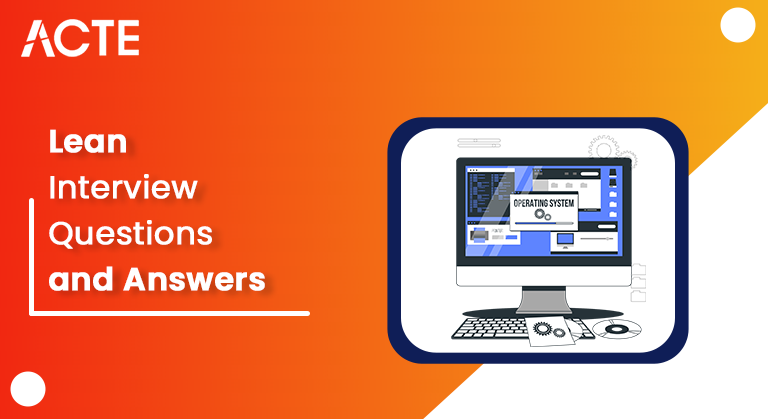
Lean manufacturing, also known as lean production, addresses the most indispensable part of manufacturing, i.e., waste. The process oversees that all of the resources are deployed efficiently during stunt production. The production also comprises neglected resources that include everything ranging from manufacturing management tools to expert staff. In this article, we’ve compiled some of the most sought-after interview questions alongside answers. Moreover, professionals will find some of the most fundamental problems, whereas advanced level questions help them land the best job. ACTE offers Lean Interview Questions that help you in cracking your interview & acquire a dream career as a Quality Analyst.
1. What is Lean manufacturing?
Ans:
- A production strategy known as “lean manufacturing” focuses on minimizing waste while maintaining or improving efficiency. Lean manufacturing is a production philosophy and management strategy that emphasizes boosting efficiency and reducing waste efficiency. The primary goal is to create more value for customers with fewer resources.
- Lean principles aim to eliminate various forms of waste, such as overproduction, waiting time, unnecessary inventory, and defects. The methodology emphasizes continuous improvement, employee involvement, and the pursuit of perfection in processes. It originated from the Toyota Production System but has since been widely adopted across various industries.
2. What are the seven wastes in Lean?
Ans:
- The seven wastes in Lean are:
- Transportation
- Inventory
- Motion
- Waiting
- Overproduction
- Overprocessing
- Defects
3. What is the purpose of 5S in Lean?
Ans:
5S is a methodology to organize and maintain a workplace efficiently, emphasizing Sort, Set in order, Shine, Standardise, and Sustain. The purpose of 5S in Lean is to establish and maintain an organized, efficient, and standardized workplace. The 5S principles are Sort, Set in order, Shine, Standardize, and Sustain. These practices aim to improve productivity, safety, and overall work quality by eliminating waste, reducing errors, and creating a visual and well-organized work environment.
4. Explain the concept of Just-in-Time (JIT) in Lean.
Ans:
- JIT is a strategy used to generate items at the exact time they are needed in the production process, minimizing inventory and storage costs. Just-in-Time (JIT) in Lean is a production strategy that aims to produce items at the exact time they are needed in the production process. The objective is to reduce stock levels and associated carrying costs while ensuring that products are manufactured efficiently to meet customer demand.
- JIT emphasizes a pull system, where production is triggered by actual customer orders, reducing the risk of overproduction and associated waste. It also involves close coordination with suppliers to ensure timely delivery of materials, contributing to overall efficiency and responsiveness in the production system.
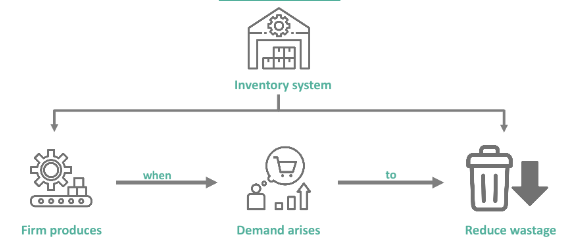
5. What role does continuous improvement play in Lean?
Ans:
Continuous improvement, or Kaizen, is central to Lean, encouraging ongoing efforts to enhance processes, reduce waste, and optimize efficiency. Continuous improvement in Lean ensures ongoing enhancement of processes, waste reduction, and optimization of efficiency. It involves iterative refinement, employee involvement, problem-solving culture, feedback loops, and maintaining standardized processes. Continuous improvement ensures that Lean principles are not static but evolve, aligning with changing customer needs and market dynamics.
6. How can Lean principles be applied beyond manufacturing?
Ans:
- Healthcare: Streamline patient care and reduce wait times.
- Software Development: Minimize lead times and enhance collaboration.
- Supply Chain Management: Optimize logistics and reduce inventory levels.
- Financial Services: Streamline transactions and improve customer service.
- Education: Optimize administrative processes and enhance learning experiences.
- Construction: Efficient project management, minimize waste.
- Retail: Optimize inventory and improve customer experience.
- Government Services: Reduce bureaucracy and enhance citizen services.
- Telecommunications: Optimize network processes and reduce downtime.
7. What is value stream mapping in Lean?
Ans:
Value stream mapping is the process of visualizing the processes involved in a process, highlighting areas of waste and opportunities for improvement. Value Stream Mapping (VSM) in Lean is a visual tool used to represent the entire process from the beginning to the end of a specific product or service. It helps identify and analyze every step in the process, highlighting areas of waste and opportunities for improvement. Value stream mapping involves mapping the flow of materials and information and documenting cycle times, lead times, and other vital metrics. The goal is to create a detailed, visual representation that allows teams to understand the current state of a process and develop plans for a more efficient future state.
8. How does Lean contribute to customer satisfaction?
Ans:
By minimizing waste and focusing on customer value, Lean processes often result in higher-quality products or services delivered more efficiently.
- Reducing Lead Times: Ensures quicker delivery.
- Improving Quality: Eliminates defects, meeting or exceeding expectations.
- Efficient Processes: Streamlines operations for better value.
- Flexibility: Responds swiftly to changes in customer demand.
- Customer-Centric Focus: Aligns processes with customer needs.
- Empowered Employees: Involves employees in continuous improvement.
- Customization: Adapts to meet individual customer requirements efficiently.
9. What is the role of leadership in implementing Lean?
Ans:
Effective leadership is crucial in fostering a culture of continuous improvement, providing support, and driving the adoption of Lean principles throughout an organization. Leadership plays a crucial role in implementing Lean by setting the vision, fostering a culture of continuous improvement, providing resources, and actively participating in Lean initiatives. Influential leaders communicate the importance of Lean principles, support employee engagement, and drive the organizational change necessary for Lean success.
