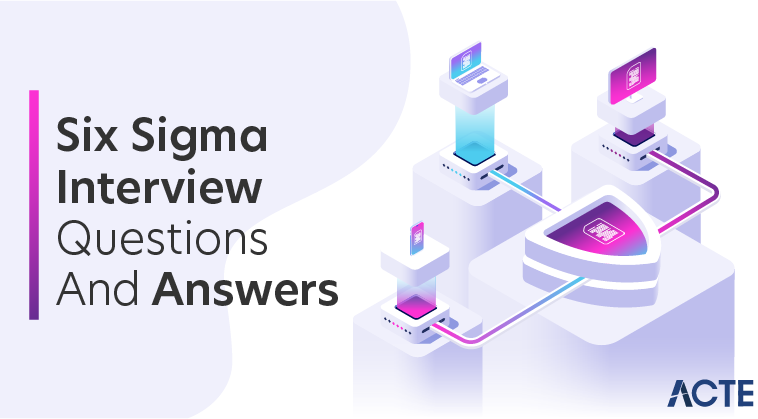
Six Sigma is a strategic methodology used to improve business processes by reducing defects and variations. It employs a structured problem-solving approach known as DMAIC (Define, Measure, Analyze, Improve, Control) to identify and rectify issues within existing processes. Emphasizing statistical analysis and tools, Six Sigma aims to achieve high levels of quality by minimizing errors, typically targeting fewer than 3.4 defects per million opportunities. It places a strong focus on understanding and meeting customer requirements, aligning processes to ensure products or services meet or exceed customer expectations. The methodology often involves specific roles and certifications like Champions, Black Belts, Green Belts, and Yellow Belts, each trained to different levels of expertise. Continuous improvement is central to Six Sigma, where optimized processes are continuously refined to sustain efficiency, reduce waste, improve quality, and enhance overall customer satisfaction.
1. What does Six Sigma?
Ans:
Six Sigma is the set of techniques and tools for improving a quality of processes. This data-driven and disciplined methodology can be used in the any process, from manufacturing to transactional and from a product to service. Six Sigma approaches are merged with the concept of process control, maximized productivity, and reduced waste.2. What does critical principles of Six Sigma?
Ans:
- Process improvement
- Formulate a flexibility in processes
- Effectively managing the cross-functional teams
3. What does COPQ in Six Sigma?
Ans:
- cost of lost opportunity
- Labor cost
- Rework cost
- Disposition costs
4. What does definition of DPMO or DPPM?
Ans:
Defects Per Million Opportunities is referred to as DPMO, and Defective Parts Per Million as DPPM.Here defects are inclusive of flaws or discrepancies on an item.5. What does Pareto Principle?
Ans:
The Pareto principle states that, for the many events, roughly 80% of results from 20% of the causes. However, people’s misconception is 20 + 80 = 100 — however it’s not always accurate because most things are be not 1/1.- data = [30, 15, 25, 10, 20]
- data.sort(reverse=True)
- top_20_percent = data[:len(data)//5]
- print(f”Top 20% contributors: {top_20_percent}\nPercentage they represent in the list: {sum(top_20_percent)/sum(data) * 100:.2f}%”)
6. Mention some of the Quality Management tools in Six Sigma.
Ans:
- CTQ Tree
- SIPOC analysis
- COPIS analysis
7. What does various kinds of variations used in the Six Sigma?
Ans:
Mean, Median, Range and Mode8. Who makes up the Six Sigma implementation team?
Ans:
Six Sigma Deployment Leader, Six Sigma Champion, Six Sigma Master Black Belt (MBB), Six Sigma Black Belt (BB)9. What does difference between Six Sigma DMAIC and DMADV methodologies?
