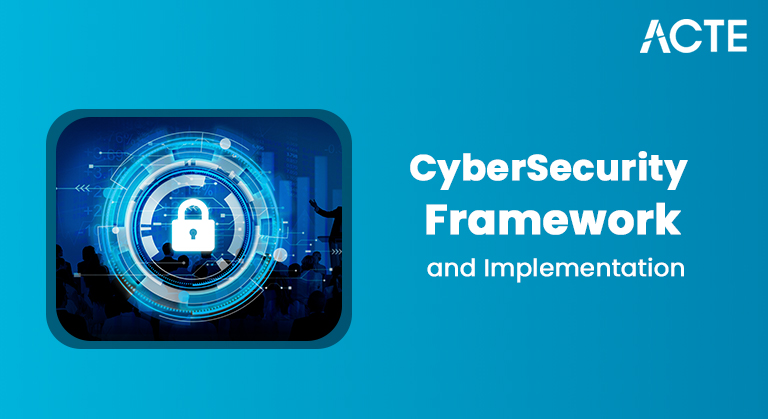
- Introduction to Supply Chain Management Process
- Key Components of the Supply Chain Process
- Procurement and Supplier Management
- Production Planning and Scheduling
- Inventory Management and Control
- Logistics and Distribution
- Order Fulfillment and Customer Service
- Conclusion
Introduction to Supply Chain Management Process
The supply chain management process involves the coordinated flow of goods, information, and finances as products move from raw material suppliers all the way to end customers. This complex process is designed to ensure that products are produced and delivered efficiently, fulfilling customer demands while minimizing costs and waste. Effective management of the supply chain is essential for businesses to remain competitive in their industries. It helps improve operational efficiency by streamlining activities, reducing delays, and optimizing resource utilization. Moreover, a well-managed supply chain enhances customer satisfaction by ensuring timely delivery of quality products and services. The supply chain management process, supported by PMP Training, consists of several interconnected stages that work together to achieve these goals. Strategic planning is the foundation of the process, involving decisions related to sourcing suppliers, production scheduling, inventory levels, and logistics. This stage requires a deep understanding of market conditions, customer needs, and organizational capabilities. Execution follows planning and includes the actual procurement of materials, manufacturing of products, and transportation to distribution centers or retailers. Accurate and timely information sharing is critical during this stage to coordinate activities and prevent bottlenecks. Continuous monitoring and evaluation are also key components of the supply chain process. Companies must track performance metrics such as delivery times, inventory turnover, and order accuracy to identify areas for improvement. Challenges such as supply disruptions, fluctuating demand, and global trade complexities require businesses to be agile and adaptive. Best practices in supply chain management include leveraging technology for real-time visibility, fostering collaboration among partners, and investing in risk management strategies. Understanding and optimizing each stage of the supply chain management process enables companies to build resilient, efficient, and customer-focused supply chains that drive long-term success.
Interested in Obtaining Your PMP Certificate? View The PMP Certification Training Offered By ACTE Right Now!
Key Components of the Supply Chain Process
A typical supply chain management process includes several key components that must function together to ensure smooth and efficient operations. These components include procurement, production, inventory management, logistics, order fulfillment, and customer service. Each plays a critical role in moving products from suppliers to end customers while meeting business goals. Procurement is the process of sourcing raw materials and managing relationships with suppliers to ensure quality inputs are available when needed. It involves negotiating contracts, evaluating suppliers, and monitoring performance to reduce costs and risks. Production planning follows procurement and focuses on scheduling manufacturing activities, a process that can be better managed when you Learn Burndown Charts With Jira. This step ensures that products are made on time, within budget, and according to quality standards. Effective production planning helps optimize the use of labor, equipment, and materials while minimizing downtime. Inventory management is responsible for controlling stock levels throughout the supply chain. It balances having enough inventory to meet demand without tying up excessive capital in excess stock. Accurate forecasting and real-time inventory tracking are vital to this component. Logistics handles transportation and warehousing of goods. It ensures that products move efficiently between suppliers, production sites, warehouses, and customers. This includes selecting carriers, managing routes, and optimizing storage. Order fulfillment is the process that guarantees customers receive their orders accurately and on time. It involves picking, packing, and shipping products. Finally, customer service supports post-sale activities by addressing inquiries, handling returns, and maintaining customer satisfaction.
