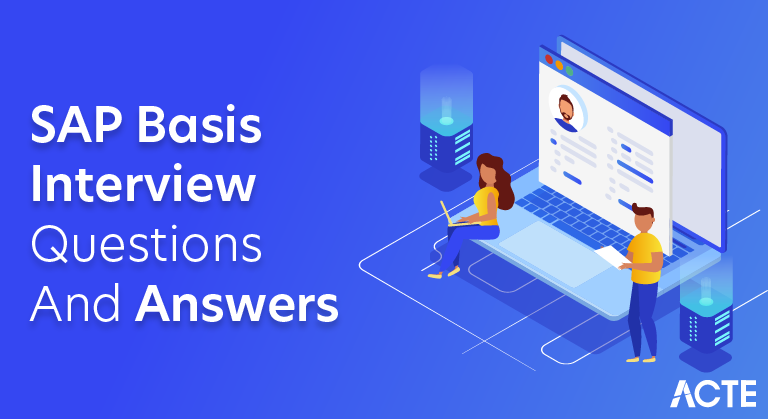
Six Sigma is a data-driven methodology aimed at improving the quality of processes by identifying and eliminating defects. It uses statistical tools and techniques within a structured framework, primarily through the DMAIC and DMADV methodologies, to enhance efficiency, reduce variability, and ensure consistent quality. Six Sigma’s goal is to achieve near-perfect processes, with a defect rate of no more than 3.4 per million opportunities.
1. Describe Six Sigma.
Ans:
Six Sigma (6σ.. is a collection of methods and resources for raising process quality. This methodical and data-driven approach may be used in every Process, from transactional to manufacturing, from services to products. Since Bill Smith initially presented it in 1986 while he was employed at Motorola, it has grown in acceptance across a variety of sectors and businesses to enhance business operations.
2. List a few of the fundamental Six Sigma concepts.
Ans:
Aspect | DMAIC | DMADV |
---|---|---|
Purpose | Used for improving existing processes. | Used for designing new processes or products. |
Acronym | Define, Measure, Analyze, Improve, Control. | Define, Measure, Analyze, Design, Verify. |
Application | Typically applied in process improvement projects. | Typically applied in new product or process development projects. |
Emphasis | Focuses on problem-solving and optimization of existing processes. | Emphasizes on creating new processes or products with little to no defects. |
3. What does Six Sigma mean by COP?
Ans:
The price paid for creating flaws is known as the Cost of Poor Quality or COPP. The following factors are involved in this cost. Closing the gap between the expected and actual quality of the good or service; The opportunity cost. Costs associated with labour; rework; disposal; and additional materials A reduction in sales or revenue; Additional utility cost. COP excludes the following.
4. Could you please define DPMO and DPPM?
Ans:
- Defects Per Million Opportunities is referred to as DPMO, and Defective Parts Per Million as DPPM.
- In this case, an item’s flaws or discrepancies (more than one problem. They are considered defects.
5. Define The Pareto Principle.
Ans:
The Pareto principle, also known as the 80/20 Rule, asserts that around 80% of the cone fences stem from 20% of the causes for numerous occurrences. Eighty percent of the outcome comes from twenty percent of the input. Labourers’ efforts produce 80% of the output; 20% of the consumers generate 80% of the revenue; 80% of the traits are caused by 20% of the utilization; and 20% of the flaws cause 80% of the crashes. The idea that 20 + 80 = 100 is a common misunderstanding, although it’s only sometimes valid because most things aren’t 1/1.
6. List a few of the Six Sigma Quality Management tools.
Ans:
Numerous tools are available for quality management. Among them are the following:
- Taguchi methodologies;
- CTP Tree;
- SOPOC analysis;
- COPIS analysis and cost-benefit analysis.
- Value stream mapping;
- Workplace visualisation
7. What types of variations are employed in Six Sigma?
Ans:
The two types of variation are as follows.
- Mean
- Median
- Scope
- Attitude
8. Who is on the Six Sigma implementation team?
Ans:
The following individuals typically comprise the Six Sigma implementation team.
- Six Sigma Champion;
- Six Sigma Deployment Leader
- Master Black Belt (MBB. Six Sigma
- Black Belt (BB. Six Sigma
- Green Belt (GB. Six Sigma
- Yellow Belt (YB. Six Sigma
9. How do the Six Sigma DMAIC and DMADV techniques vary from one another?
Ans:
When a process or product is already in place at your business but isn’t fulfilling client requirements, you should use the DMAIC technique rather than the DMADV methodology. Or it needs to be operating at a sufficient level. The following situations call for the application of the DMADV methodology rather than the DMAIC methodology. Your organization needs to design a new process or product because one currently doesn’t exist. Despite being optimized—whether with DMAIC or not—the current product or Process still falls short of customer specifications or Six Sigma standards.
