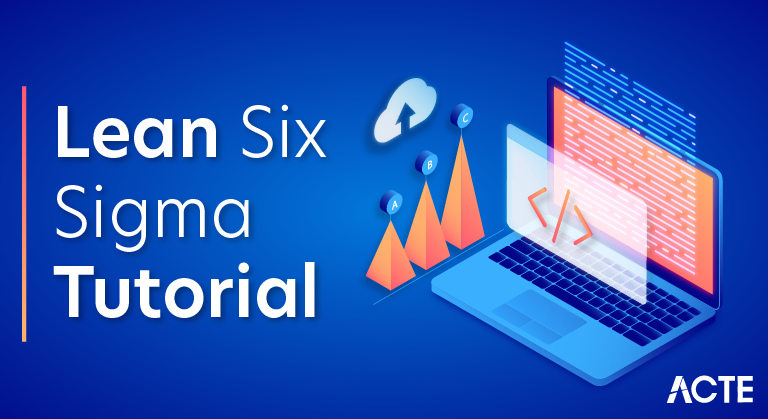
- Lean Six Sigma is a process improvement methodology designed to eliminate problems, remove waste and inefficiency, and improve working conditions to provide a better response to customers’ needs.
- It combines the tools, methods and principles of Lean and Six Sigma into one popular and powerful methodology for improving your organization’s operations.
- Lean Six Sigma’s team-oriented approach has proven results in maximizing efficiency and dramatically improving profitability for businesses around the world.
- Still wondering, “What is Lean Six Sigma exactly?” Read on for an in-depth dive into what it is, why it matters, and how to do it right.
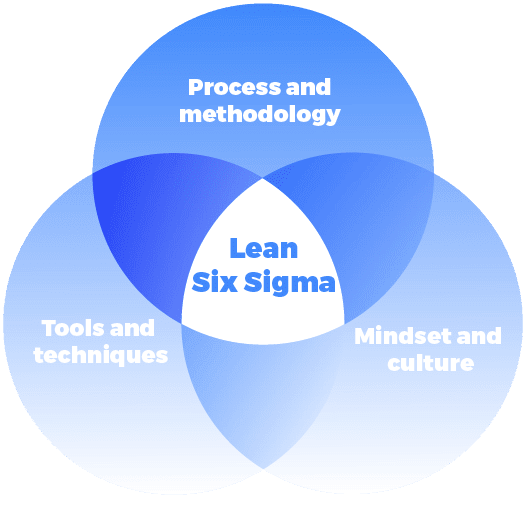
There are three key elements to Lean Six Sigma.
Tools and techniques:
A comprehensive set of tools and analytical techniques that are used to identify and solve problems.
Process and methodology:
A series of phases that organize the use of the problem-solving tools to ensure that the true root causes are found and that a solution is fully implemented.
Mindset and culture:
- A way of thinking that relies on data and processes to achieve operational performance goals and continuously improve.
- These three elements reinforce each other. Analytical techniques are not used effectively unless there is a process for applying them and a mindset of continuous improvement creating the need for them.
- An improvement process does not produce the desired results unless it includes the tools and techniques that define the activity of the process steps and there is a culture that insists on systemic data-based approach to solving problems.
- Finally, a culture that seeks to continuously improve will be frustrated if there are no tools and techniques for analysis and no process or methodology that can be applied to organize and focus the improvement efforts. Fortunately, the Lean Six Sigma approach to business improvement includes all three layers.
That is continuous improvement?
- Continuous improvement as a business strategy and discipline developed as an offshoot of Frederick Winslow Taylor’s Principles of Scientific Management. Taylor described business as a series of interlocking workflows or processes that should be managed using data.
- In the 1930’s Walter Shewhart developed a set of management disciplines for process control and continuous improvement. These disciplines were based upon Taylor’s principles of business workflows and a reliance on data. Shewhart’s work is the foundation for the engineering and management disciplines of Quality Assurance and Quality Control found in most organizations today.
- One of Shewhart’s students and proteges was Edward Deming, who used these principles to remake the Japanese automotive industry into a global quality and engineering powerhouse following World War II.
What is Lean?
- Lean was developed in Toyota as part of the Toyota Production System, which was built around the work of Shewhart and Deming. Toyota had been a client of Deming and established its operational management practices on the principles he taught. The fundamental driver of Lean is the elimination of waste.
- In fact, a good description of the Lean approach is, “a set of tools that assist in the identification and the steady elimination of waste.”
- If a company is doing large-scale, high-quantity production like Toyota; then a process with waste in it means that company is creating large-scale, high quantity waste. No company wants to do this. The Lean approach uses tools to analyze the business process.
