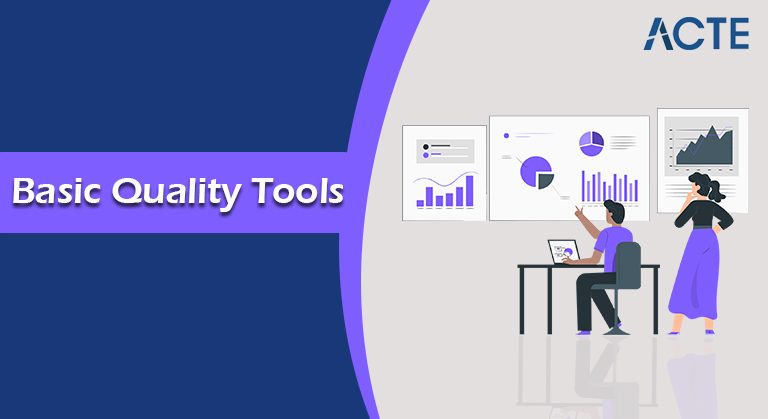
- Introduction to Basic quality tools
- Where did the quality devices start?
- Histogram
- Pareto Chart
- Root Cause Analysis
- Check Sheet
- Control Chart
- Scatter Diagram
- Flow Charts
- When would it be advisable for you to utilize Basic Quality Tools?
- Advantages of Basic Quality Tools
- Conclusion
- The seven quality devices were initially evolved by Japanese educator of designing Kaoru Ishikawa. They were executed by Japan’s modern preparation program during the country’s post bellum period as it went to factual quality control for the purpose of value confirmation. Their objective was to execute fundamental, easy to use tools that laborers from different foundations with shifted ranges of abilities could carry out without broad preparation.
- Today, these quality administration tools are as yet thought to be the highest quality level for investigating an assortment of value issues. They’re as often as possible executed related to the present most broadly utilized interaction improvement philosophies, including different periods of Six Sigma, TQM, consistent improvement cycles, and Lean administration.
- A histogram graph shows the recurrence dispersion. It shows the set of experiences or patterns of a variable.
- The variable can abscond, guarantees, scraps, revamps, reaction time, and so forth Deviation in a variable, for example, practicality and precision can be addressed graphically utilizing a histogram.
- The varieties are likewise called perception or recurrence, which is plotted on the upward pivot, while the boundary is on the even hub. For instance, rough examining requires long periods of planning, however, to see the conveyance, you can involve chronicled information as a histogram.
- Drawing Histograms is simple. Partition the whole reach into equivalent spans (canisters). The recurrence of the container is plotted on the upward hub and the span on the level.
- It gives a speedy perspective on variety inside an interaction.
- It furnishes boundaries with the most noteworthy recurrence and greatest likelihood.
- Assists with getting sorted out huge informational collections into a diagram.
- It is a decent show device.
- It’s very simple to draw.
- It very well may be utilized to make a show to partners.
- It improves speedy independent direction.
- It recognizes the degree of deviation.
- It shows the positioning of the reason for the deformity.
- It is hard to analyze two datasets.
- It must be utilized for consistent, not discrete information.
- Presently, let us move to the second device of seven essential quality devices.
- A Pareto diagram is a histogram that arranges the perception and distinguishes the “imperative few.” The word fundamental few becomes important as they maximumly affect the arrangement.
- All ventures have issues, and an undertaking director can’t invest energy in tackling that multitude of issues. Henceforth, you should focus on the fundamental few causes that are influencing your task most.
- In the wake of focusing on issues, you can see that tackling 20% of Root Causes takes out 80% of issues. This peculiarity is known as the Pareto rule.
- A Pareto diagram is a vital device in quality administration and Six Sigma. It is an upward reference diagram that shows issues or valuable open doors in a focus on hand. The classes from the left of the diagram incorporate fundamentally unrelated things organized in diminishing requests.
