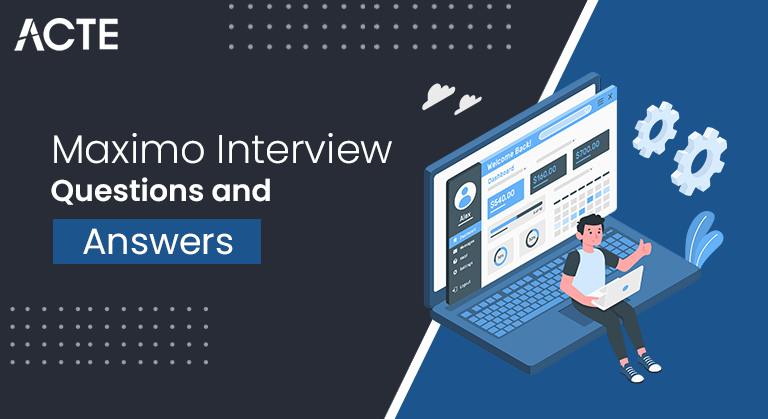
Maximo is an enterprise asset management (EAM) software solution created by IBM. It is intended to assist organizations in managing their assets, such as facilities, equipment, vehicles, and other physical assets, during their entire existence. Maximo offers capabilities for asset planning, procurement, tracking, maintenance, and retirement to improve performance and dependability. In addition to these key functions, Maximo includes condition-based monitoring, predictive maintenance, and mobile access. The programme integrates with other corporate systems, providing for smooth data transfer between Maximo and other business applications.
1. What is Maximo?
Ans:
Maximo, short for IBM Maximo Asset Management, is a comprehensive enterprise asset management (EAM) software solution developed by IBM. It is designed to help organizations manage their assets throughout their entire lifecycle, including facilities, equipment, vehicles, and infrastructure. Maximo provides a centralized platform for organizations to streamline asset-related processes, optimize maintenance activities, and enhance overall operational efficiency.
2. Explain the key features of Maximo.
Ans:
Key features of Maximo include robust asset tracking and management, preventive maintenance scheduling, work order management, asset management, work order management, preventive maintenance, inventory management, procurement, contract management, mobile asset management, spatial asset management, inventory control, procurement, and reporting capabilities.
3. Describe the architecture of Maximo.
Ans:
Maximo follows a three-tier architecture consisting of a client, application, and database tier. The components include:
- A client tier (browser-based interface for end-users).
- An application tier (Java EE-based application server hosting Maximo applications).
- A database tier (where the Maximo database resides, often supported by databases like Oracle or IBM Db2).
4. How does Maximo support asset management?
Ans:
Maximo supports asset management through features like asset tracking, condition monitoring, and maintenance planning. Organizations can efficiently manage their assets by tracking their location, maintenance history, and overall performance. The software enables proactive maintenance strategies, reducing downtime and extending the lifespan of assets.
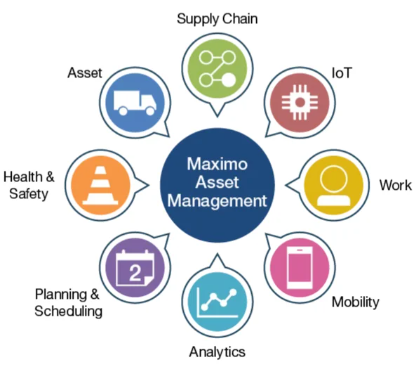
5. What are the main modules in Maximo?
Ans:
The main modules in Maximo cover various aspects of asset management, including:
- Asset Management
- Work Order Management
- Inventory Management
- Contract Management
- Procurement
- Service Request Management
6. What is the purpose of the Work Order module?
Ans:
The Work Order module in Maximo is designed to manage and track work orders related to asset maintenance and repair. It facilitates the planning, scheduling, and executing maintenance activities, ensuring that assets are well-maintained and operational. It includes features for creating work orders, assigning tasks, managing resources, and tracking the progress of maintenance work.
