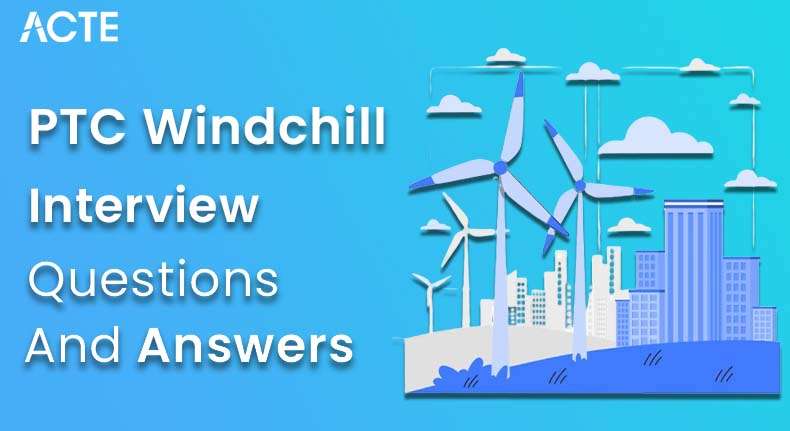
PTC Windchill stands out as a premier software solution for product lifecycle management (PLM). It effectively optimizes product development procedures across diverse industries. Equipped with powerful features including CAD data management and workflow automation, Windchill fosters enhanced collaboration and operational efficiency. This software accelerates time-to-market, drives cost reductions, and elevates product quality standards. Its comprehensive toolset positions it as a vital asset for organizations aiming to streamline their product lifecycle management processes.
1. What is PTC Windchill?
Ans:
PTC Windchill is a comprehensive PLM software by PTC Inc., designed to streamline product creation, management, and retirement. It centralizes product data and processes, enhancing collaboration across departments and locations. Key functions include managing CAD files, documents, BOMs, change and configuration management, quality control, and regulatory compliance. This integration boosts efficiency, reduces time to market, and improves product quality for manufacturers.
2. How does Windchill handle change operations?
Ans:
Windchill provides robust change management capabilities for comprehensive control and documentation of product data and process changes. This ensures the integrity of product information and keeps all stakeholders effectively informed, minimizing disruption to delivery. The process involves submitting requests, evaluating impacts, planning, approving, and implementing changes. All revisions are fully traceable and aligned with business objectives.
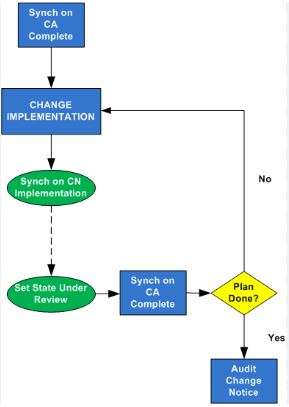
3. Explain the part of Workflows in Windchill?
Ans:
- Workflows in Windchill are essential for automating and managing business processes. They define a sequence of tasks and stages a document or product data must go through during its lifecycle, similar to review, blessing, and release processes.
- Workflows ensure that the right information reaches the right people at the right time, administering business rules and norms.
- This robotization reduces homemade crimes, enhances effectiveness, and ensures compliance with internal and external regulations.
- Customizable workflows allow associations to knitter processes according to their specific functional requirements.
4. Discuss Windchill’s capabilities in integration with other systems.
Ans:
Windchill boasts expansive integration capabilities with colorful ERP( Enterprise Resource Planning), MRP( Manufacturing Resource Planning), and CAD(Computer-backed Design) systems, easing flawless data exchange and process synchronization across different business functions. This integration enables a unified view of product information, enhances collaboration among departments, and streamlines workflows, thereby reducing time to vend and lowering costs.
5. What’s Windchill PDMLink, and how does it separate from other Windchill results?
Ans:
Windchill PDMLink is a web-ground, comprehensive product data operation result that centralizes and manages product information and processes. Unlike other Windchill results that might concentrate on specific aspects of PLM, similar to design operation( ProjectLink) or quality operation( Quality results), PDMLink provides a foundation for all product data and lifecycle processes. It supports the creation, operation, and dispersion of product structures and attestation, easing collaboration across the enterprise.
6. How does Windchill support nonsupervisory compliance?
Ans:
- Windchill supports nonsupervisory compliance by furnishing comprehensive tools and processes for managing attestation, product data, and quality processes in agreement with assiduity norms and regulations.
- It ensures that products are designed, manufactured, and serviced according to the needed guidelines, reducing the threat of non-compliance penalties, recalls, and brand damage.
- Features like inspection trails, controlled workflows, and electronic autographs help in maintaining transparent, traceable, and secure processes. For diligence like healthcare, aerospace, and automotive, where regulations are strict, Windchill’s capability to maintain compliance is inestimable.
7. Describe the conception of interpretation control in Windchill.
Ans:
Interpretation control in Windchill is an abecedarian aspect that manages various performances and variations of documents, CAD models, and other product data. It ensures that users can fluently identify, access, and work on the correct interpretation of a document or product element. Interpretation control is critical in product development for maintaining literal data, collaboration among platoon members, and managing changes efficiently.
8. In what way does PLM differ from PDM?
Ans:
Aspect | PLM | PDM |
---|---|---|
Scope | Encompasses entire product lifecycle | Focuses on managing product data |
Purpose | Optimizes product development processes | Manages product-related data |
Components Managed | Processes, people, systems, and data | Product data such as CAD files, documents, and revisions |
Goals | Reduce time-to-market, enhance collaboration | Maintain data integrity, improve design collaboration |
Key Features | Workflow automation, collaboration tools | Centralized data repository, version control |
9. How does Windchill grease collaboration across different departments and external mates?
Ans:
Windchill enhances collaboration with its centralized data system, providing authorized access to all stakeholders. Features like web-based access, shared workspaces, real-time updates, and communication tools enable efficient teamwork across departments and locations. Controlled access for external partners, suppliers, and customers improves integration across the supply chain. This collaborative environment speeds up product development, improves decision-making, and fosters innovation.