10. What is the role of standardization in Lean?
Ans:
Standardization in Lean ensures consistency in processes, making it easier to identify and eliminate variations and inefficiencies >Standardization in Lean is essential for creating consistency and stability in processes. It involves establishing uniform procedures, methods, and work instructions to minimize variations and enhance efficiency. Standardization simplifies training, makes it easier to identify abnormalities, and facilitates continuous improvement by providing a stable baseline for further optimizations.
11. How does Lean address employee involvement and empowerment?
Ans:
- Lean encourages employee involvement by valuing their input, fostering a culture of continuous improvement, and empowering them to make decisions that impact their work. Lean emphasizes employee involvement and empowerment by fostering a culture where workers are actively engaged in decision-making and problem-solving.
- Teams are encouraged to contribute ideas, participate in continuous improvement initiatives, and have a sense of ownership over their work processes. This not only enhances job satisfaction but also taps into the valuable insights of those closest to the processes, leading to more effective Lean implementations.
12. What is the concept of pull production in Lean?
Ans:
Pull production is a Lean strategy where items are produced based on customer demand, minimizing excess inventory and reducing the risk of overproduction. The concept of pull production in Lean involves manufacturing goods in response to actual consumer demand as opposed to forecasting or pushing products into the process. It aims to minimize waste by only producing what is needed when it is needed, reducing excess inventory and associated costs. Pull systems are driven by customer orders, creating a more responsive and efficient production flow.
13. How can visual management aid in Lean implementation?
Ans:
- Visual management uses visual cues like charts and signage to make information easily accessible, promoting transparency and aiding in monitoring processes. Visual management in Lean involves using visual cues, like charts, graphs, and displays, to communicate information about processes, performance, and objectives.
- It aids in Lean implementation by making information easily accessible, facilitating quick decision-making, and promoting a transparent work environment. Visual management helps teams identify and address issues promptly, promotes better communication, and supports the overall efficiency and effectiveness of Lean practices.
14. Explain the concept of Heijunka in Lean manufacturing.
Ans:
Heijunka is a production smoothing technique that aims to level the production schedule, reducing fluctuations and enabling a more predictable workflow. Heijunka, in Lean manufacturing, refers to production leveling or smoothing. It involves balancing and distributing the production workload evenly over some time rather than having large fluctuations. The goal is to minimize overproduction, reduce inventory, and create a more predictable and efficient production flow. Heijunka helps organizations respond more effectively to changes in customer demand by maintaining a consistent production rate.
15. What is the role of Gemba in Lean?
Ans:
- Gemba refers to the actual place where work is done. Lean emphasizes the importance of going to the workplace to observe and understand processes firsthand for effective improvement. Gemba, in Lean, refers to the actual place where value is created – the shop floor, workspace, or any location where work is done.
- The role of Gemba in Lean is crucial as it encourages leaders and teams to go to the source to observe, understand, and improve processes. By being physically present at the Gemba, practitioners can identify inefficiencies, gather insights from frontline workers, and decide wisely to improve overall performance and quality.
16. What is the difference between Lean and Six Sigma?
Ans:
Aspect | Lean | Six Sigma | Focus | Emphasizes waste elimination and efficiency. | Focuses on reducing variation and defects for quality improvement. | Primary Goal | Aims for efficiency, continuous improvement, and customer satisfaction. | Aims for efficiency, continuous improvement, and customer satisfaction. | Approach | Streamlines processes by eliminating non-value-added activities. | Applies statistical methods to identify and reduce process variation. |
---|
17. Can Lean principles be applied to product development?
Ans:
Yes, Lean principles like iterative prototyping, cross-functional collaboration, and customer feedback can be applied to optimize product development processes. By promoting iterative and incremental development, minimizing unnecessary features, and incorporating customer feedback early in the process, Lean principles help enhance the efficiency and effectiveness of product development. Applying Lean thinking can lead to faster time-to-market, reduced development costs, and the creation of products that better meet customer needs.
18. What are some common challenges in implementing Lean?
Ans:
- Resistance to Change
- Lack of Leadership Support
- Inadequate Training
- Misunderstanding of Lean
- Difficulty in Measurement
- Cultural Misalignment
- Overemphasis on Cost Reduction
In order to overcome these obstacles, a comprehensive strategy includeseffective communication, leadership involvement, ongoing training, and a commitment to a cultural shift toward continuous improvement.
19. How does Lean support environmental sustainability?
Ans:
By minimizing waste and optimizing processes, Lean contributes to environmental sustainability by reducing resource consumption and promoting efficient use of materials. Lean supports environmental sustainability by minimizing waste and optimizing resource use. Lean emphasizes efficiency and does away with needless procedures. Reduces energy consumption, material waste, and environmental impact. Continuous improvement in Lean practices also encourages the identification and implementation of eco-friendly alternatives and sustainable practices, aligning with the broader goal of environmental stewardship.
20. What is the role of Kanban in Lean production?
Ans:
A visual scheduling tool called Kanban aids in managing workflow efficiently, signaling when to produce or replenish items based on actual demand.
- Visualizing Work: Kanban provides a visual representation of tasks.
- Limiting Work in Progress: Set limits to prevent overloading.
- Pull System: Initiates work based on actual demand.
- Continuous Improvement: Highlights areas for optimization and allows process adaptation.
21. How does Lean foster a culture of continuous learning and enhancement?
Ans:
Lean fosters a culture of ongoing development by supporting feedback, learning from mistakes, and adapting processes based on evolving needs.
- Kaizen: Encourages small, continuous changes.
- Respect for People: Values employee input and collaboration.
- Visual Management: Enhances transparency for improvement.
- Standardized Work: Establishes processes with a focus on ongoing enhancement.
22. What is the significance of takt time in Lean manufacturing?
Ans:
Takt time is the rate at which goods must be produced in order to satisfy customers’ demands. It helps synchronize production with customer needs, preventing overproduction. Takt time in Lean manufacturing is crucial as it represents the pace at which products must be produced to meet customer demand. By aligning production with takt time, Lean ensures a smooth workflow, minimizes overproduction, and helps balance resources efficiently, contributing to a more responsive and customer-centric manufacturing process.
23. How can Lean be applied in a service-oriented industry?
Ans:
Lean principles can be applied in service industries by identifying and eliminating waste in processes, improving customer satisfaction, and optimizing resource utilization.
- Identify Value: Define customer value in services.
- Process Mapping: Visualize and analyze service workflows.
- Waste Reduction: Streamline processes and eliminate inefficiencies.
- Standardization: Establish consistent service procedures.
- Continuous Improvement: Foster a culture of ongoing refinement.
- Customer Focus: Prioritize customer needs and feedback.
- Visual Management: Use visuals to monitor and manage processes.