Five principles of lean manufacturing
Value
- Value is determined by what the customer considers to be important within a product or service, rather than what the individuals developing or delivering the product or service consider important.
Value Stream
- The set of business activities and steps involved in creating and delivering products and services to the customer; it is the connection of the steps together rather than considering each step in isolation.
Flow
- The degree to which there is smooth uninterrupted flow of activities that add value to the customer, rather than waste and inefficiency that impedes the flow through the value stream.
Pull
- The degree to which the value stream is only processing products and services for which there is a customer demand, rather than creating something and hoping someone wants it.
Perfection
- The continuous assessment of value stream performance to identify and improve the value created and delivered to the customer, rather than resisting changes that improve the process of creating and delivering customer value.
Three types of waste
Using the terms of the Toyota Production System, the Lean methodology identifies and strives to eliminate three types of waste:
- Muda
Non-value added work – pure waste. - Mura
Unevenness in flow – unpredictable variation requires compensation elsewhere in the system. - Muri
Over-burdening resources beyond their normal rated capability – stresses and damages resources so that they are unable to do a normal workload. - As you can probably tell from both of these lists, the principles of Lean can be applied to any business process or operation, not just manufacturing. It is now used in literally all functions and all industries.
What is Six Sigma?
- Six Sigma was first developed at Motorola during the late 1980s. The methodology was pioneered by Bill Smith, a quality engineer, whose goal was to improve the way the quality and measurement systems worked so as to eliminate errors.
- The Motorola systems tolerated error rates that created too much scrap, rework, redundant testing and often customer dissatisfaction.
- The Six Sigma approach focused on identifying and eliminating anything that caused variation in the process. When the variation is gone, the process results can be precisely predicted – every time.
- By designing the system so that these precisely predictable results fall within the zone of acceptable performance from a customer perspective, process errors are eliminated.
- But the engineers at Motorola went one step further. They knew from experience that many process changes were not effective because they did not get to the root cause of the problem. Also, the changes they made would not stick, as the operators reverted back to doing things in the original manner over time. Six Sigma was organized with five phases to address these issues.

What are the five phases of Six Sigma?
- Define
In this phase the boundaries for the process being analyzed are set and the expectations or desired performance for that process are defined from a customer perspective. This is to ensure a change does not degrade the customer experience, but instead enhances it. - Measure
In this phase the current performance of the process, product or service is measured to determine what is actually occurring, especially from a customer perspective. This is to ensure the analysis and solution are based on actual performance, not theoretical or anecdotal information. - Analyze
In this phase the process, product or service is analyzed using the measured data to determine the source or sources of the variation that are causing the problem. This is to ensure the true root cause(s) is identified and not just a symptom. - Improve
In this phase the possible changes to the process, product or service are assessed and a solution set of changes is designed and tested. This is to ensure the solution creates the desired effect and that the variation is reduced or eliminated. - Control
In this phase the changes are implemented, the supporting systems are also updated and the process, product, or service is put under control – normally statistical process control – to ensure the solution is fully implemented in a sustainable manner and to identify if performance starts to degrade. - The methodology of Six Sigma will work with any process, product or service that has a definable performance goal and measurable characteristics, because the methodology heavily relies on data.
Similarities and differences
- Lean and Six Sigma have been combined because, although they are different, they are complementary. The similarities allow them to mesh together well. The differences ensure that there are analytical tools and solution options available that will improve the process, product or service.
- It is due to the similarities that both types of analysis can be done simultaneously on the same process, product, or service.
Similarities of Lean and Six Sigma
- Both rely on a definition of value that is based upon the customer experience. The customer is king (or queen).
- Both use a process flow mapping approach to understand the process. Even when the analysis is based upon a product or service, there is a process that is associated with creating and delivering that product or service.
- Both rely on data for determining current performance and for determining the impact of future performance. The data collected in a Lean Six Sigma project can often be used to support both Lean analysis and Six Sigma analysis. The reliance on data helps to ensure that the true root cause is identified.
- Both are applied using improvement projects that typically will be implemented by a small cross-functional team. The duration of the project and the size of the team will depend upon the scope and scale of the process, product or service being analyzed for improvement.
- Both have migrated beyond the manufacturing operation and are now used for all functions and for all internally facing and externally facing processes. They are also used in all industries including industrial, consumer, government, education, and nonprofits.
- Improvements based upon using either approach will normally both reduce waste and reduce variation. Removing wasted steps and activities (muda) eliminates sources of variation, and removing variation eliminates wasted process capacity and steps associated with accommodating the variation (mura and muri).