10. How does Windchill help an association on its journey in the context of digital transformation?
Ans:
Windchill serves as the backbone of the digital thread enterprise, connecting people, processes, and data across the product lifecycle. By digitizing product data and processes, it leverages IoT, AR, and analytics to enhance manufacturing, service, and development. Windchill supports the creation of digital twins, enabling virtual examination, servicing, and simulation of physical products. This digital foundation drives value by accelerating innovation, reducing costs, and improving product quality.
11. What role does Windchill’s trait operation play?
Ans:
For Windchill to define, store, and manage the parcels or features of product data, trait operation is essential. It enables associations to maintain consistency and thickness across the product lifecycle by customizing and standardizing the data linked to their documents, corridors, and products. Perpetration entails creating characteristics in Windchill’s data model, connecting them to particular kinds of information, and making sure these characteristics are appropriately preserved.
12. How does Windchill ensure data security and access control within an association?
Ans:
- Windchill ensures data security and access control through robust user operation, authorization settings, and access control lists( ACLs) that define what data users or groups can view, edit, or manage.
- Directors can configure these settings to align with organizational programs and design requirements, ensuring that sensitive information is defended and only accessible to the authorized labor force.
- Also, Windchill supports integration with enterprise authentication systems like LDAP or Active Directory, further enhancing security by using commercial credentials and security protocols.
- This concentrated approach to security helps prevent unauthorized access and ensures compliance with data protection regulations.
13. Describe the Windchill product configuration process?
Ans:
In Windchill, product configuration is defining and controlling a product’s variations to satisfy various customer requirements or requests. Configurable modules, choices, and rules that specify how items can be altered are set up throughout this phase. Product configuration plays a crucial role in lowering crime rates and guaranteeing that all configurations are workable and satisfy customer needs by enabling associations to manage and automate the generation of product variants effectively.
14. Discuss the part of Windchill in managing engineering BOMs and manufacturing BOMs.
Ans:
Windchill plays a critical part in managing engineering BOMs( eBOMs) and manufacturing BOMs( mBOMs) by furnishing a platform for creating, managing, and coinciding BOMs across different stages of the product lifecycle. The BOM represents the product as designed by engineering, while the mBOM reflects how the product will be manufactured. Windchill facilitates the transition from BOM to BOM, ensuring that manufacturing receives accurate and over-to-date product information.
15. How does Windchill support design operations?
Ans:
- Windchill supports design operations through its ProjectLink module, which provides tools for planning, executing, and covering product development systems.
- Crucial features include design timelines, task assignments, resource operation, and collaboration tools that allow platoon members to communicate and partake documents efficiently.
- By integrating design operations with PLM processes, Windchill ensures that product development conditions are aligned with design pretensions, schedules, and coffers.
- This integration helps associations to deliver systems on time and within budget while maintaining high norms of product quality and invention.
16. Describe the process of enforcing a new workflow in Windchill?
Ans:
Enforcing a new workflow in Windchill involves defining the process inflow, including stages, tasks, decision points, and blessings needed for managing product data or documents. Considerations include:
- Understanding the business process being automated.
- Relating stakeholders and their places.
- Determining the data and conduct associated with each step.
Configuring announcements and escalations is also critical to ensure timely conduct and opinions. Careful planning and testing are essential to ensure the workflow meets business conditions and enhances effectiveness without introducing backups or complexity.
17. What strategies can be employed to optimize the performance of a Windchill system?
Ans:
Optimizing the performance of a Windchill system involves several strategies, including tackle optimization, proper system configuration, regular conservation, and database tuning. Ensuring that the garçon tackle and network structure are acceptable and scalable can significantly impact performance. Configuring Windchill settings, similar to cache sizes and line processing, to match the association’s operation patterns can also enhance system responsiveness.
18. Explain how Windchill facilitates the operation of product variants and options.
Ans:
Windchill facilitates the operation of product variants and options through its Variant Specification and Option and Variant operation modules. These tools allow companies to define a product family’s possible variations and manage complex product structures with multitudinous configurable options. By using these features, associations can produce a master product structure that includes all possible variants, from which specific configurations can be deduced to meet client or request conditions.
19. What are the challenges of data migration to Windchill?
Ans:
- Data migration to Windchill presents challenges similar to ensuring data delicacy, maintaining data integrity, and minimizing time-out during the migration process.
- Prostrating these challenges requires thorough planning, including mapping out how living data will fit into the Windchill data model, relating data sanctification needs, and developing a detailed migration strategy.
- Airman migrations and testing are pivotal to identifying and addressing issues before the full migration. Employing educated professionals and using technical migration tools can also create a smoother transition.
20. How does Windchill contribute to the sustainability pretensions of an association?
Ans:
Windchill contributes to an association’s sustainability pretensions by supporting the design and development of further sustainable products and processes. It enables lifecycle assessments, material selection grounded on environmental impact, and the operation of nonsupervisory compliance related to sustainability. By easing the effective exercise of designs and accouterments, reducing waste through bettered planning and collaboration, and supporting the operation of end-of-life recycling and disposal information, Windchill helps associations reduce their environmental footmark and achieve their sustainability objectives.
