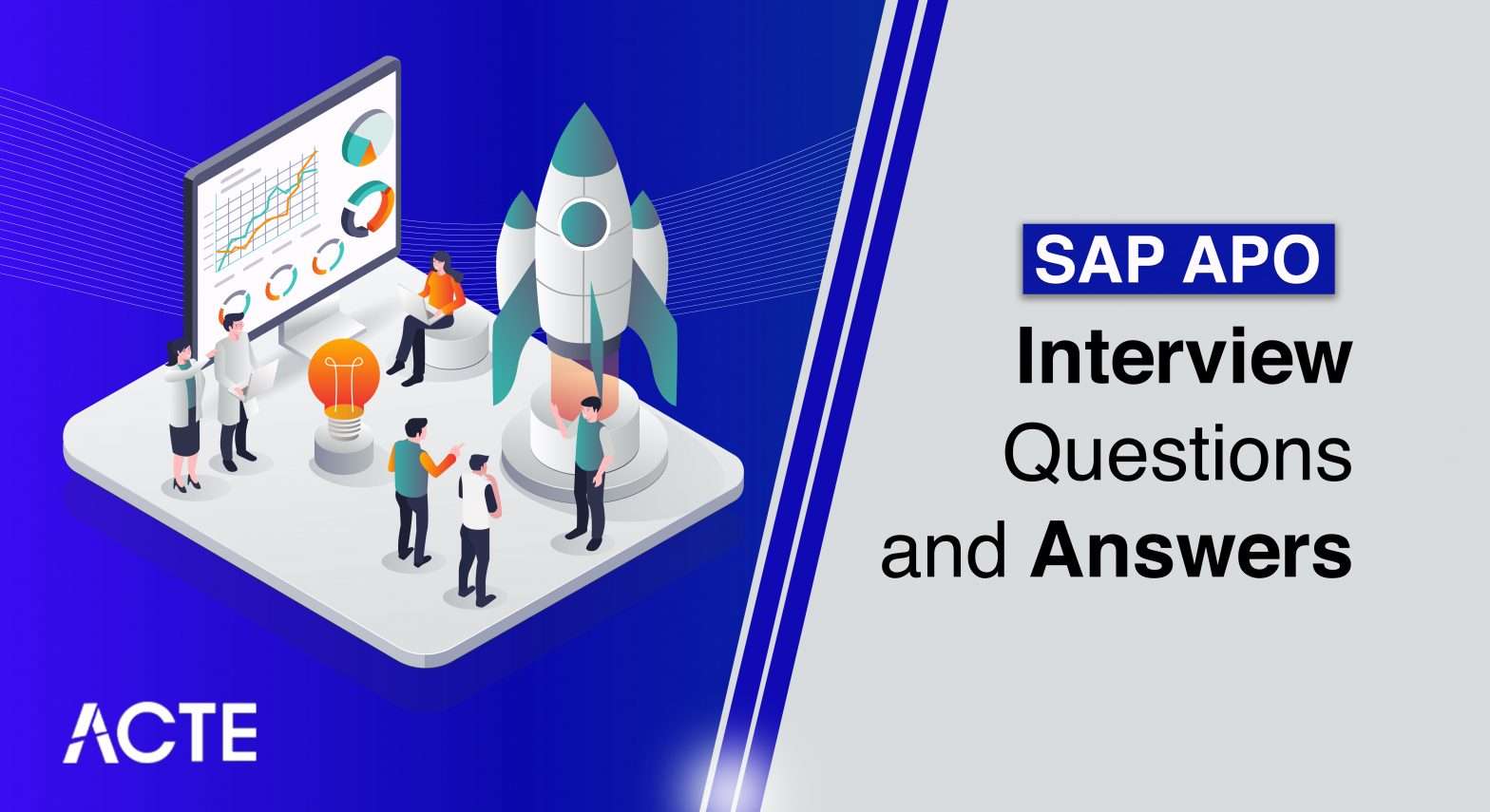
SAP APO (Advanced Planner and Optimizer) is a comprehensive solution for optimizing supply chain management. It includes modules like Demand Planning (DP), Supply Network Planning (SNP), Production Planning and Detailed Scheduling (PP/DS), and Global Available-to-Promise (GATP). SAP APO helps organizations forecast demand, plan production and distribution, and optimize inventory levels. It integrates with ERP systems to enhance operational efficiency, reduce costs, and improve customer service by ensuring timely delivery and optimal resource utilization.
1. What is SAP APO, and what are its main components?
Ans:
SAP Advanced Planner and Optimizer (APO) is a suite designed to improve supply chain management. Its main components include Demand Planning (DP) for forecasting, Supply Network Planning (SNP) for optimizing supply chains, Production Planning/Detailed Scheduling (PP/DS) for scheduling production, Global Available-to-Promise (GATP) for order fulfilment, and Transport Load Builder (TLB) for managing transportation.
2. How does SAP APO integrate with other SAP modules?
Ans:
SAP APO integrates with SAP ECC and other modules through the Core Interface (CIF). This integration allows seamless data exchange between APO and modules such as Material Management (MM), Sales and Distribution (SD), and Production Planning (PP). CIF ensures real-time synchronization, enhancing supply chain visibility and efficiency and creating a cohesive planning environment.
