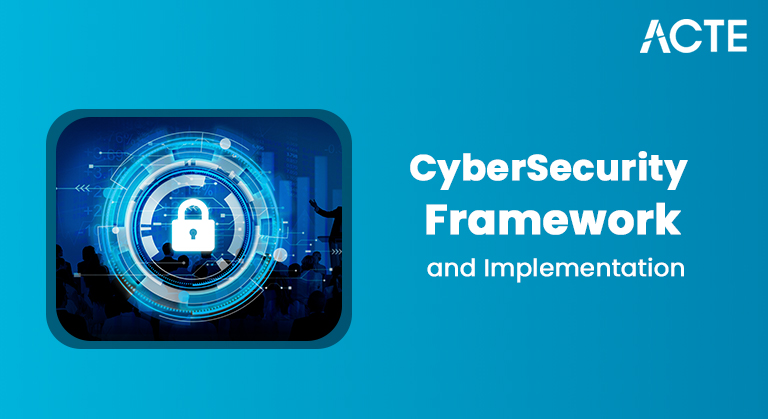
- Introduction to Quality Assurance and Quality Control
- Definition of Quality Assurance (QA)
- Definition of Quality Control (QC)
- Fundamental Differences Between QA and QC
- Objectives and Focus of QA vs QC
- Processes and Techniques in QA and QC
- Roles and Responsibilities in QA and QC
- Importance of Both QA and QC in Business Success
- Conclusion
Introduction to Quality Assurance and Quality Control
Quality management is an essential discipline within any organization that aims to deliver products or services that meet or exceed customer expectations. It involves systematic processes to ensure that all aspects of production or service delivery adhere to predefined quality standards. Within quality management, two closely related but distinct practices exist: Quality Assurance (QA) and Quality Control (QC). While both focus on maintaining product or service quality, the difference between quality control and quality assurance lies in their approaches, goals, and methods, which differ significantly. Understanding the nuances between QA and QC is critical for organizations striving for excellence and customer satisfaction.
Are You Interested in Learning More About Software Testing? Sign Up For Our Software Testing Certification Training Today!
Definition of Quality Assurance (QA)
Quality Assurance refers to the proactive, process-oriented approach aimed at preventing defects and ensuring quality throughout the production lifecycle. QA involves designing and implementing systematic procedures and standards that guide the entire workflow to avoid errors or inconsistencies. It emphasizes continuous improvement by analyzing processes and establishing controls to minimize variability. Essentially, QA ensures that the right steps are in place from the start to produce quality outputs consistently. This approach fosters a culture of quality embedded in every phase, from design to delivery, thereby reducing the chances of defects before they occur.
Definition of Quality Control (QC)
- Quality Control, on the other hand, is a reactive, product-oriented approach focused on identifying defects in the final outputs. QC involves inspecting, testing, and measuring products or services after production to verify that they meet specified quality criteria.
- It serves as a checkpoint to detect flaws and deviations, allowing corrective actions to be taken before the product reaches the customer. Unlike QA, which emphasizes prevention, QC concentrates on detection and correction of errors.
- QC activities typically include sample testing, visual inspections, functional testing, and statistical process control. By catching defects early, QC helps minimize the risk of defective products causing customer dissatisfaction or harm.
- The core distinction between Quality Assurance and Quality Control lies in their focus and timing within the production process. QA is process-centric and proactive; it focuses on designing and refining processes to prevent defects.
- QC is product-centric and reactive; it focuses on identifying and fixing defects in finished goods. QA is a managerial function that defines policies, standards, and procedures to ensure quality, whereas QC is an operational function that implements those procedures to verify compliance.
- The difference between quality control and quality assurance is especially clear in this contrast QA works to prevent problems before they arise, while QC addresses issues after products are made.
- QA encompasses the entire production lifecycle, while QC is typically limited to the final inspection or testing phase. These differences highlight that both QA and QC are complementary parts of a holistic quality management system, working together to achieve overall quality goals.
- Highlight that the difference between quality control and quality assurance isn’t about choosing one over the other, but understanding how they complement each other within a holistic quality management system, working together to achieve overall quality goals.
- Quality Assurance professionals typically hold roles such as QA Manager, Process Engineer, or Quality Systems Analyst. Their responsibilities include developing quality policies, conducting process audits, facilitating training, and driving continuous improvement initiatives.
- They work closely with production, design, and management teams to embed quality into every step. Quality Control personnel, including QC Inspectors, Test Engineers, and Quality Technicians, are responsible for inspecting products, conducting tests, recording defects, and reporting nonconformities.
