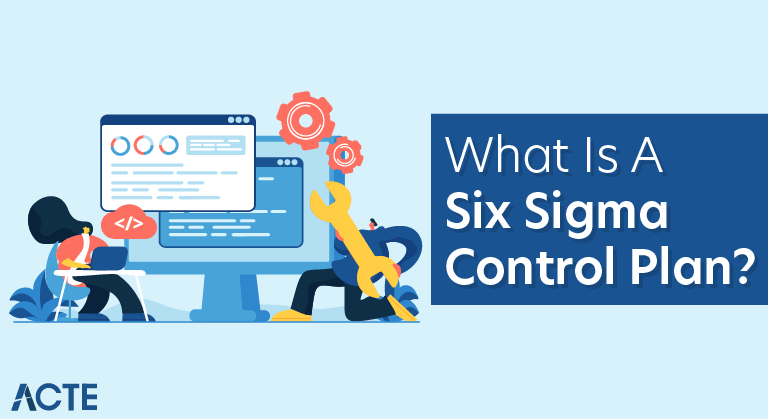
The intent of a process control plan is to control the product characteristics and the associated process variables to ensure capability (around the identified target or nominal) and stability of the product over time.
The process Failure Modes and Effects Analysis (FMEA) is a document to identify the risks associated with something potentially going wrong (creating a defect – out of specification) in the production of the product. The FMEA identifies what controls are placed in the production process to catch any defects at various stages on the processing.
Every completed Six Sigma project should have not only a control chart (if applicable), but a control plan. This ensures that the process doesn’t revert to the way it previously operated.
Use the process management summary to collect all the critical-to-quality outputs, or CTQs, for a process, a department, a division, or even an entire company. Roll up the summary to whatever level your organization needs for monitoring, reviewing, and taking action to assure acceptable process and business performance. Each time a Six Sigma project is completed, add that project’s CTQs to the summary.
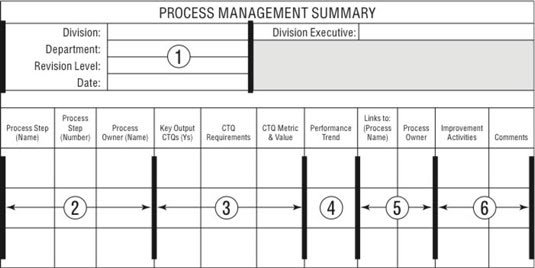
In this example, the administrative section of the summary is where you identify the organizational areas involved, plus the revision level and date of the information. The summary’s purpose is captured in the main body, where you provide enough information for anyone to readily see the current status of the CTQs, how they relate to downstream processes, and what actions, if any, are currently being taken.
Control PlanDescription:
The Control Plan is a guide for the Process Owner to assist in tracking and correcting the performance of the KPIV’s and KPOV’s.
Objective:
Develop a thorough summary document to clarify the details around controlling the key inputs and key outputs.
Once the project is closed it is not necessarily over.
The Control Plan is one part of ensuring the gains are maintained. If process performance strays out of control there are details and tools to adjust and re-monitor to ensure there has not been an over-adjustment.
It is possible that the new performance capability warrants the calculation of new control limits. If so, the test(s) used, evidence, and new control limits should also be a part of this document. It is ideal to have a simple one-page document but if appendices and attachments are needed to ensure understanding and control then include this information.
Include all relevant material and information it takes to ensure the gains are sustained. Often times there are long-term action items and the project list (possibly utilize a Gantt Chart) shall be updated and followed by the Process Owner until those actions are complete.
The GB/BB will often move on to another project after the team disbands but follow up is often required weeks or months later. The follow up is done in conjunction with the Process Owner and possibly the Controller. Adhering to the details of the Control Plan will standardize these efforts and allow quick analysis of current performance.
Below is a simple example as a one-page document. It may be necessary to add or remove information to suit your team’s needs.
