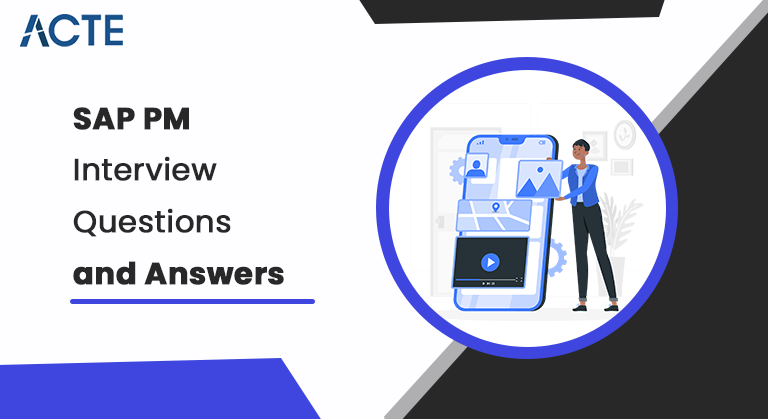
Our SAP PM interview questions generally focus on evaluating a candidate’s proficiency in SAP’s Plant Maintenance module. Areas of inquiry include expertise in equipment and functional location management, maintenance planning, work order processing, integration with other SAP modules, and a comprehensive understanding of SAP PM functionalities. Candidates might undergo assessment based on their experience in preventive and corrective maintenance, breakdown maintenance, and their proficiency in efficiently utilizing SAP PM’s user interface for effective asset management in an organizational context.
1. What is SAP PM (Plant Maintenance)?
Ans:
- Integrated Module: SAP PM is an integrated module within SAP ERP designed for managing plant maintenance activities.
- Holistic Solution: Encompasses various functions like equipment management, work orders, and preventive maintenance.
- Efficiency Enhancement: Streamlines maintenance workflows, reducing downtime and improving overall efficiency.
- Resource Management: Facilitates efficient allocation of resources, optimising maintenance processes.
- Compliance and Documentation: Ensures compliance with industry standards and enables thorough documentation of maintenance activities.
2. Explain the purpose of the SAP PM module.
Ans:
- Maintenance Management: Manages and optimises maintenance processes for machinery, equipment, and facilities.
- Downtime Reduction: Aims to minimise downtime through effective preventive maintenance strategies.
- Resource Optimization: Efficiently allocates resources, tracks costs, and enhances equipment reliability.
- Documentation: Facilitates detailed documentation of maintenance activities, ensuring compliance and transparency.
- Data Analysis: Provides data for analysing equipment performance, enabling informed decision-making.
3. Differentiate between preventive maintenance and corrective maintenance in SAP PM.
Ans:
Aspect | Preventive Maintenance | Corrective Maintenance | |
Objective |
Planned activities to prevent breakdowns |
Unplanned activities in response to failures | |
Timing | Scheduled at regular intervals | Reactive, initiated after equipment failure | |
Scope |
Targets potential issues before they occur |
Addresses issues as they arise | |
Goal | Minimise the risk of equipment Failures | Restore equipment to its normal operating state | |
Examples |
Regular inspections, lubrication, part replacements |
Equipment repairs, fixes, and emergency measures | |
Execution Control |
Proactive, planned in advance |
Reactive, triggered by incidents or malfunctions | |
Cost Implication | Generally lower cost due to planned nature | This can result in higher costs due to the unexpected nature |
4. Differentiate between preventive maintenance and corrective maintenance in SAP PM.
Ans:
- Equipment master data.
- Functional locations.
- Maintenance orders.
- Work centres.
- Maintenance task lists.
5. What is a maintenance order settlement rule in SAP PM?
Ans:
A maintenance order settlement rule in SAP PM determines how costs incurred during the execution of a maintenance order are allocated and settled. It outlines the distribution of costs among different cost centres, orders, or other relevant cost objects. By configuring settlement rules, organisations can accurately attribute labour, materials, and external services costs to specific areas within the SAP Controlling (CO) module. This ensures transparency and accuracy in tracking and analysing maintenance expenditures.
6. Explain the concept of a maintenance plant in SAP PM.
Ans:
Components of SAP PM:
- Equipment and Functional Locations: Represents physical assets and their locations.
- Maintenance Orders and Notifications: Records for planned and unplanned maintenance activities.
- Work Centers: Centralised hubs for managing resources and planning maintenance work.
- Task Lists: Structured lists defining maintenance tasks and procedures.
- Maintenance Plans: Schedules preventive maintenance activities.
- Measuring Points and Counters: Monitor and measure equipment performance.
7. What is a functional location in SAP PM?
Ans:
- Organisational Unit: Represents a physical area or site where maintenance activities are managed.
- Centralised Coordination: Acts as a central hub for maintenance planning, execution, and analysis.
- Resource Allocation: Helps in organising and allocating maintenance resources effectively.
- Data Segmentation: Allows for the segregation of maintenance activities based on plants.
8. How is maintenance strategy determined in SAP PM?
Ans:
The determination of maintenance strategy in SAP PM involves evaluating factors such as equipment criticality, reliability goals, and cost considerations. Organisations can choose from various maintenance strategies like time-based, performance-based, or condition-based, depending on the specific requirements. Equipment type, industry standards, and regulatory compliance influence the selection. Maintenance strategies guide the creation of preventive maintenance plans, balancing proactive and reactive maintenance to optimise equipment reliability and minimise downtime.