7. How does Maximo handle preventive maintenance?
Ans:
- Maximo supports preventive maintenance by allowing organizations to schedule routine maintenance tasks based on time, usage, or predefined conditions.
- This proactive approach helps prevent unplanned downtime, reduces equipment failures, and extends the life of assets.
- It automates the scheduling of routine maintenance tasks to prevent asset failures and optimize performance.
8. Explain the significance of the Asset module in Maximo.
Ans:
The Asset module in Maximo is significant as it serves as the core repository for all asset-related information. It includes details such as asset hierarchy, specifications, maintenance history, and location. This centralization of information enables organizations to make informed decisions regarding asset performance, maintenance, and lifecycle management. It tracks asset details, maintenance history, and condition monitoring and helps optimize asset performance and longevity.
9. What is the use of the Location module in Maximo?
Ans:
- Organizes physical locations of assets, such as buildings, floors, and rooms.
- Provides a hierarchical structure for efficient asset categorization.
- Enables spatial visualization of assets and their relationships.
10. How does Maximo integrate with GIS (Geographical Information System)?
Ans:
Maximo integrates with GIS by leveraging spatial data to enhance asset management. GIS integration allows users to visualize assets geographically, facilitating better decision-making. Maximo can link asset records to specific geographic locations, providing insights into asset distribution, condition, and maintenance requirements on a map.
11. How does Maximo help in managing inventory?
Ans:
- Tracks inventory levels and stock items.
- Allows creation, updating, and monitoring of stock items.
- Supports inventory transactions, including issues, transfers, and returns.
- Provides reporting and analysis tools for inventory optimization.
12. Explain the workflow management in Maximo.
Ans:
Maximo’s workflow management automates and streamlines business processes. It defines the flow of work orders, approvals, and tasks, ensuring a systematic progression through different stages. Workflow management in Maximo helps organizations enforce standardized processes, improve accountability, and reduce manual intervention, leading to increased efficiency in asset management and maintenance operations.
13. What is the purpose of the Labor module in Maximo?
Ans:
- Manages and tracks labor resources within the organization.
- Records labor hours and activities related to asset maintenance.
- Facilitates labor scheduling and allocation for work orders.
- Helps in assessing workforce availability and skills.
- Provides insights into labor utilization and efficiency.
14. What are the escalation and escalation points in Maximo?
Ans:
Escalation in Maximo refers to automatically triggering actions or notifications when predefined conditions are met. Escalation points are set at specific intervals in Maximo workflows to ensure timely response to issues. For instance, if a work order isn’t addressed within a specified timeframe, an escalation point can notify higher management, ensuring prompt resolution.
15. Explain the concept of Condition Monitoring in Maximo.
Ans:
- Monitors asset conditions in real-time.
- Uses sensors and data to predict potential failures.
- Enables proactive maintenance strategies to minimize downtime.
- Supports the identification of critical asset conditions.
16. What is the difference between Item Master and Asset in Maximo?
Ans:
Feature | Item Master | Asset | |
Purpose |
Manages inventory items and spare parts |
Manages physical assets and equipment | |
Type of Entity | Non-physical, consumable items | Physical, durable assets and equipment | |
Examples |
Spare parts, consumables, tools |
Machinery, vehicles, buildings | |
Lifecycle | Procurement to consumption or disposal | Acquisition to disposal, including maintenance |
17. How does Maximo handle service requests?
Ans:
- Captures and records user-initiated requests for services or maintenance.
- Centralizes the submission and tracking of service requests.
- Facilitates communication and workflow for service fulfillment.
- Helps prioritize and assign tasks based on service requests.
18. What is the purpose of the Job Plan in Maximo?
Ans:
A Job Plan in Maximo outlines a predefined set of tasks, materials, and labor required for maintenance activities. It serves as a template for work orders, streamlining the planning and execution of routine maintenance. Job Plans ensure consistency in maintenance procedures, improve resource allocation and contribute to efficient asset management.
