
Ans:
Little’s Law relates the throughput, time and inventory:
Flow time = Inventory (WIP)/Throughput rate
7. What’s the use of Global Trade Item Number (GTIN)?
Ans:
The Global Trade Item Number is the 14-digit item number used in an item identification system for the products.
It is the standard number used in RFID and electronic commerce.
8. How to use the PKI system in the supply chain?
Ans:
Used a Public Key Infrastructure for Securing the E-Business across the Supply Chain.
Public Key Infrastructure (PKI) offers the strong linkage between the business identities and transactions throughout the supply chain.
In the PKI system, every user has two keys: public key and private key.
These keys can be used for encrypting and decrypting information, for electronically signing electronic information, and for verifying the authenticity of the owner.
9. What is Cost analysis?
Ans:
Cost analysis=Review of potential provider’s cost elements to determine appropriateness and reasonableness.
Required for the categories of personnel & reasonableness of a personnel work time proposed indirect cost, base to which rates are applied.
Compare the estimated costs with the prior actual costs.
10. What are supply chain performance indicators?
Ans:
Cp is the measure of process capability that compares the specification width with the process width- not adjusted for lack of the process centering.
Cpk a measure of process capability that compares specification width with the process width- adjusted for lack of the process centering.
Consists of the four types of indicators:
Quality, time, financial, and productivity.
11. What are the 5 stages of a product’s life cycle?
There are the five stages of a product’s life cycle:
- Extraction
- Production
- Packaging and Transport
- Usage
- Disposal
12. What are marketing functions?
Ans:
- Buying
- Selling
- Storing
- Transporting
- Sorting
- Financing
- Information Gathering
- Risk Taking
13. What is Material management?
Ans:
A material management department, which has authority and responsibility for all the activities, concerned with the flow of materials in the company.
- Efficient use of working capital
- Responding to the market changes related to any product
- Ensuring cooperation of all departments
- Providing the best services to the customer
- Analysing the materials and supply to reduce cost
- Improve the quality and ensure supplier performance
- Maintain a minimum inventory levels
14. What are responsibilities allocated to the production environment?
Ans:
- Product fabrication
- Work schedules
15. What suggestions for optimising purchasing and production departments?
Ans:
- Product fabrication
- Lead time for delivery of material
- Work schedules
- Selection of sources of supply
16. What are different planning methods in Inventory?
Ans:
- Subinv Replenishment Planning
- Min Max Planning
- Reorder point planning
- Kanban Planning
- Periodic Automatic Replenishment
17. What are setups for different planning method (Min-Max)
Ans:
- Setup item in the master-org and assign the item to org for which can Min-Max planning is used
- Attributes, Inv Planning method: Min-Max
- Min-Max Qty should have been defined
- Safety Stock method should be a non-MRP Planned
- Determine the status of Requisitions created for the planning
18. What are setups for expense items?
Ans:
- No Stackable
- No Transactable
- No Costing, Inv Asset
19. How many key flex fields are in Inventory?
Ans:
- Account Alias
- Item
- Item Category
- Item Catalogues
- Stock Locators
- Sales Order
- Service Items
20. What is the use of sales order KFF?
Ans:
- This is used for material transaction when a source is the Sales Order
- Segments are the Sales order Numbers. Sales Order Type.Sales Order Source
21. What all setups have done in inventory organisation implementation?
Ans:
- Location
- Calendar
- Organization
- Parameter
- Cost Group
- Sub inventory
22. What are valuation accounts used in Inventory?
Ans:
- Material: An asset account tracks a material cost.
- Resource: An asset account tracks the resource cost.
- Overhead: An asset account tracks the resource and outside processing overheads.
- Outside processing An asset account that the outside processing costs.
23. What is ABC Analysis and why is it used?
Ans:
1. ABC Analysis is the Inventory categorization method to categorize items into the 3 different classes A being most valuable and C being the least valuable ones.
2. Using this Analysis, it will be simple to monitor and keep on track of valuable items like frequently doing cycle counts on the A class items, etc.
