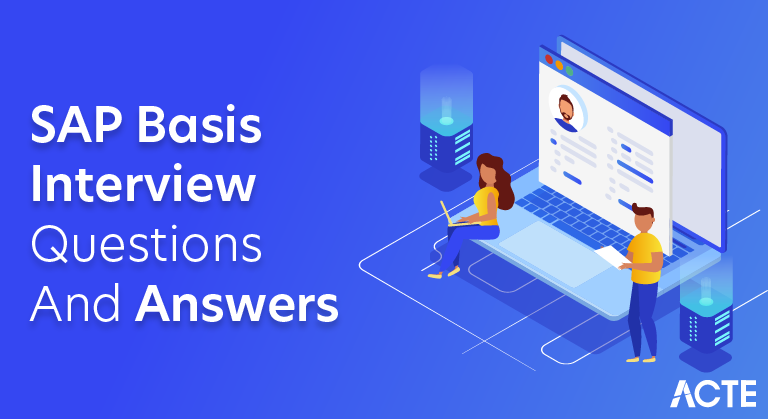
An IC engine, or internal combustion engine, is a type of engine that generates mechanical power by burning fuel inside a combustion chamber. The combustion process produces high-pressure gases, which act upon pistons, rotating a crankshaft to create motion. There are two main types: spark ignition (SI) engines, which ignite fuel with a spark plug, and compression ignition (CI) engines, which ignite fuel through compression. IC engines are commonly used in automobiles, motorcycles, aircraft, and various industrial applications due to their efficiency and versatility.
1. What is an internal combustion engine (IC engine)?
Ans:
An internal combustion engine (IC engine) is a type of heat engine that converts the chemical energy stored in fuel into mechanical energy through a series of controlled explosions. In this engine, the fuel is burned internally within a combustion chamber, typically housed within a cylinder, generating high-pressure gases. These gases then push against pistons or rotor blades, causing them to move and ultimately driving the mechanical motion of the engine.
2. What role do engine mounts play in stability and noise reduction?
Ans:
- Engine mounts secure the engine to the vehicle chassis and isolate it from chassis vibrations and road shocks.
- They help maintain vehicle stability, absorb engine vibrations, and reduce noise transmission from the engine to the passenger compartment. Properly designed engine mounts contribute to vehicle comfort, stability, and noise reduction.
3. What are the different types of internal combustion engines?
Ans:
- Spark Ignition (SI) Engines: In SI engines, the air-fuel mixture is ignited using a spark plug. This ignition process occurs at a specific point in the engine’s cycle and is typically used in gasoline-powered vehicles.
- Compression Ignition (CI) Engines: In CI engines, the air in the cylinder is compressed to a high pressure, causing it to heat up significantly. This high-temperature ignite
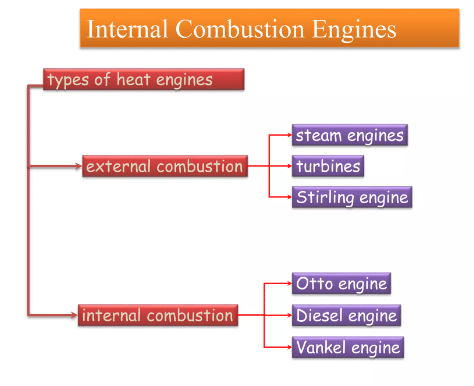
4. How does a four-stroke engine work?
Ans:
- A four-stroke engine completes four distinct strokes (intake, compression, power, and exhaust) in two revolutions of the crankshaft.
- During the intake stroke, the piston moves downward, drawing air-fuel mixture into the cylinder.
- In the compression stroke, the piston moves upward, compressing the mixture. The power stroke occurs when the spark plug ignites the compressed mixture, driving the piston downward.
- Finally, the exhaust stroke expels the spent gases from the cylinder as the piston moves upward again.
5. What is the difference between a two-stroke and four-stroke engine?
Ans:
Aspect | Two-Stroke Engine | Four-Stroke Engine |
---|---|---|
Cycle | Completes one power cycle in two strokes of the piston | Completes one power cycle in four strokes of the piston |
Intake | Combines intake and compression strokes | Separate intake and compression strokes |
Exhaust | Combines power and exhaust strokes | Separate power and exhaust strokes |
Lubrication | Oil is mixed with fuel for lubrication | Oil is stored in a separate oil reservoir and circulated for lubrication |
6. What are the advantages and disadvantages of two-stroke engines?
Ans:
Advantages:
- Simplicity and fewer moving parts.
- Lightweight and high power-to-weight ratio.
- Higher RPM capability.
- Cost-effective manufacturing.
Disadvantages:
- Poor fuel efficiency.
- Higher pollution emissions.
- Lubrication challenges.
- Noisier and more vibration.
7. What are the advantages and disadvantages of four-stroke engines?
Ans:
Advantages:
- Better fuel efficiency
- Longer lifespan
- Cleaner emissions
- Smoother operation
Disadvantages:
- More complex design
- Heavier weight
- Lower power-to-weight ratio
- Longer warm-up time
8. What is the role of a carburetor in an IC engine?
Ans:
- Air-Fuel Mixing: Carburetors mix air and fuel in the correct ratio for combustion.
- Fuel Metering: They regulate the amount of fuel entering the engine based on operating conditions.
- Idle Control: Carburetors maintain stable idle speed when the vehicle is stationary.