9. Define equipment in SAP PM.
Ans:
- Physical Assets: Represents machinery, tools, or any tangible item requiring maintenance.
- Unique Identification: Each piece of equipment has a unique identifier for tracking and management.
- Attributes: Contains details such as manufacturer, model, and maintenance history.
- Linked to Functional Locations: Can be associated with specific functional locations.
10. What is a maintenance task list, and how is it used in SAP PM?
Ans:
- Structured List: Defines a sequence of maintenance tasks to be performed.
- Details: Contains information such as task descriptions, resources required, and estimated times.
- Preventive Maintenance Planning: Used to plan and execute preventive maintenance activities.
- Standardisation: Promotes standardisation of maintenance procedures.
11. Explain the role of a work centre in SAP PM.
Ans:
- Resource Center: Provides a focal point for managing labour, tools, and equipment.
- Planning Efficiency: Enhances planning efficiency by coordinating required resources.
- Resource Allocation: Guarantees the availability of essential resources for maintenance tasks.
- Optimization: Contributes to overall maintenance optimization and effectiveness.
- Linked to Orders: Work centres are assigned to maintenance orders for task execution.
12. How do you create a maintenance order in SAP PM?
Ans:
- Access Transaction IW31: Use transaction code IW31 in SAP PM.
- Enter Order Details: Input order type, maintenance plant, equipment, and other relevant details.
- Define Operations: Specify tasks, materials, and resources required for the maintenance order.
- Assign Work Center: Allocate a work centre to ensure proper resource coordination.
- Save and Release: Save the order and release it to initiate the execution phase.
- Execution and Completion: Execute maintenance tasks, record actuals, and mark the order as completed.
13. What is the function of a control key in maintenance orders in SAP PM?
Ans:
The control key in SAP PM maintenance orders defines the overall behaviour and features associated with the order. It specifies whether an order is for planned maintenance, unplanned maintenance, or other specific types. The control key influences the order’s processing steps, status management, and workflow. By assigning a control key, organisations can customise the order’s attributes, ensuring it aligns with the intended maintenance scenario, whether it’s preventive, corrective, or other specific types of maintenance activities.
14. How do you configure a maintenance item category in SAP PM?
Ans:
- Access SAP PM Customising.
- Navigate to “Plant Maintenance” > “Maintenance and Service Orders” > “Functions and Settings for Order Types.”
- Define the maintenance item category with attributes like description and control data.
- Assign the item category to the relevant order type.
- Configure additional settings such as user statuses and field selection.
- Save the configuration, activating the new maintenance item category for use.
15. Explain the purpose of a task list selection in SAP PM.
Ans:
A task list selection in SAP PM allows users to choose specific task lists when creating or maintaining maintenance plans or maintenance items. This selection ensures that the tasks within the chosen list align with the maintenance requirements of the equipment or functional location. It provides flexibility by allowing organisations to tailor task lists based on factors such as equipment type, industry regulations, or specific maintenance scenarios. Task list selection contributes to the customization and precision of maintenance planning processes.
16. What is the use of a functional location category in SAP PM?
Ans:
A functional location category in SAP PM categorises functional locations based on specific criteria or characteristics. It helps organise and manage functional locations by grouping them according to their purpose, attributes, or usage. This categorization enhances the efficiency of maintenance management by offering a systematic strategy for handling different types of equipment or areas. Functional location categories contribute to standardised processes, facilitating consistent practices in maintenance planning, execution, and analysis.
17. How do you create a maintenance plan for a measuring point in SAP PM?
Ans:
- Access the SAP PM transaction.
- Navigate to the maintenance planning workbench.
- Create a new maintenance plan and select the measuring point as the equipment.
- Define the maintenance strategy, scheduling parameters, and frequency of tasks.
- Assign the plan to the relevant measuring point.
- Activate the plan to initiate the automatic scheduling of preventive maintenance tasks based on specified criteria related to the measuring point.
18. What is the significance of maintenance planning parameters in SAP PM?
Ans:
Maintenance planning parameters in SAP PM are crucial settings that influence how maintenance plans are created and executed. These parameters define criteria such as time-based or performance-based scheduling, planning horizon, and other conditions that impact the initiation of preventive maintenance tasks. By configuring these parameters, organisations can tailor maintenance planning to meet specific needs, ensuring timely and efficient execution of maintenance activities. Maintenance planning parameters contribute to the customization and optimization of maintenance strategies.
19. How can you perform mass changes to maintenance orders in SAP PM?
Ans:
To perform mass changes to maintenance orders in SAP PM, users can utilise the IW38 transaction. This transaction allows the display of a list of maintenance orders based on specific selection criteria. After selecting the orders that require modification, users can use the “Mass Processing” option to make changes in bulk. This could include updates to fields such as priority, status, or dates. Mass changes streamline the process of updating multiple orders simultaneously, saving time and improving efficiency in managing maintenance activities.
20. Explain the concept of a maintenance planning plant in SAP PM.
Ans:
A maintenance planning plant in SAP PM is a designated plant within the SAP system where maintenance planning activities are organised and managed. It serves as a central hub for coordinating maintenance strategies, plans, and resources related to specific equipment or functional locations. The maintenance planning plant allows organisations to group and organise maintenance tasks, facilitating streamlined planning, execution, and analysis. It enhances the efficiency of maintenance processes by providing a dedicated environment for comprehensive planning and coordination.
