
SAP ERP (Enterprise Resource Planning) is a commercial software that integrates all the information in a single software, considering various factors such as time and cost. Organizations can easily meet their business demands with the help of SAP.
1. What is SAP MM?
Ans:
SAP stands for Systems, Applications & Products in a Data Processing. SAP MM is the functional module in SAP that deals with the procurement handling and material management. In SAP MM, MM stands for a Material Management. The SAP MM module contains a master data, material valuation, invoice verification, material requirement planning, system configuration, transactions, etc., to complete procurement to pay process.
2. Which master files are most frequently used in SAP MM?
Ans:
- Material master file
- Inventory master file
- Vendor master file
3. What does goods receipt and post goods receipt?
Ans:
Goods Receipt: Goods receipt is a physical inbound transfer for goods or material into warehouse. It specifies a transfer of goods used to post goods received from an external vendors or in-plant production. All goods receipts result in increase in stock in warehouse.
Post-Goods Receipt: The Post Goods Receipt specifies a reference to the purchase order with which goods were ordered. It is used to post receipt of goods with reference orders after the purchase. If the material is delivered for a some purchase order, it is important for all the departments involved that goods receipt entry in system references this purchase order.
4. What does necessary components of SAP MM or SAP Material Management?
Ans:
- Vendor Selection
- Source determination
- Invoice Verification
- Order Processing
- Order follow up
- Determine requirements
- Goods receipts and Inventory management
5. Explain Consignment Stock? ?
Ans:
The Consignment Stocks are used to specify materials that are still available in store premises but belong to owner or seller. When buyer uses the consignment stocks, has to pay for them.
6. What does advantages of SAP MM or SAP Material Management?
Ans:
- SAP MM reduces the material costs by avoiding a stocking unnecessary or obsolete materials.
- In SAP MM, inventory losses are minimized because it provides the multi-location inventory.
7. Which type of document is purchase requisition, internal, or external document?
Ans:
A purchase requisition is internal document, and it is phase in which purchasing department is informed about requirement of items or services required for a business purposes.
8. What does different types of stocks used in SAP MM?
Ans:
- Valuated Stock
- Non-valuated stock
- Special Stock
- Unrestricted stock
- Blocked stock
- Quality Inspection Stock>
9. What does different info record types in SAP MM?
Ans:
- Standard
- Pipeline
- Subcontracting
- Consignment
The different info record types in the SAP MM are:
10. Define Internal procurement?
Ans:
The big corporate organizations own the multiple separate businesses or companies. Here, internal procurement is the process of getting material and services from identical companies. Therefore, each of these businesses maintains a full bookkeeping system with independent Balance, Profit & Loss Statements in order to document any transactions that take place between them.
11. What does different types of special stocks available in SAP MM?
Ans:
- Subcontracting
- Consignment
- Project
- Pipeline
- Sales order
- Stock transfer
- Returnable packaging with a customer
12. What does Special Procurement in SAP MM?
Ans:
In SAP MM, Special Procurement is used to specify the stocks that do not belong to the company, and these are kept at a different locations.
13. What does common assignment types in the SAP Material Management system?
Ans:
- Purchasing the organization to company code
- A Standard purchasing organization to plant
- Plant to Company code
- Purchasing an organization to Plant
14. What does importance of batch record in SAP MM?
Ans:
In SAP MM, the term “batch” is used to define the quantity of a certain product that is concurrently processed or created under the same conditions. The materials produced in batches have same values and characteristics. On other hand, the batch record is used to give the information about a particular batch product and is mainly used in knowing whether a product has gone through the GMP (Good Manufacturing Process).
15. What does important fields in purchasing view in SAP MM?
Ans:
- The base unit of measure
- Order unit
- Purchasing group
- Material group
- Valid from
- Tax indicator for the material
The most important fields in purchasing view in SAP MM are:
16. Explain Purchase Order?
Ans:
A Purchase Order is the type of confirmation list that buyer sends to his sender to confirm requirements finally. The Purchase Order not only includes the names and quantity of materials, but it also has a valuable information like details of purchasing company with the company code, name of material along with the corresponding Plant, and date for a delivery of material.
17. How can link the document to the vendor master record?
Ans:
You can link a document to vendor master record by using XK01 transaction code or by using the following menu path:
SAP Menu > Logistics > Material Management > Purchasing > Master Data > Vendor > Central > XK01- Create.