- Cold Start Enrichment: They enrich the mixture to make it easier to start during cold conditions.
9. How does fuel injection work in an IC engine?
Ans:
Fuel injection systems deliver fuel directly into the combustion chamber or intake manifold of an engine. In spark ignition engines, fuel injectors spray atomized fuel into the intake manifold or directly into the cylinder. In contrast, in compression ignition engines, fuel is injected directly into the combustion chamber. Fuel injection systems provide more precise control over fuel delivery, resulting in improved fuel efficiency and emissions performance compared to carburetors.
10. What are some common problems encountered in IC engines?
Ans:
Common problems in IC engines include:
- Overheating, poor fuel economy.
- Loss of power.
- Knocking or pinging noises.
- Oil leaks.
- Worn piston rings.
- Valve problems.
- The ignition system malfunctions.
11. What is the purpose of the crankshaft in an IC engine?
Ans:
The crankshaft converts the pistons’ reciprocating motion into rotary motion. This rotary motion drives the vehicle’s wheels or, in aircraft, rotates a propeller. It is essential to transmit the engine’s power to the drivetrain or propulsion system. As the primary component, it ensures smooth power delivery, enabling efficient movement of the vehicle or aircraft. Proper crankshaft maintenance is essential for optimal engine performance.
12. Explain the function of the camshaft in an IC engine.
Ans:
- The camshaft controls the opening and closing of the intake and exhaust valves in the engine.
- It contains lobes or cams that actuate the valves at specific times during the engine’s operation, synchronizing the intake of air-fuel mixture and the expulsion of exhaust gases for optimal performance.
13. What is the compression ratio, and why is it important in IC engines?
Ans:
The compression ratio is the ratio of the volume of the combustion chamber when the piston is at the bottom of its stroke (bottom dead center) to the volume when the piston is at the top of its stroke (top dead center). It determines the efficiency and power output of an engine, as higher compression ratios lead to more efficient combustion and increased power output.
14. How does turbocharging improve engine performance?
Ans:
- Turbocharging involves using a turbine-driven compressor to force more air into the combustion chamber, allowing for a greater volume of air-fuel mixture to be burned during each cycle.
- This results in increased engine power and efficiency, as the additional air allows for more fuel to be burned, generating more power without significantly increasing engine size.
15. Explain the difference between naturally aspirated and turbocharged engines.
Ans:
A naturally aspirated engine relies solely on atmospheric pressure to draw air into the combustion chamber. In contrast, a turbocharged engine uses a turbocharger to compress incoming air before it enters the combustion chamber. Due to the increased air intake, turbocharged engines typically produce more power and torque than naturally aspirated engines of similar size.
16. What is engine knocking, and how does it occur?
Ans:
Engine knocking, or detonation, happens when the air-fuel mixture ignites prematurely before the spark plug fires. Common causes include high compression, excessive heat, poor fuel quality, or incorrect ignition timing. This abnormal combustion can create harmful pressure spikes, which, if not resolved, may lead to engine damage. Addressing the issue quickly is crucial to prevent costly repairs and maintain engine performance.
17. How does the cooling system work in an IC engine?
Ans:
- The cooling system circulates coolant (usually a mixture of water and antifreeze) through passages in the engine block and cylinder head to absorb heat generated during combustion.
- The heated coolant is then transferred to the radiator, where it dissipates heat into the surrounding air.
- A water pump circulates the coolant, and a thermostat regulates the temperature to prevent overheating.
18. What role does engine oil play in an IC engine?
Ans:
Engine oil lubricates moving parts like pistons, bearings, and camshafts, reducing friction and wear. It also aids in cooling by transferring heat away from critical components. Additionally, it cleanses the engine by trapping contaminants and preventing damage. Regular oil changes ensure optimal performance and engine longevity. The correct oil viscosity improves engine efficiency and fuel economy. Proper oil maintenance also helps prevent costly repairs and prolongs engine life.
19. Explain the function of the exhaust system in an IC engine.
Ans:
The exhaust system removes spent gases produced during the combustion process from the engine’s cylinders and expels them into the atmosphere. It includes components such as exhaust manifolds, catalytic converters, mufflers, and exhaust pipes. The exhaust system also helps reduce noise levels and emissions to meet environmental regulations.
20. How does engine timing affect performance in an IC engine?
Ans:
- Engine timing refers to the synchronization of the opening and closing of intake and exhaust valves, as well as ignition timing in spark ignition engines.
- Proper timing ensures efficient combustion, maximizes power output, and minimizes emissions.
- Incorrect timing can lead to reduced performance, increased fuel consumption, and engine damage.
21. What is the role of the ignition system in an IC engine?
Ans:
The ignition system produces and delivers the high-voltage spark required to light the fuel and air combination in spark ignition engines. Key components include spark plugs, ignition coils, a distributor (in older systems), and an electronic control unit (ECU). It ensures precise timing and reliability for engine performance. Modern systems often feature advanced controls for optimal fuel efficiency and reduced emissions. Regular maintenance is crucial for sustained engine performance.
22. Explain the function of the piston rings in an IC engine.
Ans:
- Piston rings form a seal between the piston and the cylinder wall, preventing leakage of combustion gases from the combustion chamber into the crankcase and ensuring efficient combustion.
- They also help regulate the distribution of lubricating oil along the cylinder walls to reduce friction and wear.