19. What is the difference between a Service Request and a Work Order?
Ans:
- Service requests typically precede the creation of work orders.
- Work orders contain detailed instructions for executing specific tasks.
- Service requests are general, while work orders are specific and actionable.
- Work orders are often generated in response to approved service requests.
20. How does Maximo support contract management?
Ans:
Maximo facilitates contract management by allowing organizations to define and track various types of contracts, including service agreements and warranties. It helps manage contract details, monitor service levels, and track expiration dates. This feature ensures compliance, enhances vendor relationships, and contributes to cost-effective asset maintenance.
21. Explain the significance of the Purchasing module in Maximo.
Ans:
- Manages procurement processes and purchasing activities.
- Tracks purchase requisitions, purchase orders, and supplier information.
- Supports inventory replenishment and cost control.
- Facilitates efficient vendor management and communication.
22. What is Linear Asset Management in Maximo?
Ans:
Linear Asset Management in Maximo deals with managing assets with linear spatial characteristics, such as roads, pipelines, or railways. It allows organizations to manage these assets effectively, considering their spatial relationships, conditions, and maintenance requirements. Maximo’s Linear Asset Management supports the planning and execution of asset maintenance activities with linear configurations.
23. What is the role of the People application in Maximo?
Ans:
- Manages information about personnel within an organization.
- Tracks names, roles, contact information, and work schedules.
- Maintains records of skills, certifications, and qualifications of individuals.
- Facilitates workforce planning and resource allocation for tasks and projects.
24. Explain the role of the Maximo Integration Framework (MIF).
Ans:
The Maximo Integration Framework (MIF) facilitates the seamless integration of Maximo with other enterprise systems. MIF enables the exchange of data between Maximo and external applications, allowing for real-time updates, data synchronization, and automation of processes.
25. How can you customize Maximo applications?
Ans:
Maximo provides tools for customization to adapt the system to specific organizational needs. Users can customize Maximo applications by configuring fields, screens, and business rules. Additionally, the Application Designer allows the creation of new applications or modification of existing ones. Customization options ensure that Maximo aligns with an organization’s unique requirements, enhancing user experience and system functionality.
26. How does Maximo support mobile asset management?
Ans:
- Provides mobile access to Maximo functionalities through dedicated mobile apps.
- Allows field technicians to view and update asset information on the go.
- Enables the completion of work orders, inspections, and other tasks in the field.
- Improves overall asset management efficiency and responsiveness.
27. What is the Automation Scripting feature in Maximo?
Ans:
Automation Scripting in Maximo allows users to automate tasks, extend functionalities, and customize business logic using scripting languages such as Jython or JavaScript. Automation Scripting is used for various purposes, including validation, data manipulation, and integration, allowing organizations to tailor Maximo to their specific needs.
28. What is the purpose of the Graphical Assignment application in Maximo?
Ans:
- Visualizes and optimizes the assignment of work to resources on a map.
- Enhances decision-making for resource deployment and work scheduling.
- Improves overall efficiency in resource allocation and task assignment.
- Provides a graphical representation of work assignments for better visibility.
29. What is Maximo Scheduler, and how does it work?
Ans:
Maximo Scheduler is a module within IBM Maximo that focuses on optimizing and streamlining the scheduling of work orders and resources.
Visual Scheduling: Utilises Gantt charts to display work order schedules, helping users visualize and manage tasks over time.
Dynamic Scheduling: Allows dynamic adjustments to schedules based on real-time changes, such as resource availability or unexpected delays.
Resource Optimization: Provides tools to balance workloads, allocate resources efficiently, and ensure optimal utilization of workforce and equipment.
30. How does Maximo handle data migration and import/export?
Ans:
- Utilises Data Migration Manager for bulk data import into Maximo from external sources.
- Supports various data formats and allows mapping of fields to ensure accurate data transfer.