24. What is the process of cycle count?
Ans:
1. Create the cycle count header with the required data
2. Assign items to be counted
3. Then run required cycle count report
4. Using report do the cycle counts
5. Then go and Approve cycle count
25. Difference between MO Issue and MO Transfer?
Ans:
- MO Issue will move out stock from the inventory against an account
- MO transfer will move stock from a one subinventory to other<.li>
26. What is the Picking rule in Inventory?
Ans:
1. Picking Rule is used to determine a list of items for sales order/ shipping based on revision, Lot, Subinventory, and Locator.
2. Assign the required Picking Rule to the item in the Order Management tab.
27. What are the criteria in Cycle count?
Ans:
- Depending on the requirement, it can trigger the cycle count.
- can define the regular cycle count of the high values items.
- If back-ordered or pick denied, can trigger cycle count for those items.
28. What is differnce between Lot and Serial?
Ans:
Lot control is to control the whole batch of items. For example, in a drug industry, have batch numbers that can be controlled using the lot where you can track the complete batch using the specific data.
Serial control is to monitor and track every single qty of an item like the electronic devices where tracked by serial number.
29. How is MO difference from Subinv transfer?
Ans:
MO generally is a request of movement of items in the one organisation. It may be from the 3 sources, MO requisition, Replenish MO, Pick Wave MO. MO can be MO Issue that will issue an item from the location and MO transfer which ll transfer an item to another location.
30. What are different status attributes in Item?
Ans:
Can define the different status for an item combination these attributes as per business need
Following are attributes
1. BOM Enabled
2. Build in WIP
3. Customer order enabled
4. Internal Order enabled
5. Invoice
6. Purchasable
7. Stackable
8. Transactable
31. Why is master-org required?
Ans:
So that can have an item maintained at a master level with the common attributes and then can use the same item across multiple organisations instead of defining it again and again.
32. What are Lot control setups?
Ans:
Lot control can be set up at the item attributes at the organisation level.
Either No Control or a Full Control
33. What is a predefined locator in Subinventory?
Ans:
Can set up locator control in the 4 diff ways for each subinventory
- Prespecified: System will ask to select locator combinations which already been defined in a sub inventory during the transaction
- Dynamic Entry: Either can select any locator during the transaction or can create the new combination
- Item Level: This will take a locator which has been defined at item attribute level
34. How is WMS helpful compared to Inventory?
Ans:
Warehouse Management (WMS) enables the companies to maximise utilisation of labour, space, and equipment investments by coordinating and optimising resource usage and material flows. Specifically designed to support the needs of distribution, manufacturing, asset-intensive, and service businesses, Oracle WMS provides the single platform across the entire global supply chain.
35. Why strategy used
Ans:
After defining the rules, must set up a strategy and then associate applicable rules. After assigning the rules to a strategy, the rules engine can execute the strategies on any objects to which strategy applies. The rules engine executes each subsequent rule in the strategy until an allocation is completely filled.
36. Difference between ‘Accrue On Receipt’ and ‘Accrue at Period End’?
Ans:
Criteria | Accrue On Receipt | Accrue at Period End | |
Expense Timing | Recognizes expenses upon receipt or when goods/services are received. | Delays expense recognition until the end of the accounting period. | |
Matching Principle | Aligns with the matching principle, recognizing expenses when related revenues are earned. | May not align with the matching principle, as expenses might not match revenues. | |
Cash Flow Impact | Has an immediate impact on cash flow as expenses are recognized promptly. | Cash flow impact may be postponed until the accounting period’s end when expenses are accrued. | |
Complexity | Generally simpler to administer, suitable for businesses with frequent transactions. | Can be more complex, involving accurate estimation and tracking of accrued expenses. | |
Liabilities Visibility | Provides real-time visibility into liabilities as they occur. | Liabilities might not be immediately apparent, being recognized only at the period end. | |
Risk of Overstatement | Lower risk of overestimating liabilities due to real-time recognition. | Higher risk of overestimating liabilities with reliance on estimates and accruals. | |
Examples | Common in industries with immediate transactions, like retail. | Prevalent in industries with a time lag between receipt and expense recording, such as construction or consulting. |