Ans:
Aspect | DMAIC Methodology | DMADV Methodology | |
Purpose |
Primarily used for improving existing processes, identifying and rectifying issues within them. |
Employed for creating new processes or products with minimal defects from the outset. | |
Acronym Expansion | Define, Measure, Analyze, Improve, Control | Define, Measure, Analyze, Design, Verify | |
Objective | Reducing defects, minimizing errors, and improving efficiency within existing processes. | Developing new processes/products to meet or exceed customer expectations and minimize errors from the start. |
10. Explain fishbone/ Ishikawa diagram?
Ans:
A fishbone diagram, also referred to as an Ishikawa diagram is a type of diagram used to look into the underlying causes of issues. It gets its name from its a fishbone-like shape, where the problem is depicted as “head” of the fish, and causes are represented as the “bones” branching off the spine of fish.
11. What does Lean Six Sigma Yellow Belt?
Ans:
An organization can have more Yellow Belts. These individuals are the team members on a Lean Six Sigma project led by Green Belt or Black Belt. They should be familiar with structured methodology and the use of the cross-functional tools and techniques.
12. What does Features of Six sigma?
Ans:
- Six Sigma provides the sequential methodology and defines positions for respondents.
- Six Sigma is the data-driven methodology and involves high – quality data for mechanisms being evaluated.
- Six Sigma is about achieving success to a Financial Statements.
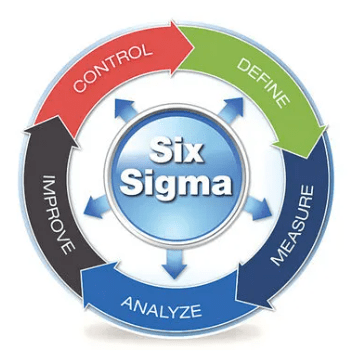
13. What does difference between Cpk and Ppk?
Ans:
Cpk is process capability index, which measures how close process is running to its specification limits, relative to natural variability of the process, and Ppk is process performance index, which verifies if sample that has been generated from a process is capable of meeting Customer CTQs (requirements)14. Explain standard deviation?
Ans:
Standard deviation is the statistical measure that quantifies a amount of variation or dispersion in the set of values. It provides the way to express how spread out the individual values in data set are, indicating the extent to which these values deviate from mean (average) of the data set.15. What does process of sigma calculation?
Ans:
Calculating sigma (σ) involves the determining the standard deviation of set of data points. Sigma, in statistical terms, represents level of variation or dispersion within a set of values. A higher sigma value indicates the lower variability, which is often desirable in different processes, especially in the manufacturing and quality control.16. What does 1.5 sigma shift?
Ans:
Statistical process control, a “1.5 sigma shift” refers to adjustment made to the process mean (average) when calculating the process capability. This shift is applied to account for a long-term process behavior and to ensure that process is stable and meets quality requirements consistently over time.
17. What does Regression? When is it used?
Ans:
Regression Analysis is the technique used to define the relationship between an output variable and the set of input variables. There are several types of a regression like Simple Linear Regression, Multiple Linear Regression, Logit Regression, Probit Regression,Curvilinear Regression18. What does difference between defect and defective?
Ans:
A defect is any non-conformance of the unit of product with specified requirements. A defective is the unit of work that contains one or more flaws.
In general, a product may have defect but can still be functional. A defective product is considered an objectionable and cannot function.
19. Explain The Quality Levels Of Six Sigma ?
Ans:
Process Report is used with the continuous data that follow bell curve distribution, while Product Report applies to a discrete data and therefore, can be used for all types of the distributions.20. Explain FMEA
Ans:
FMEA stands for the Failure Mode and Effects Analysis. It is the systematic and proactive approach to identify and evaluate a potential failures and their effects on the system, product, or process.21. What does X bar and R charts?
Ans:
They are the set of two charts, which is most commonly used statistical process control procedure used to monitor the process behavior and outcome over time. X-bar (X̄) and R Charts are tools used in the statistical process control to monitor and analyze variation in a process.22. Explain flowcharting and brainstorming.
Ans:
A flowchart is the diagram displaying the sequential steps of an event, process, or workflow. Brainstorming is the technique used to quickly generate creative or original ideas on or about the procedure, problem, product, or service.23. What does different quality levels of Six Sigma?
Ans:
Six Sigma quality level is the methodology to measure the quality of a process. Each sigma level corresponds to several acceptable defects per million, and the optimum sigma level is achieved when a process accuracy goes to 3.4 defects per million opportunities.24. What does SIPOC?