- They ensure that products meet specifications before release and collaborate with QA teams to address quality issues. Both roles require strong analytical skills, attention to detail, and communication abilities.
To Explore Software Testing in Depth, Check Out Our Comprehensive Software Testing Training Course To Gain Insights From Our Experts!
Fundamental Differences Between QA and QC
Objectives and Focus of QA vs QC
Quality Assurance aims to build confidence in the processes that deliver products or services. Its objectives include standardizing procedures, training personnel, and continuously improving workflows to eliminate sources of error. The focus is on prevention, compliance, and process improvement. By contrast, Quality Control aims to ensure that the final product conforms to customer requirements and regulatory standards. Its objectives include identifying defects, ensuring product functionality, and preventing defective products from reaching the market. The focus is on inspection, testing, and correction. While QA ensures the right process, QC ensures the right product. To explain quality assurance and quality control clearly, QA emphasizes proactive process management while QC deals with reactive product inspection. Focus is the primary distinction between QA and QC. The goal of QA is to create and uphold the proper procedure. It guarantees that each step is completed correctly the first time. By doing this, mistakes are avoided before they occur. QC, however, focuses on the final product. After the process is finished, it seeks to identify and correct errors. One way to explain quality assurance and quality control is by understanding their different questions: QA asks, Are we doing the right things? whereas QC asks, Is the product right? Both are essential to producing a dependable product. When combined, they assist businesses in creating safe, efficient, and client-focused products and services. Errors could occur more frequently without QA, which would increase expenses and result in unhappy clients.
Want to Pursue a Software Testing Master’s Degree? Enroll For Software Testing Master Program Course Today!
Processes and Techniques in QA and QC
QA processes typically involve activities such as process audits, documentation reviews, risk management, training, and implementation of quality management frameworks like ISO 9001 or Six Sigma. Techniques include process mapping, root cause analysis, preventive maintenance, and benchmarking. QC processes include activities like product inspections, sample testing, statistical quality control (SQC), control charts, and acceptance sampling. Tools such as checklists, defect tracking systems, and laboratory testing equipment are common in QC. To explain quality assurance and quality control thoroughly, it’s essential to understand that QA relies on process metrics while QC relies on product metrics, even though both use data analysis. Quality control (QC), on the other hand, is concerned with verifying that the finished product satisfies both legal requirements and customer expectations. Finding mistakes or flaws before a product is delivered to a customer is the primary goal of quality control. Frequently, samples, testing, or inspection are used to accomplish this. A food manufacturer might, for instance, test batches of canned food to ensure that they adhere to safety regulations. Before the product is shipped, they take action to address any flaws they discover. These practical examples help explain quality assurance and quality control in action QA works behind the scenes to prevent issues, while QC catches problems before they reach the customer. Reactive in nature, quality control seeks to find and fix errors that evade the process. Its objective is to ensure that only goods that meet specifications are released onto the market. For instance, a car manufacturer may check each vehicle to make sure it is assembled correctly.
Roles and Responsibilities in QA and QC
Despite technological advancements, warehousing and logistics face numerous challenges:
Importance of Both QA and QC in Business Success
To maximize performance, companies should adopt best practices such as: Implementing Integrated Technology Solutions to connect warehousing and logistics functions seamlessly. Continuous Training of Workforce to enhance skills and safety awareness. Optimizing Warehouse Layouts for efficient flow and space utilization. Adopting Lean Principles to reduce waste and streamline processes. Building Strong Relationships with Carriers and Suppliers to improve reliability and flexibility. Regularly Monitoring KPIs such as order accuracy, cycle time, and transportation costs to drive continuous improvement. Planning for Scalability and Flexibility to adapt to changing market conditions. By embracing these practices, organizations can build resilient, responsive, and cost-effective warehousing and logistics operations.
Conclusion
Think of quality assurance as your first line of defense, making sure everything runs smoothly right from the beginning. Then, quality control steps in like a safety net to catch any problems before they reach your customers. This coordinated effort clearly reflects the difference between quality control and quality assurance QA proactively prevents issues, while QC reacts to them. Working together, these two methods build a solid system that ensures your products are safe and dependable. But perhaps the most vital part? Consistently doing great work builds lasting trust with your customers and that trust is the foundation of a business that stands the test of time. When you weave these well-proven quality steps into how you do things every day, you’ll see real improvements in how well you’re doing and how happy your customers are with each step you take. This will really help you stand out from the competition.