10 Could you elaborate on the idea of the Ishikawa diagram and fishbone diagram?
Ans:
It is a visual aid for classifying possible sources of an issue in order to determine its underlying causes. The name of the diagram comes from how much it resembles a fish skeleton. An issue or effect is shown as the fish’s “head,” with the possible causes emerging from its main spine like “bones.” See our tutorial for using the fishbone diagram for more details.
11. Describe the procedure of load testing.
Ans:
- It is the act of measuring and placing demands on a computational equipment or software system.
- Load testing simulates a “load” or demand on your web application using specialized testing software to make sure it runs stable.
- Transaction response times will be used by testing software to gauge your web application’s capacity during a load test.
12. Which three procedures make up root cause analysis?
Ans:
Root cause analysis follows these three steps. Open step. In this first stage, all team members convene and engage in a brainstorming session to discuss all potential outcomes. Narrow step. Taking into account our present sigma performance, all potential explanations and situations are whittled down during this phase. Close-step: During this phase, the project team will validate each explanation on the whittled list for the current sigma performance.
13. How do CPK and PPK differ from one another?
Ans:
Answer. Ppk, or process performance index, determines whether the sample produced by the Process is capable of satisfying customer requirements (CT.s. Cpk, or process capability index, measures how close a process is operating to the boundaries of its specifications in relation to the Process’s inherent unpredictability.
14. What does the standard deviation mean?
Ans:
- The average spread is measured by the standard deviation.
- Data around the mean are used to determine the degree of variation in a process or a set of observations.
- The standard deviation, abbreviated as σ, quantifies the degree of dispersion of the data with respect to the mean.
15. What is the Process of sigma calculation?
Ans:
The variation in a process with respect to client requirements is measured by process sigma. 1. As determined by your clients, ascertain the top and lower specification limitations for the Process. 2. Determine the standard deviation and mean of the Process. 3. To determine the Sigma Level, use the formula below. [(Process Mean Upper Limit / Standard Deviation
16. What is a standard deviation?
Ans:
The 1.5 sigma shift adjustment considers the effects of several manufacturing cycles on each Process. Sigma shift acts as a buffer or margin, taking into consideration the unavoidable process drift and ensuring that the finished product’s quality or service stays high even in cases where the Process deviates midway.
17. Explain Regression. When is it applied?
Ans:
The method of defining how a set of input variables and an output variable are related is called regression analysis. Regression can take many different forms, depending on the type of underlying data. Among them are multiple linear Regression, simple linear Regression, Curvilinear Regression, Logit Regression, and Probit Regression.
18. What distinguishes a flaw from a defective thing?
Ans:
- Any non-conformance of the product’s unit with the defined requirements is considered a defect.
- A piece of work that has one or more defects is considered faulty.
- Generally speaking, a product can be defective and yet work.
- A product that has flaws is deemed unacceptable and is unable to operate.
19. How do Process and Product Reports Differ From One Another?
Ans:
While the Product Report applies to discrete data and may thus be used for any form of distribution, the Process Report is utilized with continuous data that follows a bell-curve distribution. Through the construction of its examples, the method acts as a template that may be used to guide the undertaking. A process is a collection of instructions that directs a project to produce a useful product; this is the primary distinction between a process and a product.
20. Describe the meaning of an affinity diagram.
Ans:
The affinity diagram is a graphic aid used in brainstorming and problem-solving sessions. The tool’s main purpose is to logically arrange concepts or pieces of information according to their connections or commonalities. It has the following functions.
21. What do the R and X bar charts represent?
Ans:
They consist of a pair of charts, which are often employed as a statistical process control technique to track the behavior and results of the Process across time. If a process is stable and predictable, it can be ascertained using the R chart, X-bar chart, and standard chart for variable data. The R chart displays the changes in the subgroups’ Range over time, while the X-bar chart displays changes in the mean or average over time. It is also employed to track the results of theories related to process improvement.
22. Describe brainstorming and flowcharting.
Ans:
- A flowchart, which is a diagram, shows the crucial steps of an event, Process, or workflow.
- Using the brainstorming technique. ue, one can swiftly come up with uni. ue or creative ideas regarding a process, issue, good, or service.
23. What is Lean Six Sigma?
Ans:
Lean Six Sigma is a technique for performance enhancement that focuses on reducing variation and eliminating elements that don’t help the Process. This way of thinking depends on cooperative teamwork. Lean Six Sigma enhances customer happiness and superior quality.
24. What advantages may Lean Six Sigma offer?
Ans:
One of the essential questions for a lean Six Sigma is this one.