21. How does Windchill support the conception of digital halves?
Ans:
Windchill supports the conception of digital halves by furnishing a comprehensive digital representation of a physical product. This includes detailed information on product design, manufacturing, and functional data collected through IoT bias. Integrating Windchill with IoT platforms enables real-time data inflow between the physical product and its digital counterpart, allowing for prophetic conservation, performance monitoring, and lifecycle analysis.
22. What’s the significance of the PartsLink module in Windchill?
Ans:
- The PartsLink module in Windchill is pivotal for managing part brackets and standardization across an association. It allows companies to classify corridors into logical groups, making it easier to search for and exercise being corridors rather than creating new bones.
- This module enhances product data operation by reducing indistinguishable corridors, streamlining the design process, and lowering costs associated with part procurement and force.
- By enabling more effective corridor operation, PartsLink contributes to brisk product development cycles and better product quality.
23. Describe how Windchill’s Quality results module.
Ans:
Windchill’s Quality Results module aids in maintaining product quality and compliance by integrating quality operation processes directly with the product lifecycle. It enables associations to proactively identify and manage pitfalls,non-conformances, and corrective and preventative conduct( CAPA). The module facilitates compliance with assiduity norms and regulations by ensuring that quality processes are followed and proven totally.
24. How do Windchill services similar to Windchill RV&S support complex product development processes?
Ans:
Windchill RV&S( formerly Integrity Lifecycle Manager) supports complex product development processes by managing conditions, confirmation, and source law operation in a unified platform. It allows brigades to capture and manage product conditions, ensuring they’re directly restated into design specifications. RV&S facilitates traceability throughout the product development lifecycle, enabling brigades to validate that final products meet the original conditions.
25. In what ways does Windchill grease the operation and collaboration of multi-CAD data?
Ans:
- Windchill facilitates the operation and collaboration of multi-CAD data by furnishing a centralized platform where data from colorful CAD systems can be stored, penetrated, and managed.
- It supports a wide range of CAD formats, enabling brigades to unite effectively using various CAD tools.
- Windchill ensures that all stakeholders have access to over-to-date CAD data, streamlining the design process and reducing crimes caused by interpretation mismatches or data silos.
- This capability enhances cross-functional collaboration, accelerates product development, and improves overall product quality.
26. Discuss the part of Windchill in force chain operation.
Ans:
Windchill plays a vital part in force chain operation by furnishing tools that enhance visibility, communication, and collaboration with suppliers. It allows companies to securely share product data, specifications, and conditions with their force chain mates. By easing real-time access to accurate information, Windchill improves the effectiveness of procurement processes, reduces the threat of crimes, and ensures that suppliers are aligned with the company’s product strategies and timelines.
27. How does Windchill promote sustainable product development practices within an association?
Ans:
Windchill promotes sustainable product development practices by enabling associations to incorporate sustainability criteria into the product design and development process. It facilitates the assessment of environmental impacts, similar to energy consumption, accouterments use, and end-of-life recyclability, beforehand in the design phase. By furnishing tools for lifecycle assessment and compliance with environmental regulations, Windchill helps companies design further sustainable products, reduce waste, and misbehave with global sustainability norms.
28. How do Windchill’s configuration capabilities support product variations over time?
Ans:
- Windchill’s configuration operation capabilities are essential for managing product variations over the product lifecycle.
- It provides a structured approach to managing changes, ensuring that all product configurations are duly proved, controlled, and traceable.
- Windchill enables associations to define and maintain nascences, manage change requests and change notices, and ensure that the impact of changes on product configurations is understood and controlled.
- This supports the effective operation of product variations, reduces the threat of crimes, and ensures that products meet client and nonsupervisory conditions.
29. What strategies does Windchill employ to ensure data integrity and help prevent data loss?
Ans:
Windchill employs strategies to ensure data integrity and prevent data loss, including robust data operation practices, automated backups, and secure access controls. It features interpretation control and check-in/check-out mechanisms to prevent accidental data overwrites. Changes to documents and product data are meticulously tracked and auditable. These measures collectively safeguard against data loss and ensure reliable data management, enhancing overall system resilience.
30. How does Windchill help in the transition from product design to manufacturing?
Ans:
Windchill facilitates the transition from product design to manufacturing by providing tools and processes for seamless communication and collaboration between design and manufacturing teams. It supports the effective conversion of engineering BOMs (eBOMs) to manufacturing BOMs (mBOMs). This ensures that manufacturing teams receive accurate, detailed product information. By streamlining these processes, Windchill helps maintain consistency and accuracy throughout the product lifecycle.
31. How does versioning work in Windchill?
Ans:
- Versioning in Windchill is an abbreviation point that manages changes and variations of product data to ensure delicacy and traceability throughout the product lifecycle.
- It distinguishes between major variations and minor duplications of documents or corridors, allowing brigades to track the elaboration of a product directly.
- This capability is pivotal for PLM as it ensures that all stakeholders work with the correct interpretation of product data, precluding expensive crimes and rework. Versioning also supports nonsupervisory compliance and inspection trails by furnishing a clear history of product changes.
32. Explain the significance of Windchill’s change operation process.
Ans:
Windchill’s change operation process is a structured approach that efficiently manages product changes, ensuring they’re estimated, approved, and enforced in a controlled manner. This process minimizes dislocation, reduces the threat of crimes, and ensures all changes are traceable. It significantly impacts product development by speeding up the time to vend, enhancing product quality, and reducing costs. Effective change operation fosters collaboration among cross-functional brigades, ensuring that product changes are well-coordinated and aligned with business objectives.
