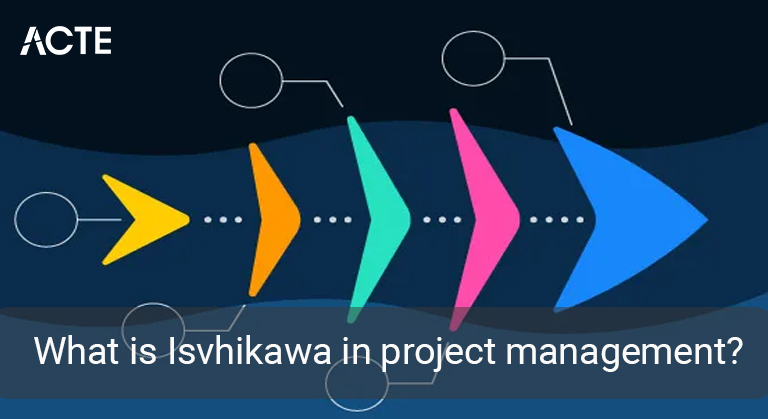
What Is an Ishikawa Diagram?
An Ishikawa graph is a chart that shows the reasons for an occasion and is frequently utilized in assembling and item advancement to layout the various strides in a cycle, exhibit where quality control issues may emerge, and figure out which assets are needed at explicit occasions.
The Ishikawa graph was created by Kaoru Ishikawa during the 1960s as a method of estimating quality control processes in the shipbuilding business.
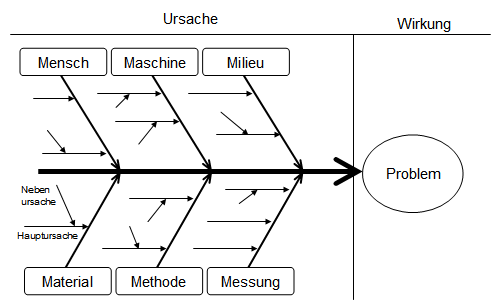
Understanding Ishikawa Diagrams :-
Ishikawa charts are now and then alluded to as fish bone graphs, herringbone outlines, circumstances and logical results outlines, or Fishikawa. They are causal charts made by Kaoru Ishikawa to show the reasons for a particular occasion. They take after a fish skeleton, with the “ribs” addressing the reasons for an occasion and the ultimate result showing up at the top of the skeleton. The reason for the Ishikawa chart is to permit the board to figure out which issues must be addressed to acquire or stay away from a specific occasion.
Other normal employments of the Ishikawa graph incorporate involving it as a procedure for making item plans that take care of useful issues. It can likewise be utilized in quality deformity counteraction to recognize potential variables causing a general impact. Each cause or justification for flaw is a wellspring of variety. Makes are generally assembled into significant classifications recognize and arrange these wellsprings of variety.
- The gathering ought to settle on an issue articulation (impact).
- Compose the issue explanation at the middle right of the flipchart or whiteboard, box it, and draw an even bolt hurrying to it.
- Compose the classifications of causes as branches from the primary bolt.
- Conceptualize potential causes. Inquire: “For what reason does this occur?” As every thought is given, the facilitator composes it as a branch from the suitable class. Causes can be written in a few spots, assuming they connect with a few classifications.
- Pose the inquiry “for what reason does this occur?” once more. Compose sub–causes fanning out the causes. Keep on inquiring “Why?” and create further degrees of causes. Layers of branches show causal connections.
- At the point when the gathering runs out of thoughts, center regard for regions in the outline where thoughts are slender.
Process to Make an Ishikawa Diagram :-

To make an Ishikawa Diagram, a gathering will require a white board, flip outline, and a few checking pens.
Conceptualize the essential classes of reasons for the issue. For example, it may check out to begin with these conventional headings: strategies, machines (hardware), individuals (labor), materials, estimation, and climate.
Using the Ishikawa diagram for quality control in project management :-
Utilizing the fishbone chart and the 5W1E strategy can be of extraordinary assistance in an assortment of circumstances and for critical thinking at large. At the point when the Ishikawa graph is utilized in project the executives, it can prompt significant quality upgrades and restorative measures, as it permits you to go to the underlying driver of the issue and tackle the issue for great. You could cut down costs, further develop representative usefulness and then some
6 M’s of the Ishikawa Diagram :-
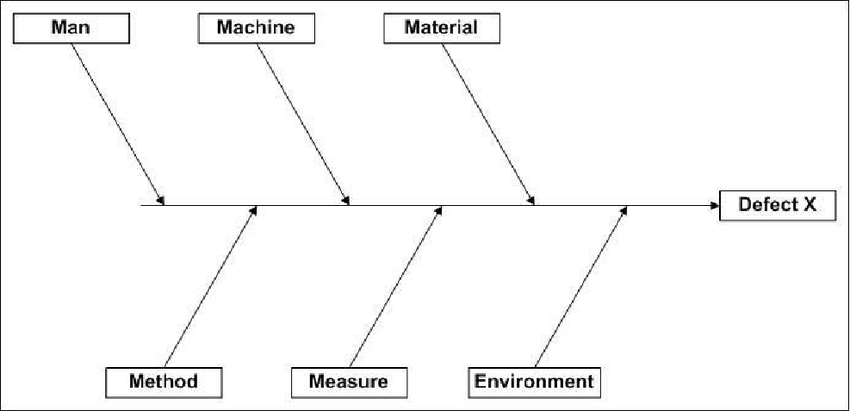
1. Machines: Numerous issues are gotten from the disappointments of machines and hardware. This might be brought about by ill-advised upkeep or the absence of support.