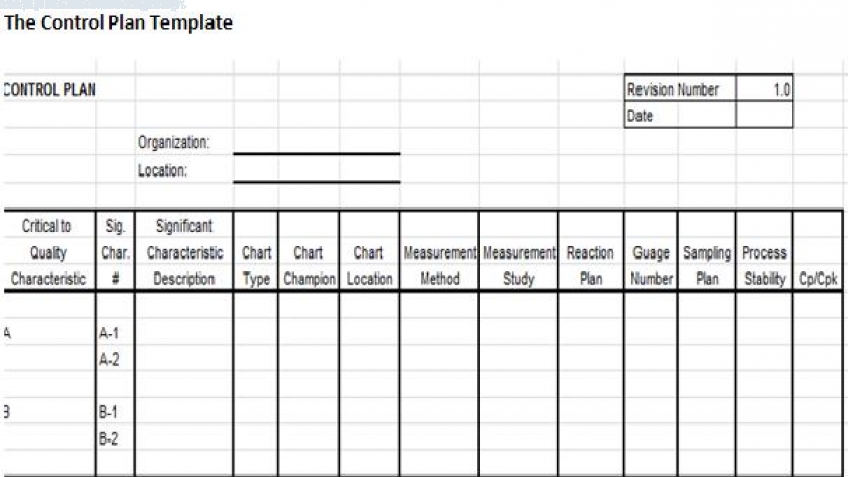
The four techniques used for process control plans are:
- Standardization
- Documentation
- Monitoring Plan
- Response Plan
Standardization:
Standardization of the “should-be” process steps is required to ensure all responsible for execution have the same understanding. Standardizing the should-be process helps answer queries like:
- What are the steps in the process?
- Who does these steps in the process and when?
- Where more detailed work instructions can be found?
Documentation:
Documentation is a necessary step to insure that the learning gained via improvement is institutionalized and shared across the team by having it documented with proper work procedures. Often the live processes have a tendency to evolve in an ad-hoc manner. How to accomplish each process activity is usually left up to the individuals and thus, much of the organizational knowledge resides only in the minds of all those responsible for execution. Procedure: A procedure is the documented sequence of steps & other instructions necessary to carry out an activity for a process.
Monitoring Plan:
Monitoring: It helps detect changes as and when they occur in the process and assure that improvements continue to hold for us to be able to meet customer requirements over a period of time. While observing a process a monitoring plan helps define:
- Key process and output measures for ongoing measurement of the improved process
- When data is to be collected and at how often
- Define the method for gathering, recording, and reporting data on the measures
Response Plan:
Response plan helps identify the next steps on what needs to be done if one detects a change in the process while monitoring. For each of the measure in the monitoring plan, the response plan helps define:
- What actions will be taken for an out-of-control event occurrence with a timeframe for the action
- Who takes action based on the monitoring data
- Where to find trouble-shooting procedures to fix problem
The key elements of a full scale implementation plan are:
- Clear Objectives
- Pilot Learning’s Incorporated
- Implementation Milestones
- Resource Needs
- Influence Strategy
- Implementation Budget
- Process Control Plan
- Process Documentation
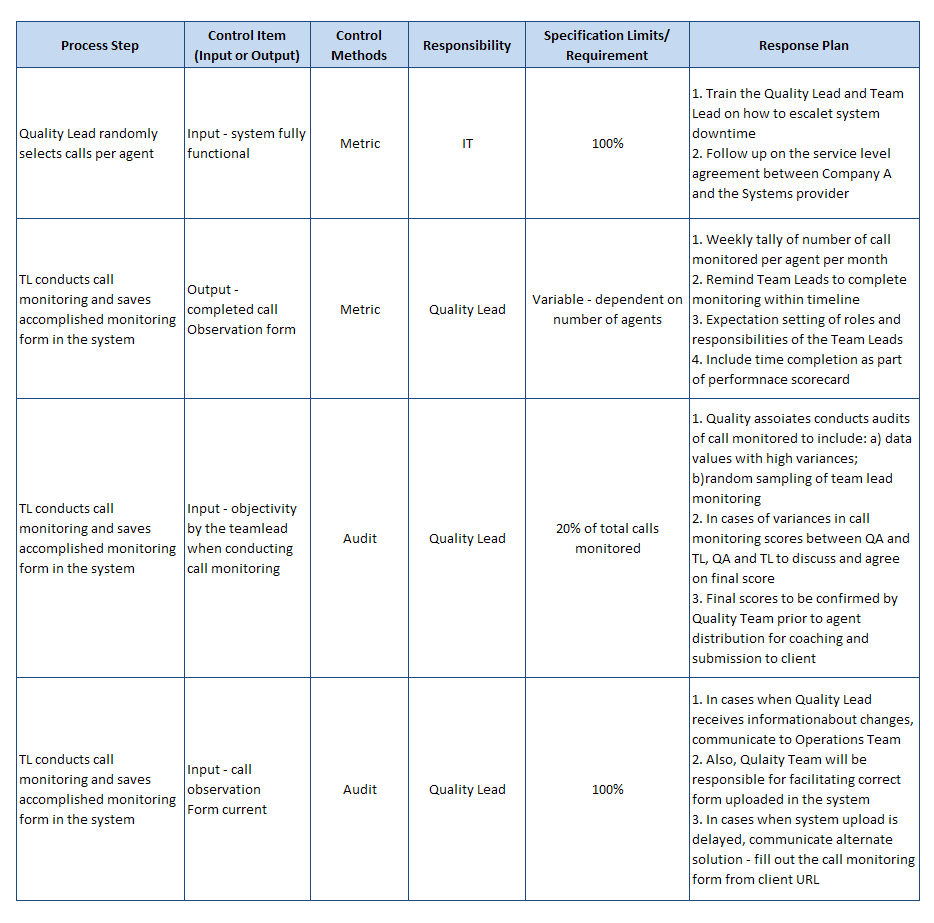