31. Explain the difference between a Service Group and a Crew in Maximo.
Ans:
Service Group:
- Represents a logical grouping of services or skills.
- Used in work order planning to define the required expertise or service category.
Crew:
- Represents a team or group of labor resources.
- Crews can be assigned to work orders for collective execution of activities.
32. How does Maximo handle linear referencing for linear assets?
Ans:
Maximo’s Linear Asset Management functionality supports the management of linear assets such as roads, pipelines, or railways. It allows organizations to represent linear assets accurately by defining linear reference systems and referencing specific locations along linear networks.
33. What is the purpose of Maximo’s KPI (Key Performance Indicator) module?
Ans:
Performance Monitoring: Allows organizations to define and track key performance indicators (KPIs) related to asset management and maintenance processes.
Real-time Metrics: Provides real-time insights into performance metrics, enabling organizations to monitor and assess their efficiency and effectiveness.
34. What is the Integration Composer in Maximo?
Ans:
The Integration Composer in Maximo is a powerful tool designed to simplify and streamline the integration of Maximo with external systems and applications. It provides a user-friendly interface for creating, configuring, and managing integration endpoints, allowing organizations to seamlessly connect Maximo with various third-party software, databases, or IoT devices.
35. How does Maximo handle calibration and test points?
Ans:
Maximo manages calibration and test points through its Calibration module. This functionality allows organizations to define asset calibration specifications, ensuring they adhere to required standards. Test points, representing specific measurement locations, can be associated with assets to monitor and record calibration readings.
36. How does Maximo handle safety plans and permits?
Ans:
Safety Plans:
- Allows the creation and management of safety plans associated with work orders.
- Ensures that safety procedures and precautions are documented.
Permits:
- Organizations can define permit types and templates based on safety requirements.
- These templates can include predefined safety measures, conditions, and approval workflows.
37. What is the Asset Configuration Manager in Maximo used for?
Ans:
The Asset Configuration Manager in Maximo is utilized for managing complex asset configurations. It allows organizations to define and maintain configurations of assets, including their components, attributes, and relationships. This feature is particularly useful for organizations with assets that have varying configurations or options.
38. How does Maximo handle the tracking of asset downtime?
Ans:
Downtime Records: Enables the creation of downtime records to capture and track periods when assets are not operational.
Downtime Causes: Associates downtime records with specific causes, such as maintenance, failures, or planned shutdowns.
Downtime Analysis: Facilitates asset performance analysis by tracking and reporting downtime occurrences.
39. How does Maximo support multi-language capabilities?
Ans:
- Provides a multilingual user interface to accommodate users from different language backgrounds.
- Allows users to interact with Maximo in their preferred language, enhancing user experience.
- Offers language packs that include translations for user interface elements and system messages.
40. What is the purpose of the Condition Codes in Maximo?
Ans:
Asset Status Classification: Condition Codes in Maximo represent an asset’s current state or condition. Helps classify assets based on their operational status, facilitating maintenance prioritization.
Maintenance Triggers: Allows organizations to define condition-based maintenance triggers.Enables timely interventions and preventive maintenance activities based on the condition of assets.
41. Explain the role of the Maximo Application Designer.
Ans:
- Allows users to customize and configure Maximo applications to align with specific business requirements.
- Enables the design and modification of user interfaces, including screens, tabs, and fields, to optimize user workflows.
- Allows customization of application behavior, business rules, and data validation to meet organizational needs.
42. What is the Maximo Health, Safety, and Environment (HSE) module?
Ans:
The Maximo HSE module focuses on health, safety, and environmental management within the asset management framework. Incident Management supports the recording, tracking, and analysis of health and safety incidents—aids in identifying root causes and implementing corrective actions to prevent reoccurrence.
43. Explain the role of the Failure Codes in Maximo.
Ans:
Failure Codes in Maximo are crucial in tracking and analyzing the reasons behind asset failures. They allow organizations to categorize and code different failures or issues that assets may experience. When work orders are generated due to asset failures, Failure Codes help document the root causes, facilitate thorough analysis, and enable preventive measures.