21. How do you create a maintenance work centre in SAP PM?
Ans:
To create a maintenance work centre in SAP PM:
- Access the SAP PM transaction.
- Navigate to “Plant Maintenance” > “Technical Objects” > “Work Centers.”
- Choose “Create” and enter the required details such as work centre category and location.
- Assign the work centre to relevant functional locations or equipment.
- Specify work centre capacity, shift data, and other parameters.
- Save the work centre, making it available for maintenance planning and execution.
22. What is the function of a maintenance planning group in SAP PM?
Ans:
In SAP PM, a maintenance planning group is a classification that groups technical objects (equipment or functional locations) based on maintenance planning criteria. This grouping aids in organising and streamlining maintenance planning activities. Maintenance planning groups can be assigned to work centres, ensuring that the proper maintenance tasks are assigned to the appropriate teams. This classification enhances the efficiency of maintenance processes by offering a systematic strategy for both preparation and implementation.
23. How can you configure a maintenance package in SAP PM?
Ans:
To configure a maintenance package in SAP PM, follow these steps:
- Access the SAP PM transaction.
- Navigate to “Maintenance Plans” or “Maintenance Orders.”
- Choose “Create Package” and define the package details, such as description and criteria.
- Assign relevant maintenance plans or orders to the package.
- Specify scheduling parameters and set package indicators.
- Save the configuration, creating a maintenance package for streamlined execution of grouped maintenance tasks.
24. What is the use of a maintenance plan called horizon in SAP PM?
Ans:
The maintenance plan call horizon in SAP PM defines the period during which the system automatically generates calls for maintenance plans. It represents the scheduling horizon within which the system considers the due dates for preventive maintenance tasks. By configuring the maintenance plan call horizon, organisations can control the frequency and timing of preventive maintenance calls, ensuring that tasks are initiated at the proper intervals. This parameter plays a crucial role in optimising maintenance schedules and minimising the risk of equipment failures.
25. Explain the concept of a maintenance order type in SAP PM.
Ans:
In SAP PM, a maintenance order type is a classification that defines the purpose and characteristics of a maintenance order. It specifies the nature of the maintenance activities, such as corrective, preventive, or inspection tasks. Each order type is associated with specific processing steps, workflow, and data requirements. By assigning a maintenance order type, organisations can customise the attributes of the order to align with the intended maintenance scenario, facilitating effective planning, execution, and analysis.
26. How do you configure maintenance cycles in SAP PM?
Ans:
To configure maintenance cycles in SAP PM:
- Access the SAP PM transaction.
- Navigate to “Maintenance Plans” or “Maintenance Orders.”
- Select “Create Cycle” and define the cycle details, including cycle start date and frequency.
- Assign relevant maintenance plans or orders to the cycle.
- Set cycle indicators and specify additional parameters.
- Save the configuration, creating a maintenance cycle for systematic scheduling and execution of grouped maintenance tasks.
27. What is the role of a Work Center in Maintenance Planning in SAP PM.
Ans:
In SAP PM, a work centre plays a pivotal role in maintenance planning by serving as a central hub for coordinating resources. It ensures efficient allocation of labour, tools, and equipment required for maintenance tasks. Work centres facilitate streamlined planning, allowing organisations to assign tasks to specific work centres based on their capabilities and expertise. This optimization enhances overall maintenance efficiency, improves scheduling accuracy, and contributes to effective resource management, ultimately ensuring that maintenance activities are carried out seamlessly.
28. How is Maintenance Plan Scheduling Performed in SAP PM?
Ans:
Maintenance plan scheduling in SAP PM is performed through the maintenance planning workbench. Users define maintenance plans specifying the tasks, frequencies, and associated equipment. The system then automatically schedules these plans based on time intervals, performance triggers, or other criteria. This ensures that preventive maintenance tasks are initiated at predetermined intervals, optimising equipment reliability and minimising downtime.
29. What is the Use of a Maintenance Planning Plant in SAP PM?
Ans:
A maintenance planning plant in SAP PM is a designated location where maintenance planning activities are organised and managed. It acts as a central hub for coordinating maintenance strategies, plans, and resources specific to equipment or functional locations within that plant. The maintenance planning plant enhances organisational efficiency by providing a dedicated environment for comprehensive planning and coordination, streamlining maintenance processes.
30. How Can You Customise the Maintenance Order Status Profile in SAP PM?
Ans:
To customise the maintenance order status profile in SAP PM, you navigate to Customising settings. In the SAP PM transaction, access “Plant Maintenance” > “Maintenance and Service Orders” > “Functions and Settings for Order Types.” Here, you can define and configure different status profiles, specifying the allowed status transitions, user statuses, and field selection based on your organisational requirements.
31. What is the use of a maintenance plan in SAP PM?
Ans:
- Defines a schedule for preventive maintenance tasks.
- Helps in systematic planning and execution of maintenance activities.
- Specifies intervals, resources, and tasks for equipment upkeep.
- Aids in reducing unplanned downtime and extending equipment life.
- Enables efficient resource allocation and cost control.
- Facilitates documentation and tracking of maintenance activities.
32. Differentiate between single cycle and multiple counter plans in SAP PM.
Ans:
- Single cycle plans are executed once based on time or performance.
- Multiple counter plans repeat tasks based on equipment usage or multiple counters.
- Single cycle plans are event-triggered, while multiple counter plans rely on counters.
- Multiple counter plans offer flexibility for complex maintenance scenarios.