18. What type of data mainly information record contains?
Ans:
The information record mainly contains a data related to the units of measurement, like the products, vendor price, materials used by specific vendors, etc. It also contains the information on the tolerance limit of under-delivery of data, planned delivery time, vendor evaluation data, availability status for a goods, etc.
19. What does integral components in SAP MM?
Ans:
- MM – CBP (Consumption-Based Planning)
- MM – PUR (Purchasing)
- MM – SRV (External Services Management)
- MM – IV (Inventory Management)
- MM – IV (Logistics Invoice Verification)
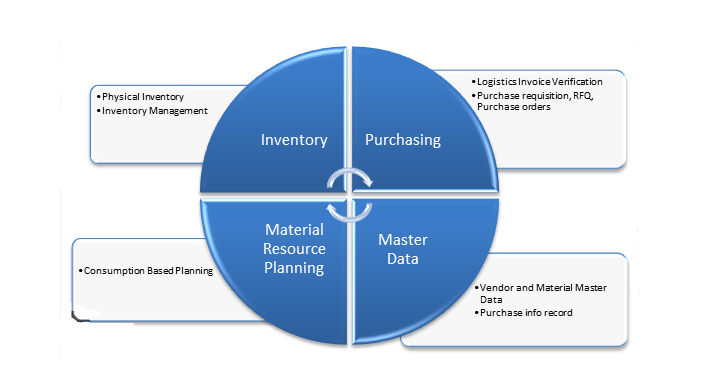
20. Which Transaction Code is used to display and reset the release of purchase order?
Ans:
You can release a purchase order at header level. It is not possible to release single item in purchase order, and and have to release all the items at a time. The ME29N Transaction Code is used to display and reset a release of a purchase order.
21. How does MM calculate prices?
Ans:
Establishing a costs that are specified in order paperwork may be done with the help of the Pricing method that is contained inside a MM module. As a result of this, now have the capacity to explain particular kinds of computations that are suitable for application in the wide variety of settings. A pricing procedure is utilized by MM whenever a company is writing up a purchase order or request for a quotation. The total value of material is calculated by taking into the account a variety of costs and expenses, like surcharges, discounts, taxes, and freight.
22. What does pre-requisites for creating purchasing info record in SAP MM?
Ans:
- Material Number
- MPN ( Manufacturer Part Number )
- Vendor Number
- Organizational level code
Following is list of pre-requisites used for creating purchasing info record in SAP MM:
23. How can flag a material for deletion in SAP MM?
Ans:
You can set a deletion flag at client level, plant level, or storage location level. The Transaction Code MM06 is used to mark material for the deletion.
24. What does full form of ERS in the context of SAP MM?
Ans:
ERS stands for an Evaluated Receipts Settlement. It refers to process of settling down receipts of goods automatically. In the ERS process, an agreement between vendor and the user that vendors do not prepare an invoice for goods ordered. Rather, system would automatically generate and post the invoice document based on purchase order and goods receipts.
25. What does Source List? What does transaction code used for creating a Source List?
Ans:
The Source List is used to identify a sources of supply for materials. The transaction code ME01 is used for creating a Source List.
26. How can change the standard price in SAP master material?
Ans:
There is no way to update or change a standard price for the material data directly. However, can perform the following steps to change standard price:
Fill in future fields price (MBEW-ZKPRS) and materials’ effective data (MBEW-ZKDAT).
27. What does use of keeping a record of information of purchase?
Ans:
It is necessary to keep the record of purchase information because it collects the various information of vendors and the materials supplied by them. For example, current price at which the vendor sells material is recorded in a purchase record.
28. Explain the terms Planned delivery and GR processing time?
Ans:
Planned delivery: The term Planned delivery specifies a number of calendar days required to obtain a material.
GR processing: The term GR processing specifies a number of workdays required after receiving material for inspection and placement into the storage.
29. What does Goods Receipt in SAP system?
Ans:
After vendor process the purchase order, the material is delivered to ordering party. This process is called the goods receipt. So, the Goods Receipts is the phase in which ordering party receives the material, and condition and quality are verified. Once the material is verified against quality, then the Goods Receipt is posted.
30. Explain the terms production order and purchase order?
Ans:
Production order: The term production order specifies the which material needs to be prepared at which time and location. It is concerned about the quantity required. It also finds the components and sequence of operations and order costs that need to be resolved.
Purchase order: The Purchase order is issued by a Vendor or the factory to supply the certain quantity of products and services at particular time and location.
31. What does purchase requisition?
Ans:
A purchase requisition is the primary document used as part of the accounting method to launch merchandise or supply purchase. And have to process the purchase order for a suitable controls, monitor a legitimacy of purchase, and identify business requirement for the products.