23. What is the difference between overhead camshaft (OHC) and overhead valve (OHV) engine designs?
Ans:
In an overhead camshaft (OHC) engine, the camshaft is located above the cylinder head and directly actuates the intake and exhaust valves. In contrast, an overhead valve (OHV) engine has the camshaft positioned within the engine block, and the valves are actuated via pushrods and rocker arms. OHC designs typically allow for better valve control and higher engine speeds compared to OHV designs.
24. How does variable valve timing (VVT) improve engine performance?
Ans:
Variable valve timing (VVT) systems synchronize the intake and exhaust valve timing to optimize engine performance based on different operating conditions. This adjustment helps enhance torque output, fuel efficiency, and emissions across various engine speeds. By altering valve timing, VVT systems enable better engine response and efficiency, leading to improved performance in both low—and high-speed ranges. VVT technology helps balance power and fuel economy while minimizing emissions.
25. Explain the function of the intake manifold in an IC engine.
Ans:
- The intake manifold distributes air-fuel mixture from the carburetor or fuel injectors to the individual cylinders of the engine.
- It also serves to regulate the flow of air and fuel, ensuring even distribution to each cylinder for uniform combustion and optimal engine performance.
26. What are the advantages and disadvantages of air-cooled engines?
Ans:
Air-cooled engines are simpler in design, lighter in weight, and require less maintenance than liquid-cooled engines. However, they tend to have limited cooling capacity, which can lead to overheating under heavy loads or high ambient temperatures. Air-cooled engines also typically produce more noise and vibration than liquid-cooled engines.
27. Explain the concept of stoichiometric combustion in IC engines.
Ans:
- Stoichiometric combustion refers to the ideal air-fuel ratio at which all the fuel is burned completely with the exact amount of oxygen available in the combustion chamber.
- For gasoline engines, the stoichiometric air-fuel ratio is typically around 14.7:1 by mass (14.7 parts of air to 1 part of fuel).
- Achieving stoichiometric combustion is important for maximizing engine efficiency and minimizing emissions.
28. What is the function of the flywheel in an IC engine?
Ans:
The flywheel stores rotational energy and helps maintain a constant crankshaft speed by smoothing out torque fluctuations during combustion cycles. It absorbs excess energy and redistributes it to reduce speed variations. Additionally, the flywheel provides the necessary inertia to aid in engine starting. It also plays a crucial role in dampening vibrations and enhancing engine stability and performance.
29. How does engine displacement affect performance in an IC engine?
Ans:
- Engine displacement, measured in liters or cubic centimeters, represents the total volume swept by all the pistons within the cylinders during one complete cycle.
- Generally, engines with larger displacements produce more power and torque due to their ability to intake and burn more air-fuel mixture per cycle.
- However, larger engines may also consume more fuel and weigh more, impacting fuel efficiency and vehicle dynamics.
30. Explain the concept of knock sensors in IC engines.
Ans:
Knock sensors detect abnormal combustion conditions, such as engine knocking or detonation, by monitoring vibrations or pressure waves in the engine block. When a knock is detected, the sensor sends a signal to the engine control unit (ECU), which can adjust ignition timing, fuel injection timing, or other parameters to prevent engine damage and optimize performance.
31. What is the function of the exhaust gas recirculation (EGR) system in an IC engine?
Ans:
- The exhaust gas recirculation (EGR) system reduces nitrogen oxide (NOx) emissions by recirculating a portion of exhaust gases back into the intake manifold, where they mix with the incoming air-fuel mixture.
- This dilutes the oxygen concentration in the combustion chamber, lowering peak combustion temperatures and reducing NOx formation.
32. Explain the concept of lean-burn combustion in IC engines.
Ans:
Lean-burn combustion involves operating the engine with an air-fuel mixture that contains a higher proportion of air (lean mixture) than stoichiometric combustion. Due to reduced pumping losses and heat losses, lean-burn engines can achieve higher thermal efficiency and lower fuel consumption. Still, they also require advanced combustion control systems to prevent misfires and maintain combustion stability.
33. What are the benefits of using electronic fuel injection (EFI) systems over carburetors in IC engines?
Ans:
Electronic fuel injection (EFI) systems offer precise control over fuel delivery, allowing for optimal air-fuel mixture ratios under various operating conditions. Compared to carburetors, EFI systems improve fuel efficiency, throttle response, engine performance, and emissions control by adapting fuel delivery in real-time based on engine load, speed, and temperature.
34. How does cylinder deactivation improve fuel efficiency in IC engines?
Ans:
- Cylinder deactivation, also known as variable displacement or cylinder-on-demand technology, temporarily shuts down specific cylinders in an engine under light-load conditions to reduce fuel consumption.
- By deactivating cylinders, the engine operates more efficiently at part throttle, effectively reducing pumping losses and improving overall fuel economy without sacrificing performance.
35. What role does the catalytic converter play in the exhaust system of an IC engine?
Ans:
The catalytic converter is a crucial pollution control device in vehicles. It reduces harmful emissions such as carbon monoxide (CO), hydrocarbons (HC), and nitrogen oxides (NOx). The device facilitates chemical reactions that convert these pollutants into less harmful substances. Specifically, it transforms CO into carbon dioxide (CO2), HC into water vapour (H2O), and NOx into nitrogen (N2). This process helps in significantly lowering the environmental impact of vehicle emissions.