OCAP Table Example
Control plans may include other data than the one presented. The important thing is that they must be available, controlled and trained to.
Visual Management is also another tool that can be used in Control phase. This shows the management of course performance by majorly displaying updated course standards, scorecards on performance, production goals, and other useful course and performance data in the work place. The objective of this tool is to drive the right behavior.
Examples of Visual Management are job aids posted on each work post, whiteboards showing daily progress against target, individual or team scorecards displayed in the team’s common area which can be the subject of discussion during team huddles.
Visual Management gives a real-time and clear line of sight to significant performance information. This also enables quick detection of performance concerns. Since this shown in a common area, this enables leads to deliver prompt response. VM also enables constant enhancement mindset that can determine chances for improvement.
Another tool tat can be used during the Control phase is the Operating Rhythm. This is a set of structured, mutually dependent interactions that manages and shows performance information to allow stakeholder set to effectively, consistently, and proactively express control operations. It provides a shared and disciplined messaging method through which stakeholders are defined with roles, agendas, and outcomes.
Operating Rhythm holds rapid employment of tasks, messaging, and ideas through identified and prearranged interactions. It allows quick response and surfacing to process problems, self-esteem issues, and individual performance. Each communication has a stated objective, clear membership, set measures, designated leader, defined actions, and frequency. By connecting the suitable group members in a closely controlled structure, operations become dependent on process rather that dependent on individuals.
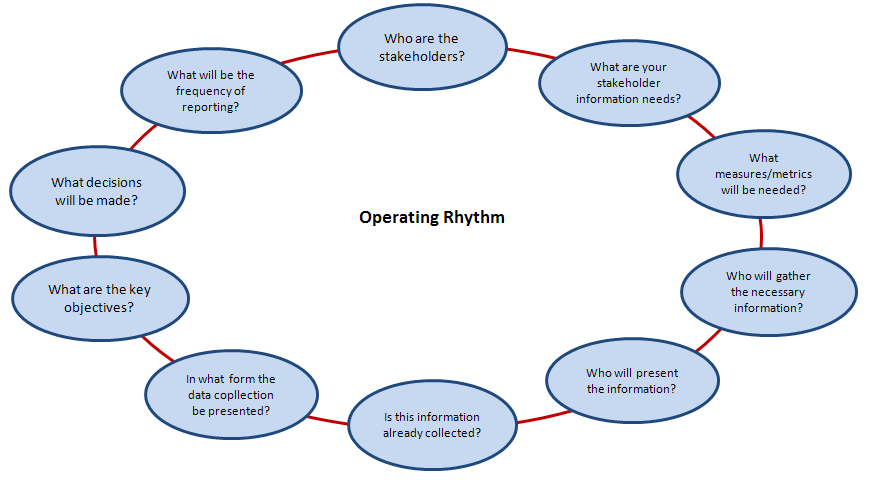
Operating Rhythm Chart
Productive assembly do not turn out by accident. There should be preparation, process, content, and follow-up. Operating Rhythm spans the entire organization thus it is imperative that everything, all factors, all aspects of the project is discussed.