32. Define master data?
Ans:
Master Data is created centrally and is valid for the almost all applications, and it remains constant over time, but have to update it regularly. For example, the VendorVendor is the type of master data, and it is used for creating a purchase orders.
33. What does material valuation?
Ans:
In SAP MM, material valuation is the module necessary to determine a stock value of materials.
34. What does main function of SAP MM?
Ans:
SAP MM (Materials Management) is the module of SAP ERP software package from SAP AG that is used for a Procurement Handling and Inventory Management. SAP Materials management covers all the tasks within the supply chain, including the consumption-based planning, planning, vendor evaluation and invoice verification.
35. What does different Procurement types that can establish Purchase requisition in SAP MM?
Ans:
Stock transfer: It is used to specify the transfer of material within organization.
Subcontracting: It is used for sending a raw material to the seller and getting back finished material.
Standard: It is used for getting a back finished material from the seller.
External service: It is used to specify a availing services from third-party sellers like maintenance.
36. What does plant in SAP MM?
Ans:
A plant is operational facility within a company code (e.g. a production facility, regional or branch office). As organizational unit within a logistics, the plant subdivides an enterprise from viewpoints of production, procurement, maintenance, and materials planning. Technical Data.
37. What is meant by consumption-based planning (CBP)?
Ans:
CBP stands for Consumption-Based Planning, which is used to forecast to find out a future requirements. It is dependent upon the past consumption values. Based on CBP, net requirement of goods is be calculated. CBP is activated either when a stock level comes below the particular reorder point or when the forecast needs to be calculate past consumption values.
38. What does term material requirement planning (MRP)?
Ans:
In SAP MM, MRP stands for the Material Requirement Planning. It is module or a sort of planning tool in SAP ERP (Enterprise Resource Planning). It is used to assist the procurement and production planners in establishing a realistic and possible plans to help initiate the procurement and production procedures.
39. What distinguishes the phrases MRP from CBP?
Ans:
The main distinction between MRP and CBP is that, while planning materials, MRP is used to forecast material requirements based on SOP (sales and operations planning). However, in CBP, material management (MM) forecasts must be made based on previous material demand.
40. What does transaction code in SAP MM?
Ans:
A transaction code is made of the letters, numbers, or both. It is entered in command field at a top of an SAP GUI screen. Every function in SAP ERP has an associated SAP transaction code that facilitates to access any function in SAP directly. A transaction code is also called the t-code.
41. What is the SAP MM material ledger?
Ans:
The SAP MM material ledger is used to record all transactions associated with buying and using materials to make items. Data from a plant’s material ledger that pertains to a certain posting period includes valuation and control information. The material ledger contains a data for material movements that are relevant to the valuation of material.
42. What does different accounts used in Invoicing?
Ans:
- Vendor accounts
- Stock accounts
- GR/IR clearing accounts
- Tax account
Following are different accounts used in Invoicing:
43. How does create Consignment Stocks?
Ans:
Everything is same as a normal PR or PO, except: Enter an item category “K” for the consignment item. This ensures that Goods Receipt is posted to the consignment stores and invoice receipt cannot be generated for item. Also, do not enter the net price.
44. What MRP procedures available in MM-CBP (Consumption Based Planning)?
Ans:
The MRP (Material Requirements Planning) uses a variety of material planning techniques. Procedure to reorder points (VM) Planning based on forecasts (VV) Planning materials according to timing (PD) These are the ones that are stated in the MRP 1 tab’s material creation (MM01) section.
45. What does Master Production Schedule (MSP) in SAP MM?
Ans:
In SAP MM, MSP stands for the Master Production Schedule. It is used to plan for the individual commodities that need to produce in each time, such as production, inventory, staffing, etc. It is linked to the manufacturing, where the plan shows how much and when every product will be demanded.
46. What does Confirmation Control Key (CCK)?
Ans:
The Confirmation Control Key or CCK is used to specify whether the notification for shipping is an expected purchase order item or not.
47. How does create Consignment Stocks?
Ans:
Everything is same as a normal PR or PO, except: Enter an item category “K” for the consignment item. This ensures that Goods Receipt is posted to the consignment stores and invoice receipt cannot be generated for item. Also, do not enter the net price.
48. What is a Quotation?
Ans:
Once a vendor has received RFQ, the vendor will send back quote that will be legally binding for a certain period of time. Specifically, the Quotation is an offer by a vendor to the purchasing organization regarding supply of material(s) or performance of service(s) subject to the specified conditions.