24. Explain the concept of value stream in Lean.
Ans:
A value stream is the sequence of steps that a company employs to provide a good or service, and Lean focuses on optimizing this stream to maximize value and eliminate waste. In Lean, a value stream is the end-to-end series of activities that deliver value to a customer. It encompasses all the steps, processes, and resources that a company employs to provide a good or service; the goal is to identify and optimize this value stream, eliminating non-value-added activities (waste) to enhance efficiency and meet customer needs more effectively. Value stream mapping is a standard tool used to visualize and analyze the entire value stream, aiding in the identification of improvement opportunities.
25. What is the role of cross-functional teams in Lean?
Ans:
Cross-functional teams in Lean bring together individuals from different departments to collaborate on process improvements, fostering a holistic and collaborative approach.
Cross-functional teams in Lean:
- Foster Collaboration
- Enhance Problem-Solving
- Facilitate Knowledge Sharing
- Ensure End-to-End Perspective
- Boost Adaptability
26. How does Lean address the balance between supply chain efficiency and responsiveness?
Ans:
Lean aims to optimize the supply chain by reducing lead times and inventory while maintaining the adaptability to react fast to shifts in consumer demand.
- Reducing Waste: Minimizing unnecessary steps.
- Optimizing Inventory: Maintaining just-in-time levels.
- Standardizing Processes: Enhancing efficiency.
- Flexibility: Adapting to changes in demand.
- Continuous Improvement: Refining processes for evolving needs.
27. What is the concept of Andon in Lean manufacturing?
Ans:
Andon is a visual signaling system used in Lean to alert teams to problems or abnormalities in the production process, enabling quick response and resolution. In Lean manufacturing, Andon is a visual management tool that signals production status. It typically involves a visual display, often a light, that workers can activate to indicate an issue or request assistance. The purpose of Andon is to quickly highlight problems in the production process, enabling swift response and resolution. It enhances communication and transparency on the shop floor, facilitating continuous improvement and efficient problem-solving.
28. How does Lean contribute to cost reduction in a production environment?
Ans:
Lean reduces costs by eliminating waste, improving efficiency, and streamlining processes, which ultimately leads to lower production costs and improved profitability.
- Waste Reduction: Eliminates non-value-added activities.
- Efficiency Improvement: Streamlines processes for productivity.
- Inventory Optimization: Minimizes excess inventory holding costs.
- Quality Improvement: Reduces costs related to defects and rework.
- Employee Involvement: Engages employees for increased efficiency.
29. What are some key performance indicators (KPIs) used to measure Lean success?
Ans:
KPIs in Lean include metrics like cycle time, lead time, defect rates, and overall equipment efficiency (OEE) to measure process performance and improvements.
- Cycle Time: Measures process or production speed.
- Lead Time: Time from process initiation to completion.
- Inventory Turns: Frequency of inventory replenishment.
- Defect Rate: The proportion of goods or services with flaws.
- Overall Equipment Effectiveness (OEE): Equipment efficiency metric.
- Customer Satisfaction: Measures meeting customer expectations.
- Employee Engagement: Reflects staff involvement and satisfaction.
30. How does Lean management differ from traditional management approaches?
Ans:
Lean management emphasizes a collaborative and problem-solving approach, involving employees in decision-making and continuous improvement, in contrast to traditional hierarchical structures.
- Focus on Value: Lean prioritizes delivering customer value.
- Waste Reduction: Lean aims to eliminate process waste.
- Continuous Improvement: Lean embraces ongoing minor improvements.
- Customer-Centric: Lean strongly emphasizes understanding and meeting customer needs.
- Employee Involvement: Lean values active employee input and participation.
- Visual Management: Lean uses visual tools for better communication.
31. What is the role of the “5 Whys” technique in Lean problem-solving?
Ans:
The “5 Whys” is a technique in Lean that involves asking “why” repeatedly to identify the root cause of a problem, helping teams address issues at their source. The “5 Whys” technique is a critical component of Lean problem-solving. It involves asking “why” repeatedly to uncover the root cause of a problem. Iteratively questioning the cause-and-effect relationships helps teams address underlying issues rather than just symptoms, fostering continuous improvement in processes
32. How can Lean principles be applied to reduce lead time in production?
Ans:
By identifying and eliminating non-value-added activities, optimizing workflow, and implementing Just-in-Time practices, Lean helps reduce lead time in production.
- Value Stream Mapping: Identify and cut non-value-added steps.
- Just-In-Time (JIT) Production: Minimize inventory to match demand.
- Kaizen (Continuous Improvement): Foster a culture of ongoing process refinement.
- Standardized Work: Ensure consistent and efficient procedures.
- Pull Systems (Kanban): Align production with actual demand.
- Cross-Training: Enable flexible workforce allocation.
- Reducing Setup Times (SMED): Streamline task transitions.
- Error Prevention: Implement measures to prevent defects.
33. What is the concept of Value Stream Mapping (VSM) and its benefits?
Ans:
A visual technique called value stream mapping is used to illustrate the entire production process. It helps identify waste, streamline processes, and improve overall efficiency.
- Concept: Visualizes the entire process, exposing waste.
- Benefits: Identifies waste, enhances visibility, facilitates improvement, promotes collaboration, aids strategic planning, focuses on customer value, and provides quantifiable data.
34. How does Lean contribute to employee motivation and engagement?
Ans:
Lean involves employees in decision-making, recognizes their contributions, and provides a sense of purpose through continuous improvement, fostering motivation and engagement. Lean principles, focused on continuous improvement and eliminating waste, can boost employee motivation and engagement in several ways. By involving employees in problem-solving and decision-making, Lean creates a sense of ownership and empowerment. Clear goals and feedback mechanisms in Lean processes provide employees with a sense of accomplishment, fostering motivation. Additionally, the emphasis on teamwork and communication in Lean promotes a collaborative work environment, contributing to higher engagement levels among employees.
35. Explain the concept of Jidoka in Lean manufacturing.
Ans:
Jidoka, or autonomation, is a Lean principle that empowers machines and operators to automatically detect and stop processes when abnormalities occur, preventing defects. Jidoka, a key concept in Lean manufacturing, means “automation with a human touch” or “autonomy.” It involves designing processes to automatically stop when a problem is detected, preventing defects from progressing down the production line. Jidoka enables machines to identify abnormalities, ensuring quality control. This not only reduces the likelihood of defective products but also empowers workers to intervene, address issues promptly, and contribute to continuous improvement. Ultimately, Jidoka enhances efficiency and quality in Lean manufacturing.
36. How does Lean address variability in processes?
Ans:
- Lean aims to minimize variability by standardizing processes, reducing uncertainty, and implementing strategies like Heijunka to level production.Lean addresses variability in processes through principles like standardization, continuous improvement, and waste reduction. By standardizing processes and identifying and eliminating variations, Lean aims to create more predictable and efficient workflows.
- Continuous improvement methods, such as Kaizen, help organizations adapt to changes and reduce variability over time. Overall, Lean encourages a systematic approach to minimize fluctuations and enhance process stability.