36. Explain the difference between naturally aspirated and supercharged engines.
Ans:
A naturally aspirated engine relies on atmospheric pressure on the combustion chamber’s air intake, relying on the engine’s intake stroke. In contrast, a supercharged engine uses a mechanically driven compressor, a supercharger, to force additional air into the combustion chamber. This process increases the air density, allowing more oxygen to enter the chamber. The higher air density results in improved combustion efficiency and increased power output.
37. What is the function of the PCV (Positive Crankcase Ventilation) system in an IC engine?
Ans:
The PCV (Positive Crankcase Ventilation) system prevents the buildup of harmful gases, such as blow-by gases and crankcase vapours, inside the engine crankcase. It recirculates these gases back into the intake manifold, where they are burned during combustion. This process helps reduce harmful emissions and prevents engine oil contamination. Additionally, it maintains proper crankcase pressure, contributing to overall engine efficiency and longevity.
38. How does the variable valve lift system improve engine performance?
Ans:
The variable valve lift system adjusts the height of the intake and exhaust valves to improve combustion chamber airflow into and out of the chamber. This optimization improves volumetric efficiency by allowing the engine to breathe better. As a result, the engine can achieve higher torque output and better fuel efficiency. This system adapts to different engine operating conditions, ensuring optimal performance across various speeds and loads.
39. What are the main factors affecting engine efficiency in IC engines?
Ans:
Engine efficiency is influenced by several factors: the compression ratio affects how much air-fuel mixture is compressed before combustion. Combustion chamber design impacts the efficiency of the burning process. Valve timing and lift optimize the intake and exhaust flow. Fuel injection or carburetion system efficiency ensures proper fuel delivery. Additionally, air intake and exhaust system design, friction losses, and thermal management are crucial in engine performance and optimization.
40. Explain the concept of engine downsizing and its impact on performance and fuel efficiency.
Ans:
- Engine downsizing involves replacing a larger-displacement engine with a smaller one, often with turbocharging or supercharging to maintain or even improve performance.
- Downsizing reduces weight, internal friction, and pumping losses, resulting in better fuel efficiency without sacrificing power output or drivability.
41. What is the role of the knock sensor in an IC engine, and how does it help prevent engine damage?
Ans:
The knock sensor detects abnormal combustion conditions, such as detonation or knocking, by sensing pressure waves or vibrations within the engine block. When a knock is detected, the sensor sends a signal to the engine control unit (ECU), which can adjust ignition timing, fuel injection timing, or other parameters to prevent engine damage and optimize performance.
42. Explain the function of the variable geometry turbocharger (VGT) in IC engines.
Ans:
- The variable geometry turbocharger (VGT) adjusts the geometry of the turbine housing or vanes to optimize exhaust gas flow and increase turbine efficiency across a wide range of engine speeds and loads.
- This allows for faster turbocharger response, reduced turbo lag, improved low-end torque, and better overall engine performance.
43. What are the advantages and disadvantages of using diesel engines compared to gasoline engines?
Ans:
Advantages of diesel engines include:
- Higher fuel efficiency.
- Better low-end torque.
- Longer lifespan due to higher compression ratios.
- Lower CO2 emissions per mile.
However, diesel engines tend to produce more nitrogen oxides (NOx) and particulate matter (PM), require more complex emissions control systems, and typically have higher initial costs compared to gasoline engines.
44. Explain the concept of exhaust gas after treatment in IC engines.
Ans:
Exhaust gas after treatment involves treating exhaust gases using various technologies and catalysts to reduce harmful emissions such as nitrogen oxides (NOx), carbon monoxide (CO), hydrocarbons (HC), and particulate matter (PM). Common after-treatment after-treatment systems include catalytic converters, diesel particulate filters (DPF), selective catalytic reduction (SCR), and lean NOx traps (LNT).
45. How does direct injection improve engine performance and efficiency compared to port fuel injection?
Ans:
- Direct injection delivers fuel directly into the combustion chamber at high pressure, allowing for more precise control over fuel delivery, better air-fuel mixing, and improved combustion efficiency compared to port fuel injection.
- Due to optimized fuel atomization and combustion, direct injection engines typically achieve higher power output, better fuel economy, and lower emissions.
46. Explain the concept of cylinder numbering and firing order in multi-cylinder IC engines.
Ans:
Cylinder numbering refers to the sequential numbering of cylinders in an engine, typically starting from cylinder #1 and progressing in numerical order. Firing order specifies the sequence in which the spark plugs or fuel injectors fire in multi-cylinder engines to ensure smooth operation and balance engine vibrations. The firing order is determined by the engine’s design and crankshaft configuration.
47. How do diesel and gasoline fuels differ, and how does it affect engine operation?
Ans:
- Diesel fuel has a higher energy density, lower volatility, and different combustion characteristics compared to gasoline.
- Diesel engines compress air to ignite the fuel, while gasoline engines use spark ignition.
- The differences in fuel properties influence engine design, combustion processes, emissions, and fuel efficiency in diesel and gasoline engines.
48. Explain the concept of engine knocking, its causes, and how it can be mitigated.
Ans:
Engine knocking, also known as detonation, occurs when the air-fuel mixture ignites prematurely or spontaneously before the spark plug fires. Causes of knocking include:
- High compression ratios.
- Hot spots in the combustion chamber.
- Low octane fuel.
- Incorrect ignition timing.
- Engine overheating.