37. What is Document Total and Account Range types on Approval Groups form?
Ans:
The Document Total type sets a maximum limit for any approval actions taken by the user to whom the approval group applies to. If the multiple Document Totals are specified, restriction will be to a Document Total, which is the lowest. The Account Range also allows for document total which is then tied to a specific range of accounts listed on a same line. It is possible to have different account ranges with different amount Limits. This allows the same user to have different dollar/account limits. It is mandatory to have the account range specified in every approval group defined.
38. What are Reminder notifications?
Ans:
Once the approver doesn’t respond to approval notification for a quite some time, then reminder notification can be sent out to approver. can send up to two reminders to the approver using the Timeout feature. And can also specify that after a certain period of time, the document be forwarded automatically to the next approver in hierarchy. This feature has to be set up by changing the PO and/or Requisition approval workflow in the Oracle Workflow Builder.
39. How do you set up a timeout feature?
Ans:
To enable Timeout feature in the PO Approval workflow, modify following activities in a Notify Approver subprocess by entering the Timeout period in their Properties windows:
- Access Oracle SCM Application
- Navigate to Security Settings
- Locate Session Timeout Settings
- Configure Timeout Duration
- Save Changes
- Test the Timeout Feature
40. What does the Account Generator process do?
Ans:
The Account Generator processes the builds charge, budget, accrual, and variance accounts for every purchase order, release, and requisition distribution based on distribution’s destination type. It is the synchronous Workflow process.
41. What are Prerequisites to use an Account Generator?
Ans:
Before using Account Generator must:
1. Define Accounting flexfield structure for every set of books.
2. Define the flexfield segment values and the validation rules.
3. Set up the Oracle Workflow.
4. Decide whether to use the Account Generator processes as seeded in the Oracle Purchasing, or need to customise them to meet accounting needs.
42. When is the charge account field not updateable?
Ans:
In following cases the charge account field is not updateable:
1. If the destination type code is the INVENTORY or SHOP FLOOR.
2. If distribution is already encumbered.
3. If PO is created from an encumbered Requisition
4. If destination type code is Expense and
If project is entered and profile option PA_ALLOW_FLEXBUILDER_OVERRIDES is set to NO
If expense accrual code= RECEIPT
43. How many Transaction Types exist?
Ans:
- Receive – Receive the items into a Receiving Dock.
- Deliver – Deliver items into expense or inventory destinations.
- Return to Vendor – Return received items directly to the vendors.
- Return to Receiving – Return delivered items to Receiving Dock or inspection.
- Accept – Accept items following inspection.
- Reject – Reject items following inspection.
- Transfer – Transfer items between the locations.
44. What are major receiving tables involved?
Ans:
RCV_SHIPMENT_HEADERS
RCV_SHIPMENT_LINES
RCV_TRANSACTIONS
RCV_RECEIVING_SUB_LEDGER
45. What are the minimum setups required for Items for Internal Sales orders?
Ans:
The items which are used for Internal Sales Order must be an Inventory enabled, internally orderable and stackable, shippable, and Order Management transactable for the source organisations. Under Inventory, you need to select Inventory Item, Transactable, and Stackable options. Under Order Management, you need to select the Internal Ordered, Internal Orders Enabled, OE Transactable, and Shippable options.
46. What are steps to perform Inter-Organization Transfer?
Ans:
1. Setup Shipping Network
2. Inventory/Transactions/Inter organisation Transfer
3. Receive against the Inter-org Transfer: Choose the Purchasing Super User responsibility.
47. What is Debit Memo Invoice?
Ans:
A Debit Memo Invoice is the document used in accounting to notify the customer that they owe additional money to the sender. It is issued by the seller or supplier to inform buyers about a debit entry made on account, indicating an increase in amount owed.