Ans:
SIPOC is acronym for the Suppliers, Inputs, Process, Outputs, and Customers. It is the tool that uses information from these five-segments and creates a process map, providing a high-level overview of Six Sigma project.25. What does MAIC in Six Sigma?
Ans:
MAIC denotes:
Measure – Accounts for the quantifying and benchmarking any process using the actual data
Analyze – Includes using the statistical tools to identify a root cause of any problem
Improve – Focus on solving root cause of problem
Control – Involves keeping the checks on issues to avoid reoccurrence and sustain the gains.
26. What does DFSS in a Six Sigma process?
Ans:
DFSS is an acronym for Define for Six Sigma. It is the process improvement system that involves designing or redesigning the service or a product as per Six Sigma quality standards.27. Explain ARMI or RASI.
Ans:
Mainly 4 variations are used in six sigma process:ARMI is an abbreviation for an Approver, Resource, Member, and Interested Party. It is the project management tool to identify a person involved in the project and its vital responsibility areas.
28. What does data collection plan?
Ans:
A data collection plan is used to collect all critical data in a system. It covers –
- Type of data that needs to be collected or be gathered
- Different data sources for analyzing the data set
29. What is MSA?
Ans:
MSA is the Measurement System Analysis. MSA is used to check if measurement system is accurate. It evaluates the system’s accuracy, precision, and stability.30. What does Top-down approach in Six Sigma?
Ans:
It is the process in Six Sigma implementation, which aligns with business strategy and consumer requirements, and paves the way for shared understanding and vocabulary. On other hand, the major disadvantage of this process is that it has extensive scope, thus it is complex to be executed within stipulated time.31. What does VSM?
Ans:
It stands for Value Stream Mapping. Using this methodology, wastes in a process can be eliminated, and the information flow needed to deliver a product or service can be mapped.32. What does affinity diagram?
Ans:
An Affinity Diagram is the analytical tool used to cluster or organize ideas into the subgroups. These ideas are mostly generated from the discussions or brainstorming sessions and used in an analyzing the complex issues.33. Explain difference between the Histogram and a Boxplot.
Ans:
A histogram graphical represents the frequency distribution of a numeric data, while the Box Plot summarizes an essential aspects of continuous data distribution.34. What does primary and secondary metrics in a Six Sigma project?
Ans:
Both primary and secondary metrics are success indicators of Six Sigma project. Primary metrics measure a processes aligned to business goal. The measurable processes can be a time taken to complete a project and/or defects in processes, among others.On other hand, secondary metrics are indirectly aligned to the business objective.
35. Why does metrics important to consider in a Six Sigma project?
Ans:
Metrics are useful in the driving performance and future decision-making. They are essential to make a processes effective and objective. For Six Sigma project’s success, one can implement metrics using SMART model.36. What does performance testing in Six Sigma? How does different from load testing?
Ans:
A performance test evaluates the system’s dependability and responsiveness under increased workload. Performance testing includes load testing, though it can also be done independently. To put it another way, load testing assesses a system’s capability for operation, whereas performance testing ascertains whether the system is operating correctly.37. Describe the significance of the Six Sigma project’s RACI matrix.
Ans:
The RACI matrix within a Six Sigma project holds significant importance by explicitly defining the roles and responsibilities of team members. Through its categorization of Responsible, Accountable, Consulted, and Informed roles, it provides clarity, preventing confusion and duplications, fostering accountability, and improving communication.38. Explain Nominal Group Technique.
Ans:
The Nominal Group Technique (NGT) is the structured method used to generate and prioritize ideas or solutions within the group setting. It encourages active participation from all the group members and ensures that every member’s input is considered.39. What does Statistical Process Control?
Ans:
Statistical Process Control (SPC) is the method of quality control that uses the statistical methods to monitor and control process to ensure it operates efficiently and produces the high-quality products or services. SPC is commonly used in the manufacturing, but it can be applied to any process where output can be measured.40. What does TRIZ stand for? Why should use it?