49. How does the ECU optimize performance in modern IC engines?
Ans:
The engine control unit (ECU) is the brain of the engine management system. It monitors and controls various engine parameters, such as fuel delivery, ignition timing, valve timing, turbocharger boost pressure, and emissions control. The ECU uses input from sensors to adjust engine operation in real-time, optimizing performance, fuel efficiency, and emissions compliance.
50. Explain the concept of cylinder deactivation in multi-cylinder IC engines and its impact on fuel economy.
Ans:
- Cylinder deactivation, also known as variable displacement or cylinder-on-demand technology, selectively shuts down specific cylinders in an engine under light-load conditions to reduce fuel consumption.
- By deactivating cylinders, the engine operates more efficiently at part throttle, effectively reducing pumping losses and improving overall fuel economy without sacrificing performance.
51. How is ignition timing controlled in IC engines, and how does it affect performance?
Ans:
Ignition timing control refers to the precise timing of the spark plug firing relative to the piston’s position in the cylinder. In modern engines, the engine control unit (ECU) can control ignition timing electronically using various methods, such as map-based timing, knock control, and camshaft position sensing. Optimizing ignition timing improves combustion efficiency, power output, fuel economy, and emissions performance.
52. Explain the concept of variable valve timing (VVT) and how it improves engine performance and efficiency.
Ans:
- Variable valve timing (VVT) systems adjust the timing of the opening and closing of the intake and exhaust valves to optimize engine performance under different operating conditions.
- By varying valve timing, VVT systems can improve torque output, fuel efficiency, and emissions performance across a wide range of engine speeds and loads.
- VVT systems achieve this by optimizing air-fuel mixture intake, exhaust scavenging, and valve overlap timing.
53. How does the cooling system maintain optimal temperatures?
Ans:
The engine cooling system regulates the temperature of the engine by dissipating heat generated during combustion and friction. It circulates coolant (usually a mixture of water and antifreeze) through passages in the engine block and cylinder head, transferring heat to the radiator, where it is dissipated into the surrounding air. Proper cooling system operation is essential to prevent engine overheating, minimize thermal stress, and maintain optimal operating temperatures for combustion efficiency and component longevity.
54. Explain the concept of fuel stratification in IC engines and its impact on combustion efficiency.
Ans:
- Fuel stratification involves creating different air-fuel mixture concentrations within the combustion chamber to optimize combustion efficiency and emissions performance.
- In stratified charge engines, such as gasoline direct injection (GDI) engines, fuel is injected directly into the cylinder in a stratified pattern, with a richer mixture near the spark plug and a leaner mixture towards the cylinder walls.
55. What is the role of the exhaust gas recirculation (EGR) system in controlling emissions in IC engines?
Ans:
The exhaust gas recirculation (EGR) system reduces nitrogen oxide (NOx) emissions by recirculating a portion of exhaust gases back into the intake manifold, where they mix with the incoming air-fuel mixture. This dilutes the oxygen concentration in the combustion chamber, lowering peak combustion temperatures and reducing NOx formation. EGR systems are effective in reducing emissions, particularly in diesel engines, and are commonly used in modern IC engines to meet stringent emissions regulations.
56. Explain the concept of homogeneous charge compression ignition (HCCI) in IC engines and its benefits.
Ans:
- Homogeneous charge compression ignition (HCCI) combines elements of spark ignition (SI) and compression ignition (CI) combustion to achieve efficient and clean combustion.
- HCCI engines operate by compressing a homogeneous mixture of air and fuel to the point of auto-ignition without the need for a spark plug.
- HCCI combustion offers benefits such as higher thermal efficiency, lower fuel consumption, and reduced emissions of nitrogen oxides (NOx) and particulate matter (PM).
57. What role does the intake manifold play in optimizing airflow and fuel delivery in IC engines?
Ans:
The intake manifold distributes air-fuel mixture from the throttle body or carburetor to the engine’s individual cylinders. It is designed to optimize airflow and fuel distribution to each cylinder for uniform combustion and optimal engine performance. Intake manifold design factors such as runner length, diameter, and plenum volume influence airflow dynamics, volumetric efficiency, and torque characteristics across the engine’s operating range.
58. What is EGR cooling, and how does it reduce emissions?
Ans:
- Exhaust gas recirculation (EGR) cooling involves passing recirculated exhaust gases through a heat exchanger or cooler before reintroducing them into the intake manifold.
- Cooling the recirculated exhaust gases reduces their temperature, which helps mitigate thermal stress on engine components and prevents excessive combustion temperatures that lead to nitrogen oxide (NOx) formation.
59. How does turbocharging boost performance, and what are the types?
Ans:
Turbocharging involves using a turbine-driven compressor to force more air into the combustion chamber, allowing for a greater volume of air-fuel mixture to be burned during each cycle. This results in increased engine power and torque without significantly increasing engine size. Different types of turbocharger configurations include single turbo, twin-scroll turbo, variable geometry turbocharger (VGT), and twin-turbo setups, each offering unique advantages in terms of response, efficiency, and packaging.
60. What are friction reduction techniques and their benefits?
Ans:
- Engine friction reduction techniques aim to minimize frictional losses between moving engine components, such as pistons, piston rings, bearings, and camshafts.
- These techniques include the use of low-friction coatings, advanced lubricants, roller bearings, lightweight materials, and optimized component designs.