3. What are the benefits of utilizing SAP APO for supply chain management?
Ans:
- SAP APO provides numerous benefits in supply chain management, including improved demand forecasting and inventory optimization.
- It enhances production planning and supplier collaboration, reducing lead times.
- APO minimizes costs and boosts efficiency by offering advanced planning and optimization tools, ensuring smooth operations across the supply chain through its integration capabilities.
4. Explain the architecture of SAP APO?
Ans:
- SAP APO’s architecture consists of a user interface layer, a database layer, and an application layer.
- It uses the SAP NetWeaver platform for integration with other systems, ensuring efficient communication.
- The Core Interface (CIF) synchronizes data between APO and ECC.
- This multi-layered architecture supports robust and scalable planning processes.
5. What is the difference between SAP APO and SAP ECC?
Ans:
Criteria | SAP APO (Advanced Planner and Optimizer) | SAP ECC (ERP Central Component) |
---|---|---|
Focus | Optimizes supply chain planning and scheduling processes. | Manages core business operations across various modules like finance, HR, etc. |
Modules | Includes Demand Planning (DP), Supply Network Planning (SNP), PP/DS, GATP, etc. | Covers modules for financials, human resources, logistics, and more. |
Functionality | Specializes in advanced planning, scheduling, and optimization of supply chain. | Supports enterprise-wide business processes and transactional data management. |
Integration | Integrates closely with SAP ECC for data exchange and master data synchronization. | Acts as the central ERP system, often integrated with SAP APO for planning. |
6. What are SAP APO’s salient characteristics?
Ans:
Key features of SAP APO include advanced demand forecasting for accurate future demand predictions. Supply Network Planning (SNP) optimizes the supply chain network, while Production Planning/Detailed Scheduling (PP/DS) enhances production efficiency. Global Available-to-Promise (GATP) ensures reliable order fulfilment. Robust integration capabilities link APO seamlessly with SAP ECC.
7. How does SAP APO support supply chain planning?
Ans:
- SAP APO supports supply chain planning through its modules, offering tools for various aspects of planning.
- Demand Planning (DP) generates accurate forecasts, and Supply Network Planning (SNP) optimizes supply chain operations.
- Production Planning/Detailed Scheduling (PP/DS) improves production efficiency.
- These tools provide a comprehensive approach to planning, resulting in an efficient supply chain.
8. What is Demand Planning in SAP APO?
Ans:
- Demand Planning (DP) in SAP APO provides tools to forecast future product demand accurately.
- It uses historical data and advanced statistical algorithms to generate precise demand forecasts, which facilitate better planning and decision-making across the supply chain.
- DP integrates with other APO modules to ensure cohesive planning processes.
9. What are the steps to create a planning book in DP?
Ans:
To create a planning book in Demand Planning (DP), the initial step involves defining a planning area using the Planning Book/Data View Administration transaction (/SAP APO/SDP8B). In this configuration process, specify key elements such as the planning area itself, relevant key figures, and time buckets. These components are crucial as they shape the structure and functionality of the planning book, tailoring it precisely to meet specific forecasting requirements.
10. What is a planning area, and how is it configured?
Ans:
A planning area in SAP APO defines the scope of planning activities, including key figures, characteristics, and time buckets. It is configured using the Planning Area Administration transaction (/SAP APO/SDP1). Here, you define the relevant key figures and their attributes, which are crucial for accurate and effective demand planning in SAP APO. Additionally, the planning area allows for the configuration of planning levels and the assignment of key figures to these levels.
11. What role do planning objects play in Demand Planning?
Ans:
- Planning objects in Demand Planning refers to entities such as products, locations, and customers that are essential for creating accurate forecasts.
- These objects are categorized into characteristics and critical figures, defining the scope and detail of planning activities.
- They play a crucial role in organizing data and generating precise demand forecasts.
12. What is the difference between statistical forecasting and consensus forecasting?
Ans:
- Statistical forecasting relies on historical data and mathematical models to predict future demand, using algorithms for accuracy.
- Consensus forecasting, on the other hand, involves collaboration among various stakeholders, combining statistical data with insights from sales, marketing, and other departments.
- This approach merges quantitative data with qualitative input for a comprehensive forecast.
13. What methods are used to handle seasonality in demand planning?
Ans:
Seasonality in demand planning is managed by examining past sales data to find trends and patterns corresponding to specific periods. Advanced forecasting models, like seasonal decomposition, are applied to separate seasonal effects from overall demand. Adjusting forecasts accordingly ensures that seasonal variations are accurately reflected in demand predictions.
14. What is the role of macros in Demand Planning?
Ans:
Macros in Demand Planning are automated scripts that perform repetitive tasks, calculations, and data manipulations. They enhance efficiency by automating complex processes, ensuring consistency and accuracy. Macros are used to customize planning books, automate data transfers, and execute specific planning functions, streamlining the demand planning workflow.
15. What is the process to configure a time series in DP?
Ans:
- Configuring a time series in DP involves defining the relevant key figures, time buckets, and data storage parameters.
- This is done through the Planning Area Administration transaction (/SAP APO/SDP1).