33. Describe the process of customizing user interfaces in Windchill.
Ans:
Customizing user interfaces in Windchill involves acclimatizing the UI to meet specific users or organizational conditions, enhancing usability and productivity. Customization considerations include:
- Relating users’ places and their particular requirements.
- Ensuring thickness with UI patterns to maintain usability.
- Balancing customizations with unborn upgrade paths.
Effective UI customization can streamline workflows, reduce training time, and ease user relinquishment. Still, it’s pivotal to plan customizations precisely to avoid complicating the interface or creating challenges during system upgrades.
34. What’s the part of Windchill PDMLink in the environment of product data operation?
Ans:
- Windchill PDMLink is a comprehensive product data operation( PDM) result within the Windchill suite that centralizes and manages product data and processes. Its part is to ensure that all stakeholders have access to over-to-date, accurate product information.
- PDMLink stands out from other PLM tools with its deep integration capabilities, robust data operation and collaboration features, and flexible workflow machine.
- Unlike some PLM tools that may bear expansive customization, PDMLink offers a broad range of out-of-the-box functionalities designed to meet the requirements of different diligence.
35. How does it handle the migration of data from heritage systems into Windchill?
Ans:
Migrating data from heritage systems into the Windchill requires careful planning, mapping of data structures, and confirmation to ensure data integrity and usability. Challenges frequently encountered include data inconsistency, deficient data, and differences in data models between the heritage systems and Windchill. To address these, a detailed migration plan is essential, including airman migrations, thorough testing, and stakeholder involvement to validate the migrated data.
36. Discuss the integration of Windchill with other enterprise systems similar to ERP or CRM.
Ans:
Integrating Windchill with ERP( Enterprise Resource Planning) or CRM( client Relationship operation) systems enhances data thickness, streamlines processes, and improves decision-making across the association. This integration allows for flawless data inflow between systems, ensuring that product information managed in Windchill is directly reflected in manufacturing, deals, and client service processes. Benefits include reduced homemade data entry, dropped crimes, and bettered response times to requests or client changes.
37. What stylish practices should be followed when setting up workflows in Windchill?
Ans:
When setting up workflows in Windchill, stylish practices include:
- Easily defining the business processes to be automated.
- Involving end-users in the design phase to ensure the workflow meets their requirements.
- Keeping workflows as simple as possible to avoid gratuitous complexity.
It’s also important to regularly review and optimize workflows based on users’ feedback and changing business conditions. Enforcing fallback mechanisms for exceptions and integrating announcements to keep applicable stakeholders informed is also pivotal for the effectiveness of workflow.
38. What safeguards against Windchill?
Ans:
- A few safety measures must be taken when using PTC Windchill to guarantee user productivity, system performance, and data integrity.
- To secure sensitive data and prevent illegal access, strong data management rules, including permissions and access controls, must first be established.
- Regular backups and data audits are also essential to prevent data loss and guarantee data correctness.
- To minimize disruptions to ongoing projects, maintenance and upgrading activities should be carefully planned and carried out during off-peak hours.
39. How does Windchill enable collaboration across remote locations?
Ans:
- By providing a web-based platform that allows access to product data and collaboration tools from any location at any time, Windchill assists the distant brigades.
- Because of its centralized data repository, distant platoon members are guaranteed to have access to the same information, which facilitates peaceful communication and decision-making.
- Collaboration tools from Windchill, like discussion boards, collaborative workspaces, and real-time announcements, help close the distance between geographically separated brigades, increasing output and shortening timeframes for product development.
40. Discuss the unborn trends in PLM.
Ans:
Unborn trends in PLM include increased integration with IoT, AI, and machine literacy technologies to enhance prophetic analytics, digital binary capabilities, and robotization throughout the product lifecycle. Windchill is conforming to these trends by incorporating advanced analytics, perfecting its digital thread capabilities to connect real-world product performance data with the digital model, and using AI to automate routine tasks and give perceptivity for better decision-making.
41. What’s the significance of PTC Windchill in Product Lifecycle Management( PLM)?
Ans:
PTC Windchill plays a pivotal part in Product Lifecycle operation by offering a robust platform that enables associations to manage complex information throughout the entire lifecycle of a product. From original conception to design, manufacturing, and service, Windchill provides a centralized system for data operation, collaboration, and process robotization. It helps companies accelerate time to vend, ameliorate product quality, and ensure nonsupervisory compliance by easing better decision-making and streamlining workflows.
42. How does Windchill facilitate the functioning of product data?
Ans:
- With the provision of a centralized system for handling all facets of product data throughout its lifecycle, Windchill facilitates the product data operation (PDM).
- Thanks to it, Brigades can safely store, arrange, and handle product data, including CAD models, paperwork, and BOMs.
- Windchill’s strong interpretation control and modification operation capabilities guarantee that users always have access to the most recent information, improving teamwork and lowering crime rates.
43. Explain what a BOM is and how Windchill manages its BOMs.
Ans:
A Bill of Accoutrements (BOM) is a comprehensive inventory that contains assembly instructions and all of the parts, assemblies, extras, and other items needed to produce a product. Windchill manages BOMs by offering a dynamic, centralized system that permits BOM creation, revision, and operation throughout the product’s lifetime. To suit the requirements of different departments, it can support multiple BOM views, including engineering, manufacturing, and service BOMs.
44. How can objects be checked out in the workspace?
Ans:
To check out objects in Windchill, navigate to the workspace, select the desired items, and choose “Check Out” from the conduct menu or toolbar. This locks the files, preventing others from making conflicting changes. After making edits, check the objects back in to update them and unlock the files for further edits. This process ensures exclusive edit rights, maintains version control, and prevents data loss or conflicts. Proper management of check-out and check-in processes helps maintain data integrity and collaboration efficiency.