- By reducing friction, engine efficiency and performance are improved, resulting in lower fuel consumption, reduced wear, and improved durability.
61. What are the different types of engine layouts, and how do they impact vehicle design and performance?
Ans:
Engine layouts include inline, V-type, flat, and rotary configurations, each with its advantages and disadvantages. Inline engines are compact and offer good balance, while V-type engines are more compact and allow for higher power densities. Flat engines have a low center of gravity, which is ideal for sports cars, and rotary engines offer high power-to-weight ratios and smooth operation.
62. Explain the concept of engine downsizing and how it relates to turbocharging.
Ans:
- Engine downsizing involves replacing a larger-displacement engine with a smaller one while maintaining or improving performance.
- Turbocharging is often used in downsized engines to compensate for the reduction in displacement.
- By forcing more air into the combustion chamber, turbochargers increase power output, allowing downsized engines to achieve similar or better performance compared to larger naturally aspirated engines.
63. What role does the lubrication system play in engine performance?
Ans:
The lubrication system provides a thin film of oil between moving engine parts to reduce friction, wear, and heat generation. It also helps to remove contaminants and dissipate heat away from critical components. Proper lubrication is essential for maintaining engine longevity, reliability, and performance by reducing wear, preventing overheating, and ensuring smooth operation.
64. Explain the concept of octane rating in gasoline and its significance in IC engine operation.
Ans:
Octane rating measures gasoline’s resistance to engine knocking or detonation. Higher octane fuels are more resistant to knocking and are commonly used in high-performance engines or engines with high compression ratios. Using fuel with the appropriate octane rating ensures smooth and efficient combustion, preventing engine damage and optimizing performance.
65. What are the main factors that influence engine combustion efficiency, and how can they be optimized?
Ans:
Factors influencing engine combustion efficiency include air-fuel mixture ratio, ignition timing, compression ratio, turbulence, and fuel atomization. Optimizing these factors involves:
- Using precise fuel injection or carburetion systems.
- Adjusting ignition timing.
- Designing efficient combustion chambers.
- Controlling airflow to achieve complete combustion and maximize thermal efficiency.
66. Explain the concept of engine knock and its effects on engine performance and longevity.
Ans:
Engine knock, also known as detonation, occurs when the air-fuel mixture ignites prematurely or unevenly in the combustion chamber, resulting in high-pressure shockwaves that can damage engine components. If not addressed promptly, knocking reduces engine performance, increases fuel consumption, and can lead to piston damage, cylinder wall scoring, and other forms of engine wear.
67. What role does the exhaust system play in optimizing engine performance and reducing emissions?
Ans:
- The exhaust system removes spent gases from the engine’s cylinders and reduces harmful emissions before they are released into the atmosphere.
- It includes components such as exhaust manifolds, catalytic converters, mufflers, and exhaust pipes.
- A well-designed exhaust system ensures efficient scavenging, reduces backpressure, and minimizes emissions to meet environmental regulations while optimizing engine performance.
68. Explain the concept of variable displacement technology in IC engines and its benefits.
Ans:
Variable displacement technology, also known as cylinder deactivation or cylinder-on-demand, selectively shuts down specific cylinders in an engine under light-load conditions to reduce fuel consumption. By deactivating cylinders, the engine operates more efficiently at part throttle, effectively reducing pumping losses and improving overall fuel economy without sacrificing performance or drivability.
69. What are the pros and cons of diesel vs. gasoline engines?
Ans:
- Due to higher compression ratios, diesel engines offer higher fuel efficiency, better low-end torque, and longer lifespans.
- However, they tend to produce more nitrogen oxides (NOx) and particulate matter (PM), require more complex emissions control systems, and typically have higher initial costs compared to gasoline engines.
- Diesel engines are well-suited for heavy-duty applications and long-distance driving, where fuel economy and torque are priorities.
70. How does cylinder head design affect combustion and performance?
Ans:
Cylinder head design influences airflow dynamics, fuel atomization, and turbulence within the combustion chamber, affecting combustion efficiency and performance. Factors such as valve size, shape and placement, combustion chamber shape, and intake/exhaust port design all play a role in optimizing airflow and fuel distribution for efficient combustion, maximizing power output, and minimizing emissions.
71. What is the intake system’s role in air-fuel optimization?
Ans:
- The intake system delivers air to the combustion chamber and mixes it with fuel for combustion.
- It includes components such as the air filter, throttle body, intake manifold, and intake valves.
- Optimizing the intake system improves airflow dynamics, volumetric efficiency, and fuel atomization, resulting in better engine performance, throttle response, and fuel efficiency.
72. Explain the concept of exhaust gas recirculation (EGR) in IC engines and its impact on emissions reduction.
Ans:
Exhaust gas recirculation (EGR) reduces nitrogen oxide (NOx) emissions by recirculating a portion of exhaust gases back into the intake manifold. This dilutes the oxygen concentration in the combustion chamber, lowering peak combustion temperatures and reducing NOx formation. EGR is an effective emissions control strategy, particularly in diesel engines, and is commonly used in modern IC engines to meet stringent emissions regulations.
73. What’s the difference between naturally aspirated and forced induction engines?
Ans:
- Naturally, aspirated engines rely on atmospheric pressure to draw air into the combustion chamber.
- In contrast, forced induction engines use mechanical compressors such as turbochargers or superchargers to force more air into the combustion chamber.