- Describe the primary advantages, such as.
- Defect elimination;
- Large team management;
- Better work prioritising;
- Improved project visibility at the team level;
- Enhanced team productivity; and
- Time savings.
- Study up on Lean.
25. What are the Lean Six Sigma tools?
Ans:
A variety of Lean Six tools Sigma comprises. FMEA – Regression analysis, value stream mapping, poka-yoke (mistake-proofing or unintentional error prevention., kaizen (continuous improvement., and Pareto charts Additionally, Go Here Lean Sigma versus Six Sigma
26. Which Six Sigma quality levels are there?
Ans:
A process’s quality can be measured using the Six Sigma quality-level approach. Each sigma level is associated with multiple acceptable faults per million, and the process accuracy reaches its optimal sigma level when there are 3.4 defects per million opportunities. For each sigma level, the acceptable Range of faults per million is. 1–6,90,000; 2–3,08,537; 3–66, 807; 4–6, 210; 5–233; 6 — 3.4.
27. Define SIPOC.
Ans:
Suppliers, Inputs, Processes, Outputs, and Customers are all referred to as SIPOCs. This tool generates a process map from data from these five segments, offering a high-level summary of a Six Sigma project. Nowadays, many businesses employ the opposite term, COPIS, which prioritizes customers and explains their worth to the company.
28. In Six Sigma, what is MAIC?
Ans:
- MAIC stands for Measure. Describes how to use real data to quantify and benchmark any process.
- Analyse. This involves determining the core source of any issue with statistical tools.
- Enhance. Concentrate on resolving the issue at its source.
- Control. This refers to monitoring problems to prevent them from happening again and maintain the gains.
29. In a Six Sigma process, what is DFSS?
Ans:
The abbreviation for Define for Six Sigma is DFSS. It is an enhancement of the procedure. system that entails creating a service or product from scratch using Six Sigma quality standards. A different way to develop new products or processes is Design for Six Sigma (DFSS), which uses a variety of methods. Define, Measure, Analyze, Improve, and Control, or DMAIC, is used in traditional Six Sigma.
30. Describe RASI or ARMI.
Ans:
The acronym for Approver, Resource, Member, and Interested Party (ARMI) is a project management tool for listing the participants and the key areas of responsibility for a project. The four levels of support—approver, resource, member, and interested party—that can be allocated to different stakeholders are referred to as ARMI. Approver: The person whose approval is necessary in order to proceed with the project.
31. What is a plan for gathering data?
Ans:
In order to gather all of the important data for a system, a data collection plan is utilised. It includes
- A data collection strategy is a road map for determining what data you need, how you’ll collect it, and how you’ll evaluate it.
- Type of data that needs to be obtained or collected.
- Various data sources for evaluating a data set. Ensuring targeted, dependable, and effective data collecting is the main goal in order to deliver insightful information for your project or study.
32. What is MSA?
Ans:
- Measurement System Analysis (MSA) is the full name of the discipline. MSA can verify the accuracy of a measurement system.
- It assesses the precision, accuracy, and regarding the project.
33. How well-versed are you in the Six Sigma Top-down approach?
Ans:
It’s a Six Sigma deployment approach that lays the groundwork for common terminology and comprehension while also being in line with corporate strategy and customer objectives. However, the main drawback of this method is its wide scope, which makes it challenging to complete within the allotted time. The top-down method cascades to different levels from higher levels, typically top management. It defines the strategic direction or overarching goals first, then breaks them down into specific tasks. At the highest level, all planning is completed.
34. What is VSM?
Ans:
- This is Value Stream Mapping’s abbreviation.
- Using this methodology, wastes in a process may be eliminated, and the information flow needed to supply a good or service can be mapped out.
- Value stream mapping, often known as VSM, is a lean manufacturing technique that involves the analysis, planning, and management of the information and material flow necessary to deliver a product to a customer.
35. What is an affinity diagram?
Ans:
An affinity diagram is an analytical technique for grouping or clustering ideas into smaller groups. These concepts are typically the result of brainstorming or discussion sessions and are applied to the analysis of difficult problems. An affinity diagram is a visual aid that can be used to arrange ideas from a brainstorming session. It is sometimes referred to as an affinity map or affinity chart. You’ll group concepts into many categories. Or groups according to how they relate to each other.
36. Describe the distinction between a boxplot and a histogram.
Ans:
A histogram graphically represents the free agency distribution of numerical data, and a box plot summarises the key elements of continuous data distribution. While box plots are less detailed and take up less space, they allow for the comparison of numerous datasets, while histograms are better at revealing the underlying distribution of the data.
