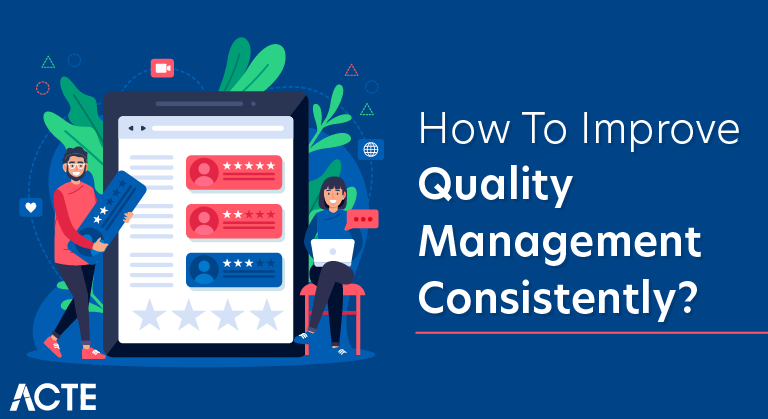
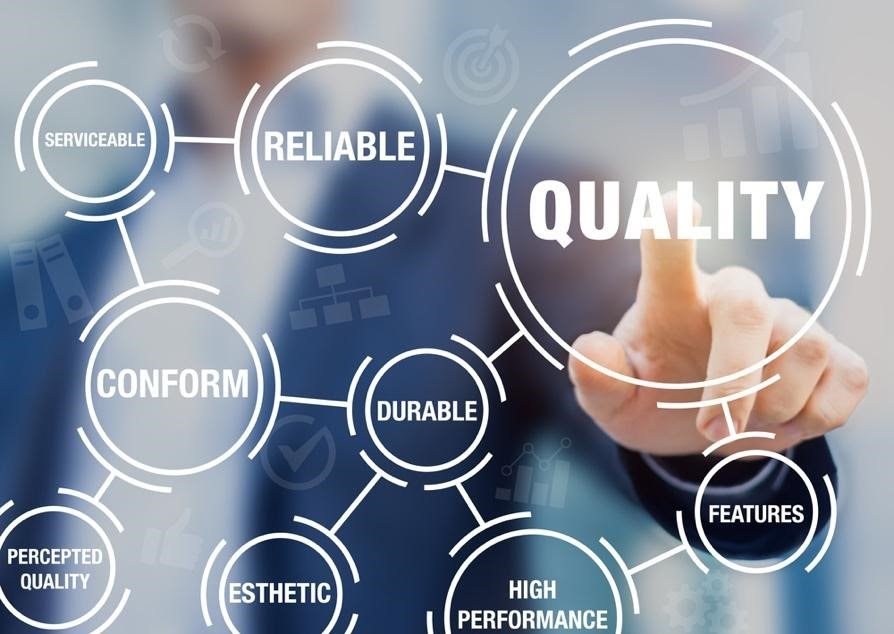
Quality management can be a make-or-break point for a manufacturing or distribution business. It can be the difference between putting out great products that satisfy your customers and producing unsatisfactory or even dangerous merchandise. It’s often not an easy process, but the rewards of getting it right are immense.
So, what can you do to make quality management not just part of your business, but a strength that separates you from your competitors? How can you reduce the cost and improve the efficacy? What are the key concepts that create real value in your processes? These seven tips can help you break open the secrets of quality management.
1. Understand the Cost of Quality model.
The Cost of Quality (COQ) model is the basic principle on which most quality management programs are based. Put simply, it states that quality always has a cost, but that investments to increase quality are more productive the earlier they’re introduced. Fixing a problem at the design stage, for example, is much cheaper than fixing it in production, and fixing it in production is massively cheaper than fixing it once it’s gone out the door. If you’re having trouble making upper management see the need to invest in quality management processes, a Cost of Quality analysis can be a great tool for making your case.
2. Know the different methods of quality management and choose the right one(s) for you.
Many different methods of quality management are used today, and each has its own advantages and drawbacks. Some of the most common include:
- Six-Sigma: An extremely popular method heavy on data crunching and measurement that has produced great results for many big names.
- FADE Model: A simple step-by-step framework of Focus, Analyze, Develop, Execute that can be integrated with many different strategies.
- PDSA Model: A cyclical model of Plan, Do, Study, Act that’s good for evaluating changes in real time as they are implemented.
- Total Quality Management: A system designed to get employees at every level involved in the long game of improving quality.
No one system is right for every company, and some can be used in conjunction with each other. Do your research and decide if implementing a new system can give you something you don’t currently have.
3. Take a good look at your AQL and decide if it’s at the right level.
- In most models, the Acceptable Quality Level (AQL) is a foundational tool for quality management. The AQL defines the minimum level of quality that’s acceptable in a product and determines whether a batch passes or fails its quality inspection.
- Although maximum quality in everything is theoretically a good goal to shoot for, in practice you’ll often find that striking a balance is essential. Using an AQL calculator, you can determine which level you’re currently operating at and look at what kind of quality levels you can expect from different sample sizes. If you’re having quality issues, you may want to look at increasing your sample size to improve accuracy.
4. Integrate your quality management and training programs.
- For quality management improvements to go from theory to practice, it’s best to start improving employees’ knowledge of best practices as early and comprehensively as possible. That’s why it’s important to incorporate your quality goals into training procedures. They’ll be much more achievable if all employees are moving toward them with a unified purpose, especially new hires.
- It’s equally crucial to make sure that floor supervisors have a good understanding of your quality goals. In many cases, they’re the ones who will help guide employees through the execution of quality improvement plans, so they should be among the first to know what’s going to change and why.
5. Generate employee buy-in by keeping them in the know and involved.
Changing the status quo is often unpopular, even when it’s done in the name of improving quality. To counteract this, many organizations choose to use strategies that maximize employee involvement in quality management and thus ideally maximize buy-in:
- Personalize each employee’s tasks in ways that play to their strengths and allow them as much autonomy as possible in problem solving.
- Use TQL strategies to involve employees at all levels in the processes most important to quality management.
- Ensure that employees have a thorough understanding of why a change needs to be made and how it’s going to work.
- Follow up throughout the process and make adjustments as needed. Don’t be afraid to “change the change” and modify what isn’t working.
6. Invest in new quality management technologies.
The applications for technological improvements in quality management are almost limitless. Consider the needs of your methodology and your sector and decide which areas you want to invest in:
- Improved data collection and customer feedback.
- More intuitive and in-depth training tools.
- Better automatic quality control sampling technologies.
- IoT devices to monitor manufacturing processes and detect defects early.
- More durable and accurate equipment that produces fewer errors.
Make sure, for example, that your quality control labs have the tools they need, such as microscopes to examine fine-tolerance parts. And, of course, training is essential to generate ROI from technology—employees need to understand how to use microscopes properly as well.
7. Make your solutions proactive.
- Quality management can often be a frustratingly reactive process, but it doesn’t have to be. Think back to the COQ model and remember that the ultimate goal of quality management should be to introduce improvements as early as possible in the process. If you’re having quality problems right now, reactive processes may be necessary—but don’t lose sight of the end goal of transitioning your quality management to a proactive model.
- Releasing quality products is the best way to make a name for yourself in manufacturing, and robust quality management is the only way to ensure that it happens. Remember that it’s an ongoing process and that there’s no finish line, so attack your quality management challenges with equal doses of patience and vigor. The rewards are rarely immediate, but they are substantial.