Integration of these components through effective communication and robust information systems is essential. When these elements work in harmony, companies can achieve key supply chain objectives such as cost reduction, quality assurance, and responsiveness. A coordinated approach helps build a resilient and customer-focused supply chain capable of adapting to market changes and sustaining competitive advantage.
Procurement and Supplier Management
- Critical First Step: Procurement is the initial and vital phase of the supply chain, responsible for securing the raw materials or components necessary for production.
- Supplier Identification and Evaluation: This stage involves finding potential suppliers, assessing their capabilities, quality standards, and pricing to select the best fit for the company’s needs.
- Supplier Management: Procurement includes negotiating contracts, maintaining strong relationships, and continuously monitoring supplier performance to ensure reliability.
- Risk Reduction: Effective procurement minimizes supply disruptions by ensuring dependable sources and diversifying suppliers where needed, which is a principle also emphasized in What Is Scrum XP.
- Sustainability Support: Incorporating sustainability criteria in procurement promotes environmentally and socially responsible sourcing, aligning with corporate social responsibility goals.
- Strategic Sourcing and Collaboration: Employing strategies like strategic sourcing and fostering collaboration with suppliers helps optimize costs, improve quality, and drive innovation.
- Compliance and Ethics: The procurement process must comply with legal regulations and ethical standards, ensuring transparency, fairness, and accountability throughout the supply chain.
- Aligning Production with Demand: Production planning ensures manufacturing activities match demand forecasts and available capacity to meet customer needs efficiently.
- Determining Production Details: The supply chain management process, supported by PMP Training, consists of several interconnected stages that work together to achieve these goals.
- Materials Requirement Planning (MRP): MRP systems help schedule material deliveries and production tasks, optimizing inventory levels and preventing shortages.
- Lean Manufacturing: Lean techniques focus on eliminating waste and improving resource utilization, contributing to cost reduction and higher efficiency.
- Minimizing Lead Times: Effective planning reduces the time between order receipt and product completion, enhancing responsiveness to market demands.
- Scheduling Coordination: Production scheduling organizes machine use, labor shifts, and maintenance to maximize equipment availability and production throughput.
- Flexibility: Maintaining adaptable production plans allows manufacturers to respond quickly to changes in customer demand or disruptions in supply, ensuring continuity.
- Movement, Storage, and Handling: Logistics manages the flow, storage, and handling of goods throughout the supply chain, ensuring materials and products move efficiently.
- Inbound Logistics: This includes receiving raw materials and components from suppliers and transporting them into manufacturing or storage facilities.
- Internal Logistics: Focuses on the movement of goods within warehouses or production facilities to support manufacturing and order fulfillment processes.
- Outbound Logistics: Involves delivering finished products to customers, managing transportation, and ensuring timely and accurate deliveries, which can impact the Project Manager Salary in India .
- Cost and Speed Optimization: Efficient logistics reduces transportation and storage costs, improves delivery speed, and enhances overall reliability and customer satisfaction.
- Distribution Strategies: Selecting the right transportation modes, managing warehouses effectively, and optimizing delivery routes are key to streamlining distribution operations.
- Third-Party Logistics and Sustainability: Third-party logistics providers (3PLs) offer specialized expertise to improve efficiency, while environmental concerns like reducing carbon emissions are increasingly important in logistics planning.
To Earn Your PMP Certification, Gain Insights From Leading Blockchain Experts And Advance Your Career With ACTE’s PMP Certification Training Today!