37. In a Six Sigma project, what are the main and secondary metrics?
Ans:
A Six Sigma project’s primary and secondary metrics serve as success indicators. Primary metrics track the procedures that are in line with the corporate objective. The time it takes to finish a project and/or process flaws are examples of measurable processes. Conversely, secondary indicators have an indirect relationship with a business goal. They offer a comprehensive view that aids in enhancing a Six Sigma project. Secondary measurements make sure the processes function properly, while primary metrics concentrate on reaching goals.
38. What is the significance of metrics in a Six Sigma project? Which model would you select to ensure that metrics are implemented successfully?
Ans:
- Metrics are helpful in guiding future decision-making and Performance. They are necessary for processes to be efficient and impartial.
- Metrics utilizing the SMART model can be implemented to guarantee a Six Sigma project’s success. Specific, Measurable, Achievable, Relevant, and Time-based is what SMART stands for.
- This comprehensive approach guarantees that the objectives can be met without resorting to harmful behavior.
39. In Six Sigma, what is performance testing? How does it vary from testing loads?
Ans:
A performance test evaluates a system’s dependability and responsiveness under increased workload conditions. Performance testing includes load testing, while load testing can also be done independently. To put it another way, load testing assesses the system’s capability for operation, whereas performance testing ascertains whether the system operates as intended.
40. Describe the significance of a Six Sigma project’s RACI matrix.
Ans:
The abbreviation for Responsible:
One who is assigned a task is RACI. Accountable. A person who delegated work to others. Experts in the relevant field are consulted to guide task performers. Knowing when a task is finished makes one informed. A matrix provides RACI Organizational clarity. Clear role definition and effective teamwork are essential for efficiently completing projects.
41. Describe the Nominal Group Method.
Ans:
It serves as a framework for collaborative decision-making. The method considers how the majority in that group, as opposed to the minority, identify problems. The term “nominal” group technique.ue (NGT. Refers an or) refersversion of a small-group consensus-building conversation. NGT asks participants to rank the thoughts or proposals made by every group member after they have had a chance to react to inquiries from thqueriesor.
42. What does statistical process control mean to you?
Ans:
Six Sigma includes Statistical Process Control (SPC). It regularly monitors, regulates, and optimizes operations to improve them. This makes it possible for the Process to run more smoothly and produce more items that meet specifications while using less scrap.
43. What is the acronym for TRIZ? Why ought you to put it to use?
Ans:
- The Theory of Inventive Problem Solving is abbreviated as TRIZ.
- It examines particular issues to find recurring patterns in other industries in search of a potential fix.
- When standard Six Sigma tools are not enabling a project to go in the intended direction, TRIZ is required.
44. In Six Sigma, what is a scatter plot diagram?
Ans:
Two distinct variables are represented graphically in a scatter plot. The dependent variable typically lies along the vertical axis, whereas the independent variable typically lies on the horizontal axis. A two-dimensional scatter plot is a type of graphical depiction used to show data sets. Six Sigma makes extensive use of its capacity to display nonlinear correlations between variables. In Six Sigma, scatter charts are a common technique. Used for problem analysis. The relationships between the variables are displayed in scatter plots.
45. How would you read a diagram showing a scatter plot?
Ans:
There is a positive correlation when the data in the X-Y plane rises higher from left to right. On the other hand, there is a negative correlation if the data flows downhill. The greater or higher the correlation between the two variables, the closer the data points are to making a straight line when plotted. The variables are considered to have a positive correlation if the data points form a straight line that extends from close to the origin to high y-values.
46. What does the P-value mean?
Ans:
- The probability value, or P-value in Six Sigma, establishes the importance of the data according to the null hypothesis.
- According to the null hypothesis, the event’s cause was not determined; as a result, the claim that is being proved actually did not occur.
- P-values range from 0 to 1, and in the event that one is, making people feel at ease with the new shift is the first thing we need to practice to make the project effective.
- Thus, the following actions always have a greater effect.
47. Define A data gathering plan.
Ans:
A data collection plan is a strategy for gathering the required data. Thus, the following topics are addressed in this strategy. The data collection plan analyses the kind of data that must be acquired or collected. Therefore, the primary goal of data collection is to comprehend the current procedure and present potential ideas for change. Three distinct primary sources are available for the collection of data, and they are as follows. Input. Simply said, input is the location from which data is created. Process. The steps of execution where variables like efficiency are present constitute the Process.
48. Which training in Lean and Six Sigma methodologies is necessary?
Ans:
List a few types of Lean Six Sigma projects.
- Here are a few real-world Lean Six Sigma projects.