- Accurate time-series configuration ensures that demand data is correctly captured, stored, and analyzed over specified time intervals for effective planning.
16. What are key figures, and how are they used in Demand Planning?
Ans:
- Key figures in Demand Planning represent quantitative data elements, such as sales quantities or inventory levels, that are critical for forecasting and analysis.
- They are used to measure and track performance, generate reports, and support decision-making processes.
- Key figures provide the numerical basis for evaluating demand and planning accuracy.
17. What is the purpose of the DP master data?
Ans:
The DP (Demand Planning) master data serves as the foundational dataset crucial for effective planning environments. It encompasses comprehensive information on products, locations, and other pertinent entities essential for ensuring data consistency and accuracy in demand forecasts. Master data management plays a pivotal role in maintaining the reliability and currency of this information, thereby ensuring that all planning activities, from forecasting to resource allocation, are founded on robust and up-to-date data sets.
18. What are the critical steps in configuring the planning area in DP?
Ans:
Configuring the planning area in DP involves defining characteristics, key figures, and time buckets. This setup is done using the Planning Area Administration transaction (/SAP APO/SDP1). Key steps include:
- Selecting the relevant data elements.
- Establishing their relationships.
- Configuring the planning parameters to support accurate and effective demand planning.
19. What are the steps to customize macros in DP?
Ans:
Customizing macros in DP involves writing and editing macro scripts to automate specific tasks within the planning process. This customization is done through the Macro Workbench, where users can create, test, and implement macros. Customized macros help streamline repetitive tasks, enhance accuracy, and tailor the planning process to specific business needs.
20. What is the role of the DP workbench?
Ans:
The DP workbench is a central tool in Demand Planning that provides a user-friendly interface for managing planning activities. It allows users to create, modify, and analyze planning books, key figures, and macros. The workbench facilitates efficient planning by offering visualization tools, data management capabilities, and access to various planning functions. Additionally, it supports integration with other SAP modules and provides customizable features to adapt to specific planning needs.
21. What approach is used to manage lifecycle planning in DP?
Ans:
- Lifecycle planning in DP involves overseeing the stages of a product’s lifecycle, from launch to decline.
- This process utilizes historical data and predictive analytics to forecast demand for new products, adjust for mature products, and phase out declining products.
- Effective lifecycle planning ensures accurate inventory levels and optimized supply chain operations.
22. What is Supply Network Planning in SAP APO?
Ans:
- Supply Network Planning (SNP) in SAP APO optimizes the supply chain by balancing supply and demand across the network.
- SNP encompasses demand, distribution, production, and procurement planning.
- It employs advanced algorithms to generate feasible plans, considering constraints and capacities, ensuring efficient resource utilization and meeting customer demands.
23. How does SNP differ from DP?
Ans:
SNP (Supply Network Planning) focuses on optimizing the entire supply chain network, covering production, distribution, and procurement. DP (Demand Planning) primarily deals with forecasting customer demand based on historical data. While DP predicts future demand, SNP aligns this demand with supply chain capabilities to create a feasible and optimized plan.
24. What is the role of the SNP optimizer?
Ans:
The SNP optimizer in SAP APO uses advanced mathematical algorithms to generate optimal supply chain plans. It considers constraints like production capacities, transportation limits, and procurement restrictions. The optimizer aims to minimize costs while meeting demand, ensuring efficient resource utilization and enhanced supply chain performance. Additionally, it incorporates real-time data and scenario analysis to adapt to dynamic changes in the supply chain environment.
25. What is the heuristic planning method in SNP?
Ans:
- The heuristic planning method in SNP involves rule-based algorithms to create feasible supply chain plans quickly.
- Unlike optimization, heuristics provide approximate solutions by following predefined rules and priorities.
- This method is helpful in generating initial plans and handling complex scenarios where speed is crucial over absolute precision.
26. What is the purpose of the transportation load builder (TLB) in SNP?
Ans:
- The Transportation Load Builder (TLB) in SNP optimizes the transportation process by consolidating shipments into optimal loads.
- It ensures efficient use of transportation resources, reduces costs, and improves delivery performance.
- TLB considers factors like shipment size, vehicle capacity, and delivery schedules to create cost-effective transportation plans.
27. What is the process for configuring the SNP planning area?
Ans:
Configuring the SNP planning area involves defining characteristics, key figures, and planning parameters. This setup is done through the Planning Area Administration transaction (/SAP APO/SDP1). Key steps include selecting relevant data elements, establishing relationships, and setting planning parameters to support effective supply network planning. Additional considerations include defining time buckets and integrating with other APO components to ensure cohesive planning processes.
28. What is a supply chain model in SNP?
Ans:
In SAP SNP (Supply Network Planning), the supply chain model encompasses a comprehensive network comprising suppliers, production facilities, distribution centers, and customers. It integrates critical data such as capacities, lead times, and operational constraints across these nodes. This model serves as the foundational framework for strategic planning and optimization within the supply chain. It enables the simulation of diverse scenarios, facilitating the creation of efficient and responsive supply chain plans.
29. How does the SNP optimizer handle constraints?
Ans:
- The SNP optimizer handles constraints by incorporating them into the optimization algorithm.