- The Pareto outline assists you with isolating the issues, and afterward, you can observe their Root Causes. You can put your work into those causes and take care of the majority of the issues.
- To draw the Pareto graph, you gather the issues in your interaction, order them by their sort, and draw a bar outline for each classification. The most often happening issues will be on the left and the most un-on the right side.
- We will take a contextual investigation of shuttle production for drawing a Pareto diagram. Accepting administrative guidelines have been kept, we will concentrate on abandons in a printed circuit leading group of the rocket.
- It assists you with zeroing in on tackling a couple of causes creating the most issues.
- It assists you with envisioning issues.
- It is an astounding visual specialized instrument.
- Pareto Chart Pros
- Ideal for focusing on discrete information.
- Very simple to draw.
- Improves fast independent direction.
- Helps center consideration around basic issues.
- It doesn’t show the Root Cause of an issue.
- The Pareto rule is a guideline and doesn’t make a difference to all circumstances.
- It shows the recurrence, not the seriousness.
- Peruse Pareto Chart exhaustively.
- It is consistently a meeting to generate new ideas where thoughts are presented in the chart until for all intents and purposes everything adding to the interaction is sorted out. The following inquiry then, at that point, is, what could turn out badly with this branch/part addressed by a bone-bolt? How can be treated development? Would it be able to be supplanted with a superior methodology? It is a thought-creating process, and all thoughts are supported, as apparently ‘insane’ thoughts might be the cardinal ones to assist with rescuing a cycle. Such a thought customarily may have been neglected.
- There can be a few regions as more thoughts keep on Flowing. It is the facilitator’s obligation not to pass judgment but rather first compose the branch addressing the thought.
- To work with a fish-bone graph meeting to generate new ideas, you ought to have delicate abilities which help in receptiveness, a craving to get reality, work on your relationship with others, and a capacity to acknowledge various thoughts, and so on.
- As these inquiries are created, you should dispassionately examine them and check for areas of shortcomings. Root Cause examinations mean you need to take care of the issue right from the very root. On the off chance that one branch isn’t adequate, you can go for additional regions.
- Imaginative reasoning and thoughts are associated with its turn of events
- Valuable for both forward (quality preparation) and in reverse (quality control) studies
- The most valuable apparatus for distinguishing the reason for an issue
- Opens an open door for the development
- It can become counterproductive on the off chance that not all around composed or worked with
- It just resolves one issue for each time; consequently, you might require a few meetings to generate new ideas for a very long time
- Peruse Root Cause Analysis exhaustively.
- Presently we will move onto the fourth of the seven essential quality apparatuses.
- Assists with getting sorted out the information gathering
- The result can be utilized for a Pareto graph or a histogram
- Works with the translation of information
- Can spike more thoughts
- Doesn’t discover the Root Cause of a distinguished imperfection.
- Relies upon the Pareto diagram or histogram for the information shown.
- The undertaking chief put forth control lines. Like control limits, particular cutoff points are likewise of two kinds: upper and lower determination limits. The client characterizes determination limits.
- At the point when the variable is passed as far as possible in one or the other heading, you can say that the item is deficient and should track down the deformity’s goal.
- Control limits are stricter all the time than the client’s determination limits. Henceforth you can say that determination limits are dependably outside UCL and LCL.
- Upper and lower control limits depend on standard measurable computations used to layout the innate capacity of a cycle. The quality group needs to set the reach between the upper and lower control limits. Generally, the cutoff is set to +/ – 3? (3-sigma) quality norm.
- 1 Sigma = 68.26%
- 2 Sigma = 95.46%
- 3 Sigma = 99.73%
- 6 Sigma = 99.99%
- A reason can be an extraordinary reason or a typical reason. An exceptional reason is a typical event and requires examination, though a typical reason is the ordinary change and is probably going to be inside as far as possible.
- A standard of seven is an illustration of a unique reason.