- Quick win projects. Also referred to as “Just-do-it projects,” these involve identifying the problem and its solution beforehand. Conse. Gently, there is no pain throughout the repair.
- Process improvement projects, or PDCAs, are where an issue arises because there is no clear reason and the outcome is not sufficient.
- DFSS, or designing new process projects, is the Process of developing a whole new process from scratch. Because there isn’t a reference procedure to compare it to, a VOC is necessary.
49. What does effect size mean?
Ans:
The quantitative Measure of the total magnitude of the experiment’s effect is called effect size. The higher the impact size, the better the link between the supplied variables. Put more simply, defining the relationship between several variables is the outcome of calculating effect size.
50. What do the control charts look like?
Ans:
In Six Sigma, a control chart is used to assess a process’s longevity over a certain time frame. This tool has a graph that indicates whether a process is scaled within acceptable bounds. Determining whether a process needs to be changed or not is another benefit of using a control chart. The organization saves work, time, and resources by doing this. To assess additional observations, additional Six Sigma tools, such as Histogram/Pareto charts, can be applied to the data generated by a control chart.
51. What does the Kano Model entail?
Ans:
Therefore, provide a thorough response. A tool for product development, the Kano Model contrasts the features with the level of satisfaction that each feature provides in order to pinpoint the Voice of the Customer (VOC. Dr. Kano created the instrument, which outlines the following five traits.
- Unsatisfactory
- Needs of the customer
- Adorers
- Indifferent
52. Have you ever used a spaghetti diagram or other tool?
Ans:
One component of lean tools that are used to remove various types of waste is a spaghetti diagram. This instrument contributes to the reduction of transit, motion, and waiting time wastes. It monitors the flow of things like people, paper, and/or products. It visually depicts the specifics, such as movement, distance, waiting period, and people or things’ gait patterns. The benefits of using a spaghetti diagram include the following.
- Indicates ineffective spaces and work arrangements.
- Reduces non-value products; draws attention to waste associated with transportation
- Lessens people’s weariness by cutting down on moments
- Enhances the meaning of the lean idea
53. Which three procedures make up root cause analysis?
Ans:
Root cause analysis follows these three steps. Open step. In this first stage, all team members convene and engage in a brainstorming session to discuss all potential outcomes. Narrow step. Taking into account our present sigma performance, all potential explanations and situations are somewhat whittled down during this phase. Close-step: During this phase, the project team will validate each explanation on the whittled list for the current sigma performance.
54. When is the right time to employ Kaizen events, in your opinion?
Ans:
Kaizen activities are useful for creating gradual enhancements. In the following scenarios, using a Kaizen event is the best course of action. When an intense cross-functional collaboration is required when a rapid solution to an urgent problem is required, when the impact of a problem looks to be very severe, when an improvement may be apparent in three to five days;
55. What are the benefits and drawbacks of Zero Defects, in your opinion?
Ans:
Mr. Philip Crosby coined the phrase “Zero Defects” in his book “Absolutes of Quality Management.” This idea, which aims for perfection in order to raise quality, is particularly well-liked. The following are some benefits and drawbacks of Six Sigma.
Advantages.
- Provides increased value to the client
- Cuts out or eliminates unintentional expenses
- Aids in Cons of planning.
- Quite challenging to achieve;
- Seems more ethereal to most businesses
- Anti. Rated technology; limited time and, therefore, an aggressive strategy
56. Why did you decide to get certified in Six Sigma?
Ans:
You can discuss your reasons for pursuing a black belt Six Sigma credential here. Among the potential causes are. A deeper comprehension of Six Sigma principles, applicability across all industries, development potential for organizations; assistance in lowering errors and raising process quality, improvement of strategy and leadership.
57. Explain the concept of Pareto.
Ans:
The Pareto Principle also referred to as the 80/20 rule, asserts that about 20% of causes account for 80% of effects. It draws attention to the unequal distribution of results, where a limited number of inputs or Most outcomes can be attributed to factors.
58. Which variants are employed in the Six Sigma process?
Ans:
The following are the many statistical metrics that were employed. A control chart in Lean Six Sigma can show two different kinds of variation. Common cause variation and particular cause variation are represented by points outside of the bounds or nonrandom patterns. A common cause variation is identified when a process measure’s control charts exhibit an unpredictable pattern or variation. Range. c. Mean. d. Median. e. Mode
59. Who is on the team for implementation?
Ans:
Members of the Six Sigma implementation team usually consist of the following. An executive sponsor is a high-ranking executive who offers resources, support, and direction for the methodology’s effort. A champion is a leader who advocates and promotes the approach. The organization’s approach guarantees congruence with strategic objectives. Master Black Belt. A specialist in Six Sigma technology. Ues, who trains, mentors, and coaches Black Belts and Green Belts.