45. What’s the purpose of the checkout process in Creo Parametric?
Ans:
- The purpose of the checkout process in Creo Parametric, when integrated with Windchill, is to ensure data integrity and manage changes effectively by allowing only one user to make changes to a train at any given time.
- When a user checks out a train, they reserve the right to modify it, and the system locks it to prevent other users from making contemporaneous changes that could lead to interpretation conflicts or data loss.
- This process enables a controlled and cooperative environment where changes are totally managed, tracked, and proven.
- Upon completing the variations, the users check the train back in, streamlining the system with the rearmost interpretation and making it available for review or further edits by other platoon members.
46. How can objects be added to the workspace in Creo Parametric?
Ans:
In Creo Parametric, users can add objects to their workspace through integration with Windchill. This feature allows them to manage product data directly within Creo. By selecting the “Add to Workspace” option in the Creo interface, users can easily incorporate and organize objects from the Windchill database. This setup is typically configured during browsing or searching for objects in Windchill, streamlining the data management process efficiently.
47. What are the different lifecycle templates associated with objects in PTC Windchill?
Ans:
In PTC Windchill, different lifecycle templates are associated with objects to define the stages an object goes through during its lifecycle, from creation to fustiness. These templates include stages similar to In Work, Released, and Obsolete, among others, depending on the specific requirements of the association. Lifecycle templates in Windchill are customizable, allowing associations to define their stages and transitions to match their product development and operation processes.
48. what are the benefits and drawbacks of establishing bespoke lifecycle nations?
Ans:
PTC Windchill custom lifecycles provide tailored workflows that align with specific product development processes, enhancing document and product data control, and improving monitoring capabilities. However, they can also introduce complexity, risk inefficiencies from poor design, and complicate system maintenance and upgrades. Implementing a unique lifecycle requires careful planning and consideration of these potential issues to ensure effectiveness.
49. Create an introductory CAD document lifecycle in PTC Windchill.
Ans:
- Creating an introductory CAD document lifecycle in PTC Windchill involves defining the series of countries and transitions that the document will suffer from its creation to its final stage.
- A simple lifecycle might include countries similar to” Draft,” In Review,” Approved,” and” Obsolete.” The” Draft” state is where the document is created and edited. Once the draft is ready, it moves to the “In Review” state, where stakeholders review the document for delicacy and absoluteness.
- Following the blessing, the document transitions to the” Approved” state, indicating it’s perfected and ready for use. Eventually, when the document is no longer demanded or applicable, it’s moved to the” Obsolete” state.
50. What types of lines can be stored and managed using PTC Windchill software?
Ans:
PTC Windchill software is designed to manage a wide array of train types, encompassing CAD lines, documents, and product data wastes, among others. It supports colorful CAD formats from major software like Creo, SOLIDWORKS, AutoCAD, and NX, enabling flawless integration with design tools. Beyond CAD lines, Windchill can manage PDFs, Microsoft Office documents, images, and, indeed, software law, making it a comprehensive result for all stages of product development.
51. What’s the function of the BOM operation point in PTC Windchill software?
Ans:
The Bill of Accoutrements( BOM) operation point in PTC Windchill is vital for directly representing the factors and assemblies that make up a product. This point allows for the creation, visualization, and operation of BOMs throughout the product lifecycle, ensuring thickness and delicacy from design through manufacturing. Windchill’s BOM operation aids in the alignment of engineering, manufacturing, and procurement departments, easing updates and changes to product information in real-time.
52. How can suppliers and merchandisers be managed using PTC Windchill software?
Ans:
PTC Windchill software enables associations to seamlessly integrate supplier data into the product lifecycle, facilitating comprehensive supplier and seller operations. Brigades can now access and evaluate vital supplier data directly within Windchill, such as lead times, cost, and corridor vacuity, thanks to this interface. Businesses may make educated decisions about supplier selection, carry out threat assessments, and effectively manage procurement by centrally managing this data.
53. What’s PDM Link used for?
Ans:
- PTC Windchill PDM Link is an important tool for Product Data Management( PDM). It acts as a central repository for all product-related information.
- It enables associations to securely store, organize, and manage product data and documents throughout the product lifecycle. PDM Link facilitates collaboration among cross-functional brigades by ensuring that everyone has access to the most up-to-date information.
- It supports interpretation control, change operation, and configuration operation processes, helping companies streamline product development, reduce time to vend and maintain compliance with assiduity norms.
54. What’s metadata, and what does it include?
Ans:
Metadata in the environment of PTC Windchill refers to the data that describes and gives information about other data within the system. This includes details about the lines and documents managed in Windchill, similar to the author, creation date, interpretation number, and any applicable descriptors that give environment or bracket. Metadata facilitates effective data operation and reclamation, enabling users to search, sort, and sludge through vast quantities of information snappily.
55. How can businesses maintain a harmonious and accurate CAD system?
Ans:
Businesses can maintain a cohesive and accurate CAD system using a centralized solution like PTC Windchill. This approach standardizes CAD practices across the organization, ensuring all users follow consistent procedures and utilize the same software. Regular training and updates are crucial for keeping the team informed about best practices and the latest software capabilities. This helps ensure efficiency and alignment across the organization.
56. What are some crucial challenges in enforcing Windchill?
Ans:
- Enforcing Windchill can present challenges similar to resistance to change, data migration complications, and aligning the system with specific business processes. To address these, associations can concentrate on comprehensive training and change operation strategies to ensure user relinquishment.