37. What is the role of Total Productive Maintenance (TPM) in Lean?
Ans:
TPM in Lean focuses on proactive equipment maintenance to prevent breakdowns, maximize equipment effectiveness, and reduce unplanned downtime. Total Productive Maintenance (TPM) plays a crucial role in Lean manufacturing by focusing on maximizing equipment effectiveness and minimizing downtime. It aims to achieve zero breakdowns, zero defects, and zero accidents. TPM integrates preventive maintenance, autonomous maintenance, and continuous improvement, aligning with Lean principles to optimize overall equipment efficiency and contribute to waste reduction in production processes.
38. How can Lean principles be adapted for small businesses?
Ans:
Small businesses can apply Lean principles by focusing on critical processes, involving employees in improvement efforts, and gradually implementing Lean tools suited to their scale. Adapting Lean principles for small businesses involves focusing on continuous improvement, minimizing waste, and maximizing value. Start by identifying key processes, involving employees in problem-solving, and implementing gradual changes. Emphasize efficiency, customer satisfaction, and employee empowerment to create a lean and agile operation tailored to the business size.
39. How does Lean support innovation within an organization?
Ans:
- Lean encourages a culture of continuous improvement and problem-solving, fostering an environment where innovation can thrive through iterative processes and employee involvement. Lean principles support innovation by fostering a culture of continuous improvement and efficiency.
- By minimizing waste and optimizing processes, Lean releases funds that may be used for creative endeavors. Additionally, Lean encourages employee involvement and problem-solving, providing a platform for creative ideas and collaborative solutions, ultimately driving innovation within the organization.
40. How does Lean address the balance between cost reduction and maintaining product quality?
Ans:
Lean seeks to reduce costs by eliminating waste and improving efficiency, but it emphasizes maintaining or enhancing product quality to meet customer expectations. Lean strikes a balance between cost reduction and maintaining product quality by identifying and eliminating non-value-added activities. By streamlining processes, reducing waste, and optimizing workflows, Lean reduces costs without compromising quality. Continuous improvement and employee involvement ensure that enhancements are made judiciously, maintaining a focus on delivering value to customers while efficiently managing resources.
41. Can Lean principles be applied in non-manufacturing settings, such as office environments?
Ans:
Yes, Lean principles can be adapted for office environments by focusing on streamlining administrative processes, reducing delays, and improving overall efficiency. Lean principles can be applied effectively in non-manufacturing settings, including office environments. The core concepts of eliminating waste, optimizing processes, and fostering continuous improvement are applicable to various industries. In offices, Lean methodologies can enhance workflow efficiency, reduce unnecessary tasks, and improve overall productivity, leading to better outcomes and customer satisfaction.
42. What is the role of a Kaizen event in Lean implementation?
Ans:
- DA Kaizen event is a short-term, focused effort to improve a specific process. It involves cross-functional teams working together to achieve rapid improvements. A Kaizen event, integral to Lean implementation, is a focused, time-bound activity where a cross-functional team identifies and implements improvements in a specific process.
- IT accelerates problem-solving and facilitates rapid change by assembling staff members with a range of backgrounds and viewpoints. The role of a Kaizen event is to drive immediate, tangible improvements, fostering a culture of continuous improvement within the organization.
43. How does Lean contribute to a more sustainable and environmentally friendly production?
Ans:
Lean reduces waste and promotes efficient resource use, contributing to sustainability goals by minimizing environmental impact and optimizing production processes. Lean contributes to sustainability and environmental friendliness by minimizing waste and optimizing resource utilization. Through practices like reducing excess inventory, energy-efficient processes, and recycling, Lean helps lower environmental impact. Continuous improvement efforts also encourage innovation in eco-friendly practices, aligning with sustainability goals and promoting responsible production methods within the organization.
44. Question: Explain the concept of Poka-Yoke in Lean manufacturing.
Ans:
Poka-Yoke refers to mistake-proofing or error prevention techniques implemented in processes to avoid defects, ensuring products meet quality standards. Poka-Yoke, a Japanese term for “mistake-proofing” or “error prevention,” is a Lean manufacturing concept focused on creating mechanisms and procedures to avoid mistakes or flaws before they occur. This involves implementing safeguards and checks to ensure that mistakes are either impossible or easily caught. Poka-Yoke aims to enhance product quality, reduce defects, and improve overall efficiency by addressing human errors and variability in the manufacturing process.
45. In what ways does Lean support better communication within an organization?
Ans:
- Lean encourages clear communication through visual management, regular team huddles, and Gemba walks, promoting transparency and effective collaboration. Lean supports better communication within an organization by promoting transparency and collaboration.
- Regular team huddles, visual management tools, and open communication channels are vital components. By involving employees in problem-solving and decision-making, Lean creates a culture where information flows more freely, fostering a shared understanding of goals and continuous improvement initiatives across the organization.
46. How can Lean principles be applied to improve supply chain management?
Ans:
Lean improves supply chain management by reducing lead times, optimizing inventory levels, and enhancing collaboration between suppliers, manufacturers, and distributors. Lean principles can be applied to improve supply chain management by focusing on efficiency, waste reduction, and continuous improvement. Streamlining processes, optimizing inventory levels, and establishing clear communication channels with suppliers help minimize delays and improve overall responsiveness. Implementing Lean practices such as Just-in-Time (JIT) inventory, demand-driven replenishment, and collaborative relationships with suppliers enhances the supply chain’s efficacy and agility, leading to improved performance and reduced costs.
47. What is the significance of a Kanban system in Lean production?
Ans:
- Kanban systems help regulate the flow of materials and information in production, preventing overproduction and ensuring a smooth, demand-driven workflow. The Kanban system in Lean production is significant for visualizing and managing workflow.
- It uses visual cues, often cards, to signal the need for production or replenishment of items. This minimizes overproduction, reduces inventory levels, and ensures a smooth flow in the production process. The Kanban system helps synchronize different stages of production, allowing for efficient resource allocation and enabling a just-in-time approach, a core aspect of Lean manufacturing.
48. How does Lean contribute to reducing the risk of defects in manufacturing?
Ans:
Lean focuses on identifying and eliminating the root causes of defects, implementing quality control measures, and fostering a culture of continuous improvement. Lean contributes to reducing the risk of defects in manufacturing by emphasizing error prevention and continuous improvement. Through practices like Poka-Yoke (mistake-proofing) and standardized work procedures, Lean aims to eliminate errors at the source. By methodically locating and resolving the underlying causes of defects, Lean minimizes variability in processes, leading to more consistent and higher-quality outputs. This proactive approach helps prevent defects rather than relying solely on detection and correction after they occur.