Production Planning and Scheduling
Inventory Management and Control
Inventory management plays a crucial role in balancing the need to have enough stock to meet customer demand while avoiding the costs associated with holding excessive inventory. Maintaining this balance is essential because too little inventory can lead to stockouts, lost sales, and dissatisfied customers, whereas too much inventory increases storage costs, ties up capital, and can result in obsolete or expired products. Effective inventory management involves carefully tracking inventory levels across warehouses and stores, establishing appropriate reorder points, maintaining safety stock to protect against uncertainties, and monitoring turnover rates to understand how quickly products move. Accurate inventory control helps companies prevent costly disruptions and inefficiencies in the supply chain, aligning with the Phases of Project Management. To achieve this, many businesses use advanced technologies such as barcode scanning and Radio Frequency Identification (RFID) systems. These tools provide real-time visibility into stock levels, locations, and movement, greatly improving accuracy and reducing manual errors. Additionally, inventory management software integrates these data points, enabling better forecasting, reporting, and decision-making. Several inventory policies and methodologies help optimize stock levels. Just-In-Time (JIT) is a strategy aimed at reducing inventory by receiving goods only when needed for production or sales. Economic Order Quantity (EOQ) is a mathematical approach that determines the optimal order size to minimize total inventory costs, including ordering and holding expenses. Both policies contribute to efficient inventory practices but require careful implementation to avoid risks. Regular physical audits and cycle counting are necessary to maintain data integrity. These activities help detect discrepancies caused by theft, damage, or recording errors, and ensure that inventory records reflect actual stock. By combining these practices, companies can improve inventory accuracy, reduce waste, and enhance overall business performance.
Looking to Master PMP? Discover the PMP Master Program Training Course Available at ACTE Now!
Logistics and Distribution
Order Fulfillment and Customer Service
Order fulfillment is a vital process that encompasses receiving, processing, and delivering customer orders accurately and within the promised timeframe. This process begins with order entry, where customer requests are recorded into the system. Once an order is received, the picking stage involves selecting the correct items from inventory. After picking, the products are carefully packed to ensure they arrive in good condition. Shipping follows packing and involves coordinating transportation to deliver the order to the customer’s specified location. Finally, delivery confirmation verifies that the order has reached the customer successfully. Each of these steps must be executed efficiently to meet customer expectations and maintain satisfaction. Efficient order fulfillment directly contributes to improved customer satisfaction and loyalty. When customers receive their orders promptly and without errors, their trust in the company strengthens, encouraging repeat business and positive word-of-mouth referrals, which explains Why Do Scrum Masters Get Paid so Much. Conversely, delays or mistakes in order fulfillment can lead to frustration, complaints, and lost sales. Therefore, businesses prioritize optimizing this process to ensure smooth and reliable delivery experiences. Customer service plays a complementary role by addressing inquiries related to orders, handling returns or exchanges, and providing after-sales support. Effective customer service helps resolve issues quickly and maintains a positive relationship even when problems occur. Technologies such as order management systems (OMS) and customer relationship management (CRM) tools are essential in facilitating seamless interactions across fulfillment and service functions. OMS helps track orders from receipt to delivery, while CRM tools manage customer communication and feedback. Real-time tracking and transparent communication are increasingly important components of order fulfillment. Providing customers with up-to-date information about the status of their shipments builds trust and reduces uncertainty. Clear communication also allows companies to proactively address potential delays, further enhancing the overall customer experience.
Preparing for a PMP Job Interview? Check Out Our Blog on PMP Interview Questions and Answers
Conclusion
The supply chain management process is a complex and interconnected system that plays a critical role in driving business success. It ensures that products and services move efficiently from suppliers through production and distribution to reach end customers. Each stage in this process, from procurement to manufacturing, logistics, inventory management, order fulfillment, and customer service, must operate in coordination to deliver value. Understanding these stages in detail allows organizations to identify opportunities for improvement, streamline operations, reduce costs, and enhance customer satisfaction. Procurement sets the foundation by securing quality raw materials and building strong relationships with reliable suppliers. Production planning ensures that manufacturing processes align with demand forecasts and resource availability. PMP Training helps ensure inventory management balances supply with demand while minimizing carrying costs. Logistics organizes transportation and warehousing to move products efficiently. Order fulfillment and customer service round out the process by ensuring timely delivery and positive customer experiences. Each element contributes to a well-functioning supply chain that supports organizational goals. In today’s global and fast-paced business environment, supply chain processes must be flexible and adaptable. Technological advancements such as artificial intelligence, real-time data analytics, cloud computing, and the Internet of Things are transforming how supply chains are managed. These tools enable better decision-making, increased visibility, and more agile responses to disruptions. At the same time, evolving market dynamics and customer expectations demand greater transparency, speed, and sustainability. To remain resilient and competitive, organizations must continuously assess and refine their supply chain strategies. Embracing digital tools, fostering collaboration among stakeholders, and committing to continuous improvement are essential steps. A responsive and well-managed supply chain not only supports daily operations but also contributes to long-term business growth and success in a rapidly changing global landscape.