60. What does “Six Sigma Level” mean?
Ans:
- It’s a method for evaluating how consistently an operation runs.
- Six Sigma Level measures a process’s capacity and quality, indicating how well it functions when applied in accordance with the methodology.
- For instance, if process accuracy reaches a point where there are only 3.4 Defects Per Million Opportunities indicates that it is necessary to consult the DPMO score.
- This is a list of a million possible places where flaws could occur.
- 66,807 d. 6,210 e. 233 f. 3.4 61; 690,000 b. 308,537 c..
61. What distinguishes Six Sigma from Lean?
Ans:
- Some of the most significant distinctions between Six Sigma and Lean are as follows.
- Lean emphasizes getting rid of waste and making operations more efficient.
- Places a strong emphasis on value generation for the consumer and ongoing improvement.
- Focuses on streamlined operations, cycle time reduction, and process flow.
- Kanban, 5S, and value stream mapping are a few examples of tools and methods.
62. How Does Load Testing Work? How does it vary from testing for Performance?
Ans:
One type of software testing methodology called load testing evaluates a system’s Performance under particular load scenarios. It entails running the system through a predetermined number of concurrent users, transactions, or data quantities to simulate real-world usage scenarios. Simply said, load testing is a subset of performance testing that assesses the behavior of the system’s behavior load levels. Simultaneously, Performance Testing encompasses an expanded array of tests to evaluate the system’s overall performance attributes.
63. Describe the top-down methodology.
Ans:
Chosen in order to match customer needs with company strategy. Whereas all teams have a say in these kinds of decisions when using the bottom-up method. The specifics, benefits, and drawbacks of top-down versus bottom-up management are discussed here.
64. Give an overview of SIPOC.
Ans:
Suppliers, Inputs, Processes, Outputs, and Customers are referred to as SIPOCs. SIPOC is a Six Sigma high-level process mapping tool that breaks down a process into its essential elements and how they work together to give a clear overview. It is a useful technique for summarising the inputs and outputs of one or more processes to describe and improve processes.
65. List a few of the instruments utilized in the Six Sigma process.
Ans:
- These are a few frequently utilized instruments during Six
- The strategic application of Six Sigma concepts and processes within an organization is known as the “Top-down approach.” Typically, 65. List a few of the instruments utilized in the Six Sigma process.
- During Six Sigma implementation, the following tools are free. Gently used.
- Definition, Measure, Analysis, Improvement, and Control (DMAIC.
66. What does DMAIC mean?
Ans:
DMAIC is an acronym for.
- Clearly describe the problem, the goals of the undertaking as well as the client’s requirements.
- Measure. Gather information and assess how well the Process is performing right now.
- Analyse. Examine the data to determine the underlying reasons and comprehend variations in the Process.
- Enhance. Create and put into action fixes to deal with problems found and make the procedure better.
67. Make a distinction between Ppk and Cpk
Ans:
Examine the table below, which summarises the variations between Cpk and Ppk. Avoid. Don’t pass up this chance to become knowledgeable about Six Sigma techniques. Take the Six Sigma Master Black Belt course. Becoming Change Agents, encouraging a continuous improvement culture, and spearheading the organization-wide implementation of techniques.
68. What does the term “Data Collection Plan” mean to you?
Ans:
A data collection plan is a systematic approach that specifies the techniques, steps, and resources to be used for data collection during a project or research. The main components of the data collection plan are as follows. Aim, sources, types, and procedures of data; Sampling strategy; Data collection technique.ues; Data .quality control; Data collection schedule
69. What is a report on a product?
Ans:
In Six Sigma, a product report is a document that offers comprehensive details about the product development process. Details regarding the Performance, city, dependability, and any flaws or problems found during development are all included in this report. A product report is a document that information about the products your company sells. Depending on the requirements and goals of the product report, this information may change.
70. List the several variations that are applied in Six Sigma.
Ans:
Below is a list of Six Sigma versions.
- Mean. The variations are computed and compared using the averaging technique. Ues.
- Median. The difference is computed and assessed using the middle point of a certain data set.
- Range. Variations in data sets with specified values are computed by dividing the difference between the greatest and lowest values by two. Next, the lowest value is added to the original.
- Mode. In a data set, the Mode is the value that occurs the most.
71. Explain the Process of Load Testing
Ans:
The Process of assessing a system’s behavior and Performance under varied stress levels using a variety of performance measures is known as load testing. These metrics are meant to give a thorough understanding of how well the system is managing the load and point out any areas that need work.
72. Define standard deviation in section
Ans:
The degree of variance in a can be expressed as the standard deviation. 70. List the various variations that are applied in Six Sigma.