- Due to increased air density, forced induction engines produce more power and torque, allowing for higher combustion pressures and greater volumetric efficiency compared to naturally aspirated engines.
74. How do knock sensors protect and optimize engine performance?
Ans:
Engine knock sensors detect abnormal combustion conditions, such as detonation or knocking, by sensing pressure waves or vibrations within the engine block. When a knock is detected, the sensor sends a signal to the engine control unit (ECU), which can adjust ignition timing, fuel injection timing, or other parameters to prevent engine damage and optimize performance. Knock sensors are essential for protecting the engine from damage and maximizing power output.
75. What is the function of the throttle body?
Ans:
- The throttle body regulates the amount of air entering the engine’s intake manifold by controlling the opening and closing of a throttle plate.
- By adjusting the throttle position, the throttle body controls engine power and torque output in response to driver inputs.
- In electronic throttle control (ETC) systems, the throttle body is controlled electronically by the engine control unit (ECU) based on driver demand and operating conditions.
76. Explain the concept of variable valve lift and its impact on engine performance and efficiency.
Ans:
Variable valve lift systems adjust the lift (height) of the intake and exhaust valves to optimize airflow into and out of the combustion chamber. By varying valve lift, these systems can improve volumetric efficiency, torque output, and fuel efficiency across different engine speeds and loads. They enhance engine performance by maximizing airflow and optimizing combustion characteristics for better efficiency and power output.
77. How does engine management software optimize performance?
Ans:
- Engine management software, often referred to as engine control unit (ECU) programming, controls various engine parameters such as fuel delivery, ignition timing, valve timing, and turbocharger boost pressure.
- By adjusting these parameters in real time based on sensor inputs, it optimizes engine performance, fuel efficiency, and emissions control across a wide range of operating conditions.
78. What is fuel stratification, and how does it affect emissions?
Ans:
Fuel stratification involves creating different air-fuel mixture concentrations within the combustion chamber to optimize combustion efficiency and emissions performance. In stratified charge engines, such as gasoline direct injection (GDI) engines, fuel is injected directly into the cylinder in a stratified pattern, with a richer mixture near the spark plug and a leaner mixture towards the cylinder walls. This stratified mixture allows for more complete combustion, reduced fuel consumption, and lower emissions compared to homogeneous charge engines.
79. How do PFI and GDI systems differ?
Ans:
- Port fuel injection (PFI) systems inject fuel into the intake manifold before it enters the combustion chamber, while gasoline direct injection (GDI) systems inject fuel directly into the cylinder.
- GDI systems offer better control over fuel delivery, improved combustion efficiency, and lower emissions compared to PFI systems.
- However, GDI systems are more complex and expensive to manufacture and may produce higher particulate emissions under certain operating conditions.
80. What are the benefits of variable compression ratio engines?
Ans:
Variable compression ratio (VCR) engines allow the compression ratio to be adjusted to optimize engine performance and fuel efficiency under different operating conditions. By varying the compression ratio, VCR engines can adapt to changes in load, speed, and fuel quality, maximizing thermal efficiency and power output while minimizing emissions and fuel consumption. VCR engines represent a promising technology for achieving the dual goals of performance and efficiency in IC engines.
81. How does crankcase ventilation impact performance and emissions?
Ans:
- The crankcase ventilation system, also known as the positive crankcase ventilation (PCV) system, removes blow-by gases and crankcase vapors from the engine crankcase and recirculates them back into the intake manifold to be burned during combustion.
- This helps prevent the buildup of harmful gases, reduces emissions, and maintains proper crankcase pressure, contributing to engine performance and emissions control.
82. What is lean-burn combustion, and how does it improve efficiency?
Ans:
Lean-burn combustion involves operating the engine with an air-fuel mixture that contains a higher proportion of air (lean mixture) compared to stoichiometric combustion. Lean-burn engines can achieve higher thermal efficiency and lower fuel consumption due to reduced pumping losses and heat losses—additionally, lean-burn combustion results in lower nitrogen oxide (NOx) emissions due to lower combustion temperatures.
83. What factors affect engine efficiency, and how can it be improved?
Ans:
Factors influencing engine efficiency include combustion efficiency, mechanical efficiency, friction losses, heat losses, and parasitic losses. Optimizing these factors involves:
- Improving combustion characteristics.
- Reducing friction between moving parts.
- Minimizing heat transfer to the surroundings.
- Reducing energy losses to auxiliary systems.
84. Explain the concept of exhaust heat recovery in IC engines and its potential benefits for energy efficiency.
Ans:
Exhaust heat recovery systems capture waste heat from the engine’s exhaust gases and convert it into usable energy, such as electricity or mechanical power, to improve overall energy efficiency. Common exhaust heat recovery technologies include exhaust gas recirculation (EGR) coolers, waste heat recovery (WHR) systems, and thermoelectric generators (TEGs). By recovering and utilizing waste heat, exhaust heat recovery systems help reduce fuel consumption and greenhouse gas emissions.
85. What’s the difference between two-stroke and four-stroke engines?
Ans:
- Two-stroke engines complete the four-stroke cycle (intake, compression, power, exhaust) in only two strokes of the piston, while four-stroke engines require four strokes.
- Two-stroke engines have simpler designs, higher power-to-weight ratios, and smoother operation but tend to produce higher emissions due to incomplete combustion.
- Four-stroke engines offer better fuel efficiency, lower emissions, and smoother operation but are more complex and heavier.