Ans:
TRIZ is the acronym for a Theory of Inventive Problem Solving. It looks at a specific problems to identify certain patterns that are the recurrent across other industries for possible solution.41. What does scatter plot diagram in Six Sigma?
Ans:
A scatter plot is the graphical diagram representing two different variables. When two variables are independent, they typically lie on a horizontal and a vertical axis, respectively. It is simpler and quicker to find a positive or negative correlation between disparate variables.42. How does interpret a scatter plot diagram?
Ans:
When the data in X-Y plane moves upwards from a left to right, it is a positive correlation. Conversely, if data moves downwards it is negative correlation.43. What does different levels available in Six sigma?
Ans:
Six sigma is nothing but the process improvement methodology where the root cause of an errors is identified and ultimately helps in improving overall process. So when it comes to a Six Sigma level, one has to check with DPMO score.44. What is MSA?
Ans:
Six Sigma involves managing common cause (inherent) and special cause (unexpected) variations to reduce defects. Tolerable variation helps identify acceptable limits within a process, while total variation encompasses the overall variability. The focus is on minimizing both common and special cause variations to enhance process stability and quality.45. Who is in charge of assembling the Six Sigma implementation team within an organisation?
Ans:
- Executive management, leaders are responsible for making decisions Champions
- Master Black belts
- Black belts
- Green Belts
46. What does executive leaders or executive management in terms of implementing six sigma team?
Ans:
These are individuals who will be responsible for driving initiatives to make sure product quality and processes are optimized to the profitable level where the entire team is being productive with the fewer operations costs incurred.47. What does Master black belt in terms of implementing six sigma team?
Ans:
The primary function of a Master black belt holder of a six sigma process is critical for an organization because the majority of organizations do not begin with the concrete six sigma process.48. What does difference between load test and performance testing?
Ans:
Load Testing: Load testing is nothing but the testing process where the load limit is beyond what client has required. This would help us understand whether application can handle the certain limit.
Performance Testing: Performance testing is all about having a more stress on the system checks and also overall application and system performance during stress conditions. In a sense, performance testing is nothing but the superset of a load test.
49. What does benefits of the six sigma process to organization and for individual practicing it
Ans:
- Works towards betterment of Quality Assurance.
- Helps individuals to build skills and turn them into the leaders.
- Have attractive salaries for an individuals having this skill.
50. What does popular myths or misunderstandings about the Six Sigma process?
Ans:
- The Six Sigma process is defined only for a reducing defects.
- Six Sigma is merely training with no real-world application.
- The Six Sigma process cannot be applied to the engineering activities.
- Customers
- Process
- Employees
- Fishbone Diagram
- Process Mapping
- Control Charts
- Pareto Chart
- Providing a strong leadership by actively promoting and supporting a Six Sigma initiatives.
- Ensuring that projects and goals are aligned with organisation’s overall strategic objectives.
- Allocating the necessary resources, including the budgets, personnel, and tools.
- Control Charts
- Pareto Chart
- Histogram
- Plot a data points over time.
- Establish a control limits.
- Monitor for a data points falling outside the control limits.
- Lean Six Sigma Green Belt
- Lean six sigma black belt
- Lean six sigma master black belt
- Reduces operational cost
- Optimizes a process as per the need of the time
- Reduces cost
- Data Analysis
- Decision Delay
- Creative Solutions
- Complex, Unique Problems
51. What does three key elements for six sigma process improvement?
Ans:
52. Explain FEMA?
Ans:
The Final Segment of Measure Phase is referred to as FEMA. In other words, it essentially advances the cause of stopping defects before they even arise. Thus, it makes sense to be proactive and ensure that a process is free of known flaws.
53. What does three steps for Root cause analysis?
Ans:
Open step: In this first stage, the entire team gets together to brainstorm through all of the potential outcomes.
Narrow step: In this stage, every scenario and explanation is narrowed down to some extent based on our current sigma performance.
Close step: The project team will verify each explanation on the reduced list for the current sigma performance during this phase.