49. What challenges might organizations face when transitioning to Lean practices, and how can they overcome them?
Ans:
- Challenges may include resistance to change and initial disruptions. Overcoming them involves strong leadership support, effective communication, and gradual implementation with employee involvement. Organizations transitioning to Lean practices may face obstacles, including reluctance to adapt, low staff involvement, and difficulties in altering established processes.
- To overcome these challenges, it’s crucial to invest in comprehensive training programs, involve employees in the transition process, and communicate the benefits of Lean methodologies. Leadership support, clear communication of goals, and a gradual, phased implementation can help address resistance. Furthermore, cultivating a culture of ongoing development and celebrating small successes can contribute to a smoother transition to Lean practices.
50. How does Lean promote flexibility in production processes?
Ans:
Lean promotes flexibility by minimizing setup times, allowing for quick changes in production, and adapting to fluctuations in customer demand.Lean promotes flexibility in production processes by focusing on minimizing waste, reducing lead times, and enhancing responsiveness to customer demand. Key elements such as Just-in-Time (JIT) inventory, Kanban systems, and cross-trained employees enable quicker adjustments to changing production requirements. This flexibility allows organizations to adapt efficiently to variations in demand, product changes, or unexpected disruptions, ensuring resources are utilized optimally, and production remains responsive to market dynamics.
51. What is the role of cross-training employees in Lean manufacturing?
Ans:
- Cross-training ensures that employees can perform multiple tasks, promoting flexibility in resource allocation and reducing dependency on specific individuals.
- Cross-training employees in Lean manufacturing is essential for creating a versatile and adaptable workforce.
- It allows individuals to develop skills beyond their primary roles, enabling them to step in and perform various tasks within the production process.
- This flexibility helps balance workloads, maintain continuous flow, and react quickly to shifts in consumer demand or unexpected absences.
- Cross-trained employees contribute to a more efficient and resilient manufacturing environment, aligning with Lean principles of minimizing waste and optimizing resources.
52. How does Lean address the concept of “Muda,” and why is it significant?
Ans:
“Muda” in Lean refers to waste. Identifying and eliminating different types of waste, such as unnecessary movement or overproduction, is crucial for Lean efficiency. Lean addresses the concept of “Muda,” which translates to waste in Japanese. Any procedure or action that does not improve the quality of the product or service. Lean principles aim to identify and eliminate many forms of waste, including excess inventory, overproduction, and needless waiting times, and defects. Significantly, reducing Muda improves efficiency, lowers costs, and enhances overall productivity by ensuring that resources are dedicated to activities that directly contribute to value creation, aligning with the core principles of Lean manufacturing.
53. How can Lean principles be integrated into the product development life cycle?
Ans:
- Lean principles can be applied to product development by focusing on iterative prototyping, reducing time-to-market, and incorporating customer feedback throughout the process. Integrating Lean principles into the product development life cycle involves applying concepts like value stream mapping, continuous improvement, and cross-functional collaboration.
- Start by identifying and eliminating non-value-added activities to streamline the development process. Implementing iterative cycles and feedback loops and involving customers early on can enhance responsiveness to changing requirements. Embrace a culture of innovation and empower teams to make data-driven decisions, ensuring resources are allocated efficiently. By incorporating Lean principles, product development becomes more agile, customer-focused, and capable of delivering value in a streamlined manner.
54. What is the role of visual controls in Lean management?
Ans:
Visual controls, such as dashboards and kanban boards, provide real-time information on performance metrics, aiding in quick decision-making and problem identification. Visual controls in Lean management play a crucial role in providing real-time information about processes. They use visual cues such as charts, graphs, or Kanban boards to make information easily understandable and accessible. This visual representation helps monitor workflow, identify bottlenecks, and ensure everyone has a clear understanding of the current status. Visual controls enhance communication, facilitate quicker decision-making, and contribute to a transparent and efficient environment, aligning with Lean principles of continuous improvement and waste reduction.
55. How does Lean contribute to improving employee morale and job satisfaction?
Ans:
- Lean involves employees in decision-making, recognizes their contributions, and fosters a sense of ownership and accomplishment, leading to improved morale and job satisfaction. Lean contributes to improving employee morale and job satisfaction by involving workers in decision-making, problem-solving, and continuous improvement efforts.
- Empowering employees to contribute ideas and implement changes fosters a sense of ownership and pride in their work. The focus on creating standardized processes and reducing unnecessary tasks can lead to more manageable workloads and reduced stress.
- Additionally, recognizing and celebrating achievements in the pursuit of efficiency and quality can positively impact morale, fostering an environment at work where workers feel appreciated and engaged.
56. What is the concept of “flow” in Lean, and why is it essential?
Ans:
“Flow” in Lean refers to the smooth and uninterrupted movement of materials or information through a process. It is essential for minimizing delays and improving overall efficiency. In Lean, the concept of “The term “flow” describes the seamless and continuous passage of goods or services via the entire value stream, from concept to delivery. It emphasizes minimizing interruptions, delays, and bottlenecks in processes. Flow is essential in Lean because it directly contributes to efficiency, reduced lead times, and the elimination of waste. By optimizing flow, organizations can enhance productivity, respond more quickly to customer demands, and achieve a streamlined and cost-effective production or service delivery process.
57. Can Lean be applied in non-profit or service-oriented organizations?
Ans:
- Yes, Lean principles can be adapted for non-profit or service organizations by fo
- cursing on improving processes, reducing waste, and enhancing overall efficiency. Lean principles can be applied effectively in non-profit and service-oriented organizations. While Lean methodologies originated in manufacturing, they have been successfully adapted to various sectors, including healthcare, education, and nonprofits.
- The emphasis on customer value, waste minimization, and ongoing improvement is applicable in service contexts. Implementing Lean practices can enhance operational efficiency, resource utilization, and overall effectiveness, even in organizations where the end product is a service rather than a physical product.
58. How does Lean address the concept of “batch size” in production?
Ans:
Lean encourages smaller batch sizes to reduce overproduction and inventory, allowing for more flexibility and responsiveness to changes in customer demand.Lean addresses the concept of “batch size” by encouraging smaller and more frequent production batches. This approach aligns with the principle of minimizing waste and allows for quicker identification and correction of defects. Smaller batch sizes reduce the amount of work in progress, decrease lead times, and enhance flexibility in responding to changes in customer demand. By optimizing batch sizes, Lean aims to improve overall efficiency, increase product quality, and ensure that resources are used more effectively throughout the production process.
59. What is the role of leadership visibility in Lean implementation?
Ans:
- Leadership visibility involves leaders actively engaging with teams, participating in Gemba walks, demonstrating a commitment to using lean concepts and encouraging a continuous improvement mindset.
- Leadership visibility is crucial in Lean implementation as it sets the tone for a culture of continuous improvement. Visible leadership involvement demonstrates a commitment to Lean principles, motivating staff members to participate actively in the procedure. Leaders who actively participate in Lean activities, such as Gemba walks (on-site observations), signal the importance of hands-on understanding and problem-solving.