- However, there are some differences in the two approaches. These differences do not create a conflict, rather they provide multiple paths that can be used to reach a similar destination. A Lean Six Sigma project should let the nature of the defect, as defined by the customer value, and the current state of the process, product, or service dictate which sets of tools are most appropriate. The final solution is often a hybrid combination of both Lean improvements and Six Sigma improvements.
What is the difference between Lean and Six Sigma?
- Different focus for problem identification – Lean is focused on waste (muda, mura, muri) and Six Sigma is focused on variation, any deviation from the target performance.
- Different types of techniques – Lean primarily uses visual techniques for both analysis and solution creation that are supported with data analysis. Six Sigma primarily uses statistical techniques for analysis and solution creation that are supported with data visualization. This leads to a myth that Lean is easier than Six Sigma, because the visual analysis of Lean is easy to understand, while many people are intimidated by Six Sigma’s numerical analysis. The reality is that both types of analysis are easy to perform with today’s statistical support tools.
- Different types of documentation for the solution – the Lean solution is documented with a revised value stream map that leads to changes in workflows and often changes in work instructions at many of the steps in the process. The Six Sigma solution is documented with changes in setup procedures and the control plan for monitoring the process and responding to variation. It will also impact work instructions and frequently leads to changes in the measurement approach or systems.
Lean Six Sigma principles
- Let’s outline the principles that have helped to make Lean Six Sigma so effective. I have been directly involved in the successful implementation of Lean Six Sigma in many organizations, and I have done consulting in several organizations who had tried and failed to implement an effective Lean Six Sigma program.
- In the successful programs, the following principles were adopted. In the failed implementations, at least one or more principles were not followed.
Addressing a real-world problem
- Lean Six Sigma is both a top-down and bottom-up methodology. The top-down element is associated with problem selection. The Lean Six Sigma project teams are focused on real-world problems that are impacting customers and processes right now.
- Often the team members are feeling the effect of the problem with rework and repair activities or addressing customer complaints. This lends a sense of urgency and importance to the project. It is not just “busy work,” it is real work.
- One of the reasons for the failure of the Quality Circle programs of the 1980s was that every team could choose its own project. While this sounds great for empowerment, often the projects selected were not real-world problems. In one organization I worked with, one of the first projects selected by a team was to repaint the lunch room and put up new curtains. Soon the whole initiative was viewed in the organization as a “fun” party time activity, but not related to real business improvement.
- It is often hard to get the organization to recognize the importance of this methodology for business success. Buy-in is much easier to achieve when both management and the team understand the importance of identifying and fixing the problem. But management does not dictate a problem and solution. Rather the analysis by the team determines the true root cause.
Analysis is accomplished by a team
- A Lean Six Sigma project is normally staffed by a cross-functional team that is involved with different aspects of the process being analyzed. Many business processes are cross-functional and a cross-functional analysis is needed to prevent sub-optimization of the process. Improving one step at the expense of another step does not eliminate waste or variation, it just moves it to a different step in the process.
- A problem I have seen in several Lean Six Sigma implementations was that the Green Belt and Black Belt project leaders worked on their own to find and fix the problem without the help of a cross-functional team. If the process and problem were small and the project leader understood the process, this would prove effective. However, with large cross-functional processes and projects, or in some cases when the project leader had no background in the type of process or problem being analyzed, the projects would become stalled and delayed.
Analysis is focused on a process
- Lean Six Sigma is best used for analyzing processes. Even when the problem under investigation is an obvious product problem, Lean Six Sigma will be much more effective when it is applied to the process that designs or builds the product, rather than looking at just the product itself. That is because the analysis is meant to investigate and improve actions, and actions are the steps of processes.
- Actions seldom happen in a vacuum with no impact from preceding or succeeding actions. Instead they must be considered in the context of the process in which they are occurring. The Lean value stream map or Six Sigma process map provide a picture of that process.
- On numerous occasions, I have found that the creation of a map of the process immediately led to an understanding of what was happening, and recognition of some of the underlying problems that are hidden when an individual is only aware of their step in the process. On a few occasions I have encountered a project team that focused solely on a product defect without considering the process that created or used the product. While they could identify the defect, they could not determine the actual cause and create a solution until a process map was created.
Analysis is based upon data
- Lean Six Sigma relies on data, not guesses. The Lean value stream map is verified with a walk-through of the process, and then data is collected at each step. The current condition of the process, product or service is measured in the Measure phase. This includes measuring the problem or defect and measuring anything that is done correctly.
