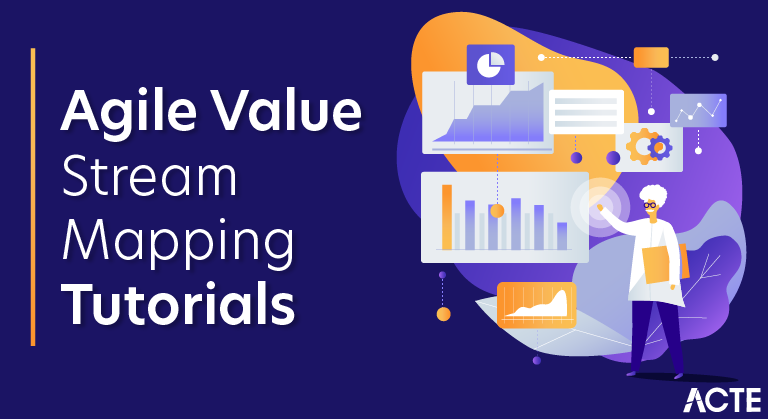
- Value stream mapping is a technique used to analyze the flow of information, people, and materials required to bring a product or service to a consumer. Value stream mapping is a concept that originated in Lean manufacturing methodologies. A typical process will consist of a series of steps and activities.
- These are classified as “value-adding,” that is, factors that add value to the customer and “non-value adding”, that is, factors that do not add value to the customer. Value stream mapping is a key tool to identify and eliminate process waste to increase efficiency, throughput, and effectiveness.
- Note that just being classified as “waste” does not mean the step or process is unnecessary. It is important to understand that ‘waste’ is not adding value to the customer and hence should be minimized or avoided.
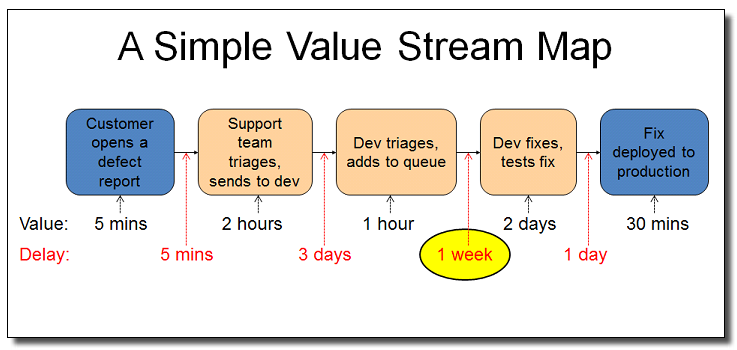
Value Stream Mapping – Stages
- Value stream mapping involves creating visual maps of the process, called Value Stream Maps. Value Stream Mapping progresses in the following stages:
Step 1: Start by identifying the product or service to be analyzed and the value being created by this process.
Step 2: Create a value stream map of the current process by identifying the steps, queues, delays, and information flows.
Step 3: Review the map to find delays, waste, and constraints. This can be done by reviewing the process and identifying activities that can be classified as waste. Also, identify the constraints if any.
Step 4: Create a new value stream map of the optimized state to be achieved in the future, by removing delays, waste, and constraints.
Step 5: Develop a roadmap to achieve the future state.
Step 6: Plan to revisit the process in the future to continually calibrate and optimize.
Value Stream Mapping-Steps
The steps involved in the value stream mapping process are as follows:
- Identify the start and end point of the process
- Identify high-level steps, inventories, and queues
- Identify support groups and alternative flows
- Classify activities as value adding and non-value adding
- Eliminate or minimize the non-value adding steps and optimize the process
Step 1:
- Identify the starting point of the process, that is, who initiates it and the endpoint that is, who gets the result of the process. For example, the objective is to get an approval of a story from the customer. The value stream mapping begins when you initiate the process of getting approval and ends when you and the customer agree on the story.
Step 2:
- Identify the high-level steps, inventories, and queues through the process. When these elements are arranged in a sequence and showcased using a flowchart, they depict the primary flow. In this example, the second step comprises the following activities:
- Select the story from backlog
- Meet the customer
- Determine Acceptance Tests
Step 3:
- Identify any supporting groups. These are added to the value stream flowchart, in turn, they become the alternative flows. In this case, on selecting the story from the product backlog, you get the story cards, which need to be considered for development in the iteration. If the customer is unavailable, the alternative flow would be to meet the customer representatives, who would act as a proxy customer.
Step 4:
- Classify each of the steps in the value stream as either a value adding or non-value adding activity. Please take some time to look at the illustration of this process given below. In this case, there are delays in between the workflow that is non-value adding activities. With these details, you can create the value stream of the system wherein the value adding activities span for 140 minutes and non-value adding activities span for 90 minutes.
- Once this demarcation is completed, you can compute the efficiency of the process cycle using the formula, total value-add time divided by total cycle time. The total value-add time is 140 minutes and the total cycle time which is the sum of value adding time and non-value adding time is 230 minutes prior to optimization. Hence, the process efficiency is 61%.