- Data migration requires careful planning and prosecution to ensure data integrity and minimize dislocations.
- Customizing Windchill to fit specific business processes might involve using PTC’s consulting services or working with educated perpetration mates to knit the system effectively to the association’s requirements.
57. What are the different products of PTC Windchill?
Ans:
PTC Windchill offers a comprehensive suite supporting the full product lifecycle, including Windchill PDMLink for unified product data, ProjectLink for design collaboration, PartsLink for part classification, MPMLink for manufacturing processes, and Quality Solutions for quality management. It also features Service Information Manager and Service Parts for service documentation, and FlexPLM for retail and consumer products, integrating all product information into a single platform.
58. What are the pivotal features of PTC Windchill?
Ans:
PTC Windchill is packed with pivotal features that support comprehensive product lifecycle operation. Crucial features include advanced data operation, allowing for the centralization of product information and ensuring that brigades can always pierce the most up-to-date data. It provides robust interpretation control and change operation processes, ensuring that product changes are precisely tracked and enforced totally.
59. What’s the part of the PTC Windchill Group Manager?
Ans:
The part of the PTC Windchill Group Manager involves managing user groups and places within the Windchill system. This part is pivotal for setting up and maintaining the security and access control mechanisms that ensure users can only pierce the data and functionality applicable to their places. The Group Manager is responsible for creating, configuring, and managing groups, assigning users to these groups, and defining the places and warrants associated with each group.
60. What is Windchill MPMLink?
Ans:
- Windchill MPMLink( Manufacturing Process operation Link) is a module within the PTC Windchill suite that bridges the gap between product development and manufacturing.
- It enables manufacturers to define, manage, and communicate manufacturing processes, plans, and instructions alongside product development.
- MPMLink facilitates the early collaboration between engineering and manufacturing brigades, ensuring that manufacturing considerations are incorporated into the product design phase.
- This integration helps reduce manufacturing costs, perfect product quality, and accelerate time to market by streamlining the transition from design to product.
61. What is Tree Picker in PTC Windchill?
Ans:
The Tree Picker in PTC Windchill is a graphical interface tool designed to simplify the selection and navigation of objects within the Windchill system. It visually represents the hierarchical structure of data, similar to corridors, documents, and product structures, allowing the users to browse and select the particulars they need fluently. The Tree Picker is particularly useful in complex product structures, where navigating through layers of data to find specific factors or documents could else be time-consuming.
62. What’s Windchill ProductPoint?
Ans:
- Windchill ProductPoint is a cooperative product developed by PTC that leverages Microsoft SharePoint technologies to give an important platform for social product development.
- It enables brigades to partake and manage product data more efficiently and unite across different locales and departments. Windchill ProductPoint facilitates easier access to Windchill’s PLM capabilities by integrating them into a familiar SharePoint terrain, enhancing users’ relinquishment and productivity.
- This result is particularly effective for managing CAD data and documents, promoting better decision-making and invention through enhanced collaboration.
63. What are the benefits of PTC Windchill software?
Ans:
PTC Windchill offers multitudinous benefits, including centralized data operation, bettered collaboration, and enhanced product quality and compliance. As a comprehensive PLM result, it allows companies to manage the entire lifecycle of a product efficiently, from generality through design, manufacturing, service, and disposal. Windchill’s capability to act as a single source of verity for product data ensures that all stakeholders have access to accurate and over-to-date information, reducing crimes and saving time.
64. Why is PTC Windchill known as a single source of verity for product data?
Ans:
PTC Windchill is recognized as a single source of truth for product data, centralizing and managing all product-related information in one unified platform. This comprehensive approach ensures that everyone involved in the product lifecycle—from designers and manufacturers to service teams and suppliers—has access to consistent, accurate, and up-to-date information. This harmonization significantly enhances collaboration and decision-making across all stages of the product lifecycle.
65. Describe the PTC Windchill support release.
Ans:
The PTC Windchill support release refers to the specific performances of the software that admit ongoing support and updates from PTC. These releases are part of PTC’s commitment to furnishing guests with nonstop advancements, security patches, and new features to enhance the software’s functionality and user experience. Support releases are critical for guests to ensure their Windchill installations are running efficiently and securely and are biddable with the rearmost assiduity norms and technologies.
66. What’s the use of the FV haul and Replica haul in PTC Windchill?
Ans:
- The FV( train Vault) Loader and Replica Loader in PTC Windchill are tools designed to ease the operation and synchronization of lines across distributed train vaults and clones in a Windchill system.
- The FV haul is primarily used for importing and exporting large volumes of data into and out of Windchill train vaults, ensuring that data is directly and efficiently managed.
- The Replica Loader, on the other hand, manages and attends to data across replicated Windchill spots, ensuring the thickness and vacuity of data across different geographic locales, which is pivotal for global associations.
67. What’s the External train Vault in PTC Windchill?
Ans:
The External Train Vault in PTC Windchill enables organizations to store Windchill-managed data outside the main database, typically on a separate storage system. This setup can improve system performance by offloading the data repository to a dedicated system optimized for data access and management. External Train Vaults are particularly useful for handling large CAD files or extensive multimedia documents, facilitating more efficient data management and access while maintaining data integrity and security.
68. How can enterprises sustain an accurate and patient CAD system?
Ans:
Enterprises can maintain an accurate and harmonious CAD system by enforcing robust data operation practices, similar to homogenizing CAD processes across brigades, using PLM tools like PTC Windchill to polarize data operation, and ensuring proper training for all users. Regular checkups and reviews of CAD data help identify inconsistencies and crimes beforehand. Integrating CAD systems with PLM and ERP systems ensures that design data is aligned with broader business processes.