- The data that is captured is used for analysis to determine the actual state of what is happening, not an assumed state. This analysis verifies the underlying causes so that the correct problem is fixed. But the reliance on data does not stop there. When a solution has been created, data is collected to determine if the solution has truly fixed the problem. And then data is used to ensure the solution stays in place and the problem does not return.
- One of the challenges that continuous improvement and problem-solving initiatives have had over the years is a difficulty accepting the reality of the current conditions. Businesses are often in denial about problems and issues. I recently worked with a company that was implementing Lean Six Sigma. One of the initial project teams was tasked with resolving a product issue that created large levels of rework in their operation and was the source of numerous customer complaints. The problem had been “solved” on numerous occasions by putting tighter controls on the process step that “caused” the problem. Except when we actually measured what was happening in each step, we found the problem was really due to several other factors.
- Because of “politics” and paradigms, the management at first rejected the analysis. But when presented with the data, they eventually recognized where the problems were originating and an effective solution was implemented. It was the data that finally broke through the paradigms about the problem.
Understand the impact of the process sigma
This next principle is focused on the Six Sigma analysis. The practical impact of sigma is that it represents the amount of normal variation that occurs. It is always tied to a specific parameter or characteristic that is being measured. Same attributes of a product or process will have virtually no variation.
That attribute never changes, no matter how often the product or process occurs. Other attributes do have variation. There is an average value, but there is uncertainty about any specific instance. Sigma is the statistical measurement of that uncertainty.
- One sigma represents the boundaries for a little over two thirds of the occurrences.
- Two sigma represents 95% of the occurrences.
- Three sigma represents over 99% of the occurrences.
- By the time you get out to six sigma, there are only about 3 chances in a million that normal variation could cause the attribute being measured to be that different from the average value.
Sigma represents variation, it says nothing about acceptability. Notice that I haven’t yet mentioned whether the attribute being measured is acceptable from a customer or standards viewpoint. An attribute could have a very small sigma, essentially no variation. But if the average value of that attribute is outside the bounds of what the customer finds acceptable, it just means that it is always defective.
By the same token, an attribute could have a very large sigma, there is a high level of uncertainty. But if the customer has no expectations concerning that attribute, it will always be acceptable regardless of the variation.
Solution addresses the real root cause(s)
- Lean Six Sigma is one of the most powerful problem-solving and continuous improvement methodologies because it identifies the characteristics of the real problem. Some methodologies start with the assumption that every problem has a unique or special cause, and if that cause can be identified and eliminated or controlled, the problem goes away. Other methodologies start with the assumption that the problem is a common occurrence within the process. The process is fundamentally flawed or inadequate and if the process were changed to avoid this flaw or correct this inadequacy, the problem goes away.
- Both goals are admirable and in fact are actually quite similar. But the way to fix the first problem is to put in place a “spot correction” to control the unique cause, and the fix for the second approach is to re-engineer the process. Unfortunately, selecting the wrong solution strategy does not improve the situation and can often make things worse. Lean Six Sigma employs the tools to differentiate between whether the problem is a special cause or a common cause.
Solution includes a control system to help it “stick”
- Lean Six Sigma does not end with identifying the problem or even with implementing a solution. The final phase of Lean Six Sigma is the Control phase. There is a natural resistance to change in most organizations. For many people and systems, change is hard. Habits must be broken, new methods learned, new information is required.
- In the Lean Six Sigma Control phase, the solution is implemented and the organization begins to use it. While this is happening, the project team is ensuring all of the supporting systems are also updated to reflect any changes and they provide training and coaching for process operators and managers on the use of the solution.
- This even includes ensuring the control systems that monitor the process are in place to identify if the process begins to revert back to the previous behavior. The project team does not declare victory and disband just because they have successfully demonstrated their solution once. Rather they stick with it through a statistically significant number of occurrences. This both demonstrates the solution really solved the problem and that the operators and managers are equipped and able to manage the improved process.
- I worked with a company in Chicago at one point to address a recurring problem in their purchasing department. The solution was a straightforward process change to eliminate a common cause problem.
- As I looked over the historical documents associated with this problem, I found that the previous solutions were similar to the one we had developed. They had been put it place and used for a year or two, and then slowly modified until the problem returned. The reason for the modifications was based upon how the senior management measured the effectiveness of the purchasing department. Rather than measuring the entire purchasing process, the measurements were tied to one step in the process.
- Optimizing that step led to sub-optimization in several other steps which created the problem. This time when a solution was implemented, I made sure the corporate measurement system was modified to measure the entire purchasing operation and not just one step. These are the types of issues often addressed in the Lean Six Sigma Control phase.