44. How does Maximo handle asset hierarchy and classification?
Ans:
Asset Hierarchy: Supports the creation of hierarchical relationships between assets.Allows organizations to represent complex asset structures, such as parent-child relationships.
Classification: Enables the classification of assets based on various criteria such as type, function, or location.Enhances organization and search capabilities within the asset management system.
Work Order Planning: Utilises asset hierarchy and classification for efficient work order planning, ensuring that maintenance activities are organized and prioritized appropriately.
45. How does Maximo handle service level agreements (SLAs)?
Ans:
Maximo facilitates the management of service level agreements (SLAs) to ensure that maintenance and service activities meet predefined performance standards. Organizations can define SLAs with specific response and resolution times for work orders. Maximo automatically monitors and tracks adherence to these SLAs, providing real-time visibility into performance metrics.
46. What is the Escalation Point in Maximo used for?
Ans:
- Defines a specific point in a workflow where an action or notification should occur if certain conditions are met.
- Commonly used to escalate overdue work orders or critical issues to higher management.
47. What is the purpose of the Graphical Work Week in Maximo?
Ans:
The Graphical Work Week in Maximo visually represents the work schedule for resources over a week. It allows users to view and manage resource assignments, work orders, and downtime in a graphical format, making it easier to optimize resource utilization. Users can drag and drop work orders within the graphical view, adjust schedules, and identify potential conflicts.
48. What are the Difference between Hard Reservations and Soft Reservations in Maximo?
Ans:
Hard Reservations: Explicitly reserved resources for a specific date and time. Firm commitments and the system prevent other users from scheduling conflicting activities.
Soft Reservations: Tentative or conditional reservations that do not block the availability of resources. It allows flexibility as the reservation is not binding, and other users can schedule conflicting activities.
49. How does Maximo handle energy management?
Ans:
- Maximo addresses energy management by providing tools to monitor, analyze, and optimize energy consumption.
- The Energy Optimization module allows organizations to track energy usage for assets, identify inefficiencies, and implement strategies for energy conservation.
50. Explain the role of the Locations and Assets application in Maximo.
Ans:
The Locations and Assets application in Maximo is a central hub for managing information about physical locations and associated assets within an organization. Users can define and organize locations hierarchically, providing a structured representation of their facilities. The Assets application allows for creating and managing asset records, including details about equipment, machinery, or other physical items.
51. How does Maximo handle tool tracking?
Ans:
Maximo offers robust tool tracking capabilities to ensure the efficient management of tools throughout their lifecycle. Users can associate tools with specific job plans, work orders, or locations, providing visibility into tool availability and usage. The system allows the recording of tool issues, returns, and transfers, enhancing accountability and minimizing tool losses.
52. What is the Multi-Site feature in Maximo?
Ans:
- Enables organizations to manage assets and operations across multiple physical locations or sites.
- Supports the segregation of data and workflows based on different sites.
- Administrators can have a global view of all sites within a single Maximo instance, simplifying system administration and maintenance.
53. What is the purpose of the Maximo Cron Task?
Ans:
The Maximo Cron Task is vital for managing scheduled tasks and background processes within the Maximo system. It allows administrators to define, schedule, and automate routine activities, ensuring the efficient execution of critical system processes. By automating these tasks, the Cron Task enhances system efficiency, optimizes resource utilization, and supports a proactive approach to system maintenance.
54. How does Maximo handle condition-based maintenance?
Ans:
- Maximo excels in handling condition-based maintenance by incorporating advanced condition-monitoring features.
- Users can define condition monitoring parameters and set thresholds based on real-time asset health data.
55. Explain the role of the Maximo System Configuration application.
Ans:
The Maximo System Configuration application allows administrators to configure and customize various system settings within the Maximo environment. It provides a centralized interface for tailoring Maximo to meet specific organizational requirements, ensuring the system aligns seamlessly with business processes. Administrators can define and modify system behaviors, user interface elements, and overall system preferences through the System Configuration application.