48. What is Pay On Receipt?
Ans:
Pay on Receipt (also known as the ERS (Evaluated Receipt Settlement) or Self-Billing) is an Oracle Purchasing’s concurrent program, which automatically creates invoices in the Oracle Payables and matches them with PO’s automatically for received amount. The short name for a program is POXPOIV.
49. What is the Ageing Period (R11i)?
Ans:
The parameter Aging period determines a transaction on receipt that can be considered for invoice creation. Forex if the aging period is given as 1, then all transactions that have transaction date less than or equal to the (sysdate-1) are considered for the invoice creation. The ageing period can be set through the profile option PO: ERS Aging period.
50. What are non-supported features of Receiving Open Interface?
Ans:
The non-supported features are include:
- Lot number transactions
- Serial number transactions
- Dynamic locator control
- Replace transactions
- Separate RECEIVE and DELIVER transactions
51. Difference Between Purchased And Purchasable Flag For Item?
Ans:
- Purchasable is the standing characteristic flag, so based on this flag, certain transactions can be managed for items.
- Purchased flag makes the decision whether or not to buy and get hold of this item.
- Purchasable flag comes to the decision whether or not to order this item in the purchase order.
- If attainable is enabled, objects can be ordered in the purchase order, if not, new buy orders can’t be created and permitted for objects.
- If purchased is enabled, object can be received if already present in the authorised buy order.
52. Explain Shipping Method?
Ans:
Shipping techniques are manners to deliver fabric. When creating a transport approach, I need to permit it earlier than I could use it in a transport network. If you disable a transport technique, it can’t be used in the transport network.
53. Describe Inter Organization Shipping Networks?
Ans:
An inter-company delivery community describes relationships and accounting facts among the transport enterprise and a destination business enterprise. need to define the transport community between the two businesses before they can transfer fabric between companies. When set up a delivery community have to pick out a transfer kind: In Transit or Direct.
54. What Is Revision Control In Oracle Inventory?
Ans:
A revision is the particular model of an object, invoice of cloth, or routing. Revision manipulation is normally enabled for figuring out a changed item. Items may be positioned underneath revision manipulation by checking the field `Revision control` in the Inventory tab at the same time as defining new item or for existing object. Base table for the Item Revision is MTL_ITEM_REVISIONS.
55. What Is a Consignment Inventory?
Ans:
Consignment Inventory is a stock that is inside possession of the consumer, however is still owned with aid of the provider. In different words, the provider locates the number of his stock in patron’s ownership and allows them to sell or consume without delay from inventory. The client purchases a stock simplest after having resold or fed on it.
56. Explain Re-order Point Planning?
Ans:
Reorder point planning calls for the forecasts to decide while to order the brand new quantity to refill stock. Reorder factor planning suggests the brand new order for item while the available quantity drops below item’s safety stock level plus forecast call for the object during its replenishment lead-time. The advised order quantity is the economic order quantity that maximises total fee of ordering and wearing stock. Oracle Inventory can robotically generate requisitions to tell the purchasing branch that replenishment order is required to deliver the organisation.
57. How can I calculate Supply Chain Working Capital Productivity Ratio?
Ans:
SWC = INV+ AR-AP
Where:
SWCP (SWC productivity) = NS/SWC
58. Explain Oracle Procurement module?
Ans:
Oracle Procurement helps an organisation manage the purchasing process efficiently. It includes the functionalities for a supplier management, purchase orders, sourcing, and negotiation, enabling an organisation to optimise procurement activities.
59. What is Oracle Advanced Supply Chain Planning (ASCP)?
Ans:
Oracle ASCP is the module that helps organisations plan supply chain activities effectively. It uses the advanced algorithms to optimise for demand and supply planning, considering factors like lead times, demand variability, and constraints.
60. How does the Oracle Manufacturing module contribute to supply chain efficiency?
Ans:
Oracle Manufacturing module assists in managing the production process. It includes the functionalities for work orders, bills of materials, and routing, allowing organisations to plan, track, and optimise manufacturing operations.