Benefits of Lean Six Sigma
- Lean Six Sigma is a continuous improvement methodology. However, a legitimate question is, what does it improve? Does it increase sales or profits?
- Does it improve customer satisfaction and lower complaints?
- Does it lower costs, improve incoming quality, outgoing quality or the cost of quality?
- Does it improve employee morale?
- Does it increase your pay and benefits, or improve your promotability?
- Does it create world peace and solve world hunger? “Yes” to all of these – except the last two. Let’s look at benefi
- ts for the business and then benefits for the individuals who attain a level of certification in Lean Six Sigma.
Organizational benefits
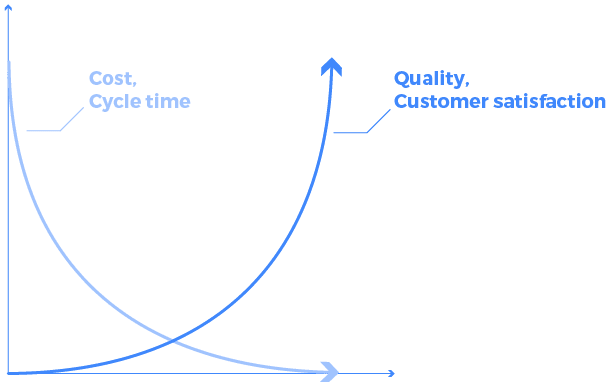
- Lean Six Sigma is a continuous improvement methodology for an organization. So, we would expect organizational benefits. In fact, the General Electric company has claimed to have realized over $2 billion of cost savings from Lean Six Sigma. Let’s consider the nature of the benefits and their implications.
Simple processes
- Lean Six Sigma will simplify the business processes. The cross-functional value stream maps will identify areas of waste and inefficiency. Many of the processes have embedded rework and work-arounds for persistent problems. When the wasted effort is removed and the rework and workarounds are no longer needed, the remaining processes are simple and often much easier to manage and control.
- This results in a faster process, which leads to better customer service and higher customer satisfaction. Both of those will normally lead to greater sales. In addition, the simpler, faster process will lower overhead costs which will increase profits. Finally, simpler processes have fewer opportunities for errors. Therefore, they normally are characterized by higher quality and fewer defects.
Fewer errors and mistakes
- Let’s dig deeper into that benefit of fewer errors and mistakes. Lean Six Sigma starts with a definition of acceptable quality based upon what the customers value. This external focus on quality prioritizes the continuous improvement efforts to address the problems that have the most impact on business success.
- In addition, the reliance on data to define problems rather than gut feel or anecdotes further prioritizes the improvement effort on the real problems in the organization. The result is that the improvements fix real problems and bring them to a level that is acceptable to the real customers. So, it is not just that Lean Six Sigma addresses errors and mistakes in the business, but rather that Lean Six Sigma addresses the errors and mistakes that matter the most.
Predictable performance
- Simple processes are easier to control and manage than complex processes, especially those processes with fewer errors and mistakes. But added to these benefits, Lean Six Sigma has a focus on reducing variation within a process. With less variation, processes become more predictable. That means predictable cycle time, predictable quality output, and predictable costs.
- And these can lead to better customer service, fewer complaints, and higher profits. This predictability becomes a tremendous advantage for an organization when operating in an environment of fast moving changes. Changing technology and customer expectations are already creating an unstable business environment. Without predictable processes it is almost impossible to create and implement an appropriate reaction to this instability.
Personal benefits
- Lean Six Sigma provides benefits for individuals within the organization who become Lean Six Sigma leaders. We will discuss the various leadership roles in more detail in a later section. First let’s identify some of the personal benefits you can expect when participating in Lean Six Sigma.
Personal effectiveness
- Lean Six Sigma provides a structured problem-solving methodology that can be used to address any type of problem. Being able to find and fix problems will improve your ability to perform in any position and industry.
- The Lean Six Sigma methodology steers you through an organized process of inquiry, analysis, problem identification and solution creation. Many of the tools and techniques can be applied to everyday problems and issues. But even if you don’t use all the tools, the organized problem-solving approach will put you in control of finding and fixing your problems.
- I have used this approach when fixing problems at my house, with local charities I support, and of course in many different business settings.
Leadership opportunity
- Lean Six Sigma is implemented through projects and projects have leaders. Leading a Lean Six Sigma project will often provide an opportunity for exposure to other functions and senior management. This exposure is in the context of someone who can find and fix a problem.