- This visibility fosters a collaborative environment, reinforces the importance of Lean practices, and inspires a shared commitment to efficiency and excellence throughout the organization.
60. How does Lean Six Sigma combine Lean principles with Six Sigma methodology?
Ans:
Lean Six Sigma integrates Lean’s focus on waste reduction with Six Sigma’s emphasis on process variation reduction, providing a comprehensive approach to continuous improvement. Lean Six Sigma utilizes tools from both methodologies, like Kaizen events, value stream mapping, and statistical analysis. By integrating Lean’s emphasis on speed and efficiency with Six Sigma’s focus on precision and quality, organizations can achieve more robust, streamlined processes that deliver high-quality products or services with minimal waste.
61. What is the role of a Value Stream Manager in Lean manufacturing?
Ans:
A Value Stream Manager is responsible for overseeing and optimizing the end-to-end production process, ensuring value is maximized, and waste is minimized. Key responsibilities include:
- Identifying areas for improvement.
- Implementing Lean principles to reduce waste and inefficiencies.
- Ensuring a smooth, continuous flow in the value stream.
Value Stream Managers also collaborate with cross-functional teams, monitor key performance indicators, and work towards achieving strategic goals related to quality, cost, and delivery. Their role is crucial in aligning the production process with Lean principles and driving continuous improvement efforts.
62. How can Lean principles be applied in the healthcare industry?
Ans:
- In healthcare, Lean principles focus on improving patient flow, reducing wait times, and eliminating inefficiencies to enhance the overall quality of care.
- Lean principles can be applied in the healthcare industry by focusing on minimizing waste, improving efficiency, and enhancing patient outcomes. This involves streamlining processes, reducing unnecessary steps, and fostering a culture of continuous improvement. Implementing tools like value stream mapping, 5S (Sort, Set in order, Shine, Standardize, Sustain), and Kaizen events can help identify and address inefficiencies in healthcare delivery. Additionally, involving frontline staff in problem-solving and emphasizing patient-centric care are crucial aspects of applying Lean principles in healthcare.
63. What is the connection between Lean and Total Quality Management (TQM)?
Ans:
Both Lean and TQM aim to improve processes and customer satisfaction, with TQM emphasizing a broader organizational commitment to quality excellence. The connection lies in their complementary nature. Lean prioritizes process simplification and the elimination of non-value-added tasks. At the same time, TQM emphasizes the importance of quality at every stage of the process. Together, they create a comprehensive framework for organizational excellence. Integrating Lean principles with TQM can lead to a more holistic approach to continuous improvement, fostering a culture of efficiency, quality, and customer satisfaction.
64. How does Lean support the concept of continuous flow in production?
Ans:
Lean promotes continuous flow by minimizing batch sizes, reducing set-up times, and ensuring a smooth, uninterrupted flow of materials and information.Lean supports continuous flow in production by minimizing waste, reducing batch sizes, and optimizing processes to ensure a smooth and efficient workflow. It emphasizes just-in-time production, where materials and components are delivered precisely when needed, reducing inventory and associated costs. Lean also focuses on creating flexible and cross-trained teams, enabling a more adaptable response to changes in demand or production requirements. This approach helps maintain a steady and continuous flow of work throughout the production process.
65. What is the role of root cause analysis in Lean problem-solving?
Ans:
- Root cause analysis in Lean involves identifying and addressing the underlying causes of problems to prevent recurrence and promote sustainable solutions. Root cause analysis is crucial in Lean problem-solving as it aids in determining the root causes of issues rather than just addressing symptoms.
- In Lean methodology, understanding the root causes enables the implementation of effective and sustainable solutions. By systematically investigating and analyzing problems, teams can uncover the fundamental reasons for deviations from the desired outcome.
- This process empowers organizations to develop countermeasures that target the source of the problem, leading to long-term improvements and preventing the recurrence of issues in the future.
66. How does Lean handle the concept of “overburden” on employees?
Ans:
Lean seeks to eliminate overburden by optimizing work processes, ensuring realistic workloads, and preventing employee burnout through continuous improvement. Lean addresses the concept of “overburden” on employees by striving to achieve a balance between workload and capacity. This involves eliminating waste and optimizing processes to Make sure staff members are well-rested with necessary tasks.
Lean principles emphasize the importance of respecting and involving employees in problem-solving, encouraging their input to improve efficiency and eliminate activities that do not add value. By maintaining a focus on continuous improvement, Lean seeks to establish a climate at work where workers feel empowered. Additionally, their workloads are aligned with their capabilities, preventing overburdening and fostering a sustainable and productive workplace.
67. What is the relationship between Lean and continuous feedback loops?
Ans:
Lean encourages continuous feedback loops to gather input from employees and stakeholders, facilitating ongoing improvement and adaptation to changing conditions. By integrating continuous feedback loops, Lean organizations can rapidly identify inefficiencies, bottlenecks, or opportunities for improvement. This information feeds into the continuous improvement cycle, allowing for timely adjustments to optimize processes, enhance quality, and respond to changing demands. The iterative nature of Lean, combined with continuous feedback, creates a dynamic environment where the organization is continually refining and adapting its practices for greater efficiency and customer satisfaction.
68. How can Lean principles be used to improve project management processes?
Ans:
- Lean principles in project management focus on eliminating unnecessary steps, improving communication, and delivering value to the customer efficiently. Lean principles can enhance project management by promoting efficiency and reducing waste.
- Techniques like value stream mapping, continuous improvement, and visual management can streamline workflows, minimize delays, and enhance overall project delivery. Emphasizing customer value, empowering teams, and fostering a culture of continuous improvement are critical aspects of applying Lean principles to project management.
69. What is the role of Gemba Kaizen in Lean, and how does it differ from regular Kaizen events?
Ans:
Gemba Kaizen involves continuous improvement at the workplace (Gemba) through small, incremental changes, contrasting with regular Kaizen events that are more focused and time-bound.In essence, Gemba Kaizen is about ongoing, incremental improvements carried out by those closest to work. At the same time, regular Kaizen events are more structured, planned activities that address more significant improvement initiatives. Both play crucial roles in fostering a culture of continuous improvement within Lean methodologies.
70. How does Lean address the concept of “overprocessing” in manufacturing?
Ans:
Lean aims to eliminate overprocessing by focusing on value-added activities and avoiding unnecessary steps or features that do not contribute to customer satisfaction. Lean principles, such as value stream mapping, help identify and analyze the entire production process to pinpoint areas of overprocessing. By streamlining workflows, eliminating redundant tasks, and optimizing processes, Lean aims to reduce overprocessing and ensure that every step contributes directly to the creation of customer value. This approach helps enhance efficiency, lower production costs, and improve overall manufacturing performance.