61. What is Oracle Logistics in supply chain management?
Ans:
Oracle Logistics helps organisations manage the movement of the goods and materials through the supply chain. It includes the functionalities for transportation management, warehouse management, and global trade management.
62. Explain Oracle SCM Cloud?
Ans:
Oracle SCM Cloud is the cloud-based suite of applications that provide end-to-end supply chain management capabilities. It includes the modules for planning, procurement, manufacturing, and logistics, and it enables an organisation to benefit from a cloud-based infrastructure and continuous updates.
63. What are key benefits of implementing Oracle SCM?
Ans:
The key benefits of implementing the Oracle SCM include improved supply chain visibility, increased efficiency, reduced costs, better decision-making through the real-time data, enhanced collaboration with the suppliers and customers, and ability to adapt quickly to changing market conditions.
64. Explain Order to Cash (O2C) in Oracle SCM?
Ans:
Order to Cash in Oracle SCM refers to a business process that starts with the receiving a customer order (Order Management) and ends with receiving payment for a shipped goods (Accounts Receivable). It involves the various modules, including Order Management, Shipping, and Accounts Receivable.
65. How does Oracle SCM support demand forecasting?
Ans:
Oracle SCM includes the demand forecasting capabilities through modules like Advanced Supply Chain Planning (ASCP). These modules use the historical data, trends, and other factors to predict a future demand, helping organisations optimise inventory and production planning.
66. Explain MRP in Oracle SCM?
Ans:
MRP in Oracle SCM is the planning process that helps organisations determine materials needed for production. It considers factors like demand, lead times, and existing inventory to generate the recommendations for purchase orders and production orders.
67. How does Oracle SCM integrate with other business applications?
Ans:
Oracle SCM integrates with the other business applications through technologies like Oracle Integration Cloud (OIC) or Oracle Middleware. These integrations enable the seamless data flow between the SCM modules and other enterprise applications like ERP, CRM, and HR systems.
68. Explain Lead Time in Oracle SCM.?
Ans:
Lead time in Oracle SCM refers to a time it takes for a product to be ordered, manufactured, and delivered. It includes the various components such as processing time, transportation time, and waiting time.
69. How does Oracle SCM address demand variability and uncertainty?
Ans:
Oracle SCM uses the advanced forecasting techniques and planning modules, such as Demand Management and Advanced Supply Chain Planning, to address demand variability and uncertainty. These tools help the organisations better anticipate and respond to the changes in demand.
70. Explain Backorder in Oracle Order Management?
Ans:
In Oracle Order Management, backorder occurs when there is insufficient inventory to fulfil the customer order. The system may reserve the available quantity and place the remaining quantity on backorder until a more stock becomes available.
71. What is Oracle Work in Process (WIP) in manufacturing?
Ans:
Oracle WIP is the module that helps organisations manage and track manufacturing processes. It includes the features for creating work orders, tracking work-in-progress, and capturing production costs.
72. How does Oracle SCM handle returns and reverse logistics?
Ans:
Oracle SCM includes the modules for managing returns and reverse logistics, allowing an organisation to process and track returned goods efficiently. This helps in maintaining customer satisfaction and optimising inventory levels.
73. Explain Safety Stock in Oracle SCM?
Ans:
Safety stock in the Oracle SCM is the extra inventory held to mitigate risk of stockouts due to variations in demand or supply chain disruptions. It acts as a buffer to ensure that there is a sufficient stock to meet the customer demand even in unexpected situations.
74. What is the Oracle Product Hub in SCM?
Ans:
Oracle Product Hub is the module that helps organisations manage the product information centrally. It provides the single source of truth for product data, supporting consistent and accurate product information across the supply chain.
75. Explain Oracle Global Order Promising (GOP) in order fulfillment?
Ans:
Oracle GOP is the module that provides a real-time visibility into product availability and promises delivery dates to the customers. It considers various factors, like inventory levels, production schedules, and transportation constraints, to make the accurate order promises.
76. Define Oracle Drop Shipments in Order Management?
Ans:
Drop shipments in Oracle Order Management refer to a process where a customer order is fulfilled directly by the supplier, without the organisation handling the product. Oracle Order Management facilitates coordination of drop shipments between the customers and suppliers.