- Interacting with team members and managers will likely improve your communication and decision-making skills. The structure of Lean Six Sigma can help you to develop your project management skills.
- And of course being able to put on your resume that you led a project team that achieved cost savings, quality improvement, and cycle time reduction will only help you as you seek that next promotion or new opportunity.
Pay and promotability
- Which brings us to the pay and promotability of Lean Six Sigma practitioners. Attaining belt certification is a valuable credential on your resume. Many job postings require that an applicant have a Lean Six Sigma credential.
- So, this will open the door for some promotions. In addition, within an organization, promotions are often based upon how you have demonstrated your leadership skills. Effectively leading a Lean Six Sigma project shows senior management and HR that you are ready for greater responsibility. The average annual salary in the USA for Lean Six Sigma Black belts is just under $100,000. The average for your industry and country will vary. However, it is safe to say that Lean Six Sigma certification will enhance your earning potential.
Industries and functions using Lean Six Sigma
Lean started in the process engineering department of an automotive manufacturer and Six Sigma started in the quality department of a high-tech system manufacturer. However, the methodologies have moved well beyond their roots in quality and process engineering. I have either participated on or coached Lean Six Sigma projects in virtually every business department including:
- C-Suite
- Call Center
- Customer Service
- Design Engineering
- Field Sales
- Finance
- Human Resources
- IT
- Legal
- Logistics
- Maintenance
- Manufacturing Engineering
- Manufacturing Operations
- Marketing
- Process Engineering
- Purchasing/Sourcing
- Quality
- R&D
- Sales
- Test
Lean has also moved well beyond the realm of manufacturing. Many industries have embraced Lean Six Sigma, and the list of companies using the methodology is much too long to be included here. In some cases the emphasis will be primarily on Lean, in some on Six Sigma, and in many it is the combination of Lean and Six Sigma.
- Agri-business
- Aviation
- Banking
- Electronics
- Financial Services
- Government
- Higher Education
- Hospitals
- Manufacturing
- Medical Devices
- Mining
- Oil and Gas
- Pharmaceuticals
- Retail
- Telecom
- Transportation
Lean Six Sigma belts
- So far we have discussed the background of Lean Six Sigma, the principles embedded in Lean Six Sigma and some of the benefits. You are probably asking, when are we going to explain how it works?
- Well, now is the time. Let’s go through the key roles and responsibilities, the five-phase structure with gate reviews, and then do a quick overview of some of the more commonly used tools and techniques.
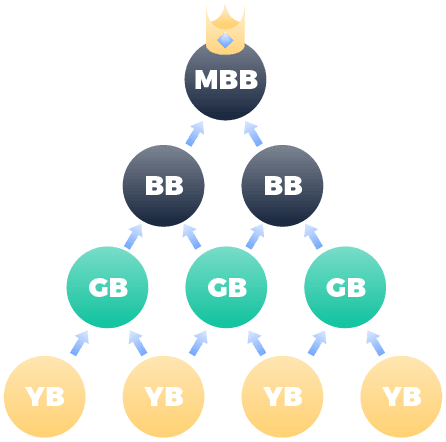
- Lean Six Sigma has adopted the roles from the Motorola Six Sigma methodology, which borrow the naming convention of the progression of mastery used within martial arts. Some organizations have their own levels and definitions of mastery. However, I will be describing the most commonly found levels in use today.
- You may have heard of Lean Six Sigma belts – these are the Yellow Belt, Green Belt, Black Belt, and Master Black Belt. Each of these roles are expected to have training, and in many cases certification appropriate to their role.
- In the early years of Lean and Six Sigma, every organization established its own standards with regards to methodology and tools and techniques. However, most organizations now rely on an independent certifying body for training and certification.
- The two most widely recognized organizations that provide certification are American Society for Quality (ASQ) and the International Association of Six Sigma Certification (IASSC). The GoSkills Lean Six Sigma courses are aligned with the IASSC Body of Knowledge. Let’s look at each of these roles in more detail.
What is Lean Six Sigma Yellow Belt?
An organization can have many Yellow Belts. These individuals are team members on a Lean Six Sigma project led by a Green Belt or Black Belt. They should be familiar with the structured methodology and the use of cross-functional tools and techniques.
- They will participate in all the project team meetings acting in the role of subject matter expert for their function or discipline. This role is performed in conjunction with their normal full-time job or position.
- A project will have as many or as few Yellow Belt members as are needed based upon the scope of the process being investigated and the nature of the problem.
- The training for a Yellow Belt normally focuses on the structure of the methodology and the use of the cross-functional problem-solving tools and techniques.