54. Explain Pareto principle?
Ans:
The tool of a Pareto chart, which is used to display data, is based on the Pareto principle. It’s known as the 80/20 rule.Using this rule will help team to focus on a specific tasks and issues which might have greater impact if they are not looked into at initial stages.
55. How does cost of six sigma implementation is estimated by the organizations?
Ans:
The cost of implementing six sigma can be covered by the company’s direct payroll. Those who worked on this project full-time will be identified and compensated appropriately. This is an indirect payroll policy, meaning that measurements, data collection, product owner discussions, and other activities are used to determine who gets paid and how.
56. What is a data collection plan?
Ans:
A data collection plan is nothing but a plan which is used to collect necessary data. So main reason to collect data is to understand a current process and portray possible improvement suggestions.
57. Name some tools used during Six Sigma implementation.
Ans:
58. Define Regression in Six Sigma.
Ans:
Regression analysis is the method used to calculate the relationship between the set of input variables with respect to an output variable. In Six Sigma analysis phase, Regression analysis can be implemented to find out waste.59. Define Defect and Defective in Six Sigma.
Ans:
A Defect in a Six Sigma is used to indicate non-compliance of a unit in a process with respect to the specified requirements. Defective in the Six Sigma is defined as the multiple unit failures or process failures. Defect and Defective are the key terminologies in the Six Sigma process to identify the problems that need to be fixed.
60. What does Process Report?
Ans:
Process Report is the part of the DMAIC process in Six Sigma. This report covers an information regarding the performance of process in each step in analytical form.
61. What does X-bar and R-charts?
Ans:
X-bar and R-charts can be defined as the quality control charts to monitor variation and mean of the process. The X-bar provides information on the changes in mean over time, while R-charts provide an information on variations in sub-groups over time.
62. Define MSA in Six Sigma.
Ans:
MSA is abbreviation for Measurment System Analysis. MSA is used to determine an accuracy of the measurement systems. MSA evaluates accuracy, precision and stability of the system.
63. What does Nominal Group technique?
Ans:
The Nominal Group technique is the methodology for making decisions within group. This methodology is focused on identification of problems by the majority, in contrast to the minority in the group.
64. What does TRIZ?
Ans:
TRIZ is abbreviation for Theory of Inventive Problem Solving. This theory focuses on the specific problems to identify any patterns which occur on the consistent basis across the similar industries to find a possible solution. TRIZ is mostly utilised when commonly used in Six Sigma tools prove insufficient to move the project in desired direction.
65. What does DPMO, and How to calculate it?
Ans:
DPMO stands for the Defects Per Million Opportunities. It is the metric used to measure the level of defects or errors in a process relative to total number of opportunities for defects to be occur. The formula for a calculating DPMO is DPMO = (Total Defects / Total Opportunities) x 1,000,000.
66. Explain Champion in Six Sigma
Ans:
67. Name some Quality Management tools ?
Ans:
68. What does Kano Model?
Ans:
The Kano Model is the technique used for product development and customer satisfaction analysis. It categorises the customer preferences into the following categories- Basic, Performance, Excitement, Indifferent, Reverse.
69. When does use Kaizen events?
Ans:
Kaizen events should be used when there is need for a rapid improvement in a specific process or area. They effectively address an immediate problems, implement quick changes, and foster continuous improvement within the short timeframe.
70. What does Control Charts ? What does rules for using them?
Ans:
Control Charts are the statistical tools used to monitor and control processes over time. They provide the visual representation of process variation and help identify when process is out of control. Rules are:
71. What does Milestones?
Ans:
It depends on methodology in the Six Sigma process, either DMAIC or DMADV, and for each stage, sometime durations should be involved, the milestones provide a time limit for each stage, if extend the time limit, the need stakeholder approval.
72. What does Mapping of Value Stream?
Ans:
Value Stream Mapping (VSM) is the Lean Six Sigma technique used to visualize and analyze steps and information involved in production of a product or the delivery of a service. It is the graphical representation of the entire process from start to finish and helps in understanding, analyzing, and optimizing the flow of materials and information
73. How does ensure sustainability of process improvements?
Ans:
To ensure sustainability, control measures are established during Control phase of the DMAIC methodology. These may include implementing standard operating procedures, conducting a regular audits, providing training to employees, and using the statistical process control techniques to monitor and maintain process performance.