56. What is the significance of Maximo Anywhere?
Ans:
Maximo Anywhere is a mobile solution that extends Maximo’s capabilities to field technicians and remote users. It allows access to Maximo functionalities on various mobile devices, providing real-time information about work orders, assets, and inventory. Field personnel can perform tasks, capture data, and update records while working offline, synchronizing when connectivity is restored.
57. How does Maximo handle rotating assets and equipment?
Ans:
- Maximo supports the management of rotating assets that are periodically exchanged or replaced.
- Utilises asset templates and serial numbers to track rotating components.
- Enables seamless asset history, maintenance, and performance tracking across rotations.
58. Explain the role of the Maximo Anywhere Administration application.
Ans:
Maximo Anywhere Administration application facilitates the configuration and administration of Maximo Anywhere, the mobile solution for field technicians. It allows administrators to define security settings, configure mobile applications, and manage synchronization parameters. Ensures seamless integration and efficient deployment of Maximo functionality in a mobile environment.
59. What is the purpose of the Condition Monitoring Workbench in Maximo?
Ans:
- Allows users to centralize and analyze condition monitoring data for assets.
- Provides a comprehensive view of asset conditions, health, and performance.
- Supports proactive maintenance by identifying trends, triggering alerts, and facilitating data-driven decision-making.
60. How does Maximo handle service contracts and warranties?
Ans:
Service Contracts: Allows organizations to define service agreements with external vendors or service providers. Tracks contract details, service levels, and associated costs.
Warranties: Manages warranties associated with assets. Tracks warranty terms, expiration dates, and entitlements.
61. Explain the role of the Maximo Application Server (MAS).
Ans:
- Serves as the core component of Maximo’s three-tier architecture.
- Hosts Maximo applications and business logic and facilitates client and database communication.
- Manages user sessions and security and ensures data integrity.
- Enables scalability and performance optimization in large-scale implementations.
62. How does Maximo handle inventory reservations?
Ans:
Maximo efficiently manages inventory reservations, providing organizations with a systematic approach to allocating and tracking materials for planned activities. Users can create reservations associated with work orders, purchase orders, or other business processes, indicating the need for specific items.
63. What is the Relationship module in Maximo used for?
Ans:
Maximo’s Relationship module is crucial for establishing connections and associations between various records within the system. It lets users define and manage relationships between assets, locations, and entities. The module enhances data connectivity by allowing users to link related records, providing a holistic view of the interdependencies within the organization.
64. What is the purpose of the Change Status action in Maximo?
Ans:
- Allows users to transition records, such as work orders or assets, from one status to another.
- Common statuses include “Draft,” “Approved,” “In Progress,” and “Complete.”
- Facilitates tracking the records lifecycle and triggers associated actions or workflows.
65. How does Maximo handle the disposal of assets?
Ans:
Maximo provides robust functionality to manage the disposal of assets effectively. When an asset reaches the end of its lifecycle, users can initiate the disposal process by creating disposal records. Asset disposal records contribute to accurate reporting and auditing practices, allowing organizations to track the entire lifecycle of assets from acquisition to disposal.
66. How does Maximo support the management of transportation assets?
Ans:
- Supports the management of vehicles, fleets, and transportation infrastructure.
- Allows tracking of maintenance schedules, fuel consumption, and overall asset performance.
- Enhances efficiency in transportation operations by optimizing maintenance and resource allocation.
67. What is the difference between rotating and non-rotating assets in Maximo?
Ans:
Maximo distinguishes between rotating and non-rotating assets based on usage patterns and maintenance requirements. Rotating assets undergo periodic replacement or rotation, often with components with limited lifespans. Maximo manages rotating assets using asset templates and serial numbers, allowing for tracking historical records across rotations. These assets are managed as standalone entities without the complexities associated with rotation.