Below is a list of Six Sigma versions.
- Mean. The variations are computed and compared using averaging techniques.
- Median. A midpoint within a specified data set is used to compute and assess the variation.
73. How is the Sigma calculation method carried out?
Ans:
Sigma calculation is a method that assesses process variation in relation to client needs. The variables that were computed comprise the following.
- The total number of faults;
- The total number of units; and
- The total number of defect opportunities.
- Yield; e. DPU; f. DPO; g. DPMO
74. Define the 1.5 Sigma shift.
Ans:
A 1.5 sigma shift is the result of the procedure following several rounds of work. Put otherwise, the Process’s Performance will shift to a negative 1.5 sigma. Any system will eventually revert to a lower performance level if restrictions are not in place. The 1.5 sigma shift is the term for this. Stated otherwise, there will be a 1.5 sigma negative shift in both the process performance and the centerline.
75. Explain Six Sigma Regression.
Ans:
The technique of regression analysis is to determine the correlation between a group of input variables and a variable that is output. Regression analysis can be used to identify waste during the Six Sigma analysis phase. When a variable changes, it can be utilized to ascertain potential outcomes and assess whether the findings continue to match the predicted results.
76. Explain what a defect is in Six Sigma.
Ans:
- In Six Sigma, a defect is an indication that a processing unit is not complying with the required specifications.
- In Six Sigma, multiple unit failures or process failures are considered defective.
- Two essential terms in the Six Sigma process for identifying issues that require attention are defective and defective.
77. Define a Process Report.
Ans:
Methodology Reports are a component of Six’s DMAIC methodology. This report includes analytical data on how well the procedure performed at each step. Process reports collect information about all processes that are executed, all processes executed by a specific user, or all executions of a single process model. For these report kinds, there are three context choices: Every Process, Procedures that a specific user has started, and Processes that are not executed.
78. What do R- and X-charts represent?
Ans:
As quality control charts, X-bar and R-charts are used to track process variance and mean. R-charts show how the sub-groups have varied over time, while the X-bar shows how the mean has changed over time. Manufacturers commonly use the X-bar and R-chart pair to visualize continuous data. The X-bar facilitates average monitoring. or the procedure means and how it varied over time. The sample range, or the difference between each sample’s greatest and lowest value, is displayed in the R-chart.
79. What Do Six Sigma Brainstorming and Flowcharting Mean?
Ans:
- In Six Sigma, flowcharting refers to the act of drawing a diagram that shows the stages that comprise an event, Process, or workflow.
- One technique for coming up with innovative and uni. ue ideas for a process, workflow, good or service, or issue is brainstorming.
80. Explain Lean Six Sigma.
Ans:
Lean Six Sigma is a performance methodology that is applied in Six Sigma that focuses on decreasing process variance and eliminating components that do not contribute value to the Process. Six Sigma is an approach. It gives businesses the resources they need to enhance the Performance of their business processes. Profits, staff morale, and the quality of the goods or services all improve as a result of this improvement in Performance and decrease in process variation. Defects also reduce as a result.
81. Explain Six Sigma’s MSA.
Ans:
Measurement System Analysis (MSA) is referred to by the acronym. MSA assesses a measurement system’s accuracy, precision, and stability. It is a free statistical and scientific instrument gently used at the measure phase of Six Sigma methodology to guarantee that the measurement done to collect data is consistent, reliable, unbiased, and right. It places a strong emphasis on standardizing data collection procedures and evaluating the information gathered.
82. Describe the Nominal Group method.
Ans:
- One approach to group decision-making is the Nominal Group Method.
- Rather than focusing on the minority within a group, this model focuses on the majority’s identification of problems.
- The term “nominal group technique. ue” (NGT.
- Refers to an organized approach to group brainstorming that promotes participation from all members and speeds up consensus regarding the relative significance of issues, problems, or solutions.
- Team members first jot down their ideas; then, they choose the one they think is best.
83. Statistical Process Control (SPC. What is it?
Ans:
One instrument utilized in Six Sigma deployment is statistical process control. SPC is used to optimize, monitor, and control processes in order to make periodic improvements to them. Control of statistical processes control (SPC. Uses technology to assess and regulate .quality while keeping an eye on industrial operations. SPC initiates a range of devices and equipment to supply quality information derived from process readings and product measures. To regulate that Process, the data is assessed and tracked when it is gathered.
84. What does TRIZ stand for?
Ans:
The Theory of Inventive Problem Solving, shortened to TRIZ, concentrates on particular issues in an effort to detect trends that recur often in related industries and possibly lead to a solution. When standard Six Sigma tools are not enough to drive the project in the right direction, TRIZ is typically utilized.