- The detailed Lean and Six Sigma analysis is normally handled by the Green Belt or Black Belt who is leading the project. However, the Yellow Belt team members are often the ones who collect the data used in analysis and help to interpret the results of the analysis.
- The Yellow Belt team members will also lead the implementation of the solution within their respective function or discipline.
- It is common for a person with Yellow Belt certification to be a member of multiple Lean Six Sigma project teams.
What is Lean Six Sigma Green Belt?
An organization will have multiple Green Belts. The Green Belt role is normally that of a project leader. The Green Belt is typically working on Lean Six Sigma projects that would fall within their area of expertise and responsibilities. These individuals know the Lean Six Sigma methodology and structure. They are also able to apply the Lean analysis tools and the statistical techniques commonly used with Six Sigma.
- These individuals lead small projects or projects that are focused on just one function. This role is normally performed in conjunction with another full-time position.
- Most Green Belts are leading a project that is associated with improving some aspect of their business processes. In some cases, a Green Belt may be assigned to a large cross-functional project being led by a Black Belt.
- Large cross-functional projects often have multiple analyses occurring simultaneously and a Green Belt will lead each of those efforts.
- As project leader, the Green Belt is responsible for ensuring that appropriate Lean Six Sigma tools and techniques are used at each phase on the project.
- This individual will normally lead the presentation and discussion of the project at the phase gate reviews. Because this individual is often the only person on the project who has been trained in the Lean analysis techniques and the statistical Six Sigma techniques, they will conduct these analyses.
What is Lean Six Sigma Black Belt?
An organization will often have multiple Black Belts. The Black Belt role is that of a subject matter expert on Lean Six Sigma for a function or location within the organization. These individuals lead large cross-functional projects and serve as coaches for the Green Belts in that department or location. This is normally a full-time position.
Black Belts know not only know how to apply the methodology and tools, they are the trainers and coaches for the Green Belts and Yellow Belts within the organization. A typical day will include:
- Conducting a team meeting for one of the project they are leading;
- Meeting with several Green Belts to review their progress and provide coaching for their next steps;
- Performing value stream or statistical analysis with data from one of the projects they are leading;
- Provide training on the use of Lean Six Sigma within their organization for Yellow Belt and Green Belt candidates;
- Meet with organizational stakeholders to discuss the status of projects and identify problems or issues for future projects.
What is Lean Six Sigma Master Black Belt?
The final level is that of Master Black Belt. Most organizations will have only one Master Black Belt, someone who is normally a senior individual responsible for managing the Lean Six Sigma initiative within the organization. This is a full-time position. Many times this Master Black Belt reports to the C-level champion for the Lean Six Sigma initiative.
- From a training and certification standpoint, this individual has the same credential as a Black Belt. However, the role and responsibilities are different.
- The Master Black Belt is not managing projects, rather they are managing the initiative.
- The Master Black Belt is normally working closely with senior leadership to determine how many Black Belts and Green Belts are needed and which functional departments or locations should get them first.
- The Master Black Belt normally maintains a status report on the portfolio of Lean Six Sigma projects; the active ones, the completed ones and the proposed ones. As such they are able to assess the impact of the overall program on the organization and they can prioritize the improvement efforts based upon the organization’s strategy.
- These individuals also work with HR to maintain the training records of all the Yellow Belts, Green Belts, and Black Belts in the organization.
- If an organization is small, or if the Lean Six Sigma initiative is small within the organization, the role of the Master Black Belt will be assumed by one of the organization’s Black Belts.
How is the Lean Six Sigma DMAIC process defined?
- Each phase has an organizing premise or question that must be addressed. Once the question is satisfactorily answered, the project can proceed to the next phase. The duration of the phase is based upon the information and data that is available. Normally at the end of each phase there is a phase gate review with the stakeholders and one or more Black Belts. Let’s take a look at each phase in more detail.
Lean Six Sigma tools and techniques
- Now that we have covered the structure and process of the Lean Six Sigma methodology, let’s look at the tools and techniques. Many of these tools and techniques were in use long before the Lean Six Sigma methodology was formulated, and have been incorporated into this methodology.
- One of the powerful aspects of Lean Six Sigma is that multiple tools are available for use in each phase. A team can then choose the tool or technique that best fits their unique situation. Organizations will often have a favorite set of techniques based upon their corporate culture or historical preferences.
- The statistical analysis tools and techniques are often associated with the Six Sigma portion of the analysis. The statistical tools help us to make sense of the data and to determine what is significant and what is not. The use of statistical software such as Excel Analysis Tool Pak or the Minitab application has minimized the amount of mathematical computation that the team members must do. However, they still need to understand which statistical techniques to use in each situation and how to interpret the results.