68. What is the role of the Maximo Cron Task Setup application?
Ans:
The Maximo Cron Task Setup application is a dedicated platform for configuring and managing cron tasks within the Maximo system. Cron tasks are automated background processes that execute predefined actions at specified intervals. The Cron Task Setup application enables administrators to define, schedule, and customize these tasks based on organizational needs.
69. What is the purpose of the Maximo Integration Framework (MIF) object structures?
Ans:
Data Integration Framework: Object Structures in MIF define the structure and format of data exchanged between Maximo and external systems.
Data Mapping: Allows organizations to map data elements between Maximo and external applications for accurate data transfer.
Standardised Interfaces: Provides standardized interfaces for inbound and outbound data exchanges, ensuring consistency in integration processes.
70. Explain the role of the Maximo Job Plan Templates.
Ans:
Maximo Job Plan Templates are crucial in standardizing and implementing organizational maintenance processes. Organizations serve as predefined sets of tasks, instructions, and specifications that can be reused across multiple job plans. By creating and utilizing templates, organizations ensure consistency in maintenance procedures, enhance efficiency, and reduce the effort required to plan and schedule recurring tasks.
71. How does Maximo handle the creation of service requests through email?
Ans:
Maximo can be configured with an Email Listener to monitor a specified email inbox. The Email Listener scans incoming emails and identifies those configured to create service requests. Utilizes mapping rules to extract relevant information from email content, such as requester, description, and priority.
72. What is the Escalation Application in Maximo used for?
Ans:
Escalation Points Configuration: Allows administrators to define escalation points in various Maximo applications.
Trigger Conditions: Specifies conditions for escalations, such as overdue work orders or unattended service requests.
Escalation Actions: Defines actions to be taken, such as sending notifications, changing record status, or initiating additional workflows.
73. How does Maximo handle asset meter groupings?
Ans:
Maximo efficiently manages asset meter groupings to facilitate the structured tracking of meter readings and measurements. Asset meters, representing various aspects such as usage, performance, or condition, can be grouped logically based on organizational needs. Maximo allows users to define meter groups, associating meters with common characteristics or measuring similar parameters.
74. How does Maximo handle the generation of purchase orders?
Ans:
Requisition Creation: Users initiate the purchase process by creating requisitions in Maximo, specifying required items and quantities.
Requisition Approval Workflow: Utilises workflow approval processes to route requisitions for approval from designated authorities.
75. What is the purpose of the Maximo Application Import/Export feature?
Ans:
The Maximo Application Import/Export feature facilitates the seamless transfer of application-related data between Maximo instances. This feature is instrumental in scenarios where organizations must migrate configuration settings, records, or entire applications from one Maximo environment to another. This functionality is particularly valuable for organizations managing multiple Maximo instances or implementing changes across different environments.
76. Explain the significance of the Maximo Scripting languages.
Ans:
Maximo Scripting languages, including Automation Scripting and Scripting Languages for Business Rules, allow users to automate and customize various aspects of Maximo. Business Logic Customization significantly impacts business logic by enabling users to define custom actions, validations, and processes. Data Manipulation facilitates data manipulation, transformation, and validation during record creation, modification, or deletion.
77. What is the purpose of the MIF processing rules?
Ans:
Data Transformation: MIF Processing Rules define how data is transformed during inbound and outbound integration processes.
Data Validation: Enforces data validation rules to ensure the integrity and accuracy of information exchanged.
Error Handling: Manages error handling and exception scenarios during data integration.
78. How does Maximo handle asset warranty tracking?
Ans:
Maximo provides robust capabilities for tracking asset warranties, ensuring organizations can effectively manage warranty information throughout an asset’s life cycle. Users can associate warranty details, such as warranty start and end dates, with individual assets in Maximo. The system facilitates tracking warranty terms, entitlements, and expiration dates.
79. How does Maximo handle the tracking of labor costs?
Ans:
Labor Reporting: Employees report labor hours directly in Maximo against specific work orders or tasks.