71. What is the role of a Hoshin Kanri in Lean management?
Ans:
Hoshin Kanri, or policy deployment, is a strategic planning tool in Lean that aligns organizational goals with daily activities, ensuring everyone works toward common objectives. Hoshin Kanri, also known as policy deployment, is a critical component of Lean management. Its role is to align organizational objectives with daily activities, ensuring everyone works toward common goals. It involves strategic planning, communication, and continuous improvement, fostering a culture of collaboration and goal-driven actions within the organization.
72. How does Lean approach the balance between automation and human involvement in processes?
Ans:
Lean encourages a balanced approach, integrating automation where it adds value and empowering humans for tasks that require creativity, problem-solving, and adaptability. Lean emphasizes a balanced approach between automation and human involvement. It seeks to optimize processes by automating repetitive tasks while valuing the human element for creativity, problem-solving, and adaptability. Lean recognizes that automation should enhance, not replace, human skills, fostering a harmonious collaboration to achieve efficiency and quality improvements.
73. What is the connection between Lean and the concept of “respect for people”?
Ans:
- “Respect for people” is a fundamental Lean concept. Emphasizing the value of involving and empowering employees, recognizing their expertise, and fostering a positive workplace culture.
- Lean’s basic tenet is “respect for people.” Philosophy. It emphasizes valuing and empowering employees, recognizing their expertise, and involving them in decision-making. Lean promotes a culture where every individual’s insights are respected, fostering a sense of ownership and continuous improvement.
- This principle aligns with the belief that engaged and respected employees contribute significantly to the success of Lean practices.
74. How does Lean address the concept of “pull production” in a service-oriented industry?
Ans:
In services, pull production involves:
- Responding to customer demand.
- Ensuring resources are allocated efficiently based on actual needs.
- Reducing waste and improving responsiveness.
In a service-oriented industry, Lean applies the concept of “pull production” by aligning service delivery with actual customer demand. Instead of pushing services based on forecasts, Lean focuses on responding to customer needs as they arise. This involves optimizing processes to efficiently provide services when customers request them, minimizing waste and ensuring a more customer-centric approach to service delivery. The goal is to enhance responsiveness and value by aligning service activities with real-time demand signals.
75. What is the role of Lead Time Reduction in Lean manufacturing?
Ans:
- Lead Time Reduction in Lean focuses on minimizing the time it takes from receiving an order to delivering the final product, enhancing overall efficiency and customer satisfaction. Lead Time Reduction is a crucial aspect of Lean manufacturing, aiming to minimize the length of time needed to transform raw resources into final goods.
- By streamlining and optimizing processes, Lean seeks to eliminate non-value-added activities, reduce waiting times, and enhance overall efficiency. This results in quicker response to customer demand, lower inventory levels, improved flexibility, and, ultimately, a more responsive and competitive manufacturing system.
76. How can Lean principles be applied to improve software development processes?
Ans:
- Lean principles in software development involve minimizing work in progress, reducing bottlenecks, and enhancing collaboration to deliver value to users more efficiently. Lean principles can enhance software development by focusing on efficiency and eliminating waste.
- Implement practices such as continuous improvement, value stream mapping, and Kanban to streamline workflows. Foster a culture of collaboration, empower teams, and prioritize customer value, minimizing unnecessary steps in the process. Regularly assess and refine processes to optimize productivity and reduce waste.
77. What is the role of a Value Stream Manager in Lean manufacturing?
Ans:
A Value Stream Manager is responsible for overseeing and optimizing the end-to-end production process, ensuring value is maximized, and waste is minimized. In Lean manufacturing, a Value Stream Manager is essential to managing and maximizing the entire value stream – the end-to-end process of delivering a product or service. They are responsible for identifying and eliminating waste, improving efficiency, and enhancing the overall flow of value to the customer. The Value Stream Manager collaborates with cross-functional teams, utilizes Lean tools and principles, and continuously strives to enhance the value stream’s performance.
Ans:
78. How does Lean contribute to improving safety in the workplace?
Ans:
- Lean promotes a safe workplace by eliminating hazards and waste, improving organization and cleanliness, and involving employees in creating and maintaining a safe environment.
- Lean contributes to workplace safety by promoting a culture of continuous improvement and waste reduction. By eliminating inefficiencies and streamlining processes, Lean reduces the risk of accidents caused by unnecessary movement or delays.
- Visual management tools and workplace organization in Lean help create transparent, organized environments, minimizing the potential for errors and accidents. Additionally, involving employees in improvement processes enhances their engagement and awareness, fostering a safer working environment.
79. Can Lean principles be applied in research and development (R&D) environments?
Ans:
Yes, Lean principles can be adapted for R&D by focusing on efficient project management, reducing lead times, and fostering a culture of innovation and continuous improvement. Lean principles can be applied in research and development (R&D) environments to improve efficiency and innovation. Practices like value stream mapping, cross-functional collaboration, and minimizing waste can enhance R&D processes. Adopting Lean principles encourages iterative and incremental development, empowers teams to focus on customer value, and encourages a continual development culture throughout the pursuit of more effective and efficient R&D outcomes.
80. How does Lean address the concept of “batch and queue” in production?
Ans:
Lean aims to eliminate the batch and queue system by promoting smaller batch sizes and continuous flow, reducing waiting times and improving overall efficiency.Lean addresses the “batch and queue” concept in production by advocating for smaller batch sizes and a continuous flow of work. Instead of accumulating large batches of work-in-progress, Lean emphasizes producing more diminutive, manageable quantities to reduce waiting times and improve overall efficiency. This approach helps identify and resolve issues more quickly, facilitates faster feedback loops, and enhances the flexibility to adapt to changes in customer demands or production requirements.
81. What is the role of a “Kaizen Blitz” in Lean implementation?
Ans:
- A Kaizen Blitz, or rapid improvement event, is a focused and intense effort to make immediate improvements in a specific area, often lasting a few days. A “Kaizen Blitz” in Lean implementation refers to a focused, short-term effort to implement improvements in a specific area or process quickly. Also known as a “Rapid Improvement Event,” the Kaizen Blitz typically involves a cross-functional team working intensively for a few days to a week.
- The objective is to locate and get rid of garbage. Streamline processes and make immediate positive changes. It encourages collaboration, engages employees in problem-solving, and accelerates improvements in a concentrated timeframe, aligning with Lean principles of continuous improvement and efficiency.
82. How does Lean incorporate the concept of “value-added” activities?
Ans:
Lean defines value-added activities as those that directly contribute to meeting customer needs. The focus is on optimizing these activities and minimizing non-value-added tasks. Lean principles encourage organizations to analyze and streamline their processes carefully, eliminating unnecessary steps or activities that do not directly contribute to customer value. By focusing on value-added activities, Lean helps optimize efficiency and enhance overall product or service quality.