- Single cycle plans are suitable for one-time or periodic tasks.
- Multiple counter plans cater to equipment with varied usage patterns.
33. How can you assign a maintenance task list to multiple pieces of equipment?
Ans:
- Use the “multiple equipment” option during task list creation.
- Assign the task list to a functional location or higher-level equipment.
- Utilise equipment categories for broader task list applicability.
- Link the task list to a maintenance plan covering multiple pieces of equipment.
- Ensure that the task list is generic and applicable to various equipment types.
- Implement a flexible and scalable task list structure.
34. Explain the concept of a task list hierarchy in SAP PM.
Ans:
- Task list hierarchy organises maintenance tasks in a structured manner.
- Consists of main task lists and sub-task lists with varying levels of detail.
- Facilitates a top-down approach to comprehensive maintenance planning.
- Main task lists represent overarching maintenance strategies.
- Sub-task lists break down strategies into specific actions for execution.
- Enhances clarity, efficiency, and flexibility in maintenance planning.
35. What is a maintenance item in SAP PM?
Ans:
- Maintenance item represents a specific task within a maintenance plan or task list.
- It defines a unit of work or activity that contributes to equipment upkeep.
- Examples include inspections, repairs, lubrication, etc.
- Each item is associated with resources, materials, and time requirements.
- Enables detailed planning and execution of maintenance activities.
- contributes to the maintenance plan’s overall efficacy plan.
36. How is equipment master data created in SAP PM?
Ans:
- Access the SAP PM module and navigate to the equipment master data section.
- Input essential information such as equipment type, description, and location.
- Specify technical details, such as manufacturer, model, and installation date.
- Assign the equipment to functional locations or higher-level equipment, if applicable.
- Update additional details like maintenance data and measurement points.
- Save and validate the entered information to create the equipment master data.
37. What is a maintenance notification, and how is it used in SAP PM?
Ans:
- A maintenance notification is an alert or report about equipment issues or failures.
- It serves as an initial record of a problem, triggering further investigation.
- Captures details like equipment affected, problem description, and priority.
- Acts as a basis for creating maintenance orders or triggering preventive actions.
- Facilitates communication and collaboration among maintenance teams.
- Essential for documenting and tracking issues throughout the maintenance process.
38. What is the difference between an internal and an external maintenance notification?
Ans:
- Internal notifications address issues within the organisation’s scope.
- External notifications involve problems affecting external parties or customers.
- Internal notifications focus on in-house equipment or facilities.
- External notifications pertain to customer equipment or services.
- The organisation’s maintenance team manages ø Internal notifications.
- External notifications may require communication and coordination with external stakeholders.
39. How do you release a maintenance order in SAP PM?
Ans:
- Navigate to the SAP PM module and access the maintenance order.
- Ensure that all required information, such as tasks and resources, is complete.
- Verify that necessary approvals and authorizations are obtained.
- Use the “Release” function in the maintenance order to make it actionable.
- Release triggers the execution phase, allowing planned tasks to commence.
- Released orders can be tracked, executed, and closed upon completion.
40. Explain the significance of a maintenance strategy in SAP PM.
Ans:
- A maintenance strategy outlines the overall approach to equipment upkeep.
- Defines the combination of maintenance types, plans, and frequencies.
- Aligns with the organisation’s goals, considering cost, reliability, and performance.
- Guides the creation of preventive maintenance plans for various equipment.
- Balances proactive and reactive maintenance activities.
- Enhances equipment reliability, reduces downtime, and optimises maintenance costs.
41. Explain the Concept of a Maintenance Plan Scheduling Horizon in SAP PM.
Ans:
The maintenance plan scheduling horizon in SAP PM defines the time frame during which the system generates calls for maintenance plans. It represents the scheduling period within which the system considers the due dates for preventive maintenance tasks. By configuring the maintenance plan scheduling horizon, organisations control the frequency and timing of preventive maintenance calls, ensuring that tasks are initiated within the desired time intervals. This parameter is crucial for optimising maintenance schedules and proactively addressing equipment maintenance needs.
42. How Do You Create a Maintenance Plan for a Piece of Equipment in SAP PM?
Ans:
To create a maintenance plan for a piece of equipment in SAP PM, you access the maintenance planning workbench. From there, you create a new maintenance plan, specifying details such as the equipment, maintenance strategy, scheduling parameters, and task frequencies. After assigning the plan to the relevant equipment, you activate it to initiate the automatic scheduling of preventive maintenance tasks based on defined criteria.
43. What is the Significance of a Maintenance Plan Package in SAP PM?
Ans:
A maintenance plan package in SAP PM bundles related maintenance plans, streamlining the execution of grouped tasks. It enhances coordination and resource allocation, facilitating efficient management of maintenance activities. By grouping plans into packages, organisations can optimise work efficiency, reduce downtime, and improve overall maintenance effectiveness.
44. How Do You Configure a Maintenance Task List Group in SAP PM?
Ans:
To configure a maintenance task list group in SAP PM, you access Customizing settings. In the SAP PM transaction, navigate to “Plant Maintenance” > “Maintenance and Service Orders” > “Maintenance Task Lists” > “Grouping Tasks” to define task list groups. This configuration allows for the systematic organisation and management of related maintenance tasks, ensuring consistency and efficiency in maintenance planning.