- Constraints can include production capacities, transportation limits, and procurement restrictions.
- The optimizer ensures that the generated plans respect these constraints while aiming to minimize costs and meet demand, resulting in feasible and efficient supply chain solutions.
30. What are the critical parameters for SNP planning?
Ans:
- Critical parameters for SNP planning include planning horizons, demand profiles, supply lead times, and resource capacities.
- Other important parameters are transportation costs, production rates, and inventory levels.
- Accurate configuration of these parameters ensures that the SNP planning process generates realistic and practical supply chain plans.
31. What methods are used to manage capacity planning in SNP?
Ans:
Capacity planning in SNP involves assessing resources against demand to ensure production meets requirements. Using SAP SNP, you define capacity resources like work centres and machines, then integrate them with production plans and demand forecasts. SNP uses heuristic and optimization algorithms to balance capacity with demand, adjusting production schedules dynamically. It also supports what-if scenarios for capacity adjustments, enabling proactive planning and resource allocation to optimize production efficiency.
32. What is the configuration process for transportation lanes in SNP?
Ans:
Configuring transportation lanes in SNP involves defining routes between locations for transporting goods. Set up transportation lanes in SAP SNP by specifying origins, destinations, carriers, modes of transport, and associated costs. This configuration facilitates efficient transportation planning and execution within the supply chain network. SNP uses transportation lane data to optimize freight costs, transit times, and delivery reliability across the network, ensuring smooth logistics operations and customer satisfaction.
33. What is the role of the supply chain engineer in SNP?
Ans:
- The supply chain engineer in SNP plays a crucial role in optimizing supply chain operations using SAP APO SNP functionalities.
- They analyze supply chain data, identify bottlenecks, and propose solutions to enhance efficiency.
- Responsibilities include configuring SNP modules, conducting supply-demand simulations, and implementing strategies for inventory management and distribution planning.
- Supply chain engineers collaborate with stakeholders to align production schedules with demand forecasts, ensuring timely delivery and cost-effective resource allocation.
34. What is Global ATP in SAP APO?
Ans:
- Global Available-to-Promise (GATP) in SAP APO consolidates ATP checks across multiple locations and product categories.
- It provides a unified view of product availability, considering global inventory, production capacities, and transportation constraints.
- GATP enhances order fulfilment by optimizing allocation decisions based on real-time data, ensuring commitments are met across the supply chain network.
- This functionality supports complex supply chain scenarios, improving customer service levels and operational efficiency.
35. How does GATP differ from standard ATP in SAP ECC?
Ans:
GATP extends ATP capabilities beyond single-location checks in SAP ECC by integrating multiple supply chain elements. Unlike standard ATP in ECC, which focuses on individual plant or storage location availability, GATP considers global inventory, transportation, and production capacities. It enables cross-location allocation, backorder processing, and dynamic order promising based on complex rules and constraints.
36. What is a product allocation in GATP?
Ans:
Product allocation in GATP refers to the distribution of limited inventory across multiple customers or sales orders during shortage situations. It defines rules for prioritizing order fulfilment based on customer importance, order size, or contractual agreements. Product allocation ensures fair distribution of scarce resources while optimizing revenue and customer satisfaction. GATP uses predefined allocation strategies and real-time data to allocate products effectively, minimizing backorders and maximizing order fulfilment rates.
37. What is the process for backorder processing in GATP?
Ans:
- Backorder processing in GATP manages orders that cannot be fulfilled immediately due to inventory shortages or production constraints.
- It prioritizes backorders based on predefined rules, such as customer priority or order date, to optimize order fulfilment.
- GATP dynamically reallocates available inventory and production capacity to reduce backlogs and meet customer commitments promptly.
- Real-time visibility into backorder status and automated alerts enable proactive decision-making, ensuring minimal impact on customer satisfaction and operational efficiency.
38. What is rule-based ATP, and how is it configured?
Ans:
Rule-based ATP (Available-to-Promise) in SAP IBP allows configuring ATP logic based on predefined rules and priorities. It guarantees that customers’ orders can be completed depending on particular standards like product availability, sourcing rules, and constraints. Configuration involves:
- Setting up rules in SAP IBP’s ATP process configuration.
- Defining order fulfilment priorities.
- Establishing conditions for checking product availability against demand.
39. How does GATP handle multi-level ATP checks?
Ans:
Global Available-to-Promise (GATP) in SAP manages multi-level ATP checks by evaluating product availability across the entire supply chain network. It considers constraints, rules, and data from multiple locations and nodes. GATP aggregates ATP results from various levels to provide comprehensive visibility into product availability and delivery commitments. This process involves integrating data from different systems, applying ATP logic across interconnected nodes, and orchestrating fulfillment decisions throughout the supply chain.
40. What is a check mode in GATP?
Ans:
In GATP (Global Available-to-Promise), a check mode determines the scope and criteria for checking product availability against customer demand. It defines how and when ATP checks are executed based on specific business requirements and operational constraints. Standard check modes include checking against current stock, future receipts, production plans, and transportation schedules. Configuration involves:
- Selecting appropriate check modes in SAP settings.
- Defining ATP rules and priorities.
- Configuring ATP profiles to align with business processes.