49. What does release group in SAP MM?
Ans:
In SAP MM, release group is the two-digit code assigned with class and contains one or more release strategies. For example, release group 01 is defined for a purchase requisitions, and release group 02 is defined for a purchase order.
50. How does Material Valuation associated with Financial Accounting?
Ans:
In SAP MM, Material valuation is directly associated with the Financial Accounting. If make any changes in a stock value, it also updates the G/L account in Financial Accounting.
51. What accounts created in SAP MM?
Ans:
- Account assignment type
- An account that will be charged when post the invoice or goods receipt
- Account assignment data that have to provide
Assignment of account is necessary for purchase order item. It is important as finds the following things:
52. How does list of all reservations in system displayed?
Ans:
The list of all the reservations can be displayed by running RM07RESL report in SAP MM.
To change the batch record, can use the transaction code MSC2N. Following is navigation path of changing a batch record:
SAP Menu -> Logistics -> Materials Management -> Material Master -> Batch ->> Change.
53. What does subcontracting cycle in SAP MM?
Ans:
The transfer of raw or input materials to the third party in exchange for delivery of finished product is. On a purchase order, products that are going to be carried out by third party are placed in “L” category. The seller is given shipment of type 541 when a raw ingredients are delivered to them. When GR of type 101 is responsible for taking care of the material consumption, movement type 543 is automatically triggered.
54. Why does need “SPLIT VALUATION”?
Ans:
It is often required that numerous stock valuations of a same material be carried out within a same valuation zone. This can be case because of a difference in price, quality, prestige, or some other factor. In these kinds of a circumstances, utilize split valuation.
In this arrangement, materials are kept track of and maintained at number of subsidiary stocks that are on the smaller scale. This level of fractional share is utilized in all transactions where worth of the company is an important consideration. When it comes to the accounting, one of first considerations for any given material is whether or not it needs a split valuation.
55. Explain “Cost Centers” ?
Ans:
Management and planning are supported through usage of accounting by the cost center. It’s tiniest manageable piece of a control zone, and it corresponds to a specific spot in real world. One could designate any section as their “cost center” in order to be better monitor their expenditures.
56. What does “batches” refer to in SAP MM?
Ans:
Batches are the smaller units that can be used to represent material’s inventory after it has been divided up. It is shorthand for entity that cannot be divided and must be defined by itself.
In manufacturing parlance, a “batch” refers to quantity of a particular substance that is created during course of a single production run.
57. What does copy of Production Order contain?
Ans:
- A Production order will detail required quantity of goods, the type of material to be manufactured, the facility at which manufacturing must take place, the day and time of production, and date and time of manufacturing.
- A Production Order not only contains materials and procedures that are going to be used, as well as the mode of payment that is going to be used for order, but it also specifies any unique handling the instructions that may be required.
58. What does quote in SAP MM?
Ans:
The supplier is obligated to be adhere to the terms of quote that they offer in response to RFQ for a certain period of time. To provide the additional clarity, a quotation is offer that is made by supplier to the purchasing organization for supply of goods or the performance of the services under particular conditions.
59. How many different ways are there to check if invoice is correct?
Ans:
Invoices that are based on the purchase orders. Even if one of the products on purchase order was delivered in the number of separate instalments, Invoice Verification will nevertheless make it possible to make unified payment for an entire order’s worth of goods and services.
A single entry is used to record aggregate total of all deliveries. invoices for a goods that were received. When invoice verification is based on receipt of goods, each individual goods receipt is billed in its own separate transaction. Receipts that do not contain the reference to a purchase order anywhere on page.
60. What does intended to be done with the profit center?
Ans:
Businesses are able to determine the effectiveness of a certain departments or divisions inside a company with the assistance of method called “profit center accounting.” A profit center is a component of accounting that helps to keep track of earnings. It is an essential part of discipline. A connection has been made between material master and the profit center on a plant level.
61. Mention the types of stocks available in special stock.
Ans:
- Subcontracting
- Consignment
- Stock Transport Order
- Third-Party Processing
- Returnable Transport Packaging
- Pipeline Handling
62. What does “receive goods” when are talking about SAP?
Ans:
Goods receipt is a term used to describe the process by which vendor satisfies the customer’s request and then ships the products to buyer. At this point, the individual who placed the order will have received a material, at which point the condition of item and its overall quality will be evaluated. The entry for receipt of the goods is not made until after material quality has been verified.