69. Describe Windchill Quality results.
Ans:
Windchill Quality Results is a suite of software operations designed to enhance product quality by integrating quality planning directly into the product development lifecycle. This suite enables associations to manage pitfalls, misbehave with quality norms, and apply nonstop enhancement practices. It facilitates failure mode and goods analysis( FMEA), root cause analysis, and corrective and preventative conduct( CAPA). By using these tools, companies can predict implicit quality issues before they do, ensuring that the final product meets the loftiest quality norms.
70. What’s the part of the Task Assistant in PTC Windchill?
Ans:
The Task Assistant in PTC Windchill plays a pivotal part in guiding users through colorful tasks and workflows within the software, making the user interface more intuitive and interactive. It provides step-by-step instructions and environment-sensitive help, allowing users to complete tasks more efficiently and directly. The Task Assistant is particularly useful for new users or those performing complex tasks, as it ensures that processes are followed rightly, reducing crimes and perfecting overall productivity.
71. Why is the purging system used in PTC Windchill?
Ans:
- The purging system in PTC Windchill is used to manage and optimize database size and performance by removing gratuitous or obsolete data from the system.
- This includes old performances of documents and CAD lines, spare data, and other information that’s no longer demanded.
- Purifying helps maintain the effectiveness of the Windchill system, ensures brisk response times, and reduces storehouse costs.
- Regularly purifying data also helps in compliance with data operation programs and reduces the threat of data clutter, making it easier for users to find and pierce applicable information.
72. What is meant by “birth” in PTC Windchill?
Ans:
In PTC Windchill, a birth is a snapshot of a product or design at a specific time, capturing associated data such as documents, CAD models, and BOMs. Nascences record and save these configurations for future reference and comparison. They are essential for change management, allowing teams to track and compare product versions over time. Nascences support effective design management, quality assurance, and regulatory compliance by ensuring changes are controlled and traceable throughout the product lifecycle.
73. What are the new modules of Windchill9.0?
Ans:
Windchill9.0 introduced several new modules and advancements to ameliorate product lifecycle operation and collaboration. Crucial additions included:
- Advanced BOM operation features.
- Enhanced design operation capabilities.
- Bettered integration with other PTC products like Pro/Mastermind.
It also introduced modules for quality operation, similar to the Quality results suite for integrating quality processes with PLM conditioning. The MPMLink for manufacturing process operation and Supplier operation for integrating suppliers into the product development process were notable for their capability to streamline operations and enhance collaboration across the product lifecycle.
74. What are some advancements included in PTC Windchill10.2?
Ans:
- PTC Windchill10.2 brought significant advancements aimed at perfecting usability, system performance, and integration capabilities.
- Crucial advancements included enhanced visualization capabilities, allowing users to interact with 3D models directly within the Windchill terrain without the need for technical CAD software.
- The interpretation also concentrated on streamlining workflows and processes, introducing smarter hunt functionalities, and bettered change operation features.
- Also,10.2 enhanced collaboration tools, making it easier for global brigades to work together efficiently.
75. What is Windchill ESI?
Ans:
Windchill Enterprise Systems Integration( ESI) is a module within the Windchill suite that facilitates the integration of Windchill with colorful enterprise systems, similar to ERP( Enterprise Resource Planning), MRP( Manufacturing Resource Planning), and other business systems. ESI is designed to ensure flawless data exchange and synchronization between Windchill and these external systems, enabling an association to keep the thickness and delicacy of product information across all the departments.
76. What are the factors of Windchill ESI armature?
Ans:
- The Windchill Enterprise Systems Integrationarmature comprises several crucial factors designed to facilitate integration between Windchill and other enterprise systems, such as ERP( Enterprise Resource Planning).
- These factors include ESI Services, which are web services furnishing the communication subcaste between the Windchill and external systems; the Data Mapping Tool, which allows for the restatement and mapping of data between Windchill and other systems; and Integration Connectors, which are predefined integrations for popular ERP systems.
- The armature also includes a robust API( operation Programming Interface) for custom integrations and a monitoring and logging frame to ensure data integrity and troubleshoot issues.
77. How may an eBOM be converted to a mBOM in PTC Windchill?
Ans:
In PTC Windchill, there are multiple steps involved in converting an engineering bill of materials (BOM) into a manufacturing bill of materials (BOM) that ensures the manufacturing perspective is accurately reflected. Typically, this procedure begins with the BOM, which is organized according to a product’s design. Users can rearrange, add, or remove elements to match the actual manufacturing process by utilizing Windchill’s features. This could entail adding new manufacturing details that aren’t included in the BOM, including wiles and institutions.
78. How are Sequences Used in PTC Windchill?
Ans:
Sequences in PTC Windchill define the order of actions or operations within workflows and processes. They ensure that tasks are performed logically and efficiently, particularly in complex processes where timing and sequence impact design outcomes. Sequences help organize workflows, specify task prerequisites, and ensure all steps are completed in the correct order. This is crucial for managing product development, where coordination across departments is needed to achieve design milestones.
79. What is meant by ‘Part’ in PTC Windchill?
Ans:
- In PTC Windchill, a ‘Part’ refers to any item or element that can be collectively linked and managed within the system.
- This includes physical factors like screws, electronic corridor, assemblies, and indeed software rudiments. Corridors in Windchill are abecedarian realities around which product information is structured.
- They’re used to make up Bills of Accoutrements( BOMs) and can have associated metadata, documents, CAD lines, and more.
- The Part structure allows for the effective operation of product data across its lifecycle, enabling users to track, interpret, and control the elaboration of each element within the larger product’s environment.