74. How does ensure the success of a Six Sigma project?
Ans:
Ensuring the success of a Six Sigma project involves several key factors. First, clear and measurable goals should be established, aligning with the organization’s strategic objectives. Adequate resources, including skilled team members and necessary tools, must be allocated. Comprehensive data analysis and process mapping are essential to identify areas for improvement.
75. Describe the Quality levels of Six Sigma.
Ans:
It is the method, where a set of tools is used to measure the process quality. It signifies how well business process is monitored. Each sigma level corresponds to a number of the acceptable defects per million. When the accuracy of a business process reaches 3.4 defects per million opportunities, the optimum sigma level is reached.
76. What does some common Six Sigma tools and techniques?
Ans:
Common tools and techniques in Six Sigma include the Process Mapping, Fishbone Diagrams (Ishikawa), Statistical Process Control (SPC) charts, Histograms, Pareto Analysis, Regression Analysis, and Design of Experiments (DOE), among others. These tools help in analyzing and improving the processes effectively.
77. How does prioritize projects in Six Sigma environment?
Ans:
Projects can be prioritized based on the various factors like potential impact on customers, financial benefits, strategic alignment with an organizational goals, and level of effort required. Prioritization matrices, cost-benefit analysis, and input from the stakeholders are often used to make an informed decisions about project priorities.
78. What does Green Belt in Six Sigma?
Ans:
A Green Belt is the Six Sigma team member who has been trained in methodology and plays a role in the process improvement projects. They typically work part-time on a Six Sigma projects while also performing regular job responsibilities.
79. Difference between Process Map and a Value Stream Map?
Ans:
A Process Map is the visual representation of the individual steps in a specific process, while Value Stream Map is a broader view that includes all activities (value-added and non-value-added) needed to deliver the product or service to a customer.
80. Explain DPU (Defects Per Unit) in Six Sigma.
Ans:
DPU is a metric for calculating the number of defects in a given unit or product. It measures the process’s quality by calculating the average number of defects per unit produced.
81. Explain Process Variation in Six Sigma?
Ans:
Process variation refers to the deviation of process from its intended outcome. Six Sigma aims to minimize the process variation to improve consistency and quality. There are the two types of process variation: Common cause variation and special cause variation.
82. What does value of Six Sigma?
Ans:
The value of Six Sigma is chance of 3.4 errors per million opportunities. This helps businesses in operating at 99% accuracy. The process control is attained at such precision.
83. What does difference between CPK and PPK?
Ans:
CPK is a process capability index. It measures how close the process is running to specification limit, relative to natural variability of the process. PPK stands for process performance index. It helps in verifying whether a sample that is generated for the process is capable of meeting the customer requirements or not.
84. Name some common levels of Six Sigma Certification.
Ans:
85. What does benefits of Six Sigma?
Ans:
86. How does sustain improvements made through Lean Six Sigma?
Ans:
Sustaining improvements requires the establishing control measures and monitoring key process indicators. This can include the implementing standard operating procedures, providing a training to employees, conducting regular audits, and engaging the stakeholders to ensure continuous adherence to improved processes.
87. Explain the concept “Voice of the Customer” in Lean Six Sigma?
Ans:
The Voice of the Customer (VOC) represents needs, expectations, and requirements of the customer. In Lean Six Sigma, capturing a VOC is crucial for understanding customer preferences, identifying the critical-to-quality characteristics, and aligning the process improvements to meet customer expectations.
88. What does disadvantage of six sigma?
Ans:
89. What does applications of six sigma?
Ans:
Manufacturing Industry, Service Industry, Healthcare Sector, Financial Services, Information Technology, Education Sector and Government and Public Sector.
90. What does Lean Six Sigma Green Belt?
Ans:
There will be several Green Belts within an organisation. The project leader position is typically held by a Green Belt. Working on Lean Six Sigma projects that fit within their purview and duties is what a Green Belt usually does. These people are familiar with the Lean Six Sigma framework and methodology.