41. What steps are involved in configuring a location substitution in GATP?
Ans:
To configure a location substitution in GATP, navigate to transaction /SAP APO/LOC3, select the relevant product and location combination, and define the substitution rule. Specify the substitute location and conditions under which substitution should occur, such as lead time or capacity constraints. Save the substitution rule and activate it to ensure it is effective in the ATP check. Test the configuration thoroughly in a sandbox environment before deploying it in production to ensure it meets business requirements and does not adversely impact ATP results.
42. What are the critical steps in setting up a GATP process?
Ans:
Setting up a GATP (Global Available-to-Promise) process involves several key steps. First, define product allocation rules and strategies based on business priorities. Configure ATP groups to control availability check behaviour across different product categories. Establish product substitution rules to manage inventory shortages effectively. Integrate GATP with relevant SAP ERP modules for real-time data exchange. Customize ATP check rules and tolerances to align with business needs.
43. What methods are used to handle product availability in GATP?
Ans:
- Handling product availability in GATP involves configuring ATP rules and strategies to ensure accurate and timely availability checks.
- Define ATP categories and priorities based on product characteristics and customer requirements.
- Use product substitution and alternative sourcing strategies to manage shortages and fulfil orders on time.
- Monitor inventory levels and update ATP data regularly to reflect real-time stock availability.
44. What is PP/DS in SAP APO?
Ans:
- PP/DS (Production Planning and Detailed Scheduling) in SAP APO is an advanced planning tool that enhances production planning and scheduling capabilities.
- It enables detailed scheduling based on finite capacity and material availability.
- PP/DS optimizes production sequences, considers constraints, and generates feasible production plans to meet demand efficiently.
- It integrates with SAP ERP and other APO modules to synchronize manufacturing operations with overall supply chain planning.
45. How does PP/DS integrate with other modules in SAP APO?
Ans:
PP/DS integrates closely with other SAP APO modules like Demand Planning, Supply Network Planning (SNP), and Global Available-to-Promise (GATP). It receives demand forecasts and planned orders from Demand Planning and SNP. PP/DS utilizes these inputs for detailed production scheduling, taking into account material availability and resource constraints. It sends detailed production schedules and capacity requirements back to SNP for further supply chain optimization.
46. What is a planning board in PP/DS?
Ans:
A planning board in PP/DS serves as a graphical user interface for production planners to visualize and manage production schedules. It displays detailed scheduling information, such as operations, work centres, materials, and timelines. Planners use the planning board to create and modify production orders, schedule operations, and allocate resources. It supports interactive planning activities like drag-and-drop rescheduling, capacity levelling, and scenario simulation.
47. What are the steps to create a production plan in PP/DS?
Ans:
- Start by importing demand forecasts and planned orders from SAP APO Demand Planning and SNP modules.
- Use the planning board to visualize demand and available capacity across production resources.
- Generate a feasible production schedule considering material availability, resource constraints, and production priorities.
- Adjust the plan as needed to optimize production efficiency and meet customer demand on time.
- Collaborate with stakeholders to validate the plan and ensure alignment with business goals.
48. What is the difference between finite and infinite planning?
Ans:
- Finite planning considers resource constraints such as labour, materials, and machine capacity to schedule production activities within realistic limits.
- It generates detailed schedules based on available resources and prioritizes orders accordingly to meet demand.
- Infinite planning, on the other hand, assumes unlimited capacity and schedules production without considering resource constraints.
- It provides a broad overview of production requirements but may not reflect real-world limitations.
49. What is the concept of pegging in PP/DS?
Ans:
Pegging in PP/DS refers to the relationship between dependent objects in a production plan, such as orders, operations, and materials. It establishes linkages to maintain traceability and dependency management throughout the production process. Pegging identifies relationships like material requirements for specific operations or operations dependent on preceding tasks. It ensures that changes to one element in the production plan trigger updates and adjustments in related items, maintaining consistency and accuracy.
50. What is the role of the PP/DS optimizer?
Ans:
The PP/DS (Production Planning and Detailed Scheduling) optimizer in SAP APO plays a crucial role in optimizing production plans and schedules to meet demand while considering constraints and objectives. It uses algorithms to generate feasible schedules based on factors like resource availability, production capacities, material availability, and order priorities. The optimizer aims to minimize costs, reduce lead times, and maximize resource utilization.
51. What methods are used to manage scheduling in PP/DS?
Ans:
- In PP/DS (Production Planning and Detailed Scheduling), scheduling is managed through the scheduling board.
- Here, planners can view and adjust production orders, work centres, and capacities in real-time.
- They utilize algorithms to optimize schedules based on available resources and production priorities, ensuring efficient production flow and meeting customer demand.
- Integration with ERP systems like SAP ECC allows for synchronized data updates and real-time visibility into production schedules, enhancing responsiveness to changes and minimizing production delays.
52. What are the critical parameters for production planning in PP/DS?
Ans:
- Critical parameters in PP/DS for production planning include demand forecasts, lead times, production capacities, and resource availability.
- These parameters are essential for creating feasible production plans that meet customer demand while optimizing resource utilization.