- Process Capability – this is a statistical ratio that compares the normal process variability with the customer or specification limits. It is expressed with process capability indices of Cp, Pp, Cpk, Ppk, or process sigma. The process capability ratio is an excellent predictor of whether the process will be able to deliver defect-free results.
- Descriptive Statistics – these are statistics that describe the normal behavior of a measured parameter within a process or product. It includes the mean, median, mode, and standard deviation.
- Inferential Statistics – these are statistics used to relate the statistical performance of a sample to the statistical performance of the larger data population that the sample represents. These statistics are based upon the sampling approach used and include confidence interval and confidence level.
- Measurement System Analysis – this is a comprehensive analysis of an inspection or test systems ability to correctly determine a measured value within a process or product. It includes an assessment of accuracy, precision, stability, linearity, and discrimination.
- Gage R&R – this is a subset of a typical measurement systems analysis that focuses on the precision of the measurement system. It is a set of experiments using products or processes with predetermined known values and measuring them to determine whether the measurement system will consistently assign the same values.
- Hypothesis Tests – These are statistical tests of a data set to determine whether an assumption about the data can be verified or not. Typically, it is used within Lean Six Sigma to determine if data samples are similar or if there is a statistical difference. If data sets can be shown to be dissimilar, that is an indication that the factor which separates the two data sets has a significant impact on process or product performance. There are many different statistical techniques used depending upon whether the data is normal or non-normal, continuous or discrete, and the number of data sets or parameters being evaluated.
- Correlation – this is a hypothesis test that is used to show whether two continuous data parameters are related, and how they are related.
- Regression Tests – this is a hypothesis test that determines the mathematical relationship between two or more continuous data parameters.
- T Tests – this family of hypothesis tests is used to compare the descriptive statistics of two data samples to determine if they are similar.
- ANOVA – this technique is used to compare the descriptive statistics of two or more data samples to determine if they are similar.
- Tests of Proportions – this family of hypothesis tests is used to determine if two samples of discrete data are similar.
- Chi-Square Test – this technique is used to determine if two or more samples of discrete data are similar.
- Design of Experiments – this is a statistical technique for creating a set of tests with test specimens that are designed to include or exclude certain features and with attributes set at the minimum or maximum level. Based upon the set of experiments, a best case design can be created with the appropriate design features and design targets. This technique is often used when creating a new product or process during the Improve phase.
- Control Charts – these are charts that track the performance of selected process or product parameters and determine whether the variation that is displayed is due to common causes or special causes. There are many different control chart designs, based upon the characteristics of the data and the attribute being measured. These charts are normally used in the Control phase as means of ensuring the improved process performance is sustained.
Project and team management tools and techniques
Lean Six Sigma projects must also be able to interact with stakeholders and customers. There are several techniques that have proven effective in this regard. Some of these are based upon understanding the perspective of external stakeholders and some of these are useful for organizing and communicating with internal stakeholders, such as team members.
- Critical to Quality (CTQ) – these are the process, product, or service parameters that are the attributes of customer value. They are determined by the stakeholders, not the project team.
- Project Charter – this is a project management document used to authorize the project and provide boundaries on the scope of the activity. The format varies from organization to organization.
- In-frame/Out-of-frame – this technique is used to clarify boundaries for a project team. The scope of the project is described in the frame. Areas that are not to be included in the analysis are listed as out-of-frame.
- SIPOC – This stands for Supplier, Input, Process, Output, Customer. It is a technique used to define the limits of the process that is being analyzed and to clarify the stakeholders for the process.
- Cross-functional team – this refers to the makeup of the Lean Six Sigma team. Normally there is at least one representative from each function who has responsibility for performing activities within the process being studied.
- Team decision-making – this is a set of practices used by teams to reach consensus when making decisions. Although many of the team conclusions are determined by the results of the data analysis, there are still decisions to be made in team operation, solution development, and implementation planning.
- Stakeholder management – this is a set of practices that are used to identify the key stakeholders for the Lean Six Sigma project. The key performance goals and communication pattern are also established for each stakeholder.
- Culture change management – this is a set of communication and implementation practices that focus on building buy-in and support for changing processes and work practices. This is often needed during the Improve and Control phases to ensure the solution is viable and sustainable.
- Implementation planning – the implementation of the solution is often a project as big or bigger than the Lean Six Sigma analysis project. This is a set of project management practices used to plan and execute a project.