45. What is a Maintenance Strategy in SAP PM, and How is it Determined?
Ans:
A maintenance strategy in SAP PM outlines the overall approach to maintenance activities for specific equipment or functional locations. It is determined based on factors such as equipment criticality, reliability goals, and cost considerations. Organisations can choose from various maintenance strategies, including time-based, performance-based, or condition-based. The selection is influenced by equipment type, industry standards, and regulatory requirements, guiding the creation of preventive maintenance plans for optimised equipment reliability and minimising downtime.
46. Explain the Use of a Maintenance Planning Plant in SAP PM.
Ans:
The maintenance planning plant in SAP PM represents a specific location where maintenance planning activities are coordinated and managed within the SAP system. It allows organisations to group and organise maintenance tasks based on plant locations, facilitating streamlined planning, execution, and analysis. The maintenance planning plant enhances resource allocation, scheduling efficiency, and overall coordination, contributing to the effective management of maintenance processes.
47. How Can You Customise the Maintenance Order Type in SAP PM?
Ans:
Customising the maintenance order type in SAP PM involves accessing Customizing settings. Navigate to “Plant Maintenance” > “Maintenance and Service Orders” > “Functions and Settings for Order Types” in the SAP PM transaction. Here, you can define and configure maintenance order types, specifying attributes, allowed status transitions, and field selection based on your organisational needs.
48. What is the Function of a Maintenance Item Category Group in SAP PM?
Ans:
The maintenance item category group in SAP PM categorises maintenance item categories based on specific criteria or characteristics. It aids in organising and managing maintenance tasks by grouping them according to their attributes. This categorization enhances efficiency in maintenance planning and execution, ensuring consistency and systematic organisation of related maintenance items.
49. What is a breakdown maintenance scenario in SAP PM?
Ans:
- Represents an unplanned equipment failure.
- Triggers immediate maintenance action.
- A reactive approach to address urgent issues.
- Focuses on restoring equipment to regular operation.
- Often involves quick response and minimal planning.
- Captures downtime and repair details for analysis.
50. How can you link a maintenance plan to a measuring point in SAP PM?
Ans:
- Access the maintenance plan in SAP PM.
- Add or specify the relevant measuring point.
- Assign the measuring point to the plan’s task list.
- Linking allows for condition-based monitoring.
- Enables automatic triggering of maintenance tasks.
- Enhances precision in preventive maintenance.
51. What is the purpose of a maintenance work centre in SAP PM?
Ans:
- Represents a physical or organisational unit.
- Centralises resources for maintenance tasks.
- Coordinates labour, tools, and equipment.
- Facilitates efficient task execution.
- Enhances planning and scheduling.
- Essential for optimising maintenance processes.
52. How do you configure a catalogue profile in SAP PM?
Ans:
- Access the configuration menu in SAP PM.
- Choose “Catalogues” and define catalogue profiles.
- Specify attributes like code, description, etc.
- Configure settings for catalogue codes.
- Assign catalogue profiles to relevant objects.
- Provides a standardised structure for data.
53. Explain the concept of a measuring point in SAP PM.
Ans:
- Represents a location where readings are taken.
- Monitors equipment conditions and performance.
- Includes physical points like gauges or sensors.
- Captures data for preventive maintenance.
- Linked to maintenance plans for automation.
- Critical for condition-based maintenance strategies.
54. What is the maintenance history of SAP PM, and how is it maintained?
Ans:
- Records historical data of maintenance activities.
- Includes details like dates, tasks, and resources.
- Captures breakdowns, repairs, and preventive actions.
- Helps in analysing equipment performance.
- Maintained through documentation and system updates.
- Essential for decision-making and future planning.
55. How Do You Perform a Time-Based Maintenance Plan in SAP PM?
Ans:
To perform a time-based maintenance plan in SAP PM, you create a new maintenance plan in the maintenance planning workbench. Select the time-based scheduling option and define the maintenance strategy, scheduling parameters, and task frequencies. Assign the plan to the relevant equipment or functional location and activate it. The system will then automatically schedule preventive maintenance tasks based on the specified time intervals.
56. What is a Maintenance Item Category in SAP PM, and How is it Used?
Ans:
A maintenance item category in SAP PM classifies specific maintenance tasks within a maintenance plan. It defines attributes such as description, control data, and associated resources. Maintenance item categories enable detailed planning and tracking of individual maintenance tasks, facilitating systematic execution and analysis within the overall maintenance plan.
57. Explain the Concept of a Maintenance Order Operation in SAP PM.
Ans:
In SAP PM, a maintenance order operation represents a specific task or activity within a maintenance order. Each operation has attributes such as work centre, duration, and required materials. Operations are used to break down and structure the work to be performed, providing a detailed overview of the tasks involved in executing a maintenance order.
58. How Do You Create a Maintenance Plan for Multiple Pieces of Equipment in SAP PM?
Ans:
To create a maintenance plan for multiple pieces of equipment in SAP PM, you access the maintenance planning workbench. Choose the “Multiple Equipment” option and specify the relevant equipment. Define the maintenance strategy, scheduling parameters, and task frequencies. Assign the plan to the selected equipment and activate it, allowing the system to automatically schedule routine upkeep duties for every piece of machinery within the plan.
59. What is the Use of a Maintenance Order Operation in SAP PM?
Ans:
A maintenance order operation in SAP PM represents a specific task or activity within a maintenance order. It provides detailed information such as the work centre, duration, and required materials for executing that task. Operations help structure the work to be performed, allowing for a systematic breakdown of maintenance activities and facilitating effective resource planning and execution.