86. What is HCCI, and how does it improve efficiency?
Ans:
Homogeneous charge compression ignition (HCCI) engines combine elements of spark ignition (SI) and compression ignition (CI) combustion to achieve efficient and clean combustion. HCCI engines operate by compressing a homogeneous mixture of air and fuel to the point of auto-ignition without the need for a spark plug. HCCI combustion offers benefits such as higher thermal efficiency, lower fuel consumption, and reduced emissions of nitrogen oxides (NOx) and particulate matter (PM).
87. What role do sensors play in performance and emissions control?
Ans:
- Engine sensors monitor various engine parameters such as air intake, exhaust gas composition, engine temperature, and pressure.
- They provide real-time data to the engine control unit (ECU), allowing for precise control over fuel delivery, ignition timing, valve timing, and emissions control systems.
- By monitoring and adjusting engine parameters, sensors help optimize engine performance, fuel efficiency, and emissions compliance.
88. How does cylinder deactivation improve fuel efficiency?
Ans:
Cylinder deactivation, also known as variable displacement or cylinder-on-demand technology, selectively shuts down specific cylinders in an engine under light-load conditions to reduce fuel consumption. By deactivating cylinders, the engine operates more efficiently at part throttle, effectively reducing pumping losses and improving overall fuel economy without sacrificing performance or emissions compliance.
89. What challenges exist with alternative fuels in IC engines?
Ans:
- Alternative fuels in IC engines face challenges related to fuel compatibility, combustion characteristics, energy density, availability, infrastructure, and emissions.
- Addressing these challenges requires advancements in engine design, fuel injection systems, emissions control technologies, and fuel distribution networks.
- Additionally, research and development efforts are needed to optimize alternative fuel formulations and improve engine compatibility and performance.
90. What are camless engines, and how do they enhance performance?
Ans:
Camless engines use electronic actuators to control valve opening and closing, eliminating the need for traditional camshafts and valve trains. By adjusting valve timing, lift, and duration in real-time, seamless engines can optimize airflow, combustion characteristics, and emissions control across a wide range of operating conditions. Compared to traditional camshaft-driven engines, seamless technology offers benefits such as improved engine performance, fuel efficiency, and emissions compliance.
91. What are the key differences between diesel and gasoline engines?
Ans:
- Diesel engines operate on the principle of compression ignition, where air is compressed to high pressures until it reaches the fuel’s autoignition temperature.
- Gasoline engines, on the other hand, use spark ignition to ignite air-fuel mixtures in the combustion chamber.
- Diesel engines have higher compression ratios, produce higher torque at lower engine speeds, and typically have better fuel efficiency.
92. What role does engine oil play in performance and protection?
Ans:
- Engine oil lubricates moving parts, reduces friction and wear, seals gaps between components, and dissipates heat away from critical engine parts.
- Its properties, such as viscosity, lubricity, thermal stability, and detergent/dispersant additives, impact its ability to provide effective lubrication and protection.
- Using the correct type and viscosity of oil, along with regular oil changes, is essential for maintaining engine performance, reliability, and longevity.
93. What causes engine knock, and what are its consequences?
Ans:
Engine knock, also known as detonation, occurs when the air-fuel mixture ignites prematurely or unevenly in the combustion chamber, resulting in uncontrolled combustion and high-pressure shockwaves. Causes of knock include high compression ratios, excessive heat, low octane fuel, and incorrect ignition timing. If not addressed promptly, engine knock can lead to engine damage, including piston and cylinder head erosion, reduced engine efficiency, and increased emissions.
94. What is the function of the water pump?
Ans:
- The water pump circulates coolant (usually a mixture of water and antifreeze) through the engine’s cooling passages, cylinder head, and radiator to dissipate heat generated during engine operation.
- By continuously circulating coolant, the water pump helps maintain optimal engine operating temperatures, preventing overheating and ensuring efficient combustion and component longevity.
95. How do exhaust after-treatment systems reduce emissions?
Ans:
Exhaust gas after-treatment systems are pollution control devices that reduce harmful emissions such as nitrogen oxides (NOx), carbon monoxide (CO), hydrocarbons (HC), and particulate matter (PM) in engine exhaust. Common after-treatment systems include catalytic converters, diesel particulate filters (DPF), selective catalytic reduction (SCR), and lean NOx traps (LNT). These systems use catalysts, filters, and chemical reactions to convert pollutants into less harmful substances before they are released into the atmosphere.
96. How can turbocharged engine efficiency be optimized?
Ans:
Factors affecting engine efficiency and performance in turbocharged engines include turbocharger size and design, intercooling, air-fuel ratio, ignition timing, and exhaust backpressure. Optimizing these factors involves:
- Selecting the appropriate turbocharger size and design.
- Optimizing air-fuel mixture ratios and ignition timing.
- Reducing intake air temperatures with intercooling.
- Minimizing exhaust restrictions to maximize power output and fuel efficiency.
97. What is the role of idle speed control?
Ans:
Engine idle speed control regulates the engine’s idle speed to maintain stability and reduce emissions during idle conditions. It achieves this by adjusting throttle position, fuel delivery, or ignition timing based on inputs from sensors such as the throttle position sensor, idle air control valve, and engine speed sensor. By optimizing idle speed control, engines can achieve smooth operation, reduced fuel consumption, and lower emissions during idle conditions.