80. What are some of the part attributes in PTC Windchill?
Ans:
Part attributes in PTC Windchill are data fields that store specific information about a part, aiding in its identification and management. Common attributes include Part Number, Name, Description, Material, Weight, and Created By. Additional attributes may cover lifecycle state, modification history, supplier details, and cost. Custom attributes can be defined to meet specific organizational needs. These attributes are crucial for searching, sorting, and managing data within Windchill, helping users efficiently handle large volumes of product information and ensure accessibility.
81. What is VRD in PTC Windchill?
Ans:
VRD in PTC Windchill stands for View Related Data. It’s a point that allows users to view all data related to a specific item or environment within the Windchill system. This could include documents, corridors, CAD models, and other affiliated particulars. The VRD point simplifies the task of managing complex product data by furnishing a centralized view of all affiliated information, making it easier for users to pierce, review, and manage the data demanded for decision-making and product development processes.
82. In Windchill, what is an end item?
Ans:
- In Windchill, an end item is the finished product or assembly that is shipped to the customer, including all of its parts and subassemblies in their fullest configuration.
- Finding an end item is essential for effectively controlling and tracking the product’s whole lifespan in the context of Windchill and product lifecycle management (PLM), from initial design to manufacture to post-purchase support.
- This accreditation facilitates compliance, quality control, and customer satisfaction by assisting organizations in making sure that the relevant specifications, documents, and requirements are correctly associated and handled for the finished product.
83. Briefly describe the usability, visualization, and other Windchill 9.0 improvements.
Ans:
Product View Lite 9.0 enhances user productivity with faster loading, interaction, and sharing of visualization data. It includes improved reporting with Cognos 8 Business Intelligence for real-time task status and project progress updates. The strong UI configuration tools allow customization based on user roles. Smart replication capabilities streamline setup and administration while boosting system speed and availability. Extended support options and industry-standard Java monitoring tools are also included.
84. Which additional modules come with Windchill 9.0?
Ans:
- PTC expanded Windchill 9.0’s functionality and enhanced user experience by adding several new modules.
- Among the noteworthy new modules were better project management tools, which provided more comprehensive planning and tracking features for product development projects.
- To improve processes and data flow across different organizational activities, enhanced integration capabilities with other software tools and systems, such as ERP (Enterprise Resource Planning) and MES (Manufacturing Execution Systems), were implemented.
- Improvements in collaboration capabilities were also made, as well as improved document and 3D model visualization tools, to help international teams communicate more effectively.
85. What features distinguish PTC Windchill?
Ans:
- A sophisticated solution for managing product data and processes over a product’s whole lifecycle, PTC Windchill is a complete product lifecycle management (PLM) system.
- It excels in cooperation, enabling team members in many locations to collaborate easily.
- Windchill serves as a central repository for all product-related data since it supports a wide variety of file types, including spreadsheets, documents, and CAD drawings and models.
- Because of its robust version control and change management capabilities, all alterations are efficiently monitored and managed, lowering error rates and raising the caliber of the final result.
86. What new modules are available with Windchill9.0?
Ans:
Windchill 9.0 introduced new modules to enhance usability, collaboration, and integration. Key additions included the Windchill Product Analytics module, which helps assess environmental impact and compliance early in the design process. Another significant addition, Windchill MPMLink, connects manufacturing process planning with product development to address manufacturing constraints upfront. These modules highlight Windchill’s focus on comprehensive product lifecycle management and sustainability.
87. Is Windchill a PDM or PLM?
Ans:
- Windchill is primarily honored as a Product Lifecycle operation( PLM) system, offering a broad range of functionalities that extend beyond traditional Product Data Management( PDM).
- While it includes robust PDM capabilities, similar to interpretation control, document operation, and CAD integration, its PLM functionalities encompass the entire product lifecycle, including conditions operation, product and portfolio operation, manufacturing process planning, and after-request services.
- This comprehensive approach allows associations to manage not just product data but also processes, systems, and people, from original conception through to withdrawal.
88. With this release, what specific capability upgrades are available?
Ans:
Several targeted feature improvements were made with Windchill9.0 to improve integration, collaboration, and user experience. Improved user interface (UI) customization features were among these developments, enabling users to tailor their workspaces to their needs more easily. Enhanced collaboration tools were implemented to facilitate more efficient communication and design operations among global brigades. Improved integration with other software tools and systems, such as ERP systems, made it possible for data to be exchanged more easily and processes to remain stable across several platforms.
89. What distinguishes Windchill from FlexPLM?
Ans:
PTC offers two PLM solutions: FlexPLM and Windchill, each designed for different needs. FlexPLM is tailored for retail, footwear, apparel, and consumer goods, managing line planning, design, development, and procurement. Windchill, focused on industries like aerospace, automotive, high-tech, and AI, provides comprehensive PLM functions for design, production, and service phases. Both solutions enhance product lifecycle management tailored to their specific industry requirements.
90. Which tool is used for PLM?
Ans:
- Several tools are available for Product Lifecycle operation( PLM), with Windchill by PTC being one of the leading results in the assiduity.
- Windchill offers a comprehensive suite of PLM capabilities, enabling associations to manage product development processes, unite across global brigades, and integrate with colorful CAD tools and enterprise systems.
- Other notable PLM tools in the request include Siemens Teamcenter, Dassault Systèmes’ ENOVIA, and SAP PLM. The choice of PLM tool generally depends on the specific requirements, assiduity focus, and IT structure of the association.
- Each of these tools provides a platform to streamline product development, enhance collaboration, and facilitate product quality and time to vend.