- Helpful for observing a cycle
- Can show the ongoing conduct of an interaction
- Saves the expense of adjusting and framework disappointment
- It tends to be customized and computerized
- Assists with meeting client determinations
- Doesn’t show the root cause(s) of a deviation
- Requires a degree of specialized skill for use
- Propensity to confuse normal reason with an exceptional reason as well as the other way around
- Peruse more on Control Charts.
- The free factor is plotted on the x-hub, while the reliant variable is on the y-pivot.
- The line displayed in the above picture is known as the line of best fit. The line is drawn with the goal that most information focuses swarm around it.
- It assists with laying out the connection between factors
- Can help in input versus yield reproductions
- Helpful for the circumstances and logical results study
- Requires precise and satisfactory information
- Presently we come to the remainder of the seven essential quality devices.
- Flow Charts show the different strides to assist quality supervisors with tracking down bottlenecks and further develop the interaction Flow execution.
- The shapes used to draw Flow diagrams are as per the following:
- An ordinary Flow graph for getting PMP accreditation is displayed underneath.
- When the Flow outline is finished, you can survey it to distinguish regions for development. This is the place where de-bottlenecking comes in. Standard Operating methods most times require a Flow outline to empower administrators to comprehend the interaction Flow.
- It is relevant in PC programming and troubleshooting of mistakes in a program.
- Can help in process enhancements
- Helpful for de-bottlenecking a cycle
- Helpful during a quality review
- Helps in critical thinking
- It can help find and in this way forestall an expected issue
- It very well may be utilized to concentrate on the worth chain of a whole cycle, e.g., SIPOC(Supplier, Input, Process, Output, Consumer) study
- Pictorial and successful for show
- It doesn’t uncover basic Root Causes
- It should be refreshed after processing survey
- Gives a more organized way to critical thinking and quality improvement
- Straightforward as well as execute yet incredibly successful
- A logical and coherent methodology for critical thinking
- Follows the 80/20 rule for example acquire 80% outcome with 20% endeavors
- Work on the nature of item and administrations
- Helps in distinguishing and examining issues during the interaction
- Fishbone preparing associates in Root Cause investigation and critical thinking
- Empowers solidarity and cultivates a sound culture
- Recognizes roots cause and settle it for all time
- Upgrade client experience and consumer loyalty
- In light of the information-driven cycle and client-driven methodology, Basic Quality devices execution is one of the best cycles that too in the briefest measure of time.
- Over seven fundamental quality apparatuses assist you with tending to various worries in an association.
- Accordingly, utilization of such tools should be an essential practice in the association to improve its effectiveness.
- Preparation stages on these apparatuses ought to be remembered for the authoritative direction program, so all the staff individuals get to get familiar with these essential tools.
- This study recognized that is exceptionally fundamental to apply each of the seven QC devices for investigating issues inside creation processes in the associations.
- Without a doubt, all of the previously mentioned quality apparatuses ought to be thought of and involved by the executives for distinguishing and taking care of value issues during creating the items and administrations.
Introduction to Basic quality tools
The capacity to recognize and resolve quality-related issues rapidly and productively is crucial for anybody working in quality affirmation or worried about process improvement. With the seven essential devices of value in your munititions stockpile, you can without much of a stretch deal with the nature of your item or interaction, regardless industry you serve. Find out with regards to these quality administration tools and track down formats to begin utilizing them rapidly.
Where did the quality devices start?
#1. Histogram:
Employments of a Histogram
Histogram Pros
Histogram Cons
#2. Pareto Chart:
Pareto diagram for the dispersion is displayed beneath:
Advantages of a Pareto Chart
Pareto Chart Cons
#3. Root Cause Analysis:
This is additionally called the Ishikawa chart, named after the Japanese Organizational Theorist, Kaoru Ishikawa. It is a visual device used to conceptualize the possible reasons for an issue. An Root Cause investigation chart is displayed underneath:
In the assembling business, the causes are characterized into the 5m’s: Man, Material, Machine, Method, and Measurement.