- Production constraints such as batch sizes, setup times, and work centre capacities are also crucial for accurate planning in PP/DS, ensuring that production schedules are realistic and achievable within specified timelines.
53. How does PP/DS handle resource planning?
Ans:
PP/DS manages resource planning by evaluating the available capacities of work centers, machines, and labor. It factors in production orders, routings, and scheduling constraints to allocate resources effectively. Resource leveling algorithms balance workloads, minimize bottlenecks, and optimize utilization. Integration with ERP systems like SAP ECC ensures that PP/DS resource planning aligns with business objectives and production strategies, supporting efficient operations and timely product delivery.
54. What is the purpose of the PDS (Product Data Structure) in PP/DS?
Ans:
The Product Data Structure (PDS) in PP/DS defines the structure of a product in terms of its components, bills of materials (BOM), and production processes. It serves as a blueprint for production planning and detailed scheduling, guiding the creation of production orders and scheduling activities. PDS enables planners to simulate different production scenarios, evaluate resource requirements, and optimize production plans based on product configurations.
55. What is the process to set up the planning board in PP/DS?
Ans:
- Setting up the planning board in PP/DS involves configuring views for production orders, work centres, and resources.
- Planners customize layouts to display relevant data such as order status, capacity utilization, and scheduling constraints.
- Filters and grouping options help organize and prioritize production activities based on critical parameters.
- Integration with SAP ECC enables real-time updates and interactive planning sessions, facilitating collaborative decision-making and agile response to production changes.
56. What is the Core Interface (CIF) in SAP APO?
Ans:
- The Core Interface (CIF) in SAP APO (Advanced Planning and Optimization) is a framework for data exchange between SAP ERP (ECC) and APO systems.
- It facilitates seamless integration of master data and transactional data such as sales orders, production orders, and stock levels.
- CIF ensures consistency and accuracy of data across both systems, supporting advanced planning processes like demand planning, supply network planning, and production planning.
- Integration models and queues manage data flow, ensuring timely updates and synchronization between SAP ECC and APO systems.
57. How does CIF facilitate data transfer between SAP ECC and SAP APO?
Ans:
CIF facilitates data transfer between SAP ECC and SAP APO by leveraging integration models, queues, and data structures. It extracts master data and transactional data from ECC, transforms it into APO-compatible formats, and loads it into APO. CIF ensures data consistency and integrity through validation checks and error-handling mechanisms. Real-time or scheduled transfers synchronize data updates across systems, supporting accurate planning and decision-making in APO.
58. What are the critical steps in setting up CIF?
Ans:
- Configuring integration models.
- Defining RFC (Remote Function Call) connections between SAP ECC and APO systems.
- Mapping data structures for master data and transactional data.
Initial data transfer establishes baseline information, followed by delta updates to synchronize changes. Monitoring and error-handling procedures ensure data integrity and reliability. CIF settings also include defining transfer rules, filtering criteria, and scheduling jobs for automated data synchronization.
59. What is the integration model in CIF?
Ans:
The integration model in CIF defines the scope and direction of data transfer between SAP ECC and APO. It specifies which master data and transactional data objects are relevant for synchronization and how they are mapped between systems. Integration models categorize data into outbound (ECC to APO) and inbound (APO to ECC) flows, supporting bi-directional data exchange. Filters and selection criteria refine data selection based on business rules and planning requirements.
60. What are the steps to monitor CIF data transfer?
Ans:
Monitoring CIF data transfer involves using SAP transaction codes like /SAPAPO/CIF and /SAPAPO/OM17 to view transfer logs, error messages, and data status. Monitoring tools provide visibility into data flow, processing times, and error rates, enabling proactive management of data synchronization issues. Alerts and notifications notify administrators of critical errors or delays in data transfer, facilitating prompt resolution.
61. What is a queue, and how is it used in CIF?
Ans:
- A queue in CIF is a mechanism for managing and processing data transfers between systems.
- It organizes and schedules data movements, ensuring orderly and efficient processing of information.
- Queues in CIF handle data flows from SAP ERP systems to SAP APO, providing timely updates of planning data such as materials, resources, and orders.
62. What methods are used to handle errors in CIF?
Ans:
Handling errors in CIF involves monitoring CIF queues for failed or incomplete data transfers. Errors are diagnosed using CIF logs and transaction codes like /SAPAPO/CIFERRLOG. Corrective actions include reprocessing CIF queues, verifying master data consistency, and resolving connectivity issues between SAP systems. Documentation and escalation procedures ensure timely resolution of CIF errors to minimize disruption to planning processes.
63. What are the best practices for using CIF?
Ans:
- Maintaining clean master data.
- Regularly monitoring CIF queues and logs.
- Performing periodic system checks.
- Ensuring proper configuration and connectivity between SAP ERP and APO.
Documentation of CIF processes and training for users involved in CIF operations help maintain smooth data synchronization and accurate planning results.
64. What is the process for configuring CIF for master data transfer?
Ans:
- Setting up integration models in SAP ECC and SAP APO.
- Defining CIF destinations.
- Mapping master data fields.
CIF queues are configured to manage data flow, with settings for data selection and filter criteria ensuring relevant master data is transferred accurately. Testing and validation procedures confirm seamless integration before production deployment.