Step 5:
- Either eliminate or minimize the non-value adding activities thereby optimizing the process. After optimizing, compute the efficiency of the process cycle using the formula, Total value-add time divided by Total cycle time. Post the optimization, the total of non-value add time is reduced by 55 minutes, thereby the total cycle time is reduced to 195 minutes. Hence, the process efficiency has improved to 72%.
Value Stream Mapping – Example
- A subsidiary group of a publicly traded company produces a variety of products used in the metal brazing, cutting, and welding industries, and an array of gas-control equipment used in industrial, medical, and laboratory applications.
- As part of its continuous improvement drive, the group wanted to improve the preparation of chrome-plated components to assemble in its gas-pressure regulators. To achieve this goal, they decided to use the technique of value stream mapping.
Solution
- The group performed a Value Stream Mapping analysis. The given image depicts the analysis and implementation processes. The Value Stream Mapping tool provides detailed information on the flow of materials through a production process.
- It helped identify areas for improvement. The analysis revealed that to ensure a steady flow of these components through the production process, “supermarkets” have to be placed at various points along the production chain. Supermarkets are locations in which a standard amount of inventory is stored. When employees notice that the supermarkets are running low on materials, they restock them.
Outcome
- After reorganizing the production process, the group witnessed various improvements. For the last 18 months, there has been no shortage of components for assembly into regulators. There was a 75% reduction in WIP related to the components. This helped to minimize inventory costs leading to significant savings.
Following are specific steps smaller companies can take to prepare for and achieve Value Stream Mapping (VSM).
Step 1: Gather Preliminary Information
Before moving ahead with VSM, be sure to gather the following information:
- A history of your product mix from the previous year’s sales
- The volume of sales for each product sold from the previous year
- A list of your annual sales goals for the next year
- Any calculated assumptions from your sales and marketing strategy that will affect your sales for the next year
- This information will be useful in creating a history of your product mix, and the volume of sales for each product will help you apply Pareto’s 80-20 rule. In most cases, you will find that 20 percent of what you build represents 80 percent of your business in a typical year.
- For example, an analysis for a company revealed that although the company offered more than 100 different base products, only five made up 72 percent of its overall business. In this case, company management initially decided to limit the value stream map to those five base products.
- However, when management looked at the sales goals for the next year, three of the base products had targeted sales numbers that varied by 5 percent, and two new products with large projected sales volumes were planned for release. As a result, the analysis was modified so that seven out of the total number of base products amounted to 86 percent of the total business. This was the final analysis by which company management limited the scope of its value stream mapping activity.
Step 2: Create a Product Quantity Routing Analysis
- To create a product quantity routing analysis, start by listing all of your customers and the products you build for each of them. Be sure to stick to the basics when it comes to your products. Don’t get bogged down with the various options that can be added to your base product. List your base standard products that differ in form, fit, and function.
- Referencing your sales from the previous year, determine the volume for each product you made for your customers. Calculate the total number of products made, showing the volume of business generated from each customer to understand what your base demand was for the prior year. In, for instance, the total is 125 units.
- Determine the percentage of business that each product represents from your total number of units sold, and then identify the mix of products that represents around 80 percent of your business. That mix will be what you want to VSM, which will allow you to begin thinking of what a model line will look like in your operation. In other words, by value stream mapping the 20 percent of the products that represent 80 percent of your business, you can identify and eliminate waste from these in-demand products so that a majority of your business becomes more efficient.
- If you are a piece-part manufacturer (PPM), you also should start the process by making a list of your customers. Use that list to calculate the total number of finished piece parts you produced from the previous year. Then determine the percentage of business that each customer represents from the volume of parts you produced.
Step 3: Group Customers and Sort Materials
- The next step is to group your customers together by the industry they represent. Figure 3 shows the total number of finished piece parts along with the total percentage of finished piece parts that each industry represents.
- Sort out the number of material types by each industry and determine how many parts account for each type. the recreational vehicle (RV) industry has both aluminum parts and steel parts. (This scenario is very common for a PPM.) In this case, simply determine how many parts from the RV industry are aluminum and how many are steel. You do not need to keep all the customer’s parts together.
- The purpose of this exercise is to identify which product families you want to map. Many PPMs do not know what their product families are, and if you try to map every product family at once in a HMLV environment, it will become too complicated.
Step 4: Sort Product Families by Build Sequence
- The next step before VSM is to construct a process quantity routing analysis to identify product families according to a similar build sequence. With this information, you will know exactly what you are mapping through the flow of your operations.
- You have to know what parts or products flow through each work center and in what order. This helps you see which products follow the same routing sequence that logically make sense to group together. You might need to look at drawings you use to build the product to ensure you understand the routing of parts through the work centers.
Step 5: Choose One Value Stream to Begin With
- It is important to know what products or piece parts comprise 80 percent of your business and which products or piece parts of that 80 percent make sense to group together as a value stream (product family). Start by value stream mapping one value stream at a time to keep things simple. You may find that although your analysis is examining 80 percent of what you build, it might be useful to group together products or piece parts from the other 20 percent with other value streams.