60. How Do You Configure a Maintenance Task List for Equipment in SAP PM?
Ans:
To configure a maintenance task list for equipment in SAP PM, navigate to “Plant Maintenance” > “Maintenance and Service Orders” > “Maintenance Task Lists.” Define the task list, specifying tasks, resources, and required materials. Assign the task list to the relevant equipment, allowing for the systematic execution of maintenance tasks based on the defined list.
61. What is a Maintenance Plan Package, and How is it Used in SAP PM?
Ans:
A maintenance plan package in SAP PM is a grouping of related maintenance plans for streamlined execution. It allows organisations to optimise resource allocation and enhance coordination by bundling maintenance plans that share common characteristics. Maintenance plan packages contribute to the efficient management of maintenance activities, reducing downtime and improving overall maintenance effectiveness.
62. Describe the process of creating a maintenance task list in SAP PM.
Ans:
- Access the task list creation screen in SAP PM.
- Define task list details, such as description and type.
- Specify operations, materials, and resources.
- Set task list indicators and control parameters.
- Assign the task list to relevant equipment or functional locations.
- Save and activate the task list for use.
63. How do you assign a material to a maintenance order in SAP PM?
Ans:
- Open the maintenance order in SAP PM.
- Navigate to the material assignment section.
- Enter the material code, quantity, and other details.
- Check availability and confirm the assignment.
- Materials are then consumed during maintenance execution.
- Ensures proper tracking of material usage.
64. What is the SAP PM order type and its significance?
Ans:
- Order type categorises maintenance tasks.
- Significance lies in task classification.
- Different types suit various maintenance scenarios.
- Determines workflows, fields, and data structures.
- Aids in standardising and streamlining processes.
- Enhances clarity and efficiency in order execution.
65. Explain the difference between a maintenance plan and a maintenance order.
Ans:
- Maintenance plan is for preventive task scheduling.
- Maintenance order is for specific maintenance tasks.
- Plan is proactive; order is reactive.
- Plan outlines tasks in advance.
- Order triggered by a specific event.
- Both contribute to overall equipment upkeep.
66. How can you schedule maintenance plans in SAP PM?
Ans:
- Access the maintenance plan in SAP PM.
- Define scheduling parameters like start date, cycle, and frequency.
- Set the scheduling type (time-based or performance-based).
- Assign the plan to relevant equipment or functional locations.
- Save and activate the plan for automatic triggering.
- Ensures systematic execution of preventive tasks.
67. What is the use of a maintenance cycle in SAP PM?
Ans:
- Maintenance cycle groups similar plans for efficient execution.
- Defines intervals for plan triggering.
- Enhances coordination of related tasks.
- Streamlines planning and resource allocation.
- Ensures cohesive maintenance activities.
- Critical for optimising preventive strategies.
68. How do you create a functional location hierarchy in SAP PM?
Ans:
- Access the SAP PM functional location master data.
- Choose the “Create Hierarchy” option.
- Define hierarchy levels and relationships.
- Assign functional locations to respective hierarchy levels.
- Save and validate the functional location hierarchy.
- Facilitates organised structure for maintenance planning.
69. Explain the Concept of a Maintenance Planning Plant in SAP PM.
Ans:
A maintenance planning plant in SAP PM is a designated plant within the SAP system where maintenance planning activities are organised and managed. It acts as a central hub for coordinating maintenance strategies, plans, and resources specific to equipment or functional locations within that plant. The maintenance planning plant enhances organisational efficiency by providing a dedicated environment for comprehensive planning and coordination, streamlining maintenance processes.
70. How to Perform Breakdown Maintenance Scenario in SAP PM.
Ans:
To address a breakdown maintenance scenario in SAP PM, the process typically involves creating a reactive maintenance order triggered by an unplanned equipment failure. Users would log the breakdown, generate a maintenance notification, and then convert it into a maintenance order. Work centres and necessary resources are assigned to address the issue promptly. The maintenance team executes corrective actions and records the time and materials used to complete the order. This scenario prioritises quick response to restore equipment functionality, minimising downtime.
71. What is the Significance of a Maintenance Work Center in SAP PM.
Ans:
A maintenance work centre in SAP PM is significant as it serves as a centralised hub for organising and managing resources required for maintenance activities. It facilitates the coordination of labour, tools, and equipment, ensuring efficient execution of maintenance orders. Work centres play a vital role in planning and scheduling, improving overall work efficiency, and enhancing the effectiveness of maintenance processes.
72. How to Create a Maintenance Plan for a Functional Location in SAP PM.
Ans:
To create a maintenance plan for a functional location in SAP PM:
- Access the maintenance planning workbench.
- Choose the functional location, define the maintenance strategy, set scheduling parameters, and specify task frequencies.
- Assign the plan to the functional location and activate it to initiate automatic scheduling.
This ensures preventive maintenance tasks are planned and executed systematically for the specified functional location.
73. Explain the Role of a Maintenance Item in SAP PM.
Ans:
In SAP PM, a maintenance item represents a specific task or activity within a maintenance plan. It defines details such as the description, control data, and assigned resources for individual tasks. Maintenance items allow for a granular breakdown of maintenance plans, facilitating detailed planning, execution, and tracking of specific maintenance activities.
74. How to Configure a Maintenance Plan for a Measuring Point in SAP PM.
Ans:
To configure a maintenance plan for a measuring point in SAP PM:
- Access the maintenance planning workbench.