63. What does RFQ process in SAP MM?
Ans:
A Request for Quotation, or RFQ, is the formal request for an estimate of the cost. A request for pricing information as well as terms and conditions is being sent to be possible vendors. An RFQ will typically include the information regarding delivery timeline, quantity, goods or services offered, and submission date.
64. What is MIRO?
Ans:
MIRO means “transfer of funds in and out.” It is charge of the verification processes for bills that are submitted by the supplier. To put itthe another way, MIRO is what MIRO employs.
65. Mention types of stocks available in valuated stock.
Ans:
Unrestricted Stock: Unrestricted stocks are stocks that are ready for use and available at hand in facility.
Quality Inspection Stock: Quality inspection stocks are those delivered materials that are retained to check or inspect a quality.
Blocked Stock: The materials that come under the blocked stocks are those found to be of bad quality.
66. What does Master Production Schedule (MPS)?
Ans:
Master Production Schedule or MSP can be defined as the plan laid out by a company for production, staffing, inventory, etc., for individual final articles. In this scheduling, the company plans which product and related quantities get produced during the period. Usually, this period spans between 3-18 months. The data used as input in the Master Production Schedule include the forecast demand, production costs, inventory cost, etc.
67. Distinguish difference between goods receipt and post goods receipt?
Ans:
Aspect | Goods Receipt | Post Goods Receipt | |
Timing |
Upon physical receipt |
After physical receipt | |
Purpose | Records receipt in inventory | Updates inventory and financial records | |
Action | Physical handling & inspection | Administrative tasks | |
Primary Role |
Warehouse staff |
Accounting/procurement |
68. What does vendor master data?
Ans:
The term “vendor master data” refers to collection of information that an organization maintains on all companies that provide it with the goods and services. The individual vendor master records store a master data that pertains to every individual vendor. This information may include name and address of the vendor, transaction currency, payment conditions, and the name of point of contact (on the sales staff).
69. Is it possible to flag content for deletion?
Ans:
The Archive and Delete programmes does not allow for the simple deletion of objects from a database without first designating them for deletion. At the client, plant, or archive level, a deletion flag can be set. These are three different levels where it can be done.
When designate content for deletion at one level, it is likewise marked for deletion at any lower levels that have a same name as the higher level at which it was marked for deletion. Use MM06 transaction in order to indicate that a material is to be removed from use.
70. Explain order of purchase?
Ans:
This is the formal and last certification of a vendor’s commitment to provide the industry with certain necessary products. All of the names of the necessary components and their corresponding plants will be included. The business code, the name of the seller, and the date of material delivery are all included in the purchase information.
71. How does it go about changing the Valuation Class in SAP MM?
Ans:
The user must Enter T-Code MMAM is t-code that only allows to change the material type; unable to alter the valuation class. The valuation class in the material master is promptly brought up to date after any time an end-user modifies the material type using MMAM transaction. Even if valuation class of a material is changed after system has initially generated it, it will still be recognized as belonging to a same material by the system.
72. Explaining the scaling in MM?
Ans:
When entering the prices into the information database, scales may be utilized. Scales may also be employed. If price of the stuff that are purchasing reduces per unit, then will make use of it. For example, the cost of material ABC would be Rs. 10 for an order of 500 pieces; but, if placed an order for more than 500 pieces, cost would be reduced to Rs. 9. Scales can be retrieved in the Purchase Order from a variety of different master data sources, such as information record, a quota structure, and the other similar resources.
73. How does OBYC valuation grouping code function?
Ans:
- Valuation in SAP can be specified either at a plant level or at the company code, and value area is segmented using the coding system. This plant-level value area is often chosen because individual plant valuations are subject to the variation.
- The use of valuation grouping codes makes an automatic account determination settings more convenient. It is possible for us to generate the common account determination across the multiple valuation areas if assign the same valuation grouping code to each valuation areas.
74. What is “NetWeaver”?
Ans:
NetWeaver is not a stand-alone product but rather an offering that is made by a SAP. It serves as an integrated platform for a technological development. Even the most recent version of foundation has a memorable moniker: the Netweaver. This technology serves as a basis for all of the mySAP applications that are currently available
75. Difference between a Purchase Request and a Purchase Order?
Ans:
In contrast to the Purchase Order, which is more formal request for goods or services from the manufacturing facility or an external vendor, a Purchase Requisition only serves as a notification of need for these items. A Purchase Order is a more formal request for a goods or services from a manufacturing facility or an external vendor. In addition, procurement categories like stock transfer, standard, consignment, and external services each have own line-item definitions that may be accessed necessary.