- This could arise because they follow the same build sequence and have similar form, fit, and function. Don’t be so militant in following the 80-20 rule that you don’t leave room for flexibility when opportunities arise that are logical to include in your analysis
- So, when choosing a value stream to start with, consider the impact that value stream has on the business unit, such as:
- Highest percent of sales volume.
- Market changes affecting consumer demand.
- Profit margins of individual products.
- Warranty data affecting various product lines.
- Most enthusiasm from the company.
Step 6: Create an Operations Flow Chart
- Next, create a flow chart of all the operations in your value stream. Refer to work order routings or the bill of materials for the product value stream as needed to identify the steps and create a starting point.
Step 7: Walk the Shop Floor
- When it’s time to map the product family, the team needs to take a walk around the shop floor. The temptation will be to gather in a meeting room staring at numbers you ran from your MRP system without ever stepping foot onto your shop floor. That’s a sure way to miss wasteful activity that the MRP system doesn’t report.
- Walk through the steps of your value stream where the work is being done. Start at the end of the process, working your way upstream to the beginning, to get a customer-supplier perspective at each step. You will be able to see any waste that’s occurring and whether it is unnecessary or acceptable. Don’t rationalize waste and assume it is happening only because of a new operator in training or a new product design, as you will miss identifying opportunities for improvement.
Step 8: Collect the Data
- As you walk upstream through your value stream, you might be wondering how in the world you are going to collect all the data for each step! It can seem overwhelming for the team. Just remember to keep your team moving, and don’t get stuck in “analysis paralysis.” Data collection is important, but not at the expense of taking months to get anything implemented.
- The first step is to refer to the routings you have available in your MRP system. Conduct time studies where applicable and review the results with the operators. If the operators and your team agree with your results, then use this data to fill in the gaps in your data box for any process that is missing data. Operators can be the best source for information when the data is unavailable and you can’t conduct a time study.
- Another option is to use data from similar jobs. Referring back to your process quantity routing analysis, you should be able to identify other part numbers in your value stream that are similar. Run a report on a handful of similar parts in your value stream to give you some data to examine.
Step 9: Construct the Value Stream Mapping (VSM)
- Metrics and Measurements. On a separate sheet of blank paper, begin constructing your value stream using symbols to indicate what is happening at each process.
- At each step, be sure to measure the appropriate metrics as they apply to your process. This paints a good picture of the current condition at each process, despite what your MRP system says or what others might tell you.
- Which metrics should you measure” That depends on your process. The point of VSM isn’t data collection; it’s to show you where the value is created and where the waste accumulates in your process.
- Flow of Information. A VSM should show not only the flow of material, but also the flow of information. If you don’t know how information flows to the shop floor, you run the risk of processes waiting for instruction, creating downtime. You also have an incomplete picture of what you need to improve without first knowing how the flow of information will support your proposed idea.
- For example, let’s say you have a weldment that takes 100 hours to complete. You decide that you want to break this into two stages into two different workcells. While it might make sense to break the work out this way, how are you going to know which parts need to be routed to each workcell” How do you know when these parts need to be routed? How will the operators record their time? How will drawings follow the work order (if you use work orders)?
- When you start mapping the flow of information, you might discover why your lead-times are so long.
Step 10: Summarize the Data and Get the Big Picture
- When you have identified all the steps in your value stream and have filled in all the data applicable to your VSM, it’s time to put it all together. Figure 8 demonstrates what a sample VSM should like when all the data has been collected. With this format, your team can stand back and look at what the data is telling you about the flow through your process.
- Remember, the point isn’t to put together an artistic portrait of the flow through your value stream, but to use your VSM to see where the value is being created and identify where wasteful activity occurs. To help you find the waste, examine the process and ask yourself, “If the customer were to walk through each step of this value stream with his checkbook in hand, would he be willing to pay for each step he sees””
- In addition, looking at your VSM, take the list of kaizen opportunities you identified in this process and begin prioritizing them by level of impact an improvement will make to the flow of your value stream. This will give your team an organized plan of action for where to start making improvements to your value stream.
- With your VSM in hand, you are armed, ready, and well on your way to eliminating waste and learning to see the whole picture. Keep in mind that learning to see is not only the first step in creating a lean organization—it is half the battle.
Benefits of a value stream map
- By creating a value stream map, you can visualize how end-to-end operations work, track actual performance, and find ways to make your processes even more efficient.
Here are some of the benefits of value stream mapping:
- Identify waste
- Identify bottlenecks
- Make processes efficient
- Improve cross-functional collaboration
- Improve end-product quality
Value stream map gives teams and businesses an organization-wide perspective on lean project management, but the goal isn’t simply to identify the current state of affairs.
In addition to mapping the current state, value stream mapping helps businesses visualize an ideal state of operations in project management, giving everyone in the organization a tangible goal to work towards.