- Create a new maintenance plan, select the measuring point as the equipment, define the maintenance strategy, set scheduling parameters, and assign tasks.
- Activate the plan to initiate the automatic scheduling of preventive maintenance tasks based on specified criteria related to the measuring point.
75. Explain the Concept of the Maintenance Plan Scheduling Parameter in SAP PM.
Ans:
Maintenance plan scheduling parameters in SAP PM define criteria for initiating preventive maintenance tasks. These parameters include time-based scheduling, performance-based triggers, and other conditions influencing the timing of maintenance calls. Configuring these parameters ensures that preventive tasks are scheduled appropriately, optimising equipment reliability and minimising downtime.
76. What is the purpose of a work centre category in SAP PM?
Ans:
- Work centre category classifies maintenance work centres.
- Indicates the type of work performed at the centre.
- Examples include mechanical, electrical, or assembly.
- Helps in resource categorization and allocation.
- Streamlines work centre selection during planning.
- Enhances efficiency in maintenance processes.
77. Explain the role of the task list type in SAP PM.
Ans:
- Task list type categorises maintenance tasks.
- Defines the structure and purpose of the task list.
- Examples include general maintenance, inspection, or overhaul.
- Determines the required data and parameters.
- Enhances consistency and standardisation.
- Ensures clarity and accuracy in task list creation.
78. What are the different status codes in SAP PM maintenance orders?
Ans:
- Created: Order is generated but not yet released.
- Released: Ready for execution.
- Confirmed: Tasks within the order are completed.
- Technically Completed: All technical activities finished.
- Closed: Entire order is completed and closed.
- Cancelled: Order is terminated before completion.
79. How do you settle costs in SAP PM maintenance orders?
Ans:
- Use settlement rules to allocate costs.
- Access the settlement transaction in SAP PM.
- Confirm the relevant costs and quantities.
- Choose the settlement profile and cost elements.
- Execute the settlement process.
- Transfers costs to relevant cost centres or orders.
80. What is the purpose of a maintenance business partner in SAP PM?
Ans:
- Represents external entities involved in maintenance.
- Includes vendors, contractors, or service providers.
- Facilitates collaboration and communication.
- Linked to maintenance orders or notifications.
- Enables tracking of external contributions.
- Enhances transparency in maintenance processes.
81. How do you create a maintenance task list for a functional location in SAP PM?
Ans:
- Access the functional location master data in SAP PM.
- Navigate to the task list assignment section.
- Choose “Create Task List” and specify details.
- Define operations, materials, and resources.
- Save and assign the task list to the functional location.
- Enables systematic planning for specific locations.
82. What is the significance of a maintenance work centre in SAP PM?
Ans:
- Centralises resources for maintenance tasks.
- Coordinates labour, tools, and equipment.
- Enhances planning and scheduling efficiency.
- Represents a dedicated unit for specific activities.
- Streamlines task execution and monitoring.
- Integral for optimising overall maintenance processes.
83. Explain the Concept of Maintenance Order Settlement in SAP PM.
Ans:
Maintenance order settlement in SAP PM is the process of distributing and allocating costs incurred during the execution of a maintenance order. It defines how costs, including labour, materials, and external services, are settled to specific cost centres or orders within the SAP Controlling (CO) module. Maintenance order settlement ensures accurate tracking and attribution of costs, providing transparency in financial analysis and reporting.
84. How to Create a Maintenance Plan for a Task List in SAP PM.
Ans:
To create a maintenance plan for a task list in SAP PM:
- Access the maintenance planning workbench.
- Choose the task list, define the maintenance strategy, set scheduling parameters, and assign tasks.
- Activate the plan to initiate the automatic scheduling of preventive maintenance tasks based on the specified task list.
This approach allows organisations to plan and execute maintenance activities systematically, following predefined task sequences.
85. Explain the Uses of a Maintenance Plan Call Horizon in SAP PM.
Ans:
The maintenance plan call horizon in SAP PM establishes the period during which the system generates calls for maintenance plans. It defines the scheduling horizon within which the system considers due dates for preventive maintenance tasks. Configuring the maintenance plan call horizon ensures that maintenance tasks are initiated at appropriate intervals, optimising the balance between proactive maintenance and equipment availability.
86. How to Configure a Maintenance Item Category in SAP PM.
Ans:
To configure a maintenance item category in SAP PM:
- Access Customising settings.
- Navigate to “Plant Maintenance” > “Maintenance and Service Orders” > “Functions and Settings for Order Types.”
- Define the maintenance item category with attributes like description and control data.
- Assign the item category to the relevant order type and configure additional settings, such as user statuses and field selection.
- Save the configuration, ensuring the new maintenance item category is activated for use.
Configuring item categories allows for customization and standardisation of maintenance order processing.
87. Explain the Integration of SAP PM with Other SAP Modules.
Ans:
MM (Materials Management):
- Shares data on materials, spare parts, and procurement for maintenance.
- Allows seamless integration of procurement processes with maintenance activities.
SD (Sales and Distribution):
- Links customer service requests to maintenance notifications.
- Facilitates coordination between sales orders and service-related maintenance.
CO (Controlling):
- Integrates with cost accounting for accurate tracking of maintenance costs.
- Provides real-time cost information for analysis and decision-making.
PP (Production Planning):
- Aligns production schedules with maintenance plans to optimise resource utilisation.