65. How does CIF handle transactional data?
Ans:
CIF handles transactional data by using CIF integration models to transfer data such as sales orders, purchase orders, and production orders between SAP ERP and SAP APO systems. Transactional data is queued in CIF and processed based on defined scheduling parameters, ensuring real-time updates and synchronization between planning and execution systems. CIF also supports the transfer of master data and configuration settings, enhancing the consistency and accuracy of information across systems.
66. What are the key performance indicators (KPIs) in SAP APO?
Ans:
Key performance indicators (KPIs) in SAP APO include forecast accuracy, inventory turnover, service level adherence, and planning cycle time. These metrics gauge the effectiveness of demand planning, supply network planning, and production scheduling processes. Monitoring KPIs helps optimize supply chain operations and enhance decision-making in response to market demands.
67. What techniques are used to optimize the performance of SAP APO?
Ans:
- Optimizing SAP APO performance involves tuning CIF settings, monitoring system health using transaction codes like ST03, and scheduling batch jobs during off-peak hours.
- Regular database maintenance and archiving of historical data reduce system load.
- Implementing SAP APO on high-performance hardware and upgrading to newer versions enhance system responsiveness and processing speed.
68. What is the role of the liveCache in SAP APO?
Ans:
- The liveCache in SAP APO is an in-memory database that stores planning data for quick access and computation.
- It supports advanced planning algorithms and simulations, enabling real-time calculations for demand forecasts, production plans, and inventory optimization.
- The liveCache maintains data consistency across SAP APO modules, facilitating accurate and responsive supply chain planning.
69. What is the approach to handle data archiving in SAP APO?
Ans:
Data archiving in SAP APO involves identifying and prioritizing data objects for archiving based on business requirements and legal regulations. Archiving sessions are executed using transaction codes like SARA and defining archiving objects. Post-archiving verification ensures data integrity, while access to archived data is maintained for reporting and compliance purposes.
70. What are typical performance issues in SAP APO, and how can they be resolved?
Ans:
- Slow response times.
- High CPU utilization during planning runs.
- Delays in data transfers via CIF.
Resolving these issues involves optimizing liveCache settings, tuning database parameters, and scheduling CIF jobs efficiently. Regular system monitoring and performance tuning mitigate bottlenecks, ensuring the smooth operation of SAP APO’s planning functions.
71. What methods are used to monitor the performance of the SNP optimizer?
Ans:
Monitoring SNP optimizer performance involves regularly reviewing key metrics such as processing time, resource utilization, and optimization results. Transaction codes like /SAPAPO/COPT01 and /SAPAPO/RRP3 are used to analyze optimizer logs and job runs. Monitor system health indicators like memory and CPU usage. Regularly optimize master data and planning parameters to enhance SNP optimizer efficiency.
72. What are the best practices for demand forecasting in DP?
Ans:
- Leveraging.
- Employing effectively leveraging historical data statistical forecasting methods.
- Adjusting forecasts for seasonality and trends.
- Collaborating closely with stakeholders for demand inputs.
Use consensus forecasting techniques and validate forecasts with actual sales data. Regularly review and adjust forecasting models based on market changes and feedback from sales teams.
73. What strategies are employed to handle large volumes of data in SAP APO?
Ans:
Handling large data volumes in SAP APO involves optimizing database performance, implementing data archiving strategies, and leveraging SAP HANA for in-memory processing. Partition large datasets and utilize data compression techniques. Regularly monitor database growth and performance metrics. Use transaction codes like /SAPAPO/OM17 for archiving and /SAPAPO/DBMAN_ANALYZE for database analysis.
74. What is the purpose of the alert monitor in SAP APO?
Ans:
The alert monitor in SAP APO proactively notifies users about critical system events, exceptions, and deviations from planned scenarios. It helps in real-time monitoring of supply chain operations, enabling quick decision-making and issue resolution. Alerts can be configured for various parameters such as stock levels, order delays, and production issues, ensuring timely actions to maintain operational efficiency.
75. What is the process for configuring alerts in SAP APO?
Ans:
- Configure alerts in SAP APO using transaction code /SAP APO/AMON1.
- Define alert rules based on key performance indicators (KPIs), thresholds, and notification criteria.
- Specify recipients and escalation paths for alerts. Test alert configurations to ensure proper functioning.
- Monitor alert logs regularly and adjust configurations as needed based on evolving business requirements and feedback from stakeholders.
76. What are the critical steps in configuring the SNP optimizer?
Ans:
- Configuring the SNP optimizer involves defining planning versions, configuring optimizer profiles, setting optimization objectives, and specifying constraints.
- Validate master data consistency and update planning parameters—test optimizer settings in a sandbox environment before deployment.
- Monitor optimizer runs using transaction code /SAP APO/RRP3 and adjust configurations based on performance and planning results.
77. What are the steps to configure the integration model in CIF?
Ans:
Configure the integration model in CIF using transaction code /SAP APO/CIF. Define logical system connections and activate integration models for relevant master data and transactional data. Specify CIF groups and filters for data transfer. Monitor CIF queues and error logs for data synchronization issues. Regularly reconcile CIF data with source systems to ensure data integrity and consistency across the supply chain.