77. What is Oracle Costing in SCM?
Ans:
Oracle Costing is used to calculate and manage costs associated with the products and manufacturing processes. It includes the features for standard costing, actual costing, and variance analysis, providing the insights into cost structures.
78. How does Oracle SCM handle collaborative planning with suppliers and partners?
Ans:
Oracle SCM includes collaboration features like Supplier Portal and Collaborative Planning to facilitate the communication and coordination with suppliers and partners. These tools help in creating a more responsive and collaborative supply chain network.
79. What is Oracle Landed Cost Management in procurement?
Ans:
Oracle Landed Cost Management helps an organisation calculate and allocate the additional costs associated with the importing goods, such as customs duties and freight charges. It provides the more accurate reflection of the total cost of procured items.
80. Explain Oracle Order promising in SCM?
Ans:
Oracle Order Promising involves the determining the availability of products and promising delivery dates to the customers based on real-time information. It considers factors like the inventory levels, production schedules, and transportation constraints to provide the accurate delivery commitments.
81. Explain Cross-Docking in Oracle SCM?
Ans:
Cross-Docking in the Oracle SCM involves unloading products from incoming shipment and directly loading them onto the outbound trucks for delivery, without the need for storage. It is the strategy to streamline distribution and reduce the handling costs.
82. How does Oracle SCM support integration of third-party logistics (3PL) providers?
Ans:
Oracle SCM supports the 3PL integration through Oracle Logistics Cloud. It enables the seamless collaboration with the third-party logistics providers for transportation management, warehouse operations, and the overall supply chain visibility.
83. What is Oracle Fusion Distributed Order Orchestration?
Ans:
Oracle Fusion DOO is the module that helps organisations manage the complex order scenarios by orchestrating an end-to-end order fulfilment process. It ensures the accurate order processing, visibility, and coordination across the various systems and channels.
84. Explain Cross-Product Line Planning in Oracle SCM?
Ans:
Cross-Product Line Planning in the SCM involves planning and optimising multiple product lines simultaneously. This approach helps organizations achieve better resource utilisation, reduce costs, and improve the overall supply chain efficiency.
85. Explain Sourcing Rules in Oracle SCM and how they influence procurement decisions?
Ans:
Sourcing Rules in the Oracle SCM define the guidelines for selecting the suppliers based on the criteria such as lead time, cost, and supplier performance. They influence the procurement decisions by providing the structured approach to supplier selection and the order fulfilment.
86. What is Oracle SCM Cloud’s Smart Contracts feature?
Ans:
Oracle SCM Cloud’s Smart Contracts feature automates and enforces predefined business rules and conditions in the supply chain transactions. It benefits transactions by reducing the manual interventions, ensuring the compliance, and enhancing efficiency of contract management.
87. Explain Cross-Channel Order Fulfilment?
Ans:
Cross-Channel Order Fulfilment in the Oracle SCM involves the fulfilling orders seamlessly across the multiple sales channels. It positively impacts customer satisfaction by ensuring consistent and efficient order fulfilment experience regardless of a sales channel.
88. What is Oracle SCM Cloud’s Global Order Promising?
Ans:
Oracle SCM Cloud’s Global Order Promising provides a centralised view of inventory and order commitments across the global supply chain. It optimises order fulfilment by considering inventory availability, production capacity, and logistics constraints to promise accurate delivery dates.
89. Describe Oracle SCM Cloud’s Order Management Cloud?
Ans:
Oracle Order Management Cloud is the module that manages an entire order-to-cash process. Key features include order capture, pricing, orchestration, and fulfilment, providing the comprehensive solution for efficient order processing.
90. What is Oracle Fusion Product Lifecycle Management (PLM)?
Ans:
Oracle Fusion PLM supports product innovation and development by managing the entire product lifecycle. It helps organizations bring products to market faster, collaborate on a design and development, and ensure compliance with the industry standards.