- Ensures minimal disruption by coordinating maintenance with production cycles.
QM (Quality Management):
- Integrates quality inspections into maintenance processes.
- Enables seamless coordination between quality checks and equipment maintenance.
WM (Warehouse Management):
- Manages spare parts inventory and aligns with maintenance needs.
- Facilitates efficient tracking and retrieval of materials for maintenance tasks.
88. How do you configure a breakdown maintenance scenario in SAP PM?
Ans:
- Define breakdown maintenance order types.
- Configure notification types for breakdowns.
- Set up priorities for rapid response.
- Assign necessary authorization roles.
- Define codes for breakdown causes.
- Establish workflow for a quick resolution.
89. What is the use of a maintenance package in SAP PM?
Ans:
- Bundles maintenance orders for efficient execution.
- Groups related tasks, reducing downtime.
- Enhances coordination and resource allocation.
- Streamlines work for specific equipment or areas.
- Enables unified tracking and reporting.
- Improves overall maintenance efficiency.
90. How is equipment history maintained in SAP PM?
Ans:
- Records all maintenance-related activities.
- Captures breakdowns, repairs, and preventive actions.
- Documents changes in equipment status or configuration.
- Provides a comprehensive historical view.
- Essential for performance analysis and decision-making.
- Accessible through the equipment master data.
91. What is a maintenance plan package in SAP PM?
Ans:
- Group maintenance plans for specific scenarios.
- Defines a set of plans applicable to a package.
- Enhances systematic planning for similar equipment.
- Streamlines the creation and management of multiple plans.
- Facilitates efficient scheduling and resource allocation.
- Promotes consistency in maintenance strategies.
92. How do you perform preventive maintenance scheduling in SAP PM?
Ans:
- Define maintenance plans with task lists.
- Set intervals for time-based or performance-based triggers.
- Assign plans to equipment or functional locations.
- Activate plans for automatic scheduling.
- Utilise scheduling parameters for flexibility.
- Ensures timely execution of preventive tasks.
93. Explain the concept of a maintenance scheduling parameter in SAP PM.
Ans:
- Defines the criteria for scheduling preventive tasks.
- Includes factors like time intervals, performance thresholds, or usage counts.
- Influences when maintenance plans are triggered.
- Offers flexibility in adapting to diverse equipment needs.
- Critical for aligning preventive measures with equipment conditions.
- Enhances customization and optimization of scheduling.
94. What is a task list group in SAP PM, and how is it used?
Ans:
- Groups task lists with similar characteristics.
- Defines common attributes for related tasks.
- Enhances consistency in maintenance planning.
- Simplifies assignment to equipment or functional locations.
- Streamlines management and updates of grouped tasks.
- Facilitates systematic and organised task list handling.
95. How do you create a maintenance item for a piece of equipment in SAP PM?
Ans:
- Access the equipment master data in SAP PM.
- Navigate to the maintenance tab and select “Create Maintenance Item.”
- Define the maintenance task details, such as description and type.
- Specify associated resources, materials, and time requirements.
- Save the maintenance item to link it with the equipment.
- Allows detailed planning and tracking of specific maintenance tasks.
96. What is the significance of a maintenance planning plant in SAP PM?
Ans:
- Represents a location for centralised maintenance planning.
- Allows grouping of equipment and tasks based on plant locations.
- Enhances organisation and coordination of maintenance activities.
- Streamlines resource allocation and scheduling within a plant.
- Facilitates efficient planning and execution of maintenance plans.
- Improves overall maintenance management and control.
97. How can you perform maintenance cost analysis in SAP PM?
Ans:
To perform maintenance cost analysis in SAP PM, organisations can utilise the system’s reporting and analytical tools to extract and analyse cost-related data from maintenance orders, notifications, and other relevant sources. By running cost reports, users can gain insights into labour, materials, and external service costs associated with maintenance activities. Integration with SAP Controlling (CO) ensures accurate cost tracking and allocation to specific cost centres or orders. This facilitates informed decision-making for optimising maintenance costs and improving resource utilisation.
98. What is the use of a work centre in maintenance orders in SAP PM?
Ans:
In SAP PM, a work centre is crucial for coordinating resources in maintenance orders. It serves as a central point for managing labour, tools, and equipment needed for executing maintenance tasks efficiently. By assigning work centres to maintenance orders, organisations streamline planning and ensure that the necessary resources are available when needed. This optimization enhances work efficiency, improves scheduling accuracy, and contributes to overall maintenance effectiveness.
99. Explain the purpose of a maintenance plan category in SAP PM.
Ans:
A maintenance plan category in SAP PM is designed to categorise maintenance plans based on specific criteria or characteristics. This categorization aids in organising and managing maintenance strategies, allowing organisations to group similar plans. Maintenance plan categories contribute to standardisation, making it easier to differentiate between various types of plans, such as time-based, performance-based, or condition-based. This classification ensures consistent application of maintenance strategies across equipment and functional locations.
100. How do you configure time-based maintenance plans in SAP PM?
Ans:
Configuring time-based maintenance plans in SAP PM involves several steps:
- Access the SAP PM transaction.
- Navigate to the maintenance planning workbench.
- Create a new maintenance plan and select the time-based scheduling option.
- Define the maintenance strategy, scheduling parameters, and frequency of tasks.
- Assign the plan to relevant equipment or functional locations.
- Activate the plan to initiate the automatic scheduling of preventive maintenance tasks based on specified time intervals.