78. What is the approach for handling custom developments in SAP APO?
Ans:
Handling custom developments in SAP APO involves following SAP’s development guidelines, creating enhancements using user exits or BAdIs, and documenting custom objects comprehensively—custom developments should be tested in a development environment before being transported to production. They should also be regularly reviewed and updated during system upgrades or enhancements. Finally, custom developments should be aligned with business requirements, and functional teams should collaborate to achieve this.
79. What is the role of DP-PI (Demand Planning – Process Integration) in SAP APO?
Ans:
- DP-PI in SAP APO facilitates seamless integration of demand planning processes with other SAP modules and external systems.
- It ensures consistent data flow between demand planning (DP) and logistics execution, production planning, and procurement processes.
- DP-PI enables real-time demand updates, enhances forecasting accuracy, and supports collaborative planning across the supply chain network.
80. What steps are involved in implementing VMI (Vendor Managed Inventory) in SAP APO?
Ans:
- Establishing collaboration agreements with vendors.
- Defining VMI-specific planning strategies.
- Configuring replenishment cycles based on vendor-managed stock levels.
Use transaction codes like /SAPAPO/VM02 for VMI planning and /SAPAPO/VM60 for monitoring VMI processes. Regularly review VMI performance metrics and adjust planning parameters to optimize inventory levels and supply chain efficiency.
81. What methods are used to handle collaborative planning in SAP APO?
Ans:
Collaborative planning in SAP APO involves integrating stakeholders across the supply chain to share forecasts, demand data, and production plans. This is facilitated through collaborative demand planning and supply network collaboration functionalities. Stakeholders can jointly adjust plans, ensuring alignment and responsiveness to market changes.
82. How does SAP APO support S&OP (Sales and Operations Planning)?
Ans:
SAP APO (Advanced Planner and Optimizer) enhances Sales and Operations Planning (S&OP) by integrating critical processes such as demand, supply, and financial planning. It enables scenario planning, demand sensing, and consensus forecasting to synchronize sales forecasts with operational strategies. By aligning these elements, SAP APO helps organizations balance demand and supply dynamics, optimize inventory levels, and improve overall business agility.
83. What is the role of the DP master data template?
Ans:
The DP (Demand Planning) master data template in SAP APO standardizes and organizes essential data elements like product hierarchies, customer information, historical sales data, and planning parameters. It ensures consistency and accuracy in demand forecasts across different organizational units, improving forecast quality and planning efficiency. Additionally, it facilitates streamlined data integration and updates, reducing manual data entry errors.
84. What are the critical challenges in implementing SAP APO?
Ans:
- Complex data integration from various ERP systems.
- Ensuring data accuracy and consistency.
- Adapting to organizational processes.
- Training users on advanced planning functionalities.
- Additionally, managing change across the organization and aligning IT infrastructure to support APO’s requirements are critical.
85. What are the methods to ensure data consistency between SAP ECC and SAP APO?
Ans:
- Data consistency between SAP ECC (ERP Central Component) and SAP APO (Advanced Planning and Optimization) is crucial for effective supply chain management.
- This consistency is maintained through regular data replication and synchronization processes facilitated by CIF (Core Interface).
- CIF ensures that both master data (such as product, location, and customer details) and transactional data (like sales orders and production plans) relevant to planning in APO remain synchronized with ECC.
86. What are the key differences between SAP APO and SAP IBP (Integrated Business Planning)?
Ans:
SAP APO (Advanced Planner and Optimizer) is a robust on-premise solution renowned for its advanced planning capabilities. It encompasses modules such as Demand Planning (DP), Supply Network Planning (SNP), Production Planning and Detailed Scheduling (PP/DS), and Global Available-to-Promise (GATP). These modules enable organizations to optimize their supply chain processes, enhance production scheduling, and manage inventory effectively within their infrastructure.
87. How does SAP APO support real-time decision-making?
Ans:
SAP APO supports real-time decision-making through its Demand Planning (DP) and Supply Network Planning (SNP) modules. These modules provide real-time visibility into demand changes, supply constraints, and inventory positions. Advanced analytics and scenario planning capabilities enable quick response to disruptions, optimizing operational efficiency and customer service levels.
88. What are the future trends in SAP APO and supply chain planning?
Ans:
- Enhanced Predictive analytics integration with AI and machine learning.
- Increased use of IoT for real-time data capture.
- Adoption of digital twins for simulating supply chain scenarios.
- There’s also a shift towards more agile and responsive planning methodologies to cope with dynamic market conditions.
89. How does SAP APO handle supply chain disruption?
Ans:
SAP APO handles supply chain disruption through scenario planning, which allows companies to simulate various disruption scenarios and evaluate their impact on supply chain operations. It enables quick identification of alternate supply sources, rerouting of logistics, and adjustments to production schedules to mitigate disruptions and maintain continuity.
90. What strategies are used to improve supply chain visibility with SAP APO?
Ans:
SAP APO improves supply chain visibility by integrating data from various sources into a centralized platform. It provides real-time updates on inventory levels, demand forecasts, production schedules, and logistics movements. Enhanced visibility enables proactive decision-making, reduces lead times, optimizes inventory levels, and improves overall supply chain efficiency.