Considering this, it is significant all the time to regulate the activity of all hardware, so the activity is near flawlessness, keeping away from harms.2. Materials: This issue is connected with the utilization of materials all the while. Might be connected with out-of-spec material or mistaken volume. Consequently it is critical to have a decent connection with your provider, so he offers right items, in the right amount and obviously, in the best quality.
3. Labor: It is connected with the mentalities of representatives in the execution of exercises. This issue can be brought about by their scurry, foolishness, absence of capability or even absence of ability. You realize people are powerless to disappointment, isn’t that right? Thus, to stay away from mistakes in specific cycles, it is prescribed to utilize the Poka Yoke. Yet, what is Poka Yoke? It is a mistake resistant gadget intended to stay away from absconds in assembling processes.
4. The compelling force of nature: These are issues connected with the interior and outer climate of the association. When discussing outside factors you can discuss contamination and the climate insecurity, for instance. Also in the inside climate it very well may be the absence of room, inaccurate format, commotion, among others. It is vital to have a work space good for everybody, so they have a more noteworthy joy in playing out their obligations. With everything filling in as arranged, you decrease the turn of the workers, lessening cost and thusly expanding the benefit.
5. Estimations: This “M” is connected with the measurements used to quantify, control and screen processes. You might be utilizing a mistaken method for estimating your cycle. This is creating revamp and hurting your cycle.
6. Strategies: Alludes to the strategies and techniques embraced by the association during exercises. The technique can be characterized through programming and arranging apparatuses. It addresses the manner in which you plan the advancement of your exercises and how to control what’s going on.
- The primary advantage of utilizing the graph is the way that is a visual instrument, straightforward and simple to examine ;
- It impacts all workers engaged with the interaction to focus on the outcomes to be accomplished;
- It assists with observing the underlying driver of the issue;
- Can be utilized as a measurable apparatus for complete quality control;
- It focuses on an examination in more detail, assisting with settling on more compelling choices;
- It has a conventional use and adaptable design, being material in issues of various qualities.
Benefits :-
There are many benefits to involving this quality apparatus in the business climate. I will currently list 6 of them so you can consider it:
- Regardless of its incredible pertinence and effortlessness in cause definition, the instrument has not just sure focuses. We can refer to certain detriments, for example,
- It doesn’t flag the genuine gravity of the issue; Frequently exertion is squandered in recognizing the reason for impacts that have no extraordinary significance.
- It ought to be utilized ideally by representatives who as of now have some information about the PDCA cycle;
- Since it is a moderately basic apparatus, it is important to have a business structure good for this carry out;
- Since they cover various regions and an enormous number of individuals, it is conceivable that exists various sentiments, being important to know how to control them.
Drawbacks :-
Notwithstanding these detriments it is important to play it safe when creating and carrying out the Ishikawa Diagram:
- The Ishikawa Diagram is a significant instrument in finding the main driver of an issue. It carries a ton of advantages to the entire interaction.
- With a more clear perspective on the impacts it is feasible to go to remedial and preventive lengths on the issue all the more successfully, and afterward dispose of its main driver.
- These days, all areas, regardless of whether in industry, advertising, money and others, utilize this outline continually, showing its significance.
- What’s more it’s memorable’s vital, consistently center around the customer while proposing the activities, as they are the most answerable for the achievement of your organization.
Extremely important tool :-
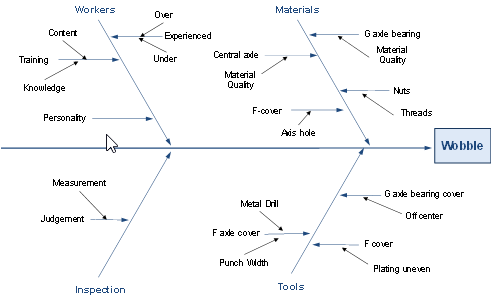
Conclusion :-
The Ishikawa diagram, also known as a fishbone diagram, is a useful tool in project management, particularly when it comes to quality control. Conducting a proper risk analysis, anticipating and solving problems are essential management skills to lead successful projects.