Man: Are the staff prepared, are they roused, are they talented, experienced, intermittently evaluated/tried, is the preparation satisfactory, is it fit for reason or only recreation in work out, who works with the preparation, what is the history of the facilitator, and so forth.
Material: Are the information materials in great condition, would they be able to be promptly obtained, what is the grade of material, are preparing units and working tools accessible, and so on.
Machine: What sort of machine are we utilizing, is it dependable, do we have in-house fixing or do we want to re-appropriate it, how great is its exhibition, and so forth.
Technique: Is it a standard strategy or optional?
Estimation: Is the instrument adjusted, touchy, exact? Is the result approximated? What is the resistance blunder? What about recording? Is it appropriately finished?
Root Cause Analysis Pros
Root Cause Analysis Cons
#4. Check Sheet:
A check sheet is otherwise called an agenda. This is an information assortment sheet that works with information translation. Since it catches quantitative information as trait information, it is otherwise called a count sheet. The distinctions between quality information and variable information are:
The Check Sheet works with the information assortment for additional investigation. Consider the table beneath showing a review of a creation line of a packaging organization. The number of recurrence of each deformity is addressed in the count of slices.
Actually, look at Sheet Pros
Actually, look at Sheet Cons
#5. Control Chart:
A control diagram is a graphical instrument that assists you with seeing whether the interaction is in charge. Changes happen in each interaction, however, it turns into a reason for concern when they cross the put down certain boundaries and the cycle is crazy. A control outline has two cutoff points: control cutoff points and detail limits. Control limits are of two kinds:
Upper control limit (UCL): This is as far as possible, and when the variable crosses it, you will start an examination.
Lower control limit (LCL): This is the base point, and when the variable crosses it, you will start an examination.
Note that
A sigma addresses the quality norm. 6-sigma is the best norm and has been taken on by organizations like Motorola, Bank of America, General Electric, Airlines, JP Morgan Chase., to decrease squander and further develop consumer loyalty and productivity.
The Rule of Seven: When seven information focuses are seen on one side of the mean, there is cause for an examination, as the interaction might be crazy. This is displayed in the control diagram beneath.
Control Chart Pros
Control Chart Cons
#6. Scatter Diagram:
A Scatter Diagram shows you the connection between two factors. The main variable is free, while the other is the reliant variable. A Scatter outline assists you with concentrating on the connection between’s two factors. For instance, assume the number of blunders in an item cluster could be connected with the number of long periods of extra time by faculty. All things considered, the quantity of mistakes is the reliant variable, while the extra time hour is the autonomous variable.
Scatter Diagram Pros
Disperse Diagram Cons
#7. Flow Charts:
Flow Chart Pros
Flow Chart Cons
When would it be advisable for you to utilize Basic Quality Tools?
Basic Quality tools can be done during the quality administration, quality improvement process, six sigma execution processes or even the standard PDCA cycle for the quality reason for upgraded quality administration. In the primary period of estimating and recognizing, Fishbone Diagram otherwise called circumstances and logical results outline, Pareto Chart and Control Chart can be used. In the following periods of evaluation and examination, Scatter Diagram, Histogram and Checklist can be done. The Control Chart can be used reliable quality improvement.
Advantages of Basic Quality Tools:
The Basic Quality apparatuses are organized and crucial tools that assist organizations with working on their administration and creation process for accomplishing upgraded item quality. From evaluating and looking at the creation interaction, distinguishing proof of key difficulties and issues to controlling the change present in the item quality and giving answers for counteraction of imperfections in future, the straightforward and execute, Basic Quality tools are extremely successful. A portion of the significant business advantages of Basic Quality tools are recorded underneath.
4C group of confirmed experts has given 80+ execution of Basic Quality Tools and 120+ Basic Quality Tools Training. By taking care of 200+ quality issues, 4C has enabled clients to lessen the 80% expense of low quality. To speed up your quality administration process and lessen your expense of low quality, contact our specialists now.