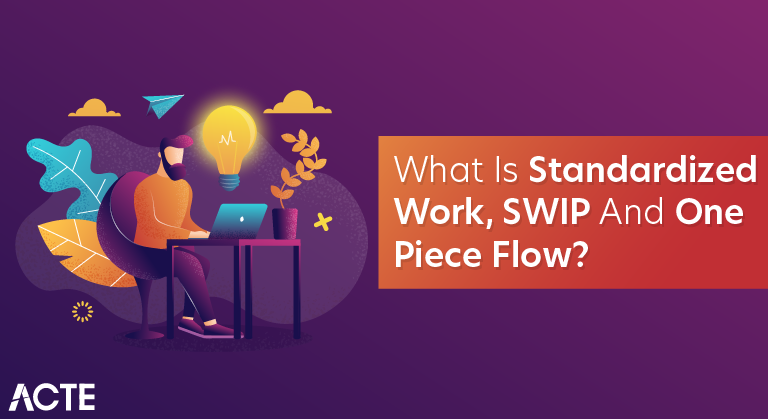
Standard Work is one of the more misunderstood concepts in Lean manufacturing. It is neither standardization nor work standards. You can learn more about Standard Work here, and here if you are new to Standard Work.
There are three elements to Standard Work:
- Takt time is a fundamental concept of Lean manufacturing that is widely understood.
- Work sequence is fairly intuitive.
- Then there is Standard Work in Process or SWIP. This is a bit trickier. Let’s dive in.
SWIP Defined
SWIP is the minimum necessary in process inventory (work in process or WIP) to maintain Standard Work. No more, no less. So how do we calculate Standard Work in Process quantity? There are a number of questions you need to ask.
Technically you can get fairly close if you say SWIP = Sum of Cycle Times / Takt Time but you still need to go back and figure out how much SWIP goes where.
So here are the step by step rules to determining SWIP:
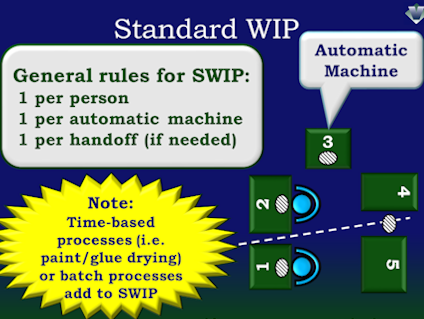
1) What is the crew size?
Since Standard Work is the most effective combination of manpower, material and machine i.e. the best known method today, based on takt, work sequence, and SWIP, by definition there should be manual work. If it’s a fully-automated “lights off” process, you really don’t have Standard Work. At that point you probably have an CNC program.
In any case, because crew size is determined as the sum of manual cycle time / takt time, you will need one piece of SWIP per person.
Rounding rule: There is no rounding, unless you have found a way to have less than a full person, in which case you round up to the nearest whole number.
2) Which processes are single-piece automatic cycle machines?
Standard Work presupposes that there is multi-process or multi-machine handling. It also presupposes that human and machine work are separated, wherever possible, and that when there is an automatic cycle, the worker will unload, load and walk away. It also presupposes that automatic cycle times are less than takt time. This means that for every automatic cycle process, there will be at least one piece of SWIP in the machine.
Rounding rule: There is no rounding since you cannot have less than a full machine, if you do… round up to the nearest whole number.
Note that these are single-piece automatic cycles, meaning that you can unload and load one piece each time. The calculation for automatic cycles with batch processes or cycle times and lead times longer than takt is different (see below).
Another way you can state this is that:
SWIP(single-piece auto) = Automatic Cycle Time / Takt Time
And then round up, but it is a waste to do this calculation since it must always be within takt, and therefore 1:1.
3) Which processes have a single-piece non-machine automatic cycle?
Non-machine automatic cycle is an awkward phrase, but this includes things like the time for paint to dry, the time for epoxy to cure, the time for hot parts to cool, etc. There may be no machine involved, but it takes a certain amount of time for something to happen “automatically” with the parts left alone.
SWIP(single-piece non-machine auto) = Automatic Cycle Time / Takt Time
Rounding rule: Always round up to the nearest whole number.
Often a turntable or a FIFO rack is used for parts needing to cure, so that the first one in (being cured the longest) is the first one out (done curing). There should be one done curing every takt, and a new one with epoxy placed in the rack or turn table each takt.
4) Which processes have a batch automatic cycle?
These are processes in which the equipment design allows you to unload and load only a batch at a time, instead of one at a time. A good example would be heat treating processes in which you need to pull a vacuum and cannot open the door for hours once the cycle starts. You take a batch of parts out, then load another batch. The cycle time per piece may be lower than takt, but the overall automatic cycle time is over takt.
In this case:
SWIP(batch auto cycle) = (Automatic time / Takt time) x 2
Rounding rule: Round up to the nearest whole number, then multiply by 2. Why times two? Any time you have a batch process that does not allow you to take one or add one each takt, you will need an extra quantity of complete parts. Think of it as a pulley and pail used to get water from a well. Sometimes called tsurube system for “well bucket” in Japanese, it is the idea of having one bucket at the end of the rope in the bottom of the well, full of water, and one bucket at the top, full of water. During takt you empty out the bucket one by one, and fill it back up one by one, getting ready to lower the bucket into the well. The analogy is not perfect since the water is in the bucket before it goes down the well, and there is a transformation that happens to the bucket in the well (batch process).
In formulas 2, 3 and 4 there is no manual cycle time included in the calculation. Why? This is because rule #1 takes care of that. Since every manual cycle time must be within takt by definition of Standard Work, and since the unload / load time will involve one piece, there is no need to add manual time back into the calculation (in most cases).
5) Which processes leave the cell and are processed at a vendor operation or at another department?
The concept of the pulley & pail is the same as rule #4. The formula is slightly different, since instead of the automatic cycle time you need to determine the lead time which includes time to get the order to the outside process, time in queue, time to transport it back, etc. and can be days even for processes that take only minutes.
SWIP(vendor op) = (Lead time / Takt time) x 2
Rounding rule: Round up to the nearest whole number, then multiply by 2.
This type of pulley & pail system will allow you to flow through a batch process, vendor operations or shared resource and maintain one piece flow and Standard Work, with minimum WIP.
It’s really not that complicated, just a series of “if… then” statements. The key thing is to think in one piece flow and be able to see past so-called monuments, outside processing and shared equipment which seem to prevent continuous flow.
The Final Ugly Equation
So when it comes time to answer “How to calculate the SWIP quantity?” the answer is slightly ugly:
SWIP(total) = SWIP(manual) + SWIP(single-piece auto cycle)+SWIP(single-piece non-machine auto)+SWIP(batch auto cycle)+ SWIP(vendor op)
Someone who is a trained mathematician (volunteers?) could probably state this more elegantly as an algorithm.
Exceptions to the Rule
There are several special cases where there are additional considerations to the rules above. One example is when the direction of workflow (manual work sequence) is the reverse of the process flow (material flow). Some labor-optimized cells that have unbalanced automatic cycle times can improve labor productivity by having an extra piece ready to load at the previous process, in order to eliminate waiting for the machine cycle to end.
Another exception to rule #1 is if the operator is unloading and loading a series of batch processes (the type for rule #3) and the transfer quantity is not one piece but a batch. In that case there will not be one in hand. But we are starting to approach arcana…