85. What’s DPMO, and how is it computed?
Ans:
Defects Per Million Opportunities is what DPMO stands for. It is a statistic for estimating the degree of flaws. Or process faults in relation to the overall amount of potential defects. DPMO can be computed using the following formula. DPMO = (Total Defects / Total Opportunities. x 1,000,000.
86. Describe the Champion’s function inside Six Sigma.
Ans:
Important facets of the Champion’s job consist of the following.
- Exhibiting strong leadership through the active promotion and backing of Six Sigma projects.
- Making certain that initiatives and objectives line up with the organization’s overarching strategic goals.
- Assigning funds, staff, and equipment, among other essential resources.
- Leading project teams and facilitating training sessions.
- Monitoring the project’s development and how it affects KPIs or key performance indicators.
- Monitoring the project’s development and how it affects KPIs or key performance indicators.
87. List a few tools for quality management.
Ans:
Some common quality Management instruments utilized in Six Sigma are as follows.
- Control Charts. Track the effectiveness of your processes and spot trends, variances, and anomalies.
- Prioritising with a Pareto chart is essential to Six Sigma. Therefore, it’s critical to establish all relevant consumer metrics and make sure they are addressed.
- Process. This approach strongly emphasizes streamlining procedures to increase efficacy, efficiency, and quality. It entails analyzing and improving the procedures to lower variances and flaws and produce better results.
88. What is a model of Kano?
Ans:
According to Kano, a good or service is about much more than merely working. It also involves the feelings of the clients. When a consumer purchases a new automobile, for instance, they all expect it to stop when they apply the brakes, but many will be pleasantly surprised by the voice-activated parking assistance system. The Kano Model is a method for analyzing customer happiness and developing new products. It divides client preferences into the subset ent groups
89. Describe what an FMEA is.
Ans:
Failure Mode and Effects Analysis is referred to as FMEA. It is a systematic approach used in quality management and Six Sigma to find and fix possible flaws or faults in a system, product, or Process. Analysis of Failure Mode and Effects FMEA. is a proactive approach to identifying possible business process failures so that they can be stopped in their tracks or have their impact lessened by identifying potential hotspots and assessing potential consequences.
90. How does Root Cause Analysis work? What processes are involved?
Ans:
Typically, Root Cause Analysis involves the following steps.
- Determining the issue or undesirable result.
- Compiling pertinent data and problem-related information.
- Examining the data to find probable reasons or elements influencing the issue.
- Applying methods to delve more into the root reasons.
- Assessing and ranking the determined causes according to their significance and influence.
- Finding the core reason or causes that, if fixed, will stop the issue from happening again.
91. What does DFSS mean?
Ans:
The term Design for Six Sigma is DFSS. This methodology’s approach concentrates on creating and developing new goods, procedures, or services. It places a lot of focus on fulfilling client demands and starting with high standards of quality. The Design for Six Sigma (DFSS. The methodology applies the ideas of Six Sigma to the design of goods and the operations that support their manufacturing. Businesses can create goods, processes, and services with the aid of DFSS. Design teams may create competitive, safe, and dependable products more quickly and effectively by using DFSS.
92. Explain RASI or ARMI.
Ans:
Approver, Resource Person, Member, and Interested Party, or ARMY for short, is a framework for role designation used in Six Sigma Project Management and decision-making procedures. Effective decision framework facilitates effective project management, makes holder involvement easier, and helps define roles and duties clearly.
93. How much knowledge do you possess about statistical tools?
Ans:
The use of statistical tools is essential to Six Sigma. These tools are intended to assist an organization in identifying the specifics of different process components. The following are some important domains where these techniques are useful. Performance, flaws, issues, and variants. Large data sets can be handled using statistical methods to produce reliable findings, which facilitates data processing and increases productivity.
94. What advantages may Lean Six Sigma offer?
Ans:
The advantages of Lean Six Sigma include these.
- This methodology eliminates process flaws.
- It makes managing big teams easier.
- Lean Six Sigma implementation guarantees effective business processes.
- It helps with task prioritization.
- It makes the project more transparent.
- It raises team visibility for the project.
- It increases the output of teams.
- It facilitates time savings.
95. Describe the DMAIC Six Sigma technique in detail.
Ans:
Define, Measure, Analyze, Improve, and Control is abbreviated as DMAIC. The DMAIC methodology is employed to enhance a system’s process process. The goal of this methodology is to find opportunities for process improvement within the usual time frame. The aim of using this methodology is to reach optimal process efficiency. The DMAIC implementation process consists of five phases, during which the entire Process is assessed based on multiple parameters to enhance the flow of the processes and yield better results.