Rate and Cost Calculations: Applies predefined labor rates to calculate labor costs based on reported hours.
Integration with Payroll Systems: Supports integration with payroll systems to streamline labor cost reconciliation.
Real-time Visibility: Provides real-time visibility into labor costs associated with maintenance activities.
80. How does Maximo handle asset warranty tracking?
Ans:
Maximo provides robust capabilities for tracking asset warranties, ensuring organizations can effectively manage warranty information throughout an asset’s life cycle. Users can associate warranty details, such as warranty start and end dates, with individual assets in Maximo. The system facilitates tracking warranty terms, entitlements, and expiration dates.
81. What is the significance of the Maximo Security Groups?
Ans:
Access Control: Security Groups in Maximo enable access control by defining the permissions and privileges granted to users or user roles.
Data Restriction: Allows organizations to restrict access to specific data sets based on user roles and responsibilities.
System Administration: Facilitates system administration by allowing administrators to assign security groups to users.
82. Explain the purpose of the Maximo Asset Topology Viewer.
Ans:
The Asset Topology Viewer visually represents asset relationships and hierarchies within Maximo. It allows users to explore and navigate the hierarchical structure of assets, including parent-child relationships. Maximo Asset Topology Viewer supports impact analysis by displaying the relationships between assets, helping users assess the potential impact of changes.
83. How does Maximo handle the management of tools and equipment?
Ans:
Tool and Equipment Records allows users to create records for tools and equipment, capturing details such as type, location, and maintenance history. Tool Tracking supports tool tracking by associating tools with specific work orders, job plans, or inventory locations. Maintenance Scheduling integrates with maintenance processes to schedule and track the servicing of tools and equipment.
84. What is the significance of the Maximo Work Centers?
Ans:
Maximo Work Centers hold significant importance as they provide an intuitive and role-based interface for users to efficiently manage their work and tasks. Work Centers in Maximo offer a personalized workspace where users can access relevant information, perform actions, and collaborate with team members based on their specific roles and responsibilities.
85. Explain the role of the Maximo Cron Task Instances application.
Ans:
- The Maximo Cron Task Instances application is pivotal in managing and monitoring scheduled tasks and processes within the Maximo system.
- Administrators utilize this application to view and manage instances of cron tasks, which are automated background processes executed at specified intervals.
86. How does Maximo handle the tracking of safety incidents?
Ans:
Maximo provides comprehensive tools for tracking safety incidents, contributing to robust safety management practices within organizations. Users can record details of safety incidents, including incident types, locations, and involved individuals. The system supports the documentation of incident descriptions, root causes, and corrective actions taken.
87. What is the purpose of the Maximo Security Profiles?
Ans:
- Maximo Security Profiles serve the essential purpose of defining access controls and permissions for user roles within the Maximo system.
- These profiles allow administrators to tailor the level of access users or user groups have to specific applications, actions, or data sets.
88. How does Maximo integrate enterprise resource planning systems?
Ans:
Maximo integrates with enterprise resource planning (ERP) systems to provide a unified platform for managing assets, maintenance, and related processes. Maximo can exchange data with ERP systems through well-defined integration interfaces, ensuring consistency and accuracy in information across the organization.
89. What is the significance of the Maximo Multi-language Support feature?
Ans:
The Maximo Multi-language Support feature is important for organizations operating in diverse linguistic environments. It allows users to interact with Maximo in their preferred language, enhancing user adoption and ensuring effective organizational communication. This feature supports multiple languages, customizing user interfaces, field labels, and system messages to align with language preferences.
90. What is the significance of the Maximo Data Load application?
Ans:
Bulk Data Import: Facilitates the bulk import of data into Maximo, streamlining the data loading process.
Data Migration: Supports data migration initiatives by allowing organizations to import large datasets efficiently.
Template-Based Approach: Utilises template-based data loading to ensure consistency and accuracy in data format.