76. What does sets SAP MDM and SAP MM apart from one another?
Ans:
- The MM (Material Management) module focuses on an inventory management (which might include the concerns such as material value, storage, and requirement planning, among the other things), as well as a procurement .
- The term “master data management” (MDM) refers to a process of organizing and managing a company’s most significant data, including but not limited to lists of the customers and suppliers, product descriptions, and financial information.
77. What does “Data Archiving” mean for those who not familiar with MM?
Ans:
Large amounts of data that are no longer required by a system can be removed from database through the process of data archiving. However, this data is still maintained so that it can be used for the reporting. The concept of SAP data archiving relies heavily on the objects that can be created with the SAP Archive Development Kit (ADK).
78. Explain reservation?
Ans:
Reservation is the banning of stock ahead of time to secure its availability later on. It guarantees that a supply is available and may be used as needed.
79. What does stock population?
Ans:
The term “stock population” refers to a total number of stock management units that are accounted for during the inventory take. Every single one of these SMUs is stated in terms of a stock management levels, which are then given to the particular inventory sample. When administrator sets a stock management depth, population of a stock is also defined at that time.
80. What kind of software SAP MM use?
Ans:
The SAP ERP software from SAP AG helps with the process of buying a materials and keeping track of stock. Material Management includes all the parts of the supply chain, from planning based on the consumption to planning, evaluating vendors, and checking bills
81. What does responsibilities of consultant when working with SAP MM?
Ans:
The most important responsibility of SAP MM consultant is to see the project through from beginning to end and to make certain that end users of the software are able to successfully implement a software to achieve individual objectives. have expertise in conducting the gap analysis of existing IT infrastructure, writing a user guides, and creating a workflow that covers an entire order-to-cash process.
82. What does RFQ?
Ans:
RFQ is Request For Quotation. It is the kind of form that is given to vendors for them to submit any quotation which is indicative of terms and conditions and the price of goods and materials. It has details of quantity of the goods, information about goods, the delivery date of when the form is to be submitted.
83. Mention last stage in cycle of procurement?
Ans:
The last stage of a procurement cycle is verification of the invoice. This also updates a documents which are related to accounts and finances. There is a difference between real invoice and the blocked one real invoice can be handled by verification of invoice.
84. How does parked documents shown?
Ans:
Documents that have been parked are denoted by the codes FBV3 and FB03. FBV3 shows just parked sheets, but FB03 displays all posted sheets. It is useful to utilise FBV3 to determine whether any papers require approval or completion.
85. Is it possible to make changes to Purchase Requisition after it has been created?
Ans:
Yes. To complete this transaction, please utilize the ME52N. Check to see if PO was created in response to PR that was submitted. In that event, the Purchasing Committee really needs to be aware of situation. Make sure that check the current standing of PR. If this is the case, the extent to which are permitted to make changes to document will depend on and might require approval.
86. What does someone refers to a “Price Control Indicator”?
Ans:
The “Price Control Indicator” is the record that is maintained from accounting point of view and that is referred to when determining an appropriate price to place on certain material. There are the two possible outcomes here: the first one is Standard Price (S), and the second one is Moving Average Price (V).
87. What does free item in SAP system?
Ans:
The Price will be marked zero for the free item and can tick the item as a free item while creating the PO in system.
88. What does Pricing procedure in MM?
Ans:
The Pricing process in the MM module is the channel for calculating prices in purchase papers. This allows us to assign multiple computation types for different uses. During the development of the PO and RFQ The pricing process is used in the MM module. The entire material value is based on all additions and subtractions such as surcharge, discount, tax, goods and so on.
89. What does Master Production Schedule (MPS)?
Ans:
Master Production Schedule or MSP can be defined as the plan laid out by a company for production, staffing, inventory, etc., for individual final articles. In this scheduling, the company plans which product and related quantities get produced during the period. Usually, this period spans between 3-18 months. The data used as input in the Master Production Schedule include the forecast demand, production costs, inventory cost, etc.
90. What does RTP?
Ans:
RTP (Returnable Transport Packaging) is referred to the multi-trip packaging medium (for instance, containers or pallets) through which goods can be transported multiple times between the customers and vendors. Returnable transport packaging from vendor which is stored at a place on the premises is treated as a special stock and is clearly assigned as belonging to the vendor. RTP is vendor’s property, therefore, it is excluded from a customer’s valuated stock.