83. What is the role of a Lean Steering Committee in an organization?
Ans:
A Lean Steering Committee provides oversight, guidance, and support for Lean initiatives, ensuring alignment with organizational goals and sustained improvement. The Lean Steering Committee guides Lean initiatives, sets strategic direction, prioritizes projects, allocates resources, monitors progress, removes obstacles, promotes a Lean culture, and facilitates communication. In essence, the Lean Steering Committee plays a pivotal role in driving organizational change towards a more efficient and effective operation through the application of Lean principles.
84. How does Lean support the concept of employee empowerment?
Ans:
Lean promotes employee empowerment by involving them in decision-making, providing training, encouraging ownership of processes, and fostering a sense of responsibility and engagement. Lean principles emphasize employee empowerment by fostering a culture of continuous improvement. It encourages frontline workers to identify and solve problems, promoting a sense of ownership and involvement in decision-making. This empowerment enhances employee engagement and contributes to a more efficient and adaptive organization.
85. What is the significance of creating a “visual workplace” in Lean?
Ans:
- A visual workplace uses visual cues like charts and signs to communicate information clearly, promoting transparency, reducing errors, and aiding in problem-solving. Creating a “visual workplace” in Lean is significant because it enhances communication, reduces errors, and promotes efficiency.
- Visual cues such as charts, graphs, and visual controls help employees quickly understand processes, identify issues, and maintain standardized procedures. This visual management fosters transparency, making it easier to monitor performance, implement improvements, and create a more streamlined and effective work environment.
86. How can Lean principles be applied to improve customer service processes?
Ans:
Lean improves customer service by streamlining processes, reducing response times, and eliminating inefficiencies, resulting in enhanced customer satisfaction. Lean principles can enhance customer service by eliminating waste, improving efficiency, and focusing on continuous improvement. Identify bottlenecks, streamline workflows, empower employees to solve issues promptly, and gather customer feedback for ongoing refinement. Implementing visual management tools and fostering a culture of continuous improvement can further optimize customer service processes.
87. How does Lean handle the concept of “waste” in administrative processes?
Ans:
- In administrative processes, Lean identifies and eliminates various forms of waste, such as unnecessary paperwork or delays, to improve overall efficiency.
- In Lean methodology, waste in administrative processes is identified and eliminated through principles like 5S (Sort, Set in order, Shine, Standardize, Sustain) and continuous improvement. This involves streamlining workflows, reducing unnecessary steps, and enhancing efficiency to minimize time and resource wastage in administrative tasks.
88. What is the role of a “Kamishibai” board in Lean management?
Ans:
A visual management tool called a Kamishibai board is utilized in Lean for auditing and ensuring adherence to standardized work processes through regular checks. A “Kamishibai” board in Lean management is a visual control tool used for process management and improvement. It consists of cards or visuals representing different tasks or processes. Team members regularly check and update the board, ensuring that tasks are performed as planned. This visual management system enhances communication, accountability, and continuous improvement within the organization.
89. How does Lean address the challenge of maintaining continuous improvement in the long term?
Ans:
- Lean sustains continuous improvement by fostering a culture of learning, regularly reviewing and updating processes, and integrating improvement as an ongoing part of the organizational mindset.Lean sustains continuous improvement through a culture of relentless reflection and adaptation.
- Key aspects include regular Gemba walks to observe processes, fostering a Kaizen mindset where everyone seeks minor improvements, and integrating feedback loops for ongoing evaluation. By ingraining continuous improvement as a core value and involving employees at all levels, Lean ensures that the pursuit of efficiency becomes an ongoing, intrinsic part of the organizational culture.
90. How does Lean consider the role of suppliers in the overall value chain?
Ans:
Lean emphasizes collaboration with suppliers to ensure a smooth and efficient flow of materials, reduce lead times, and improve overall supply chain performance. Lean recognizes the critical role of suppliers in the overall value chain. It emphasizes building solid relationships with suppliers to ensure a smooth and efficient flow of materials. Collaborative partnerships are encouraged, involving suppliers early in the product development process. Lean also promotes practices like just-in-time inventory and Kanban systems to synchronize production with supplier deliveries, reducing waste and enhancing overall value chain efficiency.
91. What is the role of standardized work in Lean manufacturing?
Ans:
- Standardized work in Lean involves documenting and following the best-known methods to achieve consistency, reduce variation, and provide a foundation for continuous improvement. Standardized work in Lean manufacturing establishes consistent and efficient procedures for tasks.
- It involves documenting the best-known practices and ensuring that everyone follows them. This helps eliminate variations, reduces defects, and provides a baseline for continuous improvement.
- Standardized work also facilitates cross-training, making it easier for team members to fill in for each other, contributing to overall stability and efficiency in the manufacturing process.
92. How can Lean principles be applied to improve the onboarding process for new employees?
Ans:
- Lean improves onboarding by identifying and eliminating unnecessary steps, ensuring clarity in procedures, and providing a structured, efficient orientation process. Applying Lean principles to the onboarding process involves identifying and eliminating waste while enhancing efficiency. Streamlining documentation, creating standardized onboarding procedures, and incorporating visual aids can reduce unnecessary steps and improve clarity.
- Continuous improvement should be encouraged, with feedback loops from new hires to refine the onboarding process over time. By adopting a Lean approach, organizations can enhance the onboarding experience, making it more efficient and engaging for new employees.
93. What is the role of a Lean Champion within an organization?
Ans:
A Lean Champion is an individual responsible for driving and promoting Lean principles, facilitating training, and ensuring continuous improvement throughout the organization. A Lean Champion within an organization plays a crucial role in promoting and facilitating Lean principles and practices. They are typically individuals with expertise in Lean methodologies who advocate for continuous improvement. Their responsibilities include training and coaching teams, identifying improvement opportunities, and helping to implement Lean tools and techniques. The Lean Champion catalyzes change, fostering a culture of efficiency, waste reduction, and continuous improvement throughout the organization.
94. How does Lean address the concept of “timeboxing” in project management?
Ans:
- Lean uses timeboxing to set specific time limits on tasks or phases, promoting efficiency and preventing projects from exceeding allocated resources. Lean embraces the concept of “timeboxing” by emphasizing the importance of setting clear time limits for tasks or project phases.
- This helps in focusing efforts, reducing waste, and promoting continuous improvement. By adhering to time constraints, Lean aims to enhance efficiency and deliver value promptly in project management.
95. How can Lean principles be adapted for startups or small businesses with limited resources?
Ans:
Lean principles can be applied in startups by focusing on rapid experimentation, validated learning, and minimizing waste through a “lean startup” approach. Lean principles can be adapted for startups or small businesses by focusing on essentials. Prioritize customer needs, minimize waste, iterate quickly, and engage your team in continuous improvement. Embrace a lean mindset to optimize processes